- お役立ち記事
- Optimize and Control Electrolytic Conditions: Manage electrolytic conditions to improve quality and production efficiency of metal plating processes
Optimize and Control Electrolytic Conditions: Manage electrolytic conditions to improve quality and production efficiency of metal plating processes
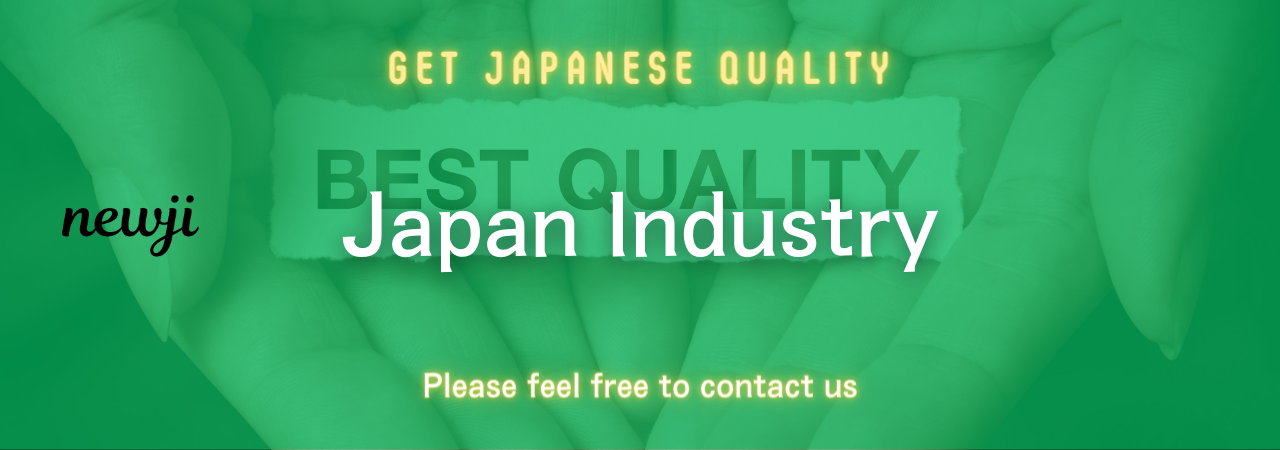
Metal plating is an essential process in various industries, from automotive to electronics.
One of the critical factors that influence the efficiency and quality of metal plating is the electrolytic conditions used during the process.
Properly managing these conditions can significantly improve the outcome of the plating procedure.
This article will provide insights into optimizing and controlling electrolytic conditions to boost production efficiency and enhance the quality of metal plating.
目次
Understanding Electrolytic Conditions
Electrolytic conditions refer to the environment within which the electroplating process occurs.
This includes the electrolyte solution, temperature, current density, and pH level.
Each factor plays a vital role in determining the overall effectiveness of the plating process.
Incorrect conditions can result in poor adhesion, uneven coatings, and other defects that compromise the quality of the plated metal.
The Role of Electrolyte Solution
Composition
The composition of the electrolyte solution is crucial for achieving the desired plating results.
Different metals require specific electrolytes for effective deposition.
For instance, copper plating typically uses a copper sulfate-sulfuric acid solution, while nickel plating employs a nickel sulfate-chloride solution.
Selecting the appropriate electrolyte for the metal being plated ensures proper ion exchange and adhesion during the process.
Concentration
In addition to composition, the concentration of the electrolyte solution significantly impacts the plating quality.
A higher concentration of metal ions in the solution generally leads to a faster plating rate.
However, excessive concentration can cause rough and uneven coatings.
Conversely, a solution with too low a concentration may result in incomplete or thin layers of metal.
Striking the right balance is essential for optimal plating performance.
Temperature Control
Temperature is another critical factor in the electrolytic process.
Maintaining the correct temperature can enhance the efficiency of the plating process and improve the quality of the final product.
Effects on Plating Rate
Temperature directly affects the rate at which metal ions are reduced and deposited onto the substrate.
Higher temperatures generally increase the plating rate due to enhanced ion mobility and reduced solution viscosity.
However, excessively high temperatures can lead to undesirable side reactions, such as hydrogen embrittlement or oxidation of the substrate.
Influence on Coating Quality
The temperature also plays a role in determining the morphology and structure of the plated layer.
Optimal temperature conditions promote uniform deposition and smooth coatings.
Inconsistent temperatures, on the other hand, can result in rough, porous, or brittle deposits.
It is crucial to monitor and control the temperature throughout the plating process to ensure high-quality results.
Managing Current Density
Current density, defined as the amount of electrical current per unit area of the substrate, is a vital parameter in electroplating.
Properly managing current density can prevent common plating defects and enhance the overall process.
Optimal Range
Each metal has an optimal current density range for effective plating.
Operating within this range ensures consistent deposition and strong adhesion.
Operating outside the optimal range can cause issues such as burning (at high current densities) or insufficient deposition (at low current densities).
Current Distribution
Uniform current distribution across the surface of the substrate is essential for achieving even coatings.
Factors such as the geometry of the substrate and the positioning of the electrodes influence current distribution.
Using auxiliary anodes or rotating the substrate can help achieve more uniform current distribution, leading to better plating results.
Importance of pH Levels
The pH level of the electrolyte solution is another critical factor that affects the plating process and the quality of the coating.
Impact on Metal Ion Availability
The pH level influences the solubility and availability of metal ions in the electrolyte solution.
Maintaining the correct pH ensures that a sufficient concentration of metal ions is available for deposition.
Too high or too low pH levels can lead to precipitation of metal hydroxides, reducing the efficiency of the plating process.
Effect on Hydrogen Evolution
The pH also impacts the evolution of hydrogen gas during electroplating.
Excessive hydrogen evolution can cause porosity and reduced adhesion of the metallic coating.
Keeping the pH within the optimal range minimizes hydrogen evolution and improves the quality of the plated layer.
Monitoring and Adjusting Electrolytic Conditions
Regular monitoring and adjustment of electrolytic conditions are essential for achieving consistent and high-quality plating results.
Implementing automated systems and sensors to measure parameters such as temperature, current density, and pH can enhance process control.
Routine maintenance and calibration of equipment ensure accurate monitoring and adjustments.
Quality Control
Implementing a robust quality control system is crucial for detecting and addressing issues related to electrolytic conditions.
Periodic testing of the electrolyte solution for contaminants and metal ion concentration helps maintain the optimal composition.
Using visual inspection and non-destructive testing methods can identify surface defects early, allowing for timely corrective actions.
Continuous Improvement
Adopting a continuous improvement approach to managing electrolytic conditions can lead to sustained enhancements in plating quality and efficiency.
Analyzing data from previous plating operations and incorporating feedback from quality control inspections can help identify areas for improvement.
Implementing changes and monitoring their impact ensures that the process evolves and adapts to produce consistently excellent results.
Optimizing and controlling electrolytic conditions are paramount for achieving high-quality and efficient metal plating.
Understanding the roles of electrolyte composition, temperature, current density, and pH levels in the plating process enables better management of these factors.
Regular monitoring, quality control, and continuous improvement practices are essential for maintaining optimal electrolytic conditions.
By paying attention to these details, manufacturers can enhance their plating operations and produce superior metal products.
資料ダウンロード
QCD調達購買管理クラウド「newji」は、調達購買部門で必要なQCD管理全てを備えた、現場特化型兼クラウド型の今世紀最高の購買管理システムとなります。
ユーザー登録
調達購買業務の効率化だけでなく、システムを導入することで、コスト削減や製品・資材のステータス可視化のほか、属人化していた購買情報の共有化による内部不正防止や統制にも役立ちます。
NEWJI DX
製造業に特化したデジタルトランスフォーメーション(DX)の実現を目指す請負開発型のコンサルティングサービスです。AI、iPaaS、および先端の技術を駆使して、製造プロセスの効率化、業務効率化、チームワーク強化、コスト削減、品質向上を実現します。このサービスは、製造業の課題を深く理解し、それに対する最適なデジタルソリューションを提供することで、企業が持続的な成長とイノベーションを達成できるようサポートします。
オンライン講座
製造業、主に購買・調達部門にお勤めの方々に向けた情報を配信しております。
新任の方やベテランの方、管理職を対象とした幅広いコンテンツをご用意しております。
お問い合わせ
コストダウンが利益に直結する術だと理解していても、なかなか前に進めることができない状況。そんな時は、newjiのコストダウン自動化機能で大きく利益貢献しよう!
(Β版非公開)