- お役立ち記事
- ピッキングシステムの最適化と効果: 倉庫作業効率向上と調達プロセスの改善
ピッキングシステムの最適化と効果: 倉庫作業効率向上と調達プロセスの改善
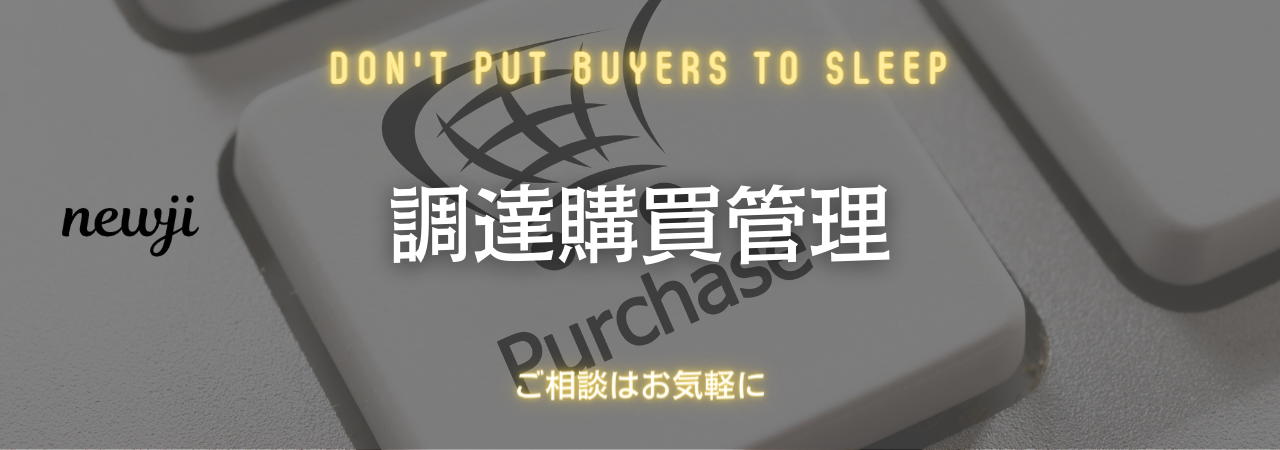
今や製造業の競争力を維持するためには、調達購買部門の効率化が不可欠です。
特にその中でも、ピッキングシステムの最適化は非常に重要です。
この記事では、ピッキングシステムの最適化とその効果について、具体的な実例も交えながら説明します。
目次
ピッキングシステムとは?
ピッキングシステムとは、倉庫内で必要な商品や部品を取り出すためのシステムのことです。
膨大な種類の商品や部品を迅速かつ正確に取り出すことが求められます。
そこで、効率的なピッキングシステムは企業の競争力を高め、コストダウンに繋がります。
種類とシステム構成
ピッキングシステムは大きく分けると、手動ピッキング、自動ピッキング、ハイブリッドピッキングの3つに分類されます。
手動ピッキング
手動ピッキングは、作業員が直接倉庫内を歩き回り商品を取り出す方法です。
ピッキングリストや端末を使用し、指示に従って商品を倉庫内から取り出します。
コストは低いものの、作業員のスキルや体力に依存するため効率には限界があります。
自動ピッキング
自動ピッキングシステムは、ロボットや搬送システムを用いて商品を自動的に取り出す方法です。
人間の手が関わる部分が少ないため、高い正確性と効率を誇ります。
しかし、導入コストが高く、初期投資が必要です。
ハイブリッドピッキング
ハイブリッドピッキングは、手動と自動を組み合わせた方法です。
一部の工程は作業員が行い、他の部分を自動化することでバランスを取ります。
初期投資を抑えつつ効率も向上させることができるため、多くの企業で採用されています。
ピッキングシステムの最適化方法
ピッキングシステムの最適化は、具体的な方法を駆使することで実現できます。
以下にその主な方法を紹介します。
ピッキングルートの最適化
ピッキングルートの最適化は、作業員が倉庫内を効率的に移動できるようにすることが目的です。
ABC分析を用いて、頻繁に使用される商品は取り出しやすい場所に配置し、後から使用する商品は奥に配置します。
これは、作業時間の短縮と無駄な移動の削減に寄与します。
倉庫レイアウトの見直し
適切な倉庫レイアウトの設計は、ピッキング効率の向上に直結します。
棚の高さや通路の広さ、商品の配置を工夫することが非常に重要です。
具体例としては、ゾーニングを行い、類似商品を同じエリアに配置することが挙げられます。
また、垂直倉庫や高層ラックの利用も効果的です。
テクノロジーの活用
最新のテクノロジーを導入することで、ピッキングシステムの効率を飛躍的に向上させることができます。
例えば、RFID(無線周波数識別)タグを使用することで、商品の場所を正確に把握し、ピッキング作業のミスを減少させることができます。
また、AR(拡張現実)技術を利用したピッキング支援システムも注目されています。
ピッキングシステム最適化による効果
ピッキングシステムの最適化は、倉庫作業の効率向上だけでなく、多岐にわたる効果をもたらします。
作業時間の短縮
最適化されたピッキングシステムは、作業時間を大幅に短縮します。
ピッキングルートや倉庫レイアウトの調整、テクノロジーの導入により、無駄な時間を削減し、生産性を向上させます。
誤ピッキングの減少
誤ピッキングは、顧客クレームや返品、追加コストを生む原因となります。
最適化されたシステムは、商品の正確な位置情報を提供するため、誤ピッキングの確率を大幅に減少させます。
在庫管理の精度向上
最新のテクノロジーを活用することで、在庫管理の精度も向上します。
特にRFIDタグやバーコードスキャンシステムは、在庫のリアルタイム管理を可能にし、不足や過剰在庫を防止します。
コスト削減
ピッキングシステムの最適化は、作業効率向上により人件費の削減や、誤ピッキングや在庫不足による余分なコストの削減に繋がります。
また、効率化されたシステムは、将来的な運用コストの抑制にも寄与します。
実例: 最適化に成功した企業のケーススタディ
ここでは、実際にピッキングシステムの最適化に成功した企業の事例を紹介します。
事例1: ABC社の取り組み
ABC社は、倉庫内のピッキング効率を向上させるために、ピッキングルートの最適化と最新のRFIDタグ技術を導入しました。
その結果、作業時間は30%短縮され、誤ピッキング件数も50%減少しました。
これにより、生産性が大幅に向上し、コスト削減効果も得られました。
事例2: XYZ製造業の取り組み
XYZ製造業は、倉庫レイアウトを見直し、垂直倉庫を導入しました。
また、AR技術を活用したピッキング支援システムも導入し、作業員の負担を軽減しました。
その結果、作業効率は25%向上し、在庫管理の精度も改善されました。
これにより、年間で数百万円のコスト削減を実現しました。
ピッキングシステムの最適化は、倉庫作業の効率向上と調達プロセスの改善に直結します。
具体的な方法としては、ピッキングルートの最適化、倉庫レイアウトの見直し、最新のテクノロジーの活用が挙げられます。
これらの取り組みを通じて、作業時間の短縮や誤ピッキングの減少、在庫管理の精度向上、コスト削減など、多岐にわたる効果を得ることができます。
ピッキングシステムの最適化は、製造業における調達購買部門の効率化において重要な役割を果たします。
これからの企業は、競争力を維持するためにも、積極的にピッキングシステムの見直しを検討することが必要です。
資料ダウンロード
QCD調達購買管理クラウド「newji」は、調達購買部門で必要なQCD管理全てを備えた、現場特化型兼クラウド型の今世紀最高の購買管理システムとなります。
ユーザー登録
調達購買業務の効率化だけでなく、システムを導入することで、コスト削減や製品・資材のステータス可視化のほか、属人化していた購買情報の共有化による内部不正防止や統制にも役立ちます。
NEWJI DX
製造業に特化したデジタルトランスフォーメーション(DX)の実現を目指す請負開発型のコンサルティングサービスです。AI、iPaaS、および先端の技術を駆使して、製造プロセスの効率化、業務効率化、チームワーク強化、コスト削減、品質向上を実現します。このサービスは、製造業の課題を深く理解し、それに対する最適なデジタルソリューションを提供することで、企業が持続的な成長とイノベーションを達成できるようサポートします。
オンライン講座
製造業、主に購買・調達部門にお勤めの方々に向けた情報を配信しております。
新任の方やベテランの方、管理職を対象とした幅広いコンテンツをご用意しております。
お問い合わせ
コストダウンが利益に直結する術だと理解していても、なかなか前に進めることができない状況。そんな時は、newjiのコストダウン自動化機能で大きく利益貢献しよう!
(Β版非公開)