- お役立ち記事
- Practice of FMEA (Failure Mode and Effects Analysis) for quality trouble prevention in manufacturing
Practice of FMEA (Failure Mode and Effects Analysis) for quality trouble prevention in manufacturing
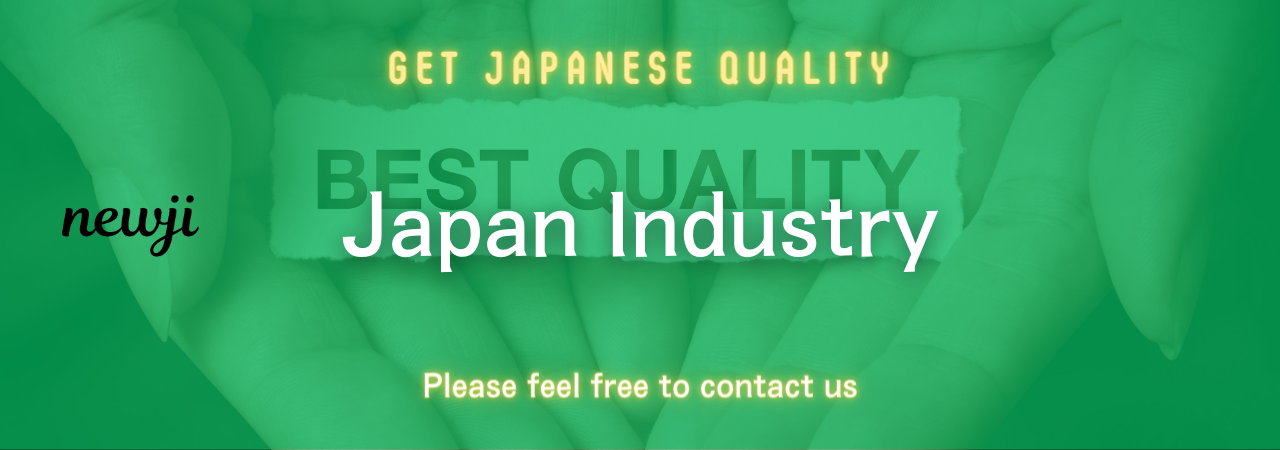
Failure Mode and Effects Analysis (FMEA) is a valuable tool used in manufacturing to improve quality and prevent defects.
By identifying potential problems before they occur, FMEA helps reduce costs and enhance the reliability of products.
In this article, we will discuss the basics of FMEA and how it can be effectively practiced to prevent quality issues in manufacturing.
目次
What is FMEA?
Failure Mode and Effects Analysis, commonly known as FMEA, is a structured approach used to identify potential failure modes, their causes, and their effects on a system or process.
It is a proactive method for risk assessment and management, which involves systematically reviewing components, assemblies, or processes to pinpoint areas of possible failure.
Types of FMEA
There are different types of FMEA that can be used depending on the focus of the analysis:
1. **Design FMEA (DFMEA):** This type focuses on potential failures in the design phase of the product or system.
2. **Process FMEA (PFMEA):** This type evaluates potential failures in the manufacturing or assembly process.
3. **System FMEA:** This is used to analyze higher-level systems and their subsystems.
Key Steps in Performing FMEA
Implementing FMEA involves several crucial steps to ensure a thorough analysis and effective outcomes.
Here’s a detailed guide on how to perform FMEA:
1. Define the Scope
Clearly outline the boundaries of the analysis.
Determine which process, product, or system you will evaluate and understand its function and limitations.
Defining the scope helps keep the analysis focused and manageable.
2. Assemble a Team
Gather a multidisciplinary team consisting of individuals with diverse knowledge about the process, product, or system.
Include engineers, designers, operators, and anyone who can provide valuable insights.
The collective expertise will enhance the identification and resolution of potential failure modes.
3. Identify Potential Failure Modes
Brainstorm possible ways the item can fail.
Document each failure mode, which can be anything that causes the product or process to not perform as intended.
Use tools like brainstorming sessions, historical data, and checklists to ensure comprehensive coverage.
4. Determine the Effects and Causes
For each identified failure mode, describe the possible effects on the end user, product, or process.
Understand the severity of these effects.
Next, identify the root causes of each failure mode.
Knowing the causes helps in developing effective mitigation plans.
5. Assign Severity, Occurrence, and Detection Rankings
Evaluate each failure mode and assign numerical rankings based on three criteria:
– Severity (S):The seriousness of the failure mode’s consequences.
– Occurrence (O): The likelihood of the failure mode happening.
– Detection (D): The probability of detecting the failure before it reaches the customer.
The rankings usually range from 1 to 10, where 1 indicates low risk and 10 represents high risk.
6. Calculate the Risk Priority Number (RPN)
Multiply the severity, occurrence, and detection rankings to calculate the Risk Priority Number (RPN) for each failure mode.
RPN = S × O × D.
The RPN helps prioritize which failure modes need urgent attention and mitigation.
7. Develop Action Plans
For high RPN failure modes, create action plans to reduce or eliminate the risk.
Options include redesigning components, changing process parameters, improving detection methods, or providing additional training.
Ensure each action plan is assigned to a responsible person and given a timeline for completion.
8. Implement and Review
Put the action plans into practice.
Monitor the process to confirm that the measures taken are effective.
Recalculate the RPN after implementing corrective actions to see if the risk has been reduced.
Continuous monitoring and re-evaluation are essential to maintaining quality over time.
Benefits of Practicing FMEA
Implementing FMEA offers numerous advantages to manufacturing organizations:
Improved Product Quality
By systematically identifying failure modes and taking preventive measures, FMEA enhances the overall quality and reliability of products.
Customers are less likely to experience defects, leading to higher satisfaction and brand loyalty.
Cost Savings
Proactively identifying and addressing potential issues reduces the likelihood of costly recalls, warranty claims, and rework.
This approach saves resources and minimizes the financial impact of defects.
Enhanced Safety
FMEA helps identify potential safety hazards associated with a product or process.
Addressing these risks beforehand protects both consumers and employees, fostering a safe environment.
Compliance with Standards
Many industries have stringent quality and safety standards.
Practicing FMEA enables organizations to meet regulatory requirements and industry standards, reducing the risk of non-compliance penalties.
Improved Communication and Collaboration
Involving a multidisciplinary team in the FMEA process promotes open communication and collaboration.
Different perspectives lead to more comprehensive risk assessments and innovative solutions.
Challenges in FMEA
While FMEA is beneficial, it is not without challenges:
Time-Consuming
Conducting a thorough FMEA can be time-consuming, particularly for complex systems or processes.
Dedicated time and resources are necessary to complete the analysis effectively.
Requires Experienced Personnel
An effective FMEA relies on the expertise and experience of the team members.
Without knowledgeable contributors, crucial failure modes may be overlooked.
Ensuring the right mix of skills and experience is essential.
Maintaining Updated Analyses
FMEAs need continuous updates as processes, designs, or systems evolve.
Organizations must establish procedures for revisiting and revising FMEA documents to keep them relevant.
Conclusion
Failure Mode and Effects Analysis (FMEA) is a proven methodology for enhancing quality and preventing defects in manufacturing.
By systematically identifying and addressing potential failure modes, organizations can improve product reliability, save costs, enhance safety, and achieve compliance with industry standards.
Despite the challenges, the benefits of practicing FMEA far outweigh the obstacles.
With a clear understanding of FMEA and a commitment to continuous improvement, manufacturing organizations can achieve outstanding quality and reliability in their processes and products.
資料ダウンロード
QCD調達購買管理クラウド「newji」は、調達購買部門で必要なQCD管理全てを備えた、現場特化型兼クラウド型の今世紀最高の購買管理システムとなります。
ユーザー登録
調達購買業務の効率化だけでなく、システムを導入することで、コスト削減や製品・資材のステータス可視化のほか、属人化していた購買情報の共有化による内部不正防止や統制にも役立ちます。
NEWJI DX
製造業に特化したデジタルトランスフォーメーション(DX)の実現を目指す請負開発型のコンサルティングサービスです。AI、iPaaS、および先端の技術を駆使して、製造プロセスの効率化、業務効率化、チームワーク強化、コスト削減、品質向上を実現します。このサービスは、製造業の課題を深く理解し、それに対する最適なデジタルソリューションを提供することで、企業が持続的な成長とイノベーションを達成できるようサポートします。
オンライン講座
製造業、主に購買・調達部門にお勤めの方々に向けた情報を配信しております。
新任の方やベテランの方、管理職を対象とした幅広いコンテンツをご用意しております。
お問い合わせ
コストダウンが利益に直結する術だと理解していても、なかなか前に進めることができない状況。そんな時は、newjiのコストダウン自動化機能で大きく利益貢献しよう!
(Β版非公開)