- お役立ち記事
- Role and Practical Methods of Flow Coating Technology in Manufacturing
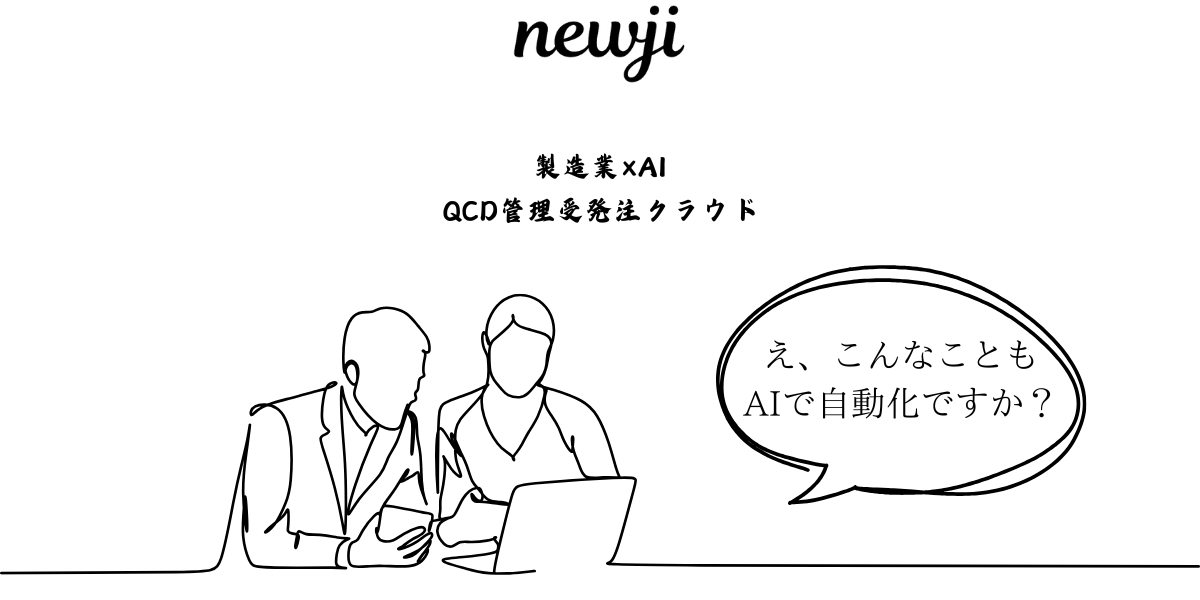
Role and Practical Methods of Flow Coating Technology in Manufacturing
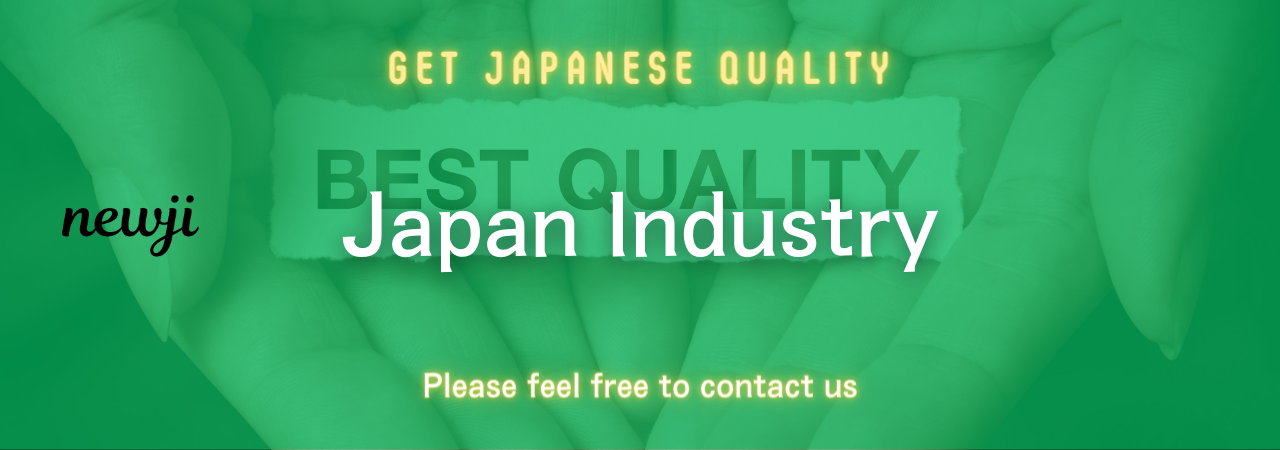
Flow coating technology has emerged as a pivotal method in modern manufacturing.
In an era where product quality and efficiency are paramount, understanding the role and practical methods of flow coating can significantly benefit manufacturers.
In this article, we delve deep into what flow coating entails, its significance in the manufacturing process, and how to effectively implement it.
目次
What is Flow Coating Technology?
Flow coating, at its core, is a technique where a liquid coating is applied to a substrate in a controlled manner.
The process involves the use of specific equipment that ensures even distribution of the coating material, minimising waste and enhancing product quality.
The coating material, which can range from paints to protective films, flows over the surface of the item, creating a smooth and uniform layer.
Importance of Flow Coating in Manufacturing
Flow coating is particularly important in industries where product consistency and surface quality are crucial.
For instance, in the automotive sector, flow coating is used to apply protective and aesthetic coatings to car parts.
In electronics, it ensures protective layers on sensitive components, safeguarding them against moisture and other environmental hazards.
Here are a few reasons why flow coating is vital in manufacturing:
Enhanced Surface Quality
One of the primary advantages of flow coating is the superior surface quality it offers.
Unlike traditional methods, where manual application can result in uneven layers and imperfections, flow coating ensures a consistent and smooth finish.
This is particularly beneficial in products where aesthetics and surface integrity are critical.
Efficiency and Cost-Effectiveness
Flow coating is a highly efficient process.
The controlled application means minimal wastage of coating material.
Additionally, the process is faster than many traditional methods, translating to lower labor costs and increased production rates.
For manufacturers, this blend of efficiency and cost-effectiveness is invaluable.
Versatility
Flow coating is versatile and can be used on a wide range of materials and products.
From metals and plastics to ceramics and electronics, its application is vast.
This versatility makes it a preferred choice for many manufacturers looking for a one-size-fits-all coating solution.
Practical Methods of Flow Coating
Knowing the benefits is one thing but understanding the practical methods of implementing flow coating technology is another.
Here are some crucial steps and considerations:
Choosing the Right Coating Material
The first step in the flow coating process is selecting the appropriate coating material.
The choice depends on the desired properties of the final product.
For instance, if protection against corrosion is required, a specific type of protective coating material would be used.
Similarly, for aesthetic purposes, different kinds of paints or finishes could be chosen.
Preparing the Substrate
Before the actual coating can be applied, the substrate (the item to be coated) must be meticulously prepared.
This typically involves cleaning to remove any dirt, grease, or previous coatings.
Ensuring a clean surface is essential for the coating to adhere properly and to achieve a high-quality finish.
Equipment Setup and Calibration
The flow coating equipment must be correctly set up and calibrated to ensure optimal performance.
This includes adjusting parameters such as flow rate, temperature, and nozzle size.
Each of these factors can affect the final quality of the coating, so precise calibration is crucial.
Application Process
During the application process, the coating material is allowed to flow over the substrate.
This can be done manually or using automated systems, depending on the scale of production and the specific requirements.
The key here is to maintain a consistent flow to ensure an even coat.
Multiple passes may be required for thicker or multi-layered coatings.
Curing and Drying
Once the coating has been applied, it needs to be cured or dried.
The method of curing depends on the type of coating material used.
For example, some materials may require heat curing, while others may simply dry at room temperature.
Proper curing is essential for the durability and performance of the coating.
Quality Control
Finally, a robust quality control process is vital.
This involves inspecting the coated items to ensure they meet the desired standards and specifications.
Regular checks and tests can help identify any issues early, allowing for prompt corrective action.
Challenges in Flow Coating
While flow coating offers numerous benefits, it is not without its challenges.
Understanding these challenges and knowing how to address them can make the difference between a successful and a flawed application.
Material Compatibility
Not all coating materials are compatible with every type of substrate.
Choosing the wrong combination can result in poor adhesion, reduced durability, and even failure of the coating.
It is crucial to conduct thorough testing and validation to ensure compatibility.
Environmental Considerations
The flow coating process can be sensitive to environmental conditions such as temperature and humidity.
These factors can influence the viscosity of the coating material and the drying time.
Manufacturers need to monitor and control these conditions to achieve consistent results.
Equipment Maintenance
Regular maintenance of the flow coating equipment is essential for prolonged performance.
Wear and tear can affect the precision of the application, leading to inconsistent coating quality.
A regular maintenance schedule can help mitigate this issue.
Conclusion
Flow coating technology plays a critical role in modern manufacturing, offering enhanced surface quality, efficiency, and versatility.
By understanding the practical methods of implementation and addressing the associated challenges, manufacturers can leverage flow coating to improve their products and processes.
As technology continues to evolve, staying updated with the latest advancements and best practices in flow coating will be key to staying competitive in the manufacturing industry.
資料ダウンロード
QCD調達購買管理クラウド「newji」は、調達購買部門で必要なQCD管理全てを備えた、現場特化型兼クラウド型の今世紀最高の購買管理システムとなります。
ユーザー登録
調達購買業務の効率化だけでなく、システムを導入することで、コスト削減や製品・資材のステータス可視化のほか、属人化していた購買情報の共有化による内部不正防止や統制にも役立ちます。
NEWJI DX
製造業に特化したデジタルトランスフォーメーション(DX)の実現を目指す請負開発型のコンサルティングサービスです。AI、iPaaS、および先端の技術を駆使して、製造プロセスの効率化、業務効率化、チームワーク強化、コスト削減、品質向上を実現します。このサービスは、製造業の課題を深く理解し、それに対する最適なデジタルソリューションを提供することで、企業が持続的な成長とイノベーションを達成できるようサポートします。
オンライン講座
製造業、主に購買・調達部門にお勤めの方々に向けた情報を配信しております。
新任の方やベテランの方、管理職を対象とした幅広いコンテンツをご用意しております。
お問い合わせ
コストダウンが利益に直結する術だと理解していても、なかなか前に進めることができない状況。そんな時は、newjiのコストダウン自動化機能で大きく利益貢献しよう!
(Β版非公開)