- お役立ち記事
- DX success story in the furniture industry – Improving operational efficiency through cloud system and AI utilization
月間76,176名の
製造業ご担当者様が閲覧しています*
*2025年3月31日現在のGoogle Analyticsのデータより
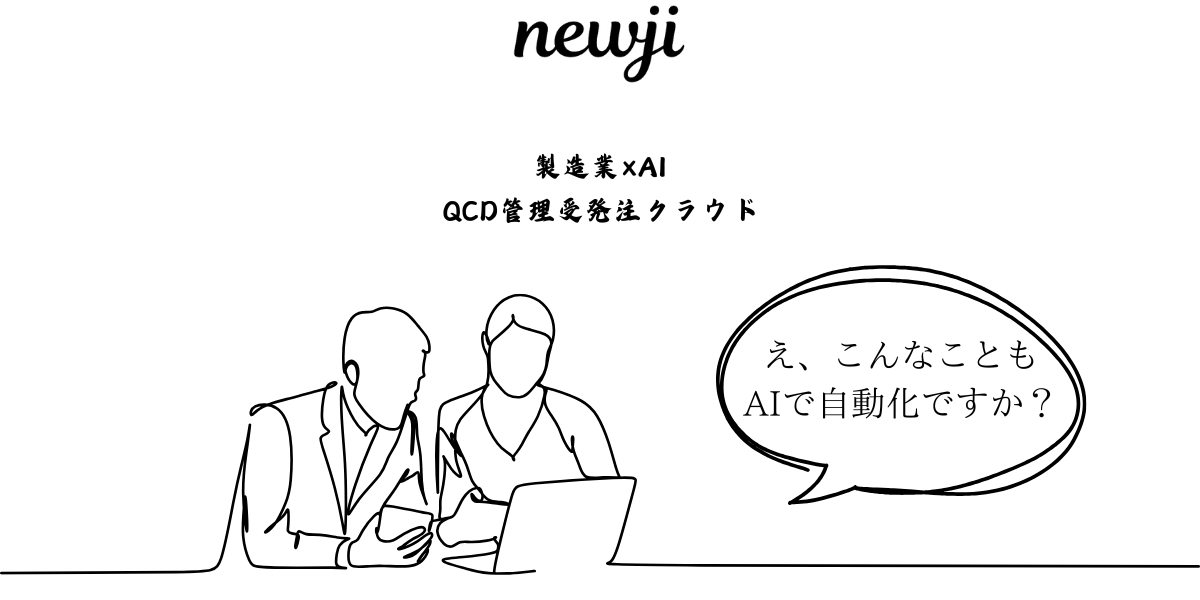
DX success story in the furniture industry – Improving operational efficiency through cloud system and AI utilization
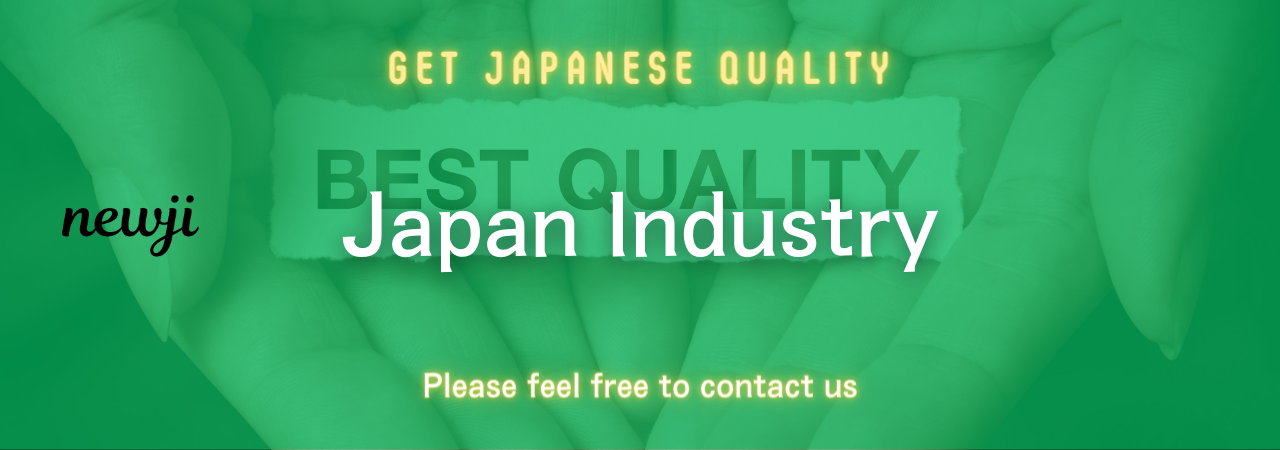
目次
Introduction to Digital Transformation in the Furniture Industry
The furniture industry, like many other sectors, is undergoing a remarkable transformation in the digital age.
The integration of new technologies such as cloud systems and artificial intelligence (AI) is paving the way for significant improvements in operational efficiency.
As competition intensifies and consumer expectations continue to rise, companies in this industry are looking for innovative solutions to stay ahead.
Digital transformation, or DX, is proving to be a game-changer, providing businesses with the tools they need to optimize processes and enhance productivity.
The Role of Cloud Systems
Cloud computing has revolutionized the way businesses operate by offering scalable and flexible solutions.
For the furniture industry, cloud systems enable companies to manage operations more effectively across all areas, from inventory to customer service.
With data stored in the cloud, employees can access information from anywhere, at any time, encouraging collaboration and quick decision-making.
One of the key benefits of cloud systems is cost reduction.
Companies no longer need to invest heavily in physical infrastructure, such as servers and storage devices.
Instead, they can leverage cloud services, which offer a pay-as-you-go model, reducing upfront costs and ensuring that they only pay for the resources they use.
This model is particularly beneficial for small and medium-sized enterprises (SMEs) in the furniture industry, which may have limited budgets.
Moreover, cloud systems support seamless integration with other digital tools and platforms.
For instance, they can easily connect with e-commerce sites and customer relationship management (CRM) systems, streamlining operations and enhancing the customer experience.
AI: A Catalyst for Operational Efficiency
Artificial intelligence is another powerful tool that is driving operational efficiency in the furniture industry.
AI technologies, such as machine learning and predictive analytics, help businesses make data-driven decisions, optimize processes, and predict future trends.
In the realm of manufacturing, AI can automate complex processes, leading to faster production times and improved product quality.
For example, AI-powered robots can handle repetitive tasks, freeing up human workers to focus on more strategic endeavors.
This not only boosts productivity but also enhances employee satisfaction by reducing physical strain.
Inventory management is another area where AI is making a significant impact.
Traditional inventory systems often involve manual checks and balances, which can be time-consuming and error-prone.
AI, on the other hand, provides real-time insights into inventory levels, helping businesses manage stock more efficiently and reduce waste.
Predictive analytics allows companies to forecast demand accurately, ensuring that they have the right products available when and where needed.
Case Study: A Success Story in the Furniture Industry
Consider the case of a mid-sized furniture manufacturer that embarked on a digital transformation journey.
By integrating cloud systems and AI into their operations, they were able to achieve remarkable results.
Initially, the company faced challenges with inventory management and order fulfillment.
Their reliance on manual processes often led to delayed shipments and dissatisfied customers.
By adopting a cloud-based inventory management system, the company gained real-time visibility into stock levels across all locations.
They could quickly identify which products were in high demand and adjust their production schedule accordingly.
This led to a reduction in overstock and stockouts, improving overall efficiency.
Simultaneously, the company implemented AI-powered tools to enhance their production line.
Automated quality control checks reduced the margin for error, while machine learning algorithms optimized the use of raw materials, minimizing waste.
The results were impressive.
The company saw a 30% reduction in inventory costs and a 20% increase in production efficiency.
Customer satisfaction improved due to faster delivery times and consistent product quality.
Overcoming Challenges in Digital Transformation
Despite the clear benefits, transitioning to a digital-first approach is not without its challenges.
Companies may face initial resistance from employees who are accustomed to traditional methods.
It is crucial for businesses to invest in training and change management to ensure a smooth transition.
Additionally, data security is a concern that needs to be addressed.
With sensitive company information and customer data being stored in the cloud, businesses must implement robust security measures to protect against cyber threats.
Moreover, choosing the right technology partners is vital.
Not all cloud and AI solutions are created equal, and businesses should conduct thorough research to identify platforms that align with their specific needs and goals.
Future Prospects of Digital Transformation in the Furniture Industry
Looking ahead, the future of digital transformation in the furniture industry is promising.
As technologies continue to evolve, companies that embrace digital solutions will be better positioned to compete in a rapidly changing market.
Personalization, augmented reality (AR), and virtual reality (VR) are some emerging trends that could further enhance the customer experience, allowing consumers to visualize products in their own space before making a purchase.
In conclusion, digital transformation is no longer a luxury but a necessity for the furniture industry.
Leveraging cloud systems and AI opens up a world of possibilities for improving operational efficiency, reducing costs, and enhancing customer satisfaction.
By embracing these technologies, furniture companies can not only survive but thrive in the digital age.
資料ダウンロード
QCD管理受発注クラウド「newji」は、受発注部門で必要なQCD管理全てを備えた、現場特化型兼クラウド型の今世紀最高の受発注管理システムとなります。
ユーザー登録
受発注業務の効率化だけでなく、システムを導入することで、コスト削減や製品・資材のステータス可視化のほか、属人化していた受発注情報の共有化による内部不正防止や統制にも役立ちます。
NEWJI DX
製造業に特化したデジタルトランスフォーメーション(DX)の実現を目指す請負開発型のコンサルティングサービスです。AI、iPaaS、および先端の技術を駆使して、製造プロセスの効率化、業務効率化、チームワーク強化、コスト削減、品質向上を実現します。このサービスは、製造業の課題を深く理解し、それに対する最適なデジタルソリューションを提供することで、企業が持続的な成長とイノベーションを達成できるようサポートします。
製造業ニュース解説
製造業、主に購買・調達部門にお勤めの方々に向けた情報を配信しております。
新任の方やベテランの方、管理職を対象とした幅広いコンテンツをご用意しております。
お問い合わせ
コストダウンが利益に直結する術だと理解していても、なかなか前に進めることができない状況。そんな時は、newjiのコストダウン自動化機能で大きく利益貢献しよう!
(β版非公開)