- お役立ち記事
- Basics of In-mold Pressure Sensors and Optimization of Molding Processes
Basics of In-mold Pressure Sensors and Optimization of Molding Processes
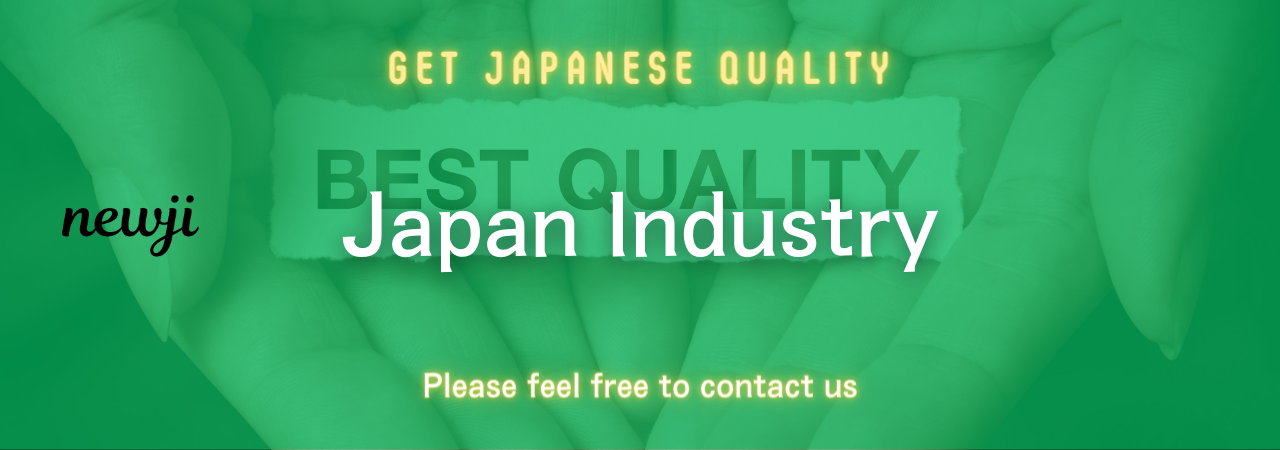
When it comes to ensuring the quality and efficiency of the manufacturing process, understanding the basics of in-mold pressure sensors can make a big difference.
These small but powerful devices play a crucial role in monitoring and optimizing molding processes.
Let’s dive into the world of in-mold pressure sensors and learn how they help improve production.
目次
What Are In-Mold Pressure Sensors?
In-mold pressure sensors are specialized devices used to measure the pressure inside a mold cavity during the injection molding process.
These sensors give real-time feedback on the conditions within the mold.
By measuring pressure, manufacturers can ensure that the molding process is running smoothly and producing high-quality parts.
Types of In-Mold Pressure Sensors
There are several types of in-mold pressure sensors available, each suited to different applications and requirements.
One common type is the piezoelectric sensor, which generates an electric charge in response to changes in pressure.
Another type is the strain gauge sensor, which measures pressure based on the deformation of a material.
Both types provide accurate and reliable readings, essential for process optimization.
Importance of In-Mold Pressure Sensors
Why are in-mold pressure sensors so important?
The answer lies in the benefits they offer.
Firstly, these sensors help improve product quality by providing constant feedback on the molding process.
If the pressure inside the mold deviates from the desired range, the sensors detect this discrepancy and alert the operators, who can then make necessary adjustments.
Secondly, in-mold pressure sensors contribute to process efficiency.
By monitoring the pressure, manufacturers can optimize molding parameters, such as injection speed and cooling time.
This results in reduced cycle times and increased throughput.
How In-Mold Pressure Sensors Work
Understanding how in-mold pressure sensors work involves a look at their components and functionality.
Components of In-Mold Pressure Sensors
In-mold pressure sensors generally consist of a sensing element, an amplifier, and a data processing unit.
The sensing element, which can be piezoelectric or a strain gauge, is placed inside the mold cavity.
It detects pressure changes and converts them into electrical signals.
These signals are then amplified and processed to provide readable data.
Real-Time Monitoring
One of the key features of in-mold pressure sensors is their ability to provide real-time monitoring.
As the injection molding process progresses, the sensors continuously collect data on the pressure within the mold.
This real-time feedback allows operators to quickly identify and address any issues that may arise.
For example, if the pressure readings indicate a potential defect, the operator can halt the process, make adjustments, and resume production, ensuring minimal waste and downtime.
Data Collection and Analysis
In addition to real-time monitoring, in-mold pressure sensors also collect data for later analysis.
This data can be used to identify trends and patterns, which can help in further optimizing the molding process.
By analyzing historical pressure data, manufacturers can fine-tune their processes to achieve better consistency and repeatability.
Optimizing Molding Processes with In-Mold Pressure Sensors
Now that we understand what in-mold pressure sensors are and how they work, let’s explore how these devices can be used to optimize molding processes.
Setting Optimal Parameters
One of the primary ways in-mold pressure sensors help optimize molding processes is by ensuring that the molding parameters are set correctly.
For example, the injection speed, pressure, and cooling time must be carefully controlled to produce high-quality parts.
By monitoring the pressure inside the mold, manufacturers can adjust these parameters in real-time, achieving the best results.
Reducing Cycle Times
Cycle time is a critical factor in the injection molding process.
Shortening the cycle time allows manufacturers to produce more parts in less time, increasing overall productivity.
In-mold pressure sensors help achieve this by providing real-time feedback on the molding process.
By quickly identifying and addressing issues, manufacturers can reduce the time required for each cycle, leading to increased throughput.
Preventing Defects
Defects in molded parts can lead to significant waste and rework, impacting profitability.
In-mold pressure sensors play a vital role in preventing defects by continuously monitoring the pressure within the mold.
If the pressure deviates from the desired range, the sensors alert the operators, who can then make the necessary adjustments.
This proactive approach helps ensure that each part meets quality standards, reducing the likelihood of defects.
Improving Consistency and Repeatability
Consistency and repeatability are essential for achieving high-quality parts in the injection molding process.
In-mold pressure sensors contribute to this by providing accurate and reliable pressure readings.
By using these readings to fine-tune the molding parameters, manufacturers can achieve consistent results across multiple production runs.
This not only improves product quality but also enhances customer satisfaction.
Conclusion
In-mold pressure sensors are powerful tools that play a crucial role in monitoring and optimizing the injection molding process.
By providing real-time feedback on the pressure within the mold, these sensors help improve product quality, increase efficiency, and reduce waste.
Whether setting optimal parameters, reducing cycle times, preventing defects, or improving consistency and repeatability, in-mold pressure sensors are indispensable for achieving the best results in injection molding.
Understanding the basics of these sensors and how they work is the first step towards mastering the molding process and reaping the benefits they offer.
資料ダウンロード
QCD調達購買管理クラウド「newji」は、調達購買部門で必要なQCD管理全てを備えた、現場特化型兼クラウド型の今世紀最高の購買管理システムとなります。
ユーザー登録
調達購買業務の効率化だけでなく、システムを導入することで、コスト削減や製品・資材のステータス可視化のほか、属人化していた購買情報の共有化による内部不正防止や統制にも役立ちます。
NEWJI DX
製造業に特化したデジタルトランスフォーメーション(DX)の実現を目指す請負開発型のコンサルティングサービスです。AI、iPaaS、および先端の技術を駆使して、製造プロセスの効率化、業務効率化、チームワーク強化、コスト削減、品質向上を実現します。このサービスは、製造業の課題を深く理解し、それに対する最適なデジタルソリューションを提供することで、企業が持続的な成長とイノベーションを達成できるようサポートします。
オンライン講座
製造業、主に購買・調達部門にお勤めの方々に向けた情報を配信しております。
新任の方やベテランの方、管理職を対象とした幅広いコンテンツをご用意しております。
お問い合わせ
コストダウンが利益に直結する術だと理解していても、なかなか前に進めることができない状況。そんな時は、newjiのコストダウン自動化機能で大きく利益貢献しよう!
(Β版非公開)