- お役立ち記事
- DX and Human Resource Diversity in Manufacturing: The Key to Innovation Creation
DX and Human Resource Diversity in Manufacturing: The Key to Innovation Creation
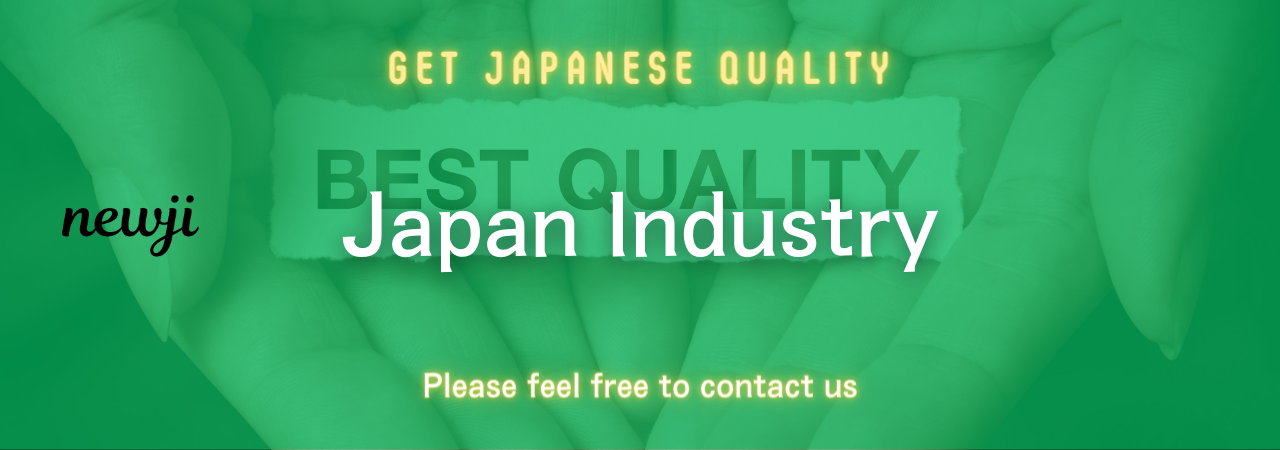
Digital transformation, often abbreviated as DX, has become a buzzword across various industries, particularly in manufacturing.
Essentially, DX refers to the integration of digital technologies into all aspects of business operations.
While technology is a pivotal element of this transformation, the human aspect is equally indispensable.
In this context, human resource diversity emerges as a critical factor.
A diverse workforce, coupled with digital transformation, can spur innovation, drive productivity, and lead to sustained growth in the manufacturing sector.
目次
Understanding Digital Transformation (DX) in Manufacturing
The Role of Digital Technologies
In manufacturing, digital transformation encompasses the use of advanced technologies such as the Internet of Things (IoT), artificial intelligence (AI), machine learning, and big data analytics.
These technologies help streamline operations, improve supply chain management, and enhance product quality.
For instance, IoT devices can monitor machinery in real-time, predicting maintenance needs before a breakdown occurs.
AI algorithms can optimize production schedules, ensuring efficient use of resources.
Enhancing Operational Efficiency
Digital transformation also allows for better decision-making processes.
Data analytics can provide insights into market trends, customer preferences, and operational bottlenecks.
By analyzing this data, manufacturers can make informed decisions, leading to cost savings and better resource allocation.
Moreover, automation of repetitive tasks frees up human workers to focus on more complex and value-added activities.
The Importance of Human Resource Diversity
Promoting Creativity and Innovation
Human resource diversity refers to the inclusion of individuals from different backgrounds, cultures, genders, and experiences in the workforce.
When people with diverse perspectives come together, they bring a variety of ideas to the table, fostering a culture of creativity and innovation.
In manufacturing, this can lead to the development of new products, improved processes, and the adoption of best practices from various fields.
Enhancing Problem-Solving Capabilities
Diverse teams are better equipped to solve complex problems.
Different viewpoints can lead to a deeper understanding of issues and more holistic solutions.
For example, a team comprised of engineers, software developers, and marketing professionals is likely to devise more comprehensive strategies than a homogeneous group.
Each member brings their unique expertise, ensuring that all aspects of a problem are considered.
Synergy Between DX and Human Resource Diversity
Driving Innovation
When digital transformation and human resource diversity go hand in hand, the potential for innovation multiplies.
Technology provides the tools and data needed to implement new ideas, while a diverse workforce supplies the creative spark and different perspectives.
Together, they create an environment conducive to continuous improvement and breakthrough innovations.
For example, diverse teams utilizing advanced data analytics can identify market niches and develop products tailored to specific customer needs.
Adapting to Market Changes
The manufacturing sector is often subject to rapid and unpredictable market changes.
Companies that embrace both digital transformation and human resource diversity are more agile and better positioned to adapt.
Digital tools enable quick data analysis and decision-making, while diverse teams bring flexibility and a broad range of solutions to the table.
This combination ensures that companies can pivot strategies and operations swiftly in response to market demands.
Barriers to Implementation and How to Overcome Them
Resistance to Change
One of the significant barriers to implementing DX and fostering human resource diversity is resistance to change.
Employees accustomed to traditional manufacturing processes may be hesitant to adopt new technologies.
Similarly, long-standing workplace cultures may resist efforts to diversify the workforce.
To overcome these challenges, companies need to invest in training and development programs.
Clear communication about the benefits of DX and diversity can also help mitigate resistance.
Investment and Costs
Another barrier is the initial investment required for digital transformation and diversity initiatives.
Advanced technologies and training programs can be costly.
However, these investments often pay off in the long run through increased efficiency, innovation, and market competitiveness.
Companies can start with pilot projects to demonstrate the value of these initiatives, gradually scaling up as they gain buy-in from stakeholders.
Case Studies and Success Stories
Global Manufacturing Giants
Several global manufacturing giants have successfully implemented DX and embraced diversity, reaping significant benefits.
For instance, Siemens has integrated IoT and AI into its manufacturing processes, resulting in improved productivity and reduced downtime.
The company also promotes diversity, with initiatives aimed at increasing gender balance and inclusivity in its workforce.
As a result, Siemens has seen a surge in innovative solutions and market growth.
Small and Medium Enterprises (SMEs)
Not only large corporations but also small and medium enterprises (SMEs) can benefit from DX and diversity.
Take the example of a mid-sized automotive parts manufacturer that integrated IoT sensors to monitor equipment health.
By pairing this digital initiative with a diverse team of engineers and IT specialists, the company reduced maintenance costs and improved production efficiency.
The diverse team’s varied experiences and expertise played a crucial role in interpreting IoT data and implementing effective solutions.
Conclusion
Digital transformation and human resource diversity are no longer optional in the manufacturing sector; they are essential.
The synergy between advanced technologies and a diverse workforce can lead to unprecedented levels of innovation and operational efficiency.
While there are challenges in implementing these initiatives, the long-term benefits far outweigh the initial hurdles.
Companies that embrace both DX and diversity are likely to lead in their respective markets, setting new standards for others to follow.
As the manufacturing landscape continues to evolve, those who invest in these areas will be better positioned to adapt and thrive.
資料ダウンロード
QCD調達購買管理クラウド「newji」は、調達購買部門で必要なQCD管理全てを備えた、現場特化型兼クラウド型の今世紀最高の購買管理システムとなります。
ユーザー登録
調達購買業務の効率化だけでなく、システムを導入することで、コスト削減や製品・資材のステータス可視化のほか、属人化していた購買情報の共有化による内部不正防止や統制にも役立ちます。
NEWJI DX
製造業に特化したデジタルトランスフォーメーション(DX)の実現を目指す請負開発型のコンサルティングサービスです。AI、iPaaS、および先端の技術を駆使して、製造プロセスの効率化、業務効率化、チームワーク強化、コスト削減、品質向上を実現します。このサービスは、製造業の課題を深く理解し、それに対する最適なデジタルソリューションを提供することで、企業が持続的な成長とイノベーションを達成できるようサポートします。
オンライン講座
製造業、主に購買・調達部門にお勤めの方々に向けた情報を配信しております。
新任の方やベテランの方、管理職を対象とした幅広いコンテンツをご用意しております。
お問い合わせ
コストダウンが利益に直結する術だと理解していても、なかなか前に進めることができない状況。そんな時は、newjiのコストダウン自動化機能で大きく利益貢献しよう!
(Β版非公開)