- お役立ち記事
- DX of Just-in-Time Production Achieves Both Zero Inventory and Optimum Production
DX of Just-in-Time Production Achieves Both Zero Inventory and Optimum Production
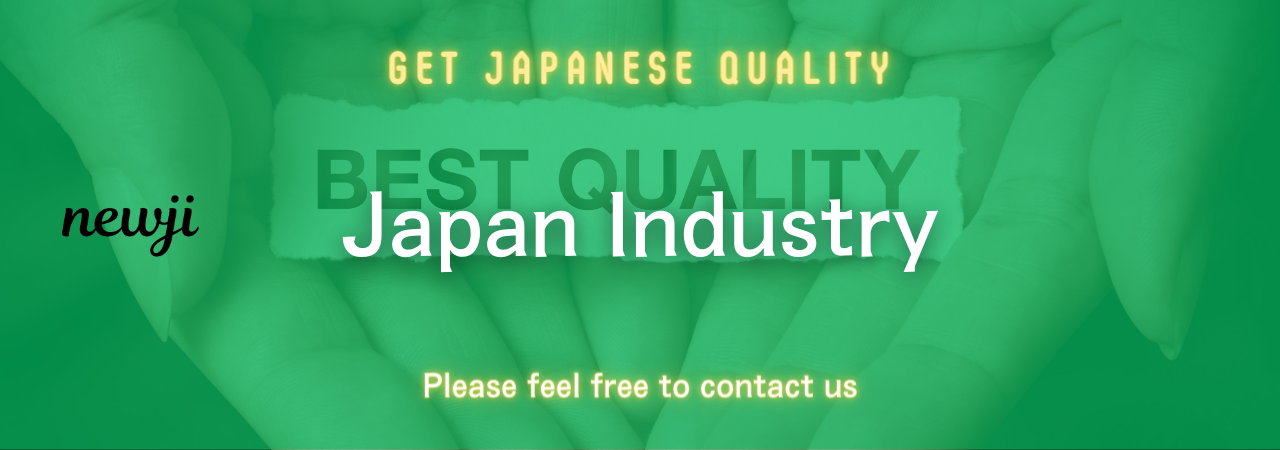
In today’s rapidly evolving industrial landscape, companies are increasingly looking toward digital transformation (DX) to streamline their operations, eliminate inefficiencies, and stay competitive.
One of the critical areas where DX is making a significant impact is Just-in-Time (JIT) production.
With the integration of advanced digital technologies, JIT production is achieving both zero inventory and optimum production.
This article will explore how DX is transforming JIT production, the benefits it offers, and the technologies driving this change.
What is Just-in-Time Production?
Just-in-Time production, or JIT, is a manufacturing methodology that aims to reduce waste and improve efficiency by producing only what is needed, when it is needed, and in the quantity needed.
The core idea is to minimize inventory holding costs and reduce lead times.
Originally developed by Toyota, JIT has become a crucial component of lean manufacturing practices worldwide.
The Role of Digital Transformation in JIT
Digital Transformation (DX) refers to the integration of digital technology into all areas of a business, fundamentally changing how it operates and delivers value to customers.
In the context of JIT production, DX is about leveraging data, automation, and connectivity to enhance the efficiency and responsiveness of manufacturing processes.
Data-Driven Decision Making
One of the primary benefits of DX in JIT production is the ability to make data-driven decisions.
Advanced analytics and big data technologies allow manufacturers to gather and analyze vast amounts of data from various sources, including supply chain partners, production lines, and customer demand patterns.
This data can be used to forecast demand more accurately, schedule production more efficiently, and minimize the risk of overproduction or stockouts.
With real-time insights, manufacturers can respond quickly to changes in market demand, ensuring they produce the right amount of products at the right time.
Enhanced Supply Chain Integration
DX enables better integration across the supply chain, which is vital for JIT production.
Technologies such as the Internet of Things (IoT), blockchain, and cloud computing facilitate seamless communication and collaboration between suppliers, manufacturers, and distributors.
This enhanced integration ensures that materials and components are delivered just in time for production, reducing the need for excess inventory.
Moreover, it allows for greater transparency and traceability, making it easier to identify and address potential disruptions in the supply chain.
Automated Production Systems
Automation is another crucial aspect of DX that is transforming JIT production.
Advanced robotics, machine learning, and artificial intelligence (AI) can automate various aspects of the production process, from material handling to quality control.
Automated systems can operate with greater precision and consistency, reducing the likelihood of errors and defects.
Additionally, they can adapt to changes in production schedules more quickly, ensuring that manufacturing processes remain agile and responsive to fluctuations in demand.
Benefits of DX in JIT Production
The integration of DX in JIT production offers several significant benefits that can help companies achieve zero inventory and optimum production.
Reduced Inventory Costs
One of the primary goals of JIT production is to minimize inventory holding costs.
By producing only what is needed and when it is needed, companies can reduce the amount of inventory they need to store.
DX further enhances this capability by providing real-time data and analytics that help manufacturers optimize inventory levels.
This reduction in inventory costs can lead to significant cost savings and improved profitability.
Improved Production Efficiency
DX technologies such as automation and advanced analytics can significantly improve production efficiency.
Automated systems can complete tasks faster and with greater accuracy than human workers, reducing production times and increasing output.
Predictive analytics can help manufacturers identify potential bottlenecks and optimize production schedules to ensure smooth operations.
By improving production efficiency, companies can reduce lead times and deliver products to customers more quickly.
Enhanced Quality Control
Quality control is a critical component of any manufacturing process.
DX technologies can enhance quality control by providing real-time monitoring and analysis of production data.
Advanced sensors and IoT devices can detect defects or anomalies early in the production process, allowing for immediate corrective action.
Machine learning algorithms can analyze historical data to identify patterns and predict potential quality issues.
These capabilities ensure that products meet the highest quality standards, reducing the likelihood of returns or recalls.
Increased Agility and Flexibility
In today’s fast-paced market, the ability to respond quickly to changes in demand is crucial.
DX technologies provide manufacturers with the agility and flexibility they need to adapt to these changes.
Real-time data and analytics enable companies to adjust production schedules and quantities based on current demand patterns.
Automated systems can quickly switch between different tasks or product lines, allowing for greater flexibility in production.
This increased agility ensures that manufacturers can meet customer needs more effectively and stay competitive in a dynamic market.
Key Technologies Driving DX in JIT Production
Several key technologies are driving the digital transformation of JIT production, enabling companies to achieve zero inventory and optimum production.
Internet of Things (IoT)
The Internet of Things (IoT) involves connecting physical devices to the internet, allowing them to collect and exchange data.
In JIT production, IoT devices can be used to monitor equipment performance, track inventory levels, and provide real-time data on production processes.
This connectivity enables manufacturers to optimize operations, prevent equipment failures, and ensure that materials and components are available when needed.
Advanced Analytics
Advanced analytics involves the use of data analysis techniques to extract insights and make informed decisions.
In the context of JIT production, advanced analytics can be used to forecast demand, optimize inventory levels, and improve production schedules.
Machine learning algorithms can analyze historical data to identify trends and patterns, enabling manufacturers to make more accurate predictions about future demand.
This data-driven approach ensures that production processes are aligned with market needs, reducing the risk of overproduction or stockouts.
Automation and Robotics
Automation and robotics are transforming manufacturing processes by automating repetitive tasks and improving precision and consistency.
Automated systems can handle tasks such as material handling, assembly, and quality control, reducing the need for manual labor and increasing production efficiency.
Robotic systems can work around the clock, ensuring that production processes continue uninterrupted.
By integrating automation into JIT production, manufacturers can achieve higher levels of productivity and reduce lead times.
Cloud Computing
Cloud computing involves delivering computing services over the internet, enabling companies to access and store data remotely.
In JIT production, cloud computing can facilitate collaboration and data sharing between different stakeholders in the supply chain.
Manufacturers can use cloud-based platforms to track inventory levels, monitor production processes, and share real-time data with suppliers and distributors.
This connectivity ensures that all parties have access to the information they need to make informed decisions and maintain seamless operations.
The digital transformation of Just-in-Time production is revolutionizing the manufacturing industry.
By leveraging advanced technologies such as IoT, advanced analytics, automation, and cloud computing, companies can achieve both zero inventory and optimum production.
These capabilities lead to reduced costs, improved efficiency, enhanced quality control, and increased agility in response to market demands.
As DX continues to evolve, it will undoubtedly play an increasingly vital role in the future of manufacturing, enabling companies to stay competitive and deliver greater value to their customers.
資料ダウンロード
QCD調達購買管理クラウド「newji」は、調達購買部門で必要なQCD管理全てを備えた、現場特化型兼クラウド型の今世紀最高の購買管理システムとなります。
ユーザー登録
調達購買業務の効率化だけでなく、システムを導入することで、コスト削減や製品・資材のステータス可視化のほか、属人化していた購買情報の共有化による内部不正防止や統制にも役立ちます。
NEWJI DX
製造業に特化したデジタルトランスフォーメーション(DX)の実現を目指す請負開発型のコンサルティングサービスです。AI、iPaaS、および先端の技術を駆使して、製造プロセスの効率化、業務効率化、チームワーク強化、コスト削減、品質向上を実現します。このサービスは、製造業の課題を深く理解し、それに対する最適なデジタルソリューションを提供することで、企業が持続的な成長とイノベーションを達成できるようサポートします。
オンライン講座
製造業、主に購買・調達部門にお勤めの方々に向けた情報を配信しております。
新任の方やベテランの方、管理職を対象とした幅広いコンテンツをご用意しております。
お問い合わせ
コストダウンが利益に直結する術だと理解していても、なかなか前に進めることができない状況。そんな時は、newjiのコストダウン自動化機能で大きく利益貢献しよう!
(Β版非公開)