- お役立ち記事
- Turning basics and modern technology: a guide to turning operations for component machining and production efficiency
Turning basics and modern technology: a guide to turning operations for component machining and production efficiency
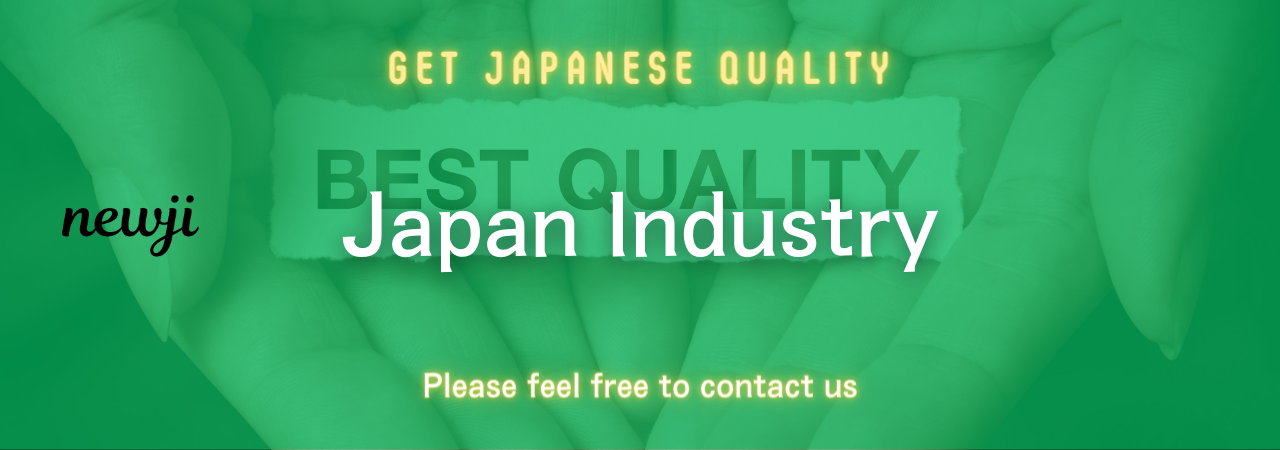
Understanding the fundamentals of turning operations can significantly enhance the efficiency of component machining and production.
In this guide, we will delve into the basics and explore how modern technology has revolutionized turning operations.
目次
What Is Turning?
Turning is a machining process used to create cylindrical parts by cutting away material from a workpiece.
The workpiece is typically rotated on a lathe while a cutting tool removes layers of material to shape it into the desired form.
This process is instrumental for producing components with high precision and accuracy.
Basic Steps in the Turning Process
The turning process comprises several critical steps:
1. Mounting the Workpiece: The workpiece is securely attached to the spindle of the lathe.
2. Tool Setup: The cutting tool is accurately positioned to ensure precise cuts.
3. Turning Passes: The lathe rotates the workpiece, and the cutting tool progressively removes material.
4. Final Touches: Secondary processes like sanding or polishing enhance the quality of the finished product.
Types of Turning Operations
There are various turning operations, each serving a specific purpose.
Understanding these will help you choose the best method for your project.
Facing
Facing involves removing material from the end of the workpiece to create a flat surface perpendicular to its axis.
This operation is essential for preparing the workpiece for subsequent machining steps.
Parting
Parting is used to cut off a section of the workpiece.
A narrow cutting tool slices through the material, ensuring minimal waste.
Grooving
Grooving creates a narrow cavity or groove on the workpiece surface.
This can be useful for creating slots or other intricate designs.
Threading
Threading is the process of cutting screw threads onto the workpiece.
Threads can be internal or external, depending on the intended application.
The Role of Modern Technology in Turning Operations
Advancements in technology have substantially improved turning operations.
Let’s explore some of the key innovations.
Computer Numerical Control (CNC) Lathes
CNC lathes have transformed the turning process by automating much of the work.
These machines use advanced software to control the movement of the cutting tool, ensuring consistent precision and efficiency.
With CNC technology, operators can easily program complex designs, reducing the need for manual adjustments and significantly lowering the risk of errors.
High-Speed Machining (HSM)
High-speed machining allows for faster cutting speeds and feed rates.
This results in shorter production times and higher output without compromising on quality.
HSM also reduces tool wear, leading to longer tool life and lower operational costs.
Material Innovation
Modern materials like carbide and ceramics have enhanced cutting tools’ performance in turning operations.
These materials offer superior hardness and heat resistance, which enable more effective and efficient cutting processes.
This development means components can be machined with higher precision and less downtime.
Advanced Lubrication Techniques
Proper lubrication is critical for efficient turning operations.
New lubrication techniques, such as minimum quantity lubrication (MQL), use small amounts of high-quality lubricants to reduce friction and heat.
This not only increases tool life but also improves the quality of the finished product.
Achieving Production Efficiency
Optimizing turning operations is crucial for achieving production efficiency.
Here are some strategies to help you maximize your machining processes.
Tool Selection
Selecting the right cutting tool is paramount for optimal performance.
Consider factors like material type, cutting speed, and desired finish.
Using tools made from high-quality materials will ensure better performance and durability.
Regular Maintenance
Maintaining your lathe and cutting tools is vital for consistent efficiency.
Regular inspections and timely replacements of worn-out parts can prevent costly downtime and extend the lifespan of your equipment.
Operator Training
A well-trained operator can significantly impact the efficiency and quality of turning operations.
Invest in regular training programs to keep your team updated on the latest techniques and technologies.
Process Optimization
Continuously evaluate and optimize your turning processes.
Utilize data analytics to monitor performance metrics and identify areas for improvement.
Implementing Lean manufacturing principles can also streamline operations and reduce waste.
The Future of Turning Operations
As technology evolves, turning operations will continue to advance.
Emerging trends such as Industry 4.0, artificial intelligence (AI), and additive manufacturing are poised to revolutionize this field.
Let’s explore what the future holds for turning operations.
Industry 4.0 and Smart Manufacturing
Industry 4.0 integrates advanced digital technologies like IoT, big data, and cloud computing into manufacturing processes.
For turning operations, this means smarter, more connected machinery that can communicate and make real-time adjustments.
This leads to increased efficiency, reduced downtime, and higher-quality outputs.
Artificial Intelligence and Machine Learning
AI and machine learning can enhance turning operations by predicting tool wear and optimizing cutting parameters.
Adaptive control systems can analyze data in real-time and adjust machining processes to achieve the best results.
These intelligent systems will further reduce manual intervention and increase overall productivity.
Hybrid Manufacturing
Hybrid manufacturing combines additive and subtractive processes, providing the benefits of both.
In turning operations, this can mean integrating 3D printing with traditional machining to create complex components with enhanced precision.
Hybrid solutions will offer greater flexibility and efficiency in production.
In conclusion, understanding the basics of turning operations and leveraging modern technology can significantly enhance component machining and production efficiency.
By adopting advanced tools and techniques, maintaining rigorous training and maintenance routines, and embracing future trends, businesses can achieve higher quality outputs and reduced operational costs.
Advancements such as CNC technology, HSM, and smart manufacturing are set to further transform turning operations, ensuring they remain at the forefront of precision engineering.
資料ダウンロード
QCD調達購買管理クラウド「newji」は、調達購買部門で必要なQCD管理全てを備えた、現場特化型兼クラウド型の今世紀最高の購買管理システムとなります。
ユーザー登録
調達購買業務の効率化だけでなく、システムを導入することで、コスト削減や製品・資材のステータス可視化のほか、属人化していた購買情報の共有化による内部不正防止や統制にも役立ちます。
NEWJI DX
製造業に特化したデジタルトランスフォーメーション(DX)の実現を目指す請負開発型のコンサルティングサービスです。AI、iPaaS、および先端の技術を駆使して、製造プロセスの効率化、業務効率化、チームワーク強化、コスト削減、品質向上を実現します。このサービスは、製造業の課題を深く理解し、それに対する最適なデジタルソリューションを提供することで、企業が持続的な成長とイノベーションを達成できるようサポートします。
オンライン講座
製造業、主に購買・調達部門にお勤めの方々に向けた情報を配信しております。
新任の方やベテランの方、管理職を対象とした幅広いコンテンツをご用意しております。
お問い合わせ
コストダウンが利益に直結する術だと理解していても、なかなか前に進めることができない状況。そんな時は、newjiのコストダウン自動化機能で大きく利益貢献しよう!
(Β版非公開)