- お役立ち記事
- Leveraging the Digital Twin in Manufacturing: New Opportunities DX Brings
Leveraging the Digital Twin in Manufacturing: New Opportunities DX Brings
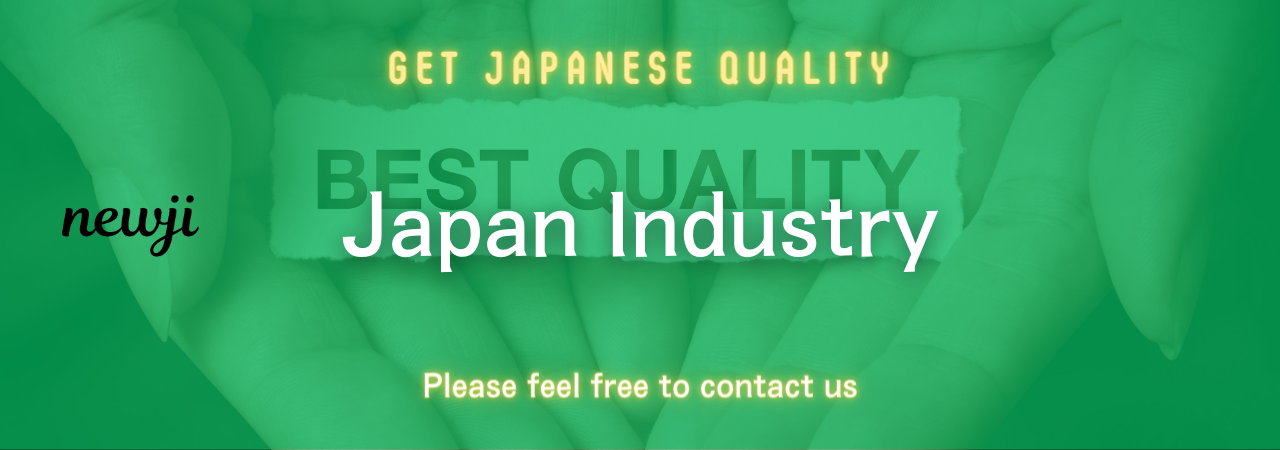
In today’s rapidly evolving technological landscape, the concept of a digital twin has emerged as a game-changer for the manufacturing industry.
Digital twins are virtual replicas of physical assets, systems, or processes.
These digital counterparts can simulate, predict, and optimize performance in the real world by harnessing data and advanced analytics.
The adoption of digital twins in manufacturing opens up new opportunities for digital transformation (DX), revolutionizing how products are designed, produced, and maintained.
目次
What is a Digital Twin?
A digital twin is a detailed virtual model that mirrors a physical object or process.
This model incorporates real-time data from sensors or other input methods, reflecting the current status, working condition, and location of the physical counterpart.
By using advanced algorithms and machine learning, the digital twin can simulate and predict real-world performance and potential issues, providing valuable insights and facilitating better decision-making.
The Role of Digital Twins in Manufacturing
Enhanced Product Design
One of the primary benefits of digital twins in manufacturing is the enhancement of product design.
Manufacturers can use digital twins to create detailed prototypes, running simulations under various conditions.
This approach allows designers to identify potential flaws and optimize the design before actual production.
Consequently, companies can save resources, reduce waste, and accelerate time-to-market.
Optimized Production Processes
Digital twins enable real-time monitoring and control of the manufacturing process.
By creating a virtual model of the entire production line, manufacturers can analyze performance, predict equipment failures, and optimize workflow.
This level of analysis helps in identifying bottlenecks, improving efficiency, and ensuring quality control.
The ability to foresee and mitigate issues before they impact production is a significant advantage.
Predictive Maintenance
The integration of digital twins with IoT (Internet of Things) devices allows for predictive maintenance strategies.
Sensors installed on machinery provide continuous feedback to the digital twin, which in turn, uses this data to forecast potential equipment failures.
This predictive approach minimizes downtime, reduces maintenance costs, and extends the lifespan of critical machinery.
Supply Chain Optimization
Digital twins can revolutionize supply chain management by providing a holistic view of the entire supply network.
By simulating different scenarios, manufacturers can predict disruptions, optimize logistics, and improve inventory management.
This predictive capability ensures a smoother supply chain, enhanced collaboration with suppliers, and better customer satisfaction.
Challenges and Considerations
Data Integration and Accuracy
For digital twins to be effective, they require accurate and comprehensive data from various sources.
Integrating data from different systems, devices, and stakeholders can be challenging.
Ensuring data accuracy and consistency is crucial to avoid incorrect simulations and predictions.
Investing in robust data integration strategies and maintaining data integrity is essential for successful implementation.
Security and Privacy
With the increasing use of IoT and connected devices in manufacturing, security and privacy concerns have become paramount.
Digital twins often require access to sensitive data, raising the risk of cyber-attacks and data breaches.
Implementing stringent cybersecurity measures, encryption, and access controls is necessary to safeguard critical information.
Scalability and Cost
The deployment of digital twins involves significant initial investments in technology, infrastructure, and skilled personnel.
For small and medium-sized enterprises (SMEs), the cost can be prohibitive.
However, the potential return on investment through increased efficiency and reduced downtime can justify the expense.
Additionally, scalable solutions and cloud-based platforms can help mitigate costs and facilitate broader adoption.
The Future of Digital Twins in Manufacturing
As technology continues to advance, the applications of digital twins in manufacturing are expected to expand.
Emerging technologies such as artificial intelligence, machine learning, and 5G connectivity will further enhance the capabilities of digital twins.
These advancements will enable even more accurate simulations, faster data processing, and real-time decision-making.
Integration with Industry 4.0
Digital twins are a key component of Industry 4.0, the fourth industrial revolution characterized by the integration of digital technologies into manufacturing.
The combination of digital twins with other Industry 4.0 technologies such as robotics, AI, and IoT will create a highly interconnected and intelligent manufacturing ecosystem.
This integration promises increased productivity, flexibility, and competitiveness in the global market.
Sustainability and Environmental Impact
The use of digital twins can contribute to more sustainable manufacturing practices.
By optimizing production processes and reducing waste, manufacturers can minimize their environmental footprint.
Moreover, digital twins can help in designing energy-efficient products and processes, aligning with global sustainability goals.
Conclusion
The implementation of digital twins in manufacturing represents a significant leap towards digital transformation.
By offering enhanced product design, optimized production processes, predictive maintenance, and improved supply chain management, digital twins provide a competitive edge in the fast-paced manufacturing sector.
However, to fully leverage the potential of digital twins, manufacturers must address challenges related to data integration, security, and scalability.
With the right strategies and investments, digital twins can unlock unprecedented opportunities for innovation and growth in manufacturing.
Embracing this technology today will pave the way for a smarter, more efficient, and sustainable manufacturing future.
資料ダウンロード
QCD調達購買管理クラウド「newji」は、調達購買部門で必要なQCD管理全てを備えた、現場特化型兼クラウド型の今世紀最高の購買管理システムとなります。
ユーザー登録
調達購買業務の効率化だけでなく、システムを導入することで、コスト削減や製品・資材のステータス可視化のほか、属人化していた購買情報の共有化による内部不正防止や統制にも役立ちます。
NEWJI DX
製造業に特化したデジタルトランスフォーメーション(DX)の実現を目指す請負開発型のコンサルティングサービスです。AI、iPaaS、および先端の技術を駆使して、製造プロセスの効率化、業務効率化、チームワーク強化、コスト削減、品質向上を実現します。このサービスは、製造業の課題を深く理解し、それに対する最適なデジタルソリューションを提供することで、企業が持続的な成長とイノベーションを達成できるようサポートします。
オンライン講座
製造業、主に購買・調達部門にお勤めの方々に向けた情報を配信しております。
新任の方やベテランの方、管理職を対象とした幅広いコンテンツをご用意しております。
お問い合わせ
コストダウンが利益に直結する術だと理解していても、なかなか前に進めることができない状況。そんな時は、newjiのコストダウン自動化機能で大きく利益貢献しよう!
(Β版非公開)