- お役立ち記事
- How to implement the Total Cost Model in the manufacturing industry
How to implement the Total Cost Model in the manufacturing industry
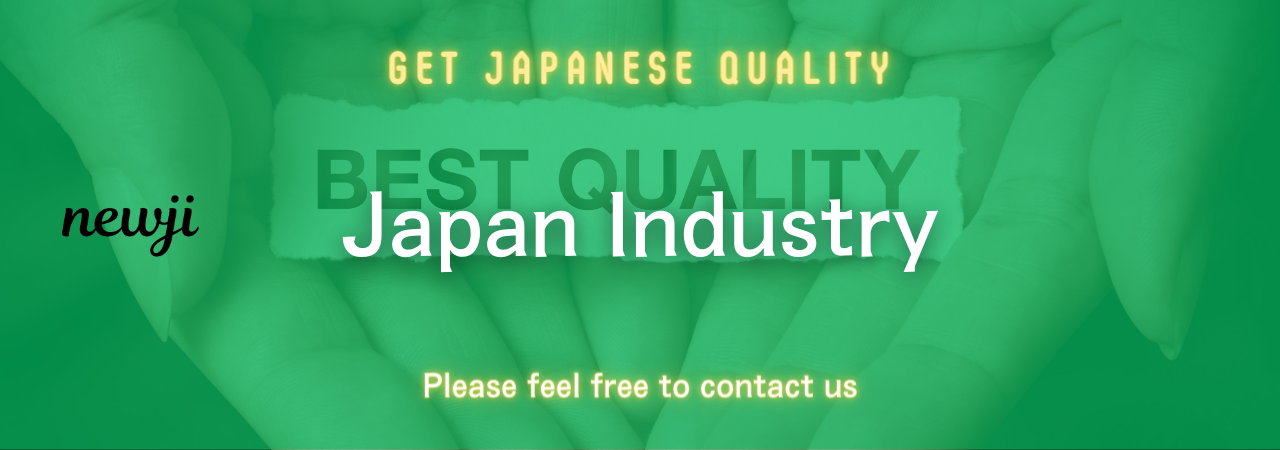
The Total Cost Model is a vital tool in the manufacturing industry, helping businesses to get a clearer understanding of all costs associated with production. Implementing this model can be a game changer, improving efficiency and reducing hidden expenses. This article will guide you through the steps to implement the Total Cost Model in your manufacturing processes.
目次
Understanding the Total Cost Model
Before diving into implementation, it’s essential to understand what the Total Cost Model is. The Total Cost Model considers all costs involved in the production of a product, including direct and indirect expenses. This comprehensive view can include materials, labor, overhead, transportation, and even the cost of poor quality. By analyzing these costs, a company can make more informed decisions and identify areas for cost-saving.
Step-by-Step Guide to Implement the Total Cost Model
Step 1: Identify All Relevant Costs
The initial step is to list all costs associated with manufacturing. Start with direct costs like raw materials and labor. Next, include indirect costs, such as maintenance, energy consumption, and administrative expenses. Don’t forget hidden costs like downtime, substandard quality, and waste disposal.
Step 2: Categorize Costs into Fixed and Variable
Once you’ve identified all costs, categorize them into fixed and variable costs. Fixed costs remain constant regardless of production levels, like rent and salaries. Variable costs fluctuate with production volume, such as raw materials and utilities. This categorization helps in understanding how costs will change with different production levels.
Step 3: Gather Accurate Data
Having accurate and up-to-date data is crucial. Collect historical data related to each cost category. Use production logs, financial records, and energy bills for this purpose. You may also need to collaborate with various departments to ensure that all relevant costs are captured.
Step 4: Use Cost Allocation Methods
In some cases, particular costs are shared among multiple products or production lines. Use cost allocation methods to distribute these shared costs accurately. Methods like Activity-Based Costing (ABC) can be particularly useful for allocating overhead expenses based on the activities that drive those costs.
Step 5: Implement Software Tools
Consider using specialized software tools to streamline the Total Cost Model implementation. Many Enterprise Resource Planning (ERP) systems come equipped with cost management modules. These tools can automate data collection, cost allocation, and reporting processes, making the implementation smoother and more accurate.
Step 6: Analyze the Data
With all data gathered and costs categorized, analyze the information to understand the total cost structure. Look for patterns and areas where costs are particularly high. This analysis will provide insights into potential inefficiencies and areas for cost reduction.
Step 7: Identify Cost-Saving Opportunities
Based on the analysis, identify opportunities to save costs. This might include renegotiating supplier contracts, optimizing production schedules, or investing in energy-efficient machinery. Focus on both short-term and long-term cost-saving strategies.
Step 8: Implement Changes and Monitor
Implement the identified cost-saving measures. Establish a monitoring system to track the effectiveness of these changes. Regularly review cost data to ensure that the Total Cost Model continues to provide accurate insights. Use dashboards and regular reports to keep all stakeholders informed.
Benefits of Implementing the Total Cost Model
Enhanced Cost Visibility
The Total Cost Model provides a comprehensive view of all production costs. This visibility helps in making informed decisions and identifying hidden expenses that can be reduced.
Improved Efficiency
By understanding the true costs, companies can streamline their operations. This might include optimizing production schedules or reducing waste, leading to improved efficiency.
Better Pricing Strategies
With a clearer understanding of total costs, businesses can devise better pricing strategies. This can help in staying competitive and maintaining healthy profit margins.
Informed Investment Decisions
The insights gained from the Total Cost Model can help in making informed decisions about investments in machinery, technology, or new production methods. This ensures that capital is invested wisely.
Challenges in Implementing the Total Cost Model
Data Accuracy
Ensuring data accuracy can be challenging, especially if information is scattered across different departments. It’s crucial to have a centralized system for data collection.
Complexity in Cost Allocation
Allocating shared costs accurately can be complex. Using advanced cost allocation methods and software tools can help in overcoming this challenge.
Resistance to Change
Employees may resist changes to established processes. Effective communication and training can help in easing this transition.
Conclusion
Implementing the Total Cost Model in the manufacturing industry is not just about understanding costs. It’s about making smarter decisions that can lead to substantial savings and improved efficiency.
By following the steps outlined in this guide and leveraging technology, companies can reap the benefits of a comprehensive cost management strategy. Regular monitoring and continual improvement are key to maintaining the effectiveness of the model.
Start today and transform your manufacturing operations with the Total Cost Model.
資料ダウンロード
QCD調達購買管理クラウド「newji」は、調達購買部門で必要なQCD管理全てを備えた、現場特化型兼クラウド型の今世紀最高の購買管理システムとなります。
ユーザー登録
調達購買業務の効率化だけでなく、システムを導入することで、コスト削減や製品・資材のステータス可視化のほか、属人化していた購買情報の共有化による内部不正防止や統制にも役立ちます。
NEWJI DX
製造業に特化したデジタルトランスフォーメーション(DX)の実現を目指す請負開発型のコンサルティングサービスです。AI、iPaaS、および先端の技術を駆使して、製造プロセスの効率化、業務効率化、チームワーク強化、コスト削減、品質向上を実現します。このサービスは、製造業の課題を深く理解し、それに対する最適なデジタルソリューションを提供することで、企業が持続的な成長とイノベーションを達成できるようサポートします。
オンライン講座
製造業、主に購買・調達部門にお勤めの方々に向けた情報を配信しております。
新任の方やベテランの方、管理職を対象とした幅広いコンテンツをご用意しております。
お問い合わせ
コストダウンが利益に直結する術だと理解していても、なかなか前に進めることができない状況。そんな時は、newjiのコストダウン自動化機能で大きく利益貢献しよう!
(Β版非公開)