- お役立ち記事
- Streamline manufacturing design with digital engineering! Reduced development time through simulation
Streamline manufacturing design with digital engineering! Reduced development time through simulation
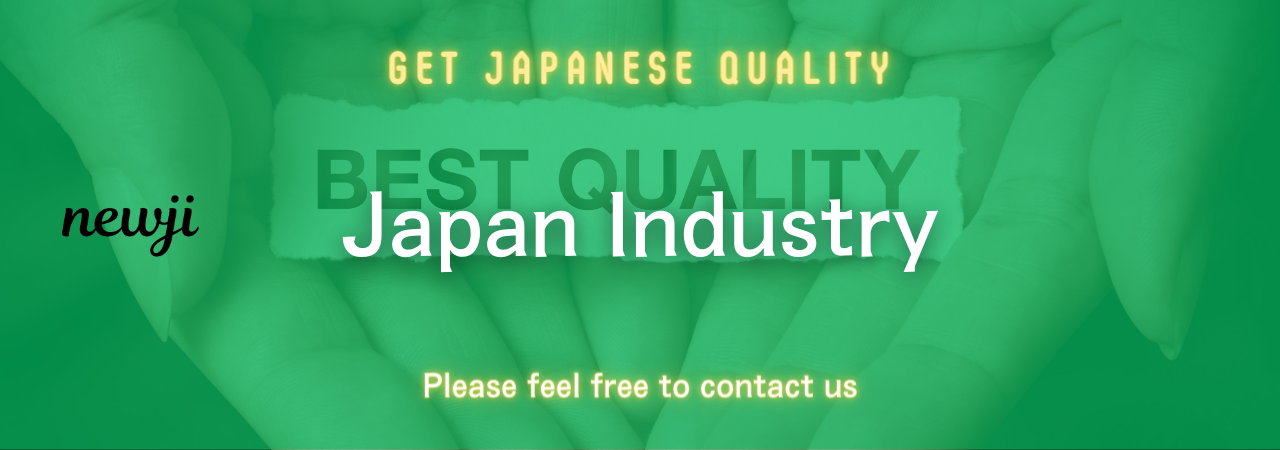
In today’s fast-paced industrial landscape, efficiency and productivity are paramount to maintaining a competitive edge.
One significant innovation, digital engineering, is revolutionizing how manufacturers approach design and development.
This technology leverages digital tools and simulations to streamline the manufacturing design process, significantly reducing development time.
目次
What is Digital Engineering?
Digital engineering is an integration of computational tools and simulations with traditional engineering practices.
This approach enables engineers to create virtual models of products and systems, allowing for thorough testing and refinement before actual production begins.
Digital engineering utilizes software to simulate various conditions, predict performance, and identify potential issues, thereby minimizing the need for physical prototypes.
Key Benefits of Digital Engineering
Digital engineering offers several key benefits that are transforming the manufacturing sector:
1. Accelerated Product Development
One of the most significant advantages of digital engineering is the rapid pace at which products can be developed.
Simulations allow for quick iterations and refinements, reducing the time from concept to market.
This acceleration not only saves costs but also enables manufacturers to stay ahead of market trends.
2. Cost Efficiency
Traditional prototyping can be expensive and time-consuming.
By leveraging digital models, manufacturers can identify and address potential issues early in the development process.
This reduces the number of physical prototypes required, cutting down on material costs and labor expenses.
3. Enhanced Design Accuracy
Digital tools provide a high degree of precision, ensuring that designs are accurate and optimized for performance.
Simulation software can test various scenarios and conditions, leading to better-informed decisions and fewer errors in the final product.
This level of accuracy enhances the overall quality and reliability of manufactured goods.
4. Improved Collaboration
Digital engineering platforms often include features that allow for real-time collaboration between teams and stakeholders.
Engineers, designers, and project managers can share models and data, making it easier to coordinate efforts and stay aligned with project goals.
This collaborative approach fosters innovation and ensures that everyone is working towards the same objectives.
5. Risk Mitigation
By simulating real-world conditions and testing virtual models, manufacturers can identify potential flaws and weaknesses before they become costly problems.
This proactive approach to risk management helps avoid production delays and ensures that products meet safety and regulatory standards.
Implementing Digital Engineering in Manufacturing
To leverage the full potential of digital engineering, manufacturers must adopt a strategic approach to implementation.
Here are some essential steps to consider:
1. Invest in the Right Tools
Choosing the appropriate digital engineering software and tools is critical.
Look for solutions that offer robust simulation capabilities, intuitive interfaces, and support for your specific industry needs.
Scalability and integration with existing systems are also important factors to consider.
2. Train Your Team
Successful implementation requires a skilled workforce familiar with digital engineering principles and tools.
Investing in training and development programs will help your team adapt to new technologies and workflows.
Providing ongoing support and resources will ensure that your staff can effectively utilize digital engineering to its fullest potential.
3. Foster a Culture of Innovation
Encourage a culture that embraces innovation and continuous improvement.
Empower your team to experiment with new ideas and approaches, allowing for creative problem-solving and innovation.
Recognize and reward efforts that contribute to efficiency and productivity gains.
4. Continuously Evaluate and Optimize
Digital engineering is not a one-time implementation but an ongoing process.
Continuously evaluate your tools, processes, and outcomes to identify areas for improvement.
Regularly updating software and refining workflows will help your organization stay at the forefront of technological advancements.
Case Studies: Success with Digital Engineering
Numerous manufacturers have successfully integrated digital engineering into their operations, yielding remarkable results.
Here are a few examples:
1. Automotive Industry
Leading automotive manufacturers have adopted digital engineering to streamline vehicle design and production.
By simulating crash tests and performance scenarios, they can ensure safety and reliability while reducing the need for physical prototypes.
This approach has significantly shortened development cycles and lowered costs.
2. Aerospace Sector
The aerospace industry relies heavily on precision and safety.
Digital engineering allows for the detailed analysis of aircraft components and systems under various conditions.
This has led to more efficient designs, improved performance, and faster certification processes.
3. Consumer Electronics
In the fast-moving consumer electronics market, staying ahead of trends is crucial.
Digital engineering enables companies to quickly develop and test new products, ensuring that they meet consumer expectations and regulatory standards.
This agility has helped firms launch innovative technologies while maintaining high quality.
The Future of Digital Engineering in Manufacturing
As technology continues to evolve, digital engineering will play an increasingly pivotal role in manufacturing.
Emerging trends such as artificial intelligence, machine learning, and the Internet of Things (IoT) are set to enhance simulation capabilities and drive further efficiencies.
Manufacturers that embrace these advancements will be well-positioned to lead the market with cutting-edge products and optimized production processes.
Digital engineering represents a powerful tool for manufacturers aiming to streamline design and reduce development time.
By adopting digital solutions, investing in training, and fostering a culture of innovation, companies can achieve significant gains in efficiency, cost savings, and product quality.
As the industry continues to evolve, staying ahead of technological trends will be key to maintaining a competitive edge.
資料ダウンロード
QCD調達購買管理クラウド「newji」は、調達購買部門で必要なQCD管理全てを備えた、現場特化型兼クラウド型の今世紀最高の購買管理システムとなります。
ユーザー登録
調達購買業務の効率化だけでなく、システムを導入することで、コスト削減や製品・資材のステータス可視化のほか、属人化していた購買情報の共有化による内部不正防止や統制にも役立ちます。
NEWJI DX
製造業に特化したデジタルトランスフォーメーション(DX)の実現を目指す請負開発型のコンサルティングサービスです。AI、iPaaS、および先端の技術を駆使して、製造プロセスの効率化、業務効率化、チームワーク強化、コスト削減、品質向上を実現します。このサービスは、製造業の課題を深く理解し、それに対する最適なデジタルソリューションを提供することで、企業が持続的な成長とイノベーションを達成できるようサポートします。
オンライン講座
製造業、主に購買・調達部門にお勤めの方々に向けた情報を配信しております。
新任の方やベテランの方、管理職を対象とした幅広いコンテンツをご用意しております。
お問い合わせ
コストダウンが利益に直結する術だと理解していても、なかなか前に進めることができない状況。そんな時は、newjiのコストダウン自動化機能で大きく利益貢献しよう!
(Β版非公開)