- お役立ち記事
- Residual stress generation mechanism and fatigue strength improvement and utilization technology
月間76,176名の
製造業ご担当者様が閲覧しています*
*2025年3月31日現在のGoogle Analyticsのデータより
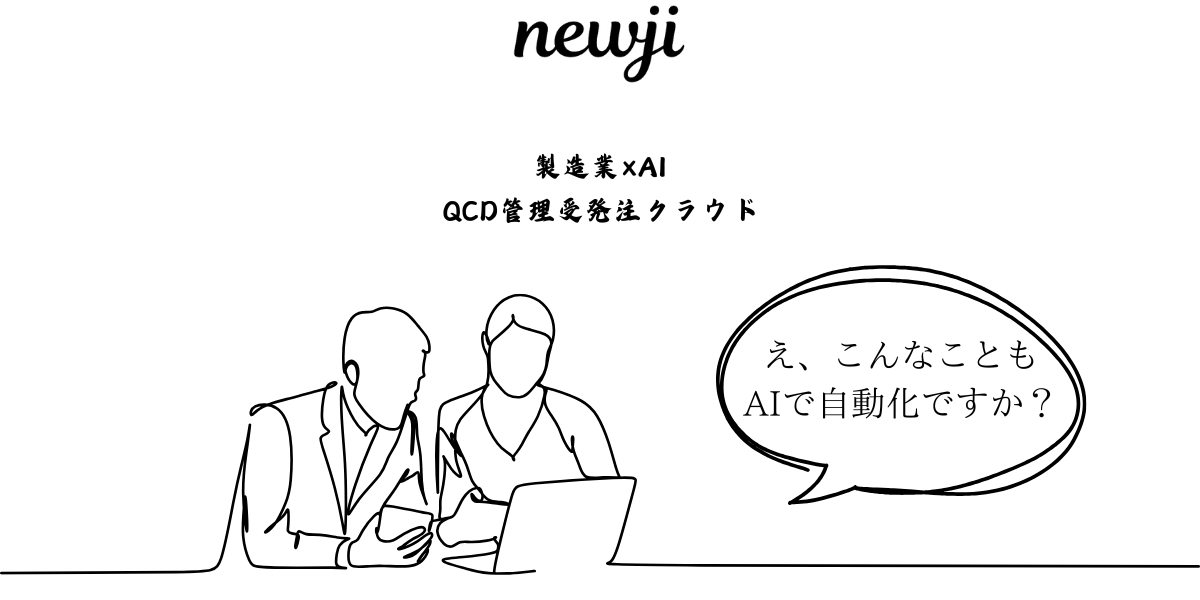
Residual stress generation mechanism and fatigue strength improvement and utilization technology
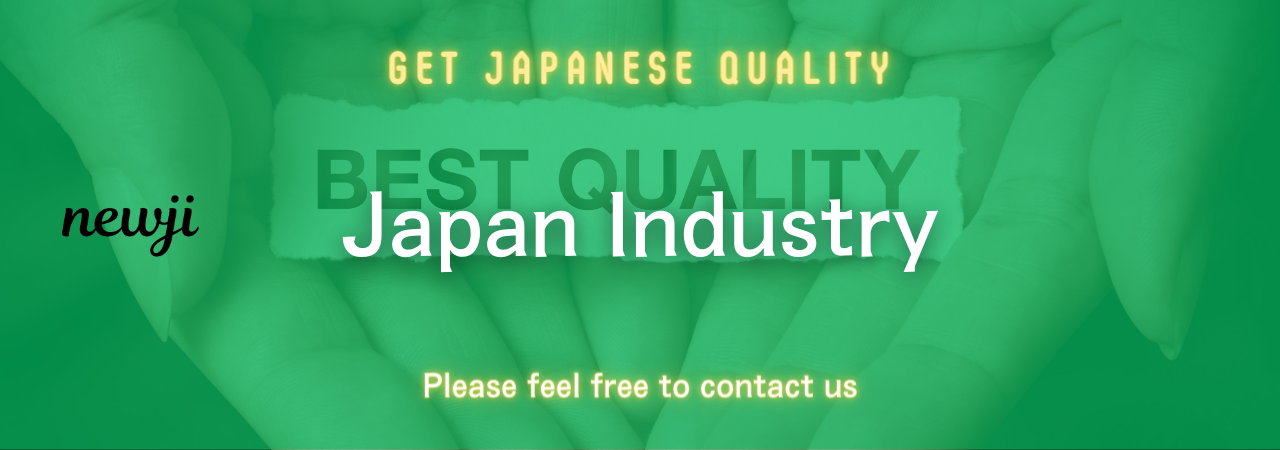
目次
Understanding Residual Stress
Residual stress is a concept that refers to the stress left in materials after they have undergone manufacturing processes, such as welding, casting, or machining.
These stresses remain within the material even when external forces are removed.
Residual stress can have both beneficial and detrimental effects on materials and structural components.
Residual stresses are generated due to the differential volume changes occurring during processes like cooling or phase transformations.
For instance, when metal parts cool, they contract.
If different parts of a component cool at different rates, it can result in uneven contraction, causing residual stress.
Mechanisms of Residual Stress Generation
One primary mechanism for residual stress generation is thermal expansion and contraction.
When a material is heated, it expands, and when cooled, it contracts.
These volume changes can lead to residual stresses, especially when cooling is non-uniform.
Another mechanism is phase transformation.
In some materials, such as steels, different phases have different densities.
When phase transformation occurs, changes in volume can lead to residual stresses.
Mechanical deformation is another way residual stresses are introduced.
When a material is subjected to plastic deformation, parts of it may have deformed plastically, while adjacent areas remain elastic.
This elastic-plastic mismatch can result in residual stresses.
Importance of Residual Stress
Residual stress can significantly affect the mechanical properties of materials.
It can improve fatigue strength, increase resistance to cracking, and enhance overall durability.
However, it can also lead to undesirable outcomes like warping or premature failure if not appropriately managed.
In certain engineering applications, beneficial residual stresses are intentionally introduced to improve performance.
For example, in shot peening, compressive residual stresses are induced on the surface of components to enhance fatigue strength.
In contrast, tensile residual stresses are generally considered harmful as they can lead to cracking or stress corrosion cracking.
Utilization of Residual Stress
Residual stress management is crucial in industries like aerospace, automotive, and construction, where material failure can have catastrophic consequences.
Understanding and controlling residual stresses help in designing components that are more durable and reliable.
Methods to Control Residual Stress
Several techniques have been developed to control and utilize residual stresses effectively.
One common method is thermal treatment, such as stress relief annealing.
This process involves heating the material to a specific temperature and then gradually cooling it.
It helps redistribute residual stresses, reducing their magnitude.
Mechanical methods like shot peening and surface rolling are used to introduce beneficial compressive residual stresses on material surfaces.
These processes improve fatigue life by making it more difficult for cracks to initiate and propagate.
Another approach is to use post-weld heat treatment.
This minimizes welding-induced residual stresses, enhancing the structural integrity of welded joints.
Improving Fatigue Strength
Improving fatigue strength is vital for components subjected to cyclic loading.
Fatigue failures often start at microscopic flaws or surface irregularities where tensile stresses are concentrated.
Strategies for Enhancing Fatigue Strength
Several strategies are employed to improve fatigue strength, many of which revolve around managing residual stresses.
Shot peening, as mentioned earlier, is widely used to introduce beneficial compressive stresses.
These stresses inhibit the initiation and propagation of surface cracks, greatly extending the fatigue life of components.
Induction hardening is another technique.
It involves heating the surface of a component using induction coils and then rapidly cooling it.
This process increases surface hardness and introduces compressive residual stresses, enhancing fatigue resistance.
Surface coatings and treatments, such as nitriding or carburizing, can also improve fatigue strength by creating a hardened surface layer with compressive stresses.
Technological Advances in Residual Stress Management
With technological advancements, residual stress management has seen significant improvements.
Modern Techniques and Tools
Non-destructive evaluation (NDE) techniques have progressed, allowing more accurate measurement of residual stresses without damaging components.
Methods like X-ray diffraction, neutron diffraction, and ultrasonic techniques are used to measure and map residual stresses, providing valuable insights into how they affect material performance.
Finite element modeling (FEM) has become an essential tool in predicting residual stress distributions.
It allows engineers to simulate manufacturing processes and understand how residual stresses develop, enabling more informed design decisions.
Additive manufacturing, or 3D printing, has introduced new challenges and opportunities in residual stress management.
Controlling residual stresses in 3D printed components is crucial for their structural integrity.
Researchers are exploring innovative methods to manage these stresses, including in-situ stress measurement and control during the printing process.
Conclusion
Residual stress management is a complex but vital aspect of material engineering.
Understanding the mechanisms of residual stress generation and utilizing technologies to control and leverage these stresses can significantly improve fatigue strength and material performance.
Through continual technological advancements and innovative approaches, industries can achieve more reliable and durable components, enhancing safety and efficiency in various applications.
資料ダウンロード
QCD管理受発注クラウド「newji」は、受発注部門で必要なQCD管理全てを備えた、現場特化型兼クラウド型の今世紀最高の受発注管理システムとなります。
ユーザー登録
受発注業務の効率化だけでなく、システムを導入することで、コスト削減や製品・資材のステータス可視化のほか、属人化していた受発注情報の共有化による内部不正防止や統制にも役立ちます。
NEWJI DX
製造業に特化したデジタルトランスフォーメーション(DX)の実現を目指す請負開発型のコンサルティングサービスです。AI、iPaaS、および先端の技術を駆使して、製造プロセスの効率化、業務効率化、チームワーク強化、コスト削減、品質向上を実現します。このサービスは、製造業の課題を深く理解し、それに対する最適なデジタルソリューションを提供することで、企業が持続的な成長とイノベーションを達成できるようサポートします。
製造業ニュース解説
製造業、主に購買・調達部門にお勤めの方々に向けた情報を配信しております。
新任の方やベテランの方、管理職を対象とした幅広いコンテンツをご用意しております。
お問い合わせ
コストダウンが利益に直結する術だと理解していても、なかなか前に進めることができない状況。そんな時は、newjiのコストダウン自動化機能で大きく利益貢献しよう!
(β版非公開)