- お役立ち記事
- Types of plating solutions used in manufacturing and selection requirements
Types of plating solutions used in manufacturing and selection requirements
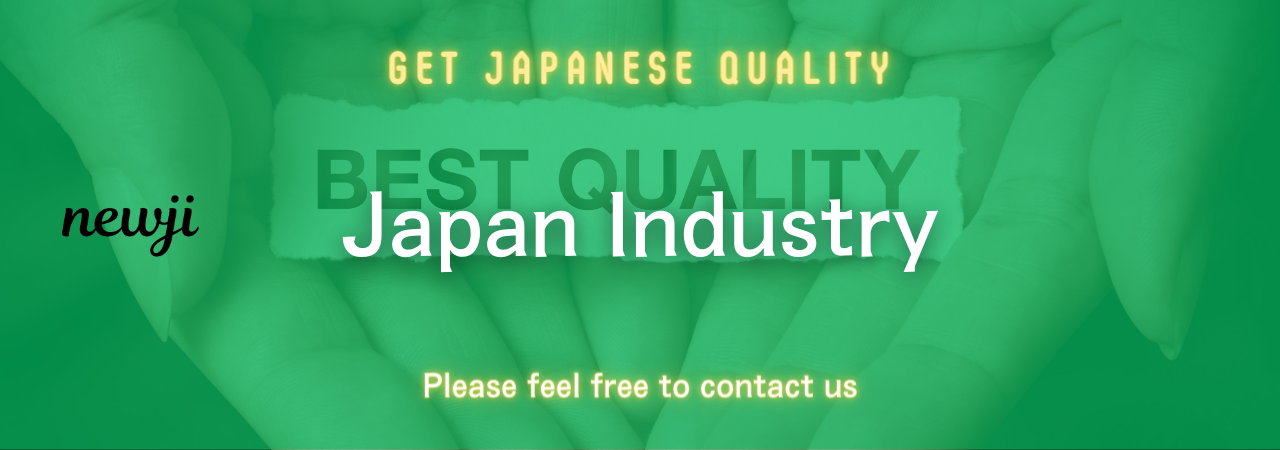
In the world of manufacturing, plating solutions are essential to achieving the desired properties on surfaces of various materials.
Plating enhances the appearance, corrosion resistance, and durability of the materials it covers.
There are several types of plating solutions used in manufacturing, each tailored to specific needs and requirements.
目次
Types of Plating Solutions
Electroplating Solutions
Electroplating is a popular method in manufacturing for coating objects with a thin layer of metal.
The process involves passing an electric current through a solution containing metal ions.
These ions are deposited onto the object’s surface.
Common metals used in electroplating include nickel, gold, silver, copper, and zinc.
Nickel plating is widely used for its excellent corrosion resistance and shiny finish.
Gold and silver plating are often chosen for their conductivity and aesthetic appeal.
Copper plating serves as an excellent base layer for further plating or as a final coat for some electrical applications.
Zinc plating offers good corrosion protection for steel components.
Electroless Plating Solutions
Unlike electroplating, electroless plating does not require an electric current.
It relies on a chemical reduction process to deposit metal onto a surface.
This method provides a uniform coating even on complex shapes and is often used for applications requiring precise control over thickness.
Electroless nickel plating, for example, is highly valued for its hardness and wear resistance.
It’s frequently used in aerospace, automotive, and electronics industries.
Electroless copper plating is also widely used in printed circuit board (PCB) manufacturing.
Chrome Plating Solutions
Chrome plating is well-known for its decorative and protective qualities.
It is often used on automotive parts, tools, and various household fixtures.
Chrome plating involves a chromium-based electroplating solution that results in a bright, mirror-like finish.
There are two main types of chrome plating: decorative and hard chrome.
Decorative chrome plating provides a shiny appearance with a thin layer of chromium.
Hard chrome plating, on the other hand, offers thicker layers, enhancing wear resistance and reducing friction.
Zinc Plating Solutions
Zinc plating is commonly used to protect steel surfaces from corrosion.
The process involves immersing the steel component in a zinc-containing solution.
The zinc layer acts as a sacrificial coating, corroding first and thereby protecting the underlying steel.
There are several variations of zinc plating solutions, including acid zinc, alkaline zinc, and cyanide zinc.
Each type offers different advantages in terms of adhesion, corrosion resistance, and ease of use.
Selection Requirements for Plating Solutions
Choosing the right plating solution for a manufacturing process involves considering several factors.
These factors ensure that the chosen method meets the desired performance and quality standards.
Material Compatibility
The first consideration is the compatibility of the plating solution with the material being plated.
Different metals and alloys respond differently to various plating processes.
It is crucial to select a plating solution that will bond effectively with the base material.
For example, while nickel plating is suitable for many metals, it may not adhere well to certain aluminum alloys.
In such cases, a different method or pre-treatment might be necessary.
Purpose of Plating
The intended purpose of the plating also plays a significant role in the selection process.
Is the primary goal to enhance aesthetics, improve corrosion resistance, or increase hardness?
Understanding the primary function helps in choosing the appropriate plating solution.
For aesthetic applications, decorative chrome or gold plating might be preferred.
For corrosion resistance, zinc or nickel plating may be more suitable.
Hard chrome or electroless nickel plating is usually chosen for applications requiring increased durability and wear resistance.
Thickness Requirements
The thickness of the plating layer is another consideration.
Different applications require different coating thicknesses.
For instance, decorative coatings generally have a thinner layer than industrial coatings designed for wear resistance.
Hard chrome plating often requires a thicker application, which can impact manufacturing time and costs.
It is essential to determine the required thickness when selecting a plating solution to ensure it meets the application’s demands.
Environmental and Safety Concerns
Environmental and safety regulations are critical factors in the selection of plating solutions.
Some plating processes involve hazardous chemicals and produce toxic waste.
Compliance with environmental standards and ensuring worker safety are paramount.
For instance, cyanide-based zinc plating solutions are effective but pose significant health and environmental risks.
Alternatives like alkaline or acid zinc solutions provide safer options while still delivering good results.
Cost Considerations
Cost is always a factor in manufacturing decisions.
Different plating solutions vary in their cost due to materials, labor, energy, and waste disposal requirements.
Balancing cost with performance and quality is essential to achieving a cost-effective solution.
While gold plating offers excellent conductivity and aesthetics, it is also one of the most expensive options.
In contrast, zinc plating provides cost-effective corrosion protection but may not deliver the same level of aesthetic appeal.
Processing Time
The time required for the plating process can impact production schedules and overall efficiency.
Some methods, like electroless plating, can be faster and more uniform but might require longer preparation and activation times.
Understanding the processing time helps in planning manufacturing timelines and ensuring that production efficiency is maintained.
Electroless nickel plating, for example, provides excellent uniformity but may take longer compared to electroplating.
In conclusion, selecting the appropriate plating solution in manufacturing involves a comprehensive evaluation of material compatibility, purpose, thickness requirements, environmental concerns, cost, and processing time.
By carefully considering these factors, manufacturers can achieve high-quality, durable, and aesthetically pleasing finishes that meet the specific needs of their products.
As the industry continues to evolve, advancements in plating technologies will likely offer even more options for achieving optimal results.
資料ダウンロード
QCD調達購買管理クラウド「newji」は、調達購買部門で必要なQCD管理全てを備えた、現場特化型兼クラウド型の今世紀最高の購買管理システムとなります。
ユーザー登録
調達購買業務の効率化だけでなく、システムを導入することで、コスト削減や製品・資材のステータス可視化のほか、属人化していた購買情報の共有化による内部不正防止や統制にも役立ちます。
NEWJI DX
製造業に特化したデジタルトランスフォーメーション(DX)の実現を目指す請負開発型のコンサルティングサービスです。AI、iPaaS、および先端の技術を駆使して、製造プロセスの効率化、業務効率化、チームワーク強化、コスト削減、品質向上を実現します。このサービスは、製造業の課題を深く理解し、それに対する最適なデジタルソリューションを提供することで、企業が持続的な成長とイノベーションを達成できるようサポートします。
オンライン講座
製造業、主に購買・調達部門にお勤めの方々に向けた情報を配信しております。
新任の方やベテランの方、管理職を対象とした幅広いコンテンツをご用意しております。
お問い合わせ
コストダウンが利益に直結する術だと理解していても、なかなか前に進めることができない状況。そんな時は、newjiのコストダウン自動化機能で大きく利益貢献しよう!
(Β版非公開)