- お役立ち記事
- A manufacturing sales team takes on a challenge: A proposal to improve energy efficiency on the shop floor
A manufacturing sales team takes on a challenge: A proposal to improve energy efficiency on the shop floor
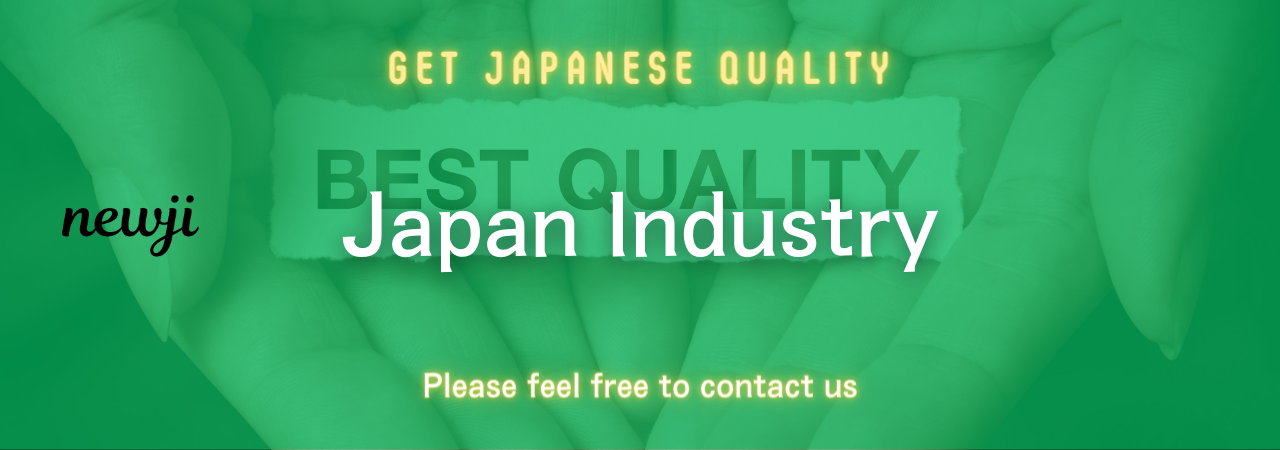
In the world of manufacturing, keeping the energy costs down is a high priority.
Not only does it help save money, but it also protects the environment.
Our manufacturing sales team has taken up an important challenge to improve energy efficiency on the shop floor.
This is a proposal aimed at identifying areas where energy can be saved, thus boosting overall efficiency and profitability.
目次
Understanding the Current Energy Usage
Before making any improvements, it’s essential to understand how energy is currently being used.
Manufacturing processes often involve machines and systems that consume vast amounts of energy.
Each step in the production line, from raw materials to finished products, demands power.
Tracking this energy use is the first step to find areas where improvements can be made.
Conducting an Energy Audit
An energy audit is a thorough examination of how energy flows through the manufacturing process.
It involves measuring the amount of energy used by different machines, equipment, and processes.
An energy audit helps identify which areas are consuming the most power and where inefficiencies exist.
The results of an energy audit provide a baseline from which improvements can be measured.
Auditors may use tools like energy meters, thermal cameras, and software to collect and analyze data.
Once the audit is completed, it will highlight areas that need attention.
Examining Equipment and Machinery
The equipment and machinery on the shop floor can be major energy consumers.
Older machines, in particular, may not be as energy-efficient as newer models.
In the energy audit, each piece of equipment is evaluated based on its power usage and efficiency.
Sometimes, a simple tune-up or maintenance of the machinery can result in significant energy savings.
Regular servicing ensures machines operate efficiently and reduces the risk of breakdowns.
Implementing Energy-Efficient Practices
Once the areas of improvement are identified, the next step is to implement energy-efficient practices.
These practices can range from making small behavioral changes to larger, more substantial upgrades.
Optimizing Machine Use
Optimizing the use of machines is often the easiest way to save energy.
This involves ensuring machines aren’t left running when not in use and scheduling operations to minimize energy consumption during peak hours.
Sequencing tasks to reduce machine idling times can also contribute to energy savings.
Upgrading to Energy-Efficient Equipment
When older machines become too inefficient, it may be cost-effective to invest in newer, energy-efficient models.
Newer equipment often comes with advanced technology designed to use less power.
While the upfront cost might be higher, the long-term savings on energy bills can justify the investment.
Over time, these savings add up, making the investment worthwhile.
Implementing Preventive Maintenance
Preventive maintenance is a proactive approach to keep machinery running smoothly.
Regular checks and servicing help detect issues early, reducing the likelihood of major repairs or energy wastage.
Preventive maintenance ensures machines operate at their optimal energy use levels, contributing to overall efficiency.
Incorporating Energy-Efficient Technologies
Besides upgrading machinery, incorporating new technologies can further enhance energy efficiency.
These technologies are designed to optimize energy consumption and reduce wastage.
Using Energy Management Systems
Energy management systems (EMS) are software solutions that monitor and control energy usage.
EMS can track real-time energy consumption, identify inefficiencies, and automate energy-saving measures.
By providing detailed insights into energy use, EMS helps managers make data-driven decisions to improve efficiency.
Implementing an EMS can lead to significant reductions in energy costs.
Installing Variable Frequency Drives (VFDs)
Variable Frequency Drives (VFDs) adjust the speed of electric motors based on demand.
Rather than running at full speed constantly, VFDs allow motors to operate more efficiently.
This adjustment reduces energy consumption, especially for machinery that doesn’t always need to run at full capacity.
Installing VFDs can result in substantial energy savings for many manufacturing applications.
Adopting Renewable Energy Sources
Considering renewable energy sources is another way to enhance energy efficiency.
Solar, wind, and other renewable energy options can provide clean power to the manufacturing facility.
Investing in renewable energy might involve installing solar panels or wind turbines on-site.
While the initial setup can be costly, the long-term benefits include reduced energy costs and a smaller carbon footprint.
Employee Involvement and Training
An essential aspect of improving energy efficiency is involving employees in the process.
Training and educating the workforce on energy-saving practices can make a significant difference.
Conducting Energy Efficiency Training
Providing training sessions for employees helps them understand the importance of energy efficiency.
Training should focus on practical steps they can take to contribute to energy-saving goals.
This could include proper machine operation, shutting down equipment when not in use, and reporting any inefficiencies noticed.
An informed workforce is more likely to take proactive steps to save energy.
Encouraging a Culture of Energy Conservation
Fostering a culture of energy conservation within the workplace can lead to sustained improvements.
Managers should encourage employees to suggest ideas for reducing energy usage and recognize their contributions.
Rewarding employees for their energy-saving efforts can motivate the entire team to stay committed to the goal.
Measuring and Sustaining Improvements
After implementing changes, it’s crucial to measure the impact and sustain the improvements.
Continuous monitoring and evaluation ensure the energy efficiency measures remain effective.
Tracking Energy Savings
Using the baseline data from the energy audit, tracking the results of implemented changes is essential.
Monitoring energy consumption regularly helps verify that the improvements are delivering the expected savings.
If the energy savings are not as projected, adjustments can be made to the strategies or practices in place.
Continuous Improvement and Adaptation
Energy efficiency is an ongoing process that requires continuous improvement and adaptation.
As technology advances and new methods become available, the manufacturing sales team should stay updated.
Regularly reviewing and updating energy-saving strategies ensures the facility remains efficient.
To summarize, improving energy efficiency on the shop floor is a multifaceted challenge that requires a strategic approach.
By conducting energy audits, implementing efficient practices, incorporating advanced technologies, engaging employees, and continuously measuring results, significant energy savings can be achieved.
These efforts not only reduce costs but also promote a sustainable and environmentally friendly manufacturing process.
The manufacturing sales team is dedicated to overcoming this challenge and driving the change necessary for a more efficient future.
資料ダウンロード
QCD調達購買管理クラウド「newji」は、調達購買部門で必要なQCD管理全てを備えた、現場特化型兼クラウド型の今世紀最高の購買管理システムとなります。
ユーザー登録
調達購買業務の効率化だけでなく、システムを導入することで、コスト削減や製品・資材のステータス可視化のほか、属人化していた購買情報の共有化による内部不正防止や統制にも役立ちます。
NEWJI DX
製造業に特化したデジタルトランスフォーメーション(DX)の実現を目指す請負開発型のコンサルティングサービスです。AI、iPaaS、および先端の技術を駆使して、製造プロセスの効率化、業務効率化、チームワーク強化、コスト削減、品質向上を実現します。このサービスは、製造業の課題を深く理解し、それに対する最適なデジタルソリューションを提供することで、企業が持続的な成長とイノベーションを達成できるようサポートします。
オンライン講座
製造業、主に購買・調達部門にお勤めの方々に向けた情報を配信しております。
新任の方やベテランの方、管理職を対象とした幅広いコンテンツをご用意しております。
お問い合わせ
コストダウンが利益に直結する術だと理解していても、なかなか前に進めることができない状況。そんな時は、newjiのコストダウン自動化機能で大きく利益貢献しよう!
(Β版非公開)