- お役立ち記事
- How to Improve the Purchasing Process in Manufacturing
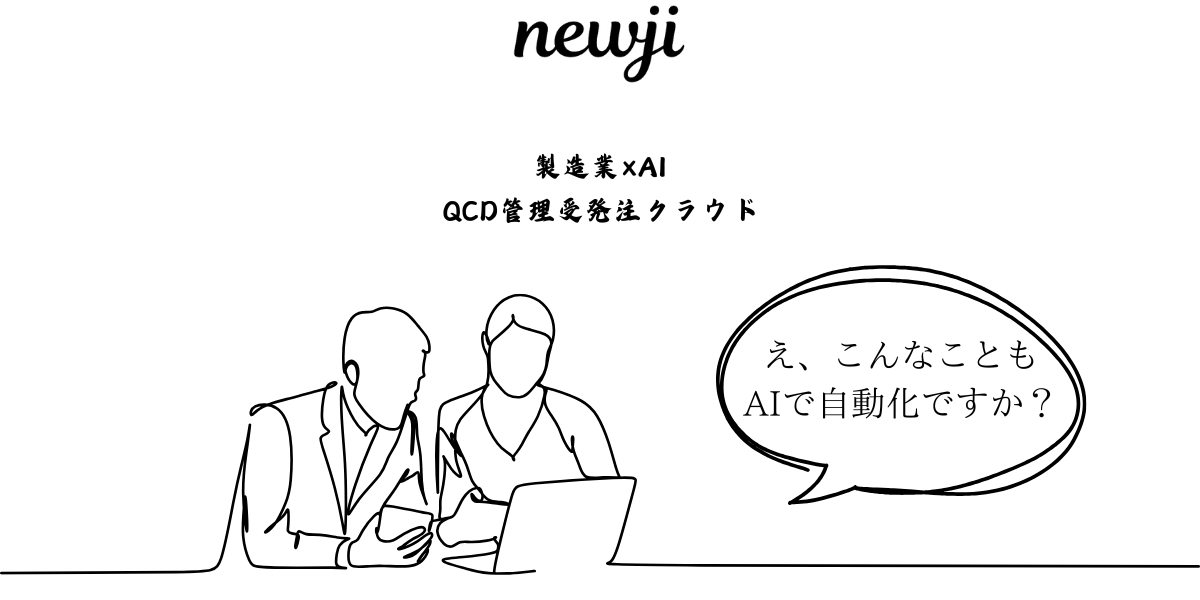
How to Improve the Purchasing Process in Manufacturing
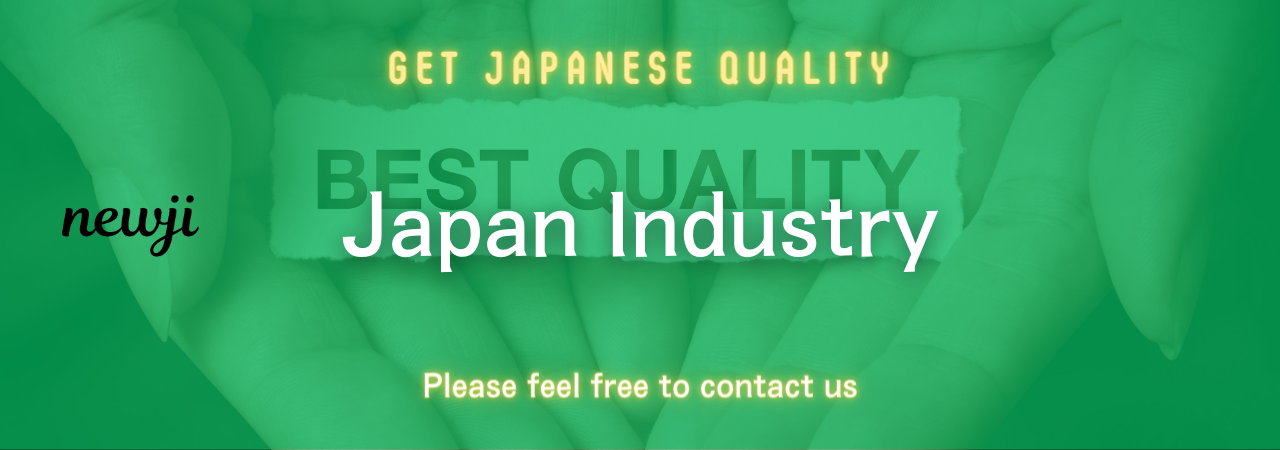
In the fast-paced world of manufacturing, improving the purchasing process is crucial.
A streamlined system can save time and money, making the entire operation more efficient.
Here, we will explore some effective ways to enhance the purchasing process in manufacturing.
目次
Understand Your Requirements
Before making any purchases, it’s essential to know what you need.
Identify the materials, parts, or services required for your production.
Take the time to list out specifications, quantities, and preferred suppliers.
This will ensure you are well-prepared when it’s time to make the purchase.
Analyze Past Data
Look at your previous purchasing records.
Recognize patterns in your buying habits.
This can provide insights into seasonal demands, supplier performance, and frequently purchased items.
By understanding past trends, you can make better decisions in the future.
Build Strong Supplier Relationships
Building a strong rapport with your suppliers is key to a smooth purchasing process.
A good relationship can lead to better prices, faster delivery, and top-quality products.
Communicate openly and regularly with your suppliers.
Discuss your needs and expectations clearly.
Evaluate Suppliers
Not all suppliers are created equal.
Periodically assess the performance of your suppliers.
Consider factors like reliability, cost, quality, and service.
A supplier who consistently meets or exceeds your expectations is a valuable partner.
Implement Technology
Technology can greatly enhance the purchasing process in manufacturing.
Using the right tools can streamline tasks, reduce errors, and improve efficiency.
Use a Procurement System
Invest in a robust procurement system.
These systems can automate many purchasing tasks, such as order processing, approvals, and payment.
They also provide valuable real-time data, making it easier to track purchases and manage inventory.
Leverage Data Analytics
Data analytics can help you make more informed decisions.
Analyze purchasing data to identify trends, monitor supplier performance, and forecast future needs.
With data-driven insights, you can optimize the entire purchasing process.
Standardize Processes
Standardizing your purchasing procedures can reduce confusion and improve efficiency.
Create clear, consistent processes for all purchasing activities.
Develop Standard Operating Procedures
Documenting your purchasing process is critical.
Create standard operating procedures (SOPs) that outline each step in the purchasing journey.
Train your team on these procedures to ensure everyone is on the same page.
Centralize Purchasing
Centralizing purchasing activities can lead to better coordination and control.
Have a dedicated team or department responsible for all purchasing tasks.
This will help avoid duplication, streamline communication, and ensure consistency.
Focus on Quality
In manufacturing, the quality of your materials can greatly impact the final product.
Ensure you are purchasing from reliable sources, and never compromise on quality.
Conduct Quality Checks
Implement quality checks for all incoming materials.
This will help you catch any defects early and avoid production delays.
Work closely with suppliers to address any quality issues promptly.
Set Quality Standards
Establish clear quality standards with your suppliers.
Ensure they understand your requirements and expectations.
Regularly review and update these standards as necessary.
Optimize Inventory Management
Effective inventory management can streamline the purchasing process and reduce costs.
Keep track of your inventory levels and avoid overstocking or understocking.
Implement Just-in-Time Inventory
The just-in-time inventory method can help reduce storage costs and minimize waste.
Only order materials when they are needed for production.
This requires precise planning and excellent supplier coordination.
Use Inventory Management Software
An inventory management system can provide real-time visibility into your stock levels.
These systems can help you track usage, manage reordering, and avoid stockouts.
Integrate your inventory management system with your procurement system for seamless operations.
Continuous Improvement
Finally, always strive for continuous improvement.
Regularly assess and refine your purchasing process.
Seek feedback from your team and suppliers for areas of improvement.
Conduct Regular Audits
Perform regular audits of your purchasing process.
Identify any inefficiencies or areas for enhancement.
Use audit findings to make informed changes and improvements.
Encourage Team Training
Invest in ongoing training for your purchasing team.
Keeping your team updated on the latest industry trends, tools, and best practices will ensure they are well-equipped to perform their roles effectively.
By following these steps, you can significantly improve your purchasing process in manufacturing.
A well-optimized system will not only enhance efficiency but also contribute to overall business success.
Take the time to implement these strategies, and you’ll see the positive impact on your operations.
資料ダウンロード
QCD調達購買管理クラウド「newji」は、調達購買部門で必要なQCD管理全てを備えた、現場特化型兼クラウド型の今世紀最高の購買管理システムとなります。
ユーザー登録
調達購買業務の効率化だけでなく、システムを導入することで、コスト削減や製品・資材のステータス可視化のほか、属人化していた購買情報の共有化による内部不正防止や統制にも役立ちます。
NEWJI DX
製造業に特化したデジタルトランスフォーメーション(DX)の実現を目指す請負開発型のコンサルティングサービスです。AI、iPaaS、および先端の技術を駆使して、製造プロセスの効率化、業務効率化、チームワーク強化、コスト削減、品質向上を実現します。このサービスは、製造業の課題を深く理解し、それに対する最適なデジタルソリューションを提供することで、企業が持続的な成長とイノベーションを達成できるようサポートします。
オンライン講座
製造業、主に購買・調達部門にお勤めの方々に向けた情報を配信しております。
新任の方やベテランの方、管理職を対象とした幅広いコンテンツをご用意しております。
お問い合わせ
コストダウンが利益に直結する術だと理解していても、なかなか前に進めることができない状況。そんな時は、newjiのコストダウン自動化機能で大きく利益貢献しよう!
(Β版非公開)