- お役立ち記事
- DX of electroless plating process improves uniformity and adhesion
DX of electroless plating process improves uniformity and adhesion
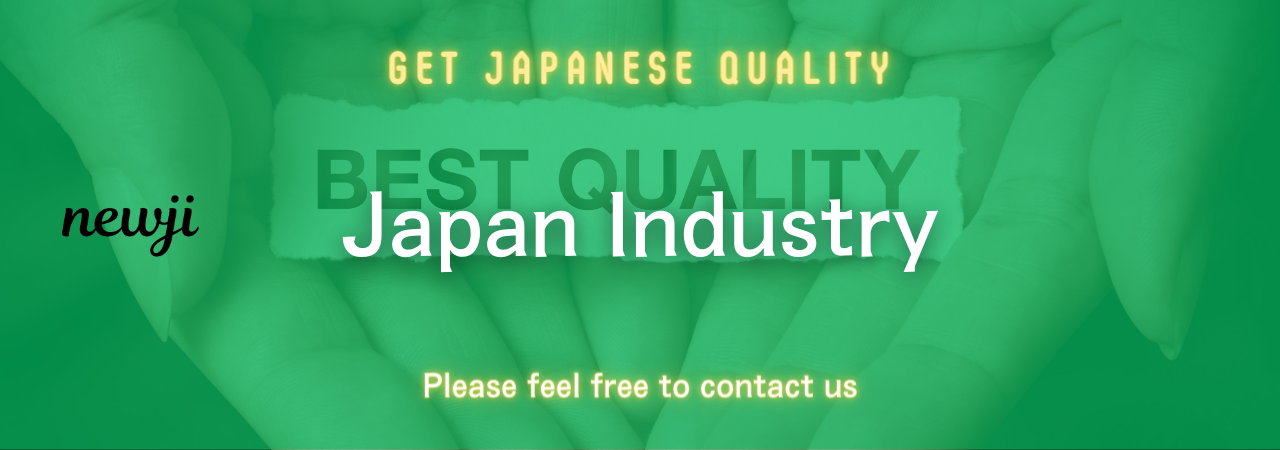
The world of electroless plating is continuously evolving, and with the introduction of digital transformation (DX), significant improvements can be achieved. For those unfamiliar, electroless plating is a method used to deposit a metal coating on a substrate without the use of electrical current. This process is crucial in various industries, including electronics, automotive, and aerospace. Let’s dive into how DX is revolutionizing the electroless plating process, enhancing uniformity and adhesion.
目次
Understanding Electroless Plating
Electroless plating, also known as autocatalytic plating, involves using a chemical bath to deposit metals on a substrate. Unlike electroplating, this method does not require electrical power. The process mainly relies on oxidation and reduction reactions, which makes it highly versatile. Metals like nickel, copper, and gold are commonly used in electroless plating.
The Importance of Uniformity and Adhesion
Uniformity in electroless plating ensures that the metal layer is evenly distributed over the substrate. This consistency is crucial for maintaining the functionality and aesthetics of the coated product. Poor adhesion can lead to peeling, flaking, or outright failure of the metal coating. High-quality adhesion ensures that the metal layer stays firmly attached to the substrate, enhancing durability and performance.
How Digital Transformation (DX) is Enhancing the Process
Digital transformation involves integrating digital technology into various business processes. In the context of electroless plating, DX leverages data analytics, automation, and advanced monitoring systems to improve outcomes.
Real-time Monitoring and Control
One of the significant benefits of DX is real-time monitoring of the plating process. Sensors and IoT (Internet of Things) devices can be installed to continuously measure factors such as temperature, pH, and chemical concentration in the plating bath. This data is then analyzed to ensure the optimal conditions are maintained, which directly contributes to enhanced uniformity and adhesion.
Predictive Maintenance
DX also enables predictive maintenance, which helps in identifying potential issues before they become major problems. By analyzing data from previous plating sessions, it is possible to predict when equipment or chemical bath needs maintenance. This proactive approach ensures that the plating process is not interrupted, thereby maintaining high levels of uniformity and adhesion.
Enhanced Process Automation
Automation driven by DX can streamline the entire plating process. Automated systems can mix chemical baths with precision, monitor environmental conditions, and even adjust parameters in real-time. This level of control ensures that the plating process runs smoothly, consistently producing high-quality results.
Benefits of DX in Electroless Plating
The integration of digital technologies into the electroless plating process offers numerous benefits.
Increased Efficiency
By automating many aspects of the plating process, companies can increase production efficiency. Automation reduces the need for manual intervention, thereby minimizing human error and speeding up the overall process.
Improved Quality Control
With real-time monitoring and data analysis, companies can achieve exceptional levels of quality control. Any deviations from the optimal parameters can be quickly identified and corrected, ensuring that each batch meets the highest standards.
Cost Savings
Although implementing DX requires an initial investment, the long-term cost savings are significant. Predictive maintenance reduces downtime and repair costs, while increased efficiency and reduced waste lower production costs. These savings can be reinvested to further enhance the plating process.
Environmental Benefits
DX can also aid in making the electroless plating process more environmentally friendly. By closely monitoring and controlling the chemical baths, companies can reduce the amount of waste produced. Moreover, predictive maintenance ensures that equipment runs efficiently, minimizing energy consumption.
Case Studies and Success Stories
Several companies have successfully integrated DX into their electroless plating processes, yielding impressive results.
Case Study: A Leading Electronics Manufacturer
A leading electronics manufacturer integrated IoT sensors and data analytics into their electroless plating process. The real-time data allowed them to maintain optimal conditions consistently. Consequently, they saw a significant improvement in the uniformity and adhesion of their metal coatings. Additionally, their production efficiency improved by 20%, and they reduced waste by 15%.
Case Study: Automotive Component Supplier
An automotive component supplier utilized predictive maintenance and process automation. By analyzing historical data, they could predict maintenance needs accurately. This approach eliminated unexpected downtimes, enhancing production efficiency and product quality. Their investment in DX paid off within a year, thanks to the cost savings and improved performance.
The Future of Electroless Plating with DX
The future of electroless plating looks promising, especially with the continued advancements in digital technology.
AI and Machine Learning
Artificial Intelligence (AI) and machine learning can further enhance the electroless plating process. These technologies can analyze vast amounts of data to identify patterns and optimize the plating parameters automatically. This capability can lead to even greater improvements in uniformity and adhesion.
Blockchain for Transparency
Blockchain technology can be used to ensure transparency in the supply chain. By keeping an immutable record of every step in the plating process, companies can verify the quality and integrity of their products. This transparency can improve customer trust and satisfaction.
Conclusion
Digital transformation is undeniably revolutionizing the electroless plating process. By leveraging real-time monitoring, predictive maintenance, and advanced automation, companies can achieve unprecedented levels of uniformity and adhesion. The benefits extend beyond the plating process, offering increased efficiency, cost savings, and environmental benefits. As digital technologies continue to evolve, the future holds even more exciting possibilities for the electroless plating industry.
資料ダウンロード
QCD調達購買管理クラウド「newji」は、調達購買部門で必要なQCD管理全てを備えた、現場特化型兼クラウド型の今世紀最高の購買管理システムとなります。
ユーザー登録
調達購買業務の効率化だけでなく、システムを導入することで、コスト削減や製品・資材のステータス可視化のほか、属人化していた購買情報の共有化による内部不正防止や統制にも役立ちます。
NEWJI DX
製造業に特化したデジタルトランスフォーメーション(DX)の実現を目指す請負開発型のコンサルティングサービスです。AI、iPaaS、および先端の技術を駆使して、製造プロセスの効率化、業務効率化、チームワーク強化、コスト削減、品質向上を実現します。このサービスは、製造業の課題を深く理解し、それに対する最適なデジタルソリューションを提供することで、企業が持続的な成長とイノベーションを達成できるようサポートします。
オンライン講座
製造業、主に購買・調達部門にお勤めの方々に向けた情報を配信しております。
新任の方やベテランの方、管理職を対象とした幅広いコンテンツをご用意しております。
お問い合わせ
コストダウンが利益に直結する術だと理解していても、なかなか前に進めることができない状況。そんな時は、newjiのコストダウン自動化機能で大きく利益貢献しよう!
(Β版非公開)