- お役立ち記事
- Optimal allocation of logistics bases in international procurement: Factors to be considered by procurement and purchasing departments in manufacturing companies
Optimal allocation of logistics bases in international procurement: Factors to be considered by procurement and purchasing departments in manufacturing companies
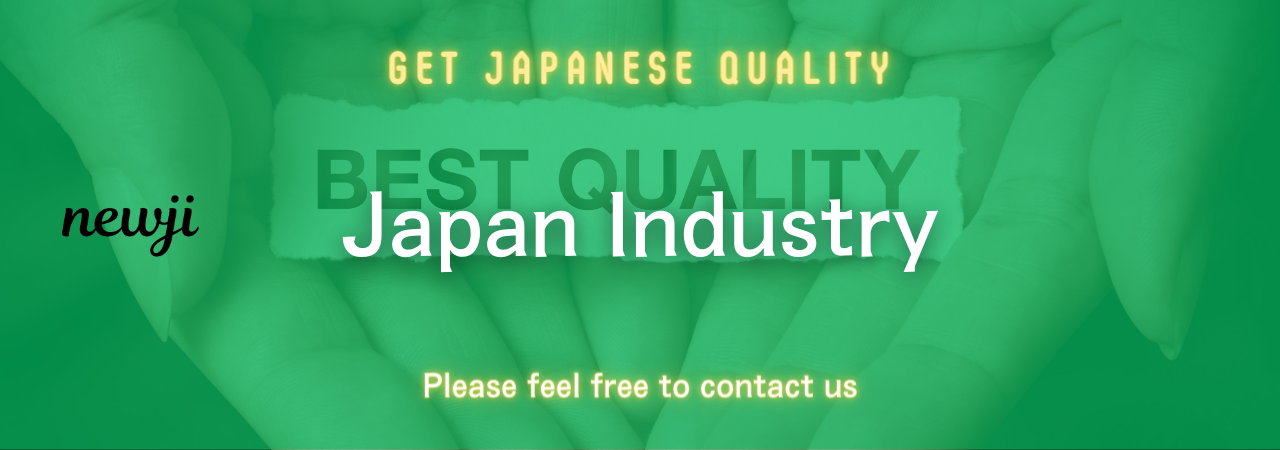
目次
Introduction to International Procurement
In today’s globalized economy, manufacturing companies often rely on international procurement to meet their production needs.
The procurement and purchasing departments play a critical role in sourcing raw materials and components from different parts of the world.
With many elements to consider, optimizing the allocation of logistics bases is vital for efficiency and cost-effectiveness.
Importance of Logistics Bases
Logistics bases, including warehouses, distribution centers, and ports, are essential for storing and distributing goods.
Their strategic location can greatly impact the overall supply chain performance.
For instance, a well-placed logistics base can reduce transit times, minimize costs, and improve supply chain resilience.
Geographical Considerations
The geographical location of logistics bases is a fundamental factor in international procurement.
Proximity to suppliers and customers can significantly affect transportation costs and delivery times.
If a manufacturing company sources raw materials from Asia but primarily serves customers in Europe, it would be strategic to have a logistics base somewhere in between these regions.
Locations like the Middle East or Central Asia could serve as ideal hubs.
Access to Transportation Infrastructure
Transportation infrastructure, such as highways, railroads, and ports, is another crucial consideration.
Logistics bases need to be accessible to these transportation modes to facilitate the smooth movement of goods.
A warehouse located near a major port can expedite international shipping processes, while one near rail or highway networks can speed up domestic transportation.
Local Regulations and Trade Policies
Navigating local regulations and trade policies is imperative for international procurement.
Different countries have varying import/export regulations, tariffs, and trade agreements.
These factors can profoundly impact the cost and complexity of moving goods across borders.
A logistics base in a country with favorable trade agreements and streamlined customs procedures can be advantageous.
Cost Factors
Cost is always a key consideration in the procurement field.
Several cost factors must be evaluated when establishing logistics bases.
Real Estate and Facility Costs
The cost of real estate and facilities varies significantly from one region to another.
Urban locations may offer better connectivity but generally come with higher real estate costs.
On the other hand, rural or less developed areas might be more cost-effective but could lack essential infrastructure.
Labor Costs and Availability
Labor costs and availability are also crucial in determining the location of logistics bases.
Regions with a skilled yet inexpensive labor force can offer cost advantages.
However, procurement departments must also consider the availability of labor.
A location with low labor costs but a shortage of skilled workers may not be ideal.
Transportation and Fuel Costs
Proximity to major transport routes and fuel costs are critical components of overall logistics costs.
Choosing a logistics base near principal transit corridors can minimize transportation expenses.
Additionally, fluctuating fuel prices should be factored into the decision-making process to ensure long-term affordability.
Technological Infrastructure
Technological advancements are transforming the logistics industry.
Manufacturing companies must consider the technological infrastructure available in potential locations for their logistics bases.
Availability of Modern Warehousing Solutions
Modern warehousing solutions, such as automated storage and retrieval systems (AS/RS), can significantly enhance efficiency and reduce operational costs.
Regions with advanced technological infrastructure are more likely to support such innovations.
Connectivity and Communication
High-speed internet and robust communication networks are essential for real-time tracking and management of goods.
Locations with excellent connectivity can facilitate better coordination and data sharing among various stakeholders in the supply chain.
Environmental and Sustainability Factors
Sustainability is becoming an increasingly important consideration for businesses globally.
Manufacturing companies must factor in environmental considerations when determining the optimal allocation of logistics bases.
Carbon Footprint
The carbon footprint associated with transportation and warehousing operations is a key consideration.
Choosing locations that minimize transportation distances can reduce carbon emissions.
Additionally, logistics bases that use renewable energy sources can further enhance a company’s sustainability profile.
Compliance with Environmental Regulations
Global environmental regulations are becoming stricter.
Companies need to ensure that their logistics operations comply with these regulations.
Locations with stringent environmental policies may promote better practices and sustainability.
Risk Management and Resilience
In an unpredictable global market, risk management is crucial.
Manufacturing companies must consider the resilience of their logistics operations.
Political Stability
Political stability in the host country is a critical factor.
Regions with frequent political turmoil can disrupt supply chains.
Procurement teams should prioritize locations with stable governance to ensure uninterrupted operations.
Natural Disasters and Climate Risks
Natural disasters and climate-related events can severely impact logistics operations.
Evaluating the susceptibility of potential locations to such risks is essential.
Companies must have contingency plans in place to address disruptions caused by natural events.
Conclusion
Optimizing the allocation of logistics bases in international procurement requires careful consideration of numerous factors.
Geographical location, cost, technological infrastructure, environmental impact, and risk management all play pivotal roles.
By systematically evaluating these aspects, procurement and purchasing departments in manufacturing companies can enhance efficiency, reduce costs, and build resilient supply chains.
With a well-thought-out logistics strategy, companies can achieve greater success in the competitive global marketplace.
資料ダウンロード
QCD調達購買管理クラウド「newji」は、調達購買部門で必要なQCD管理全てを備えた、現場特化型兼クラウド型の今世紀最高の購買管理システムとなります。
ユーザー登録
調達購買業務の効率化だけでなく、システムを導入することで、コスト削減や製品・資材のステータス可視化のほか、属人化していた購買情報の共有化による内部不正防止や統制にも役立ちます。
NEWJI DX
製造業に特化したデジタルトランスフォーメーション(DX)の実現を目指す請負開発型のコンサルティングサービスです。AI、iPaaS、および先端の技術を駆使して、製造プロセスの効率化、業務効率化、チームワーク強化、コスト削減、品質向上を実現します。このサービスは、製造業の課題を深く理解し、それに対する最適なデジタルソリューションを提供することで、企業が持続的な成長とイノベーションを達成できるようサポートします。
オンライン講座
製造業、主に購買・調達部門にお勤めの方々に向けた情報を配信しております。
新任の方やベテランの方、管理職を対象とした幅広いコンテンツをご用意しております。
お問い合わせ
コストダウンが利益に直結する術だと理解していても、なかなか前に進めることができない状況。そんな時は、newjiのコストダウン自動化機能で大きく利益貢献しよう!
(Β版非公開)