- お役立ち記事
- DX in the spinning process realizes extremely high-quality yarns
DX in the spinning process realizes extremely high-quality yarns
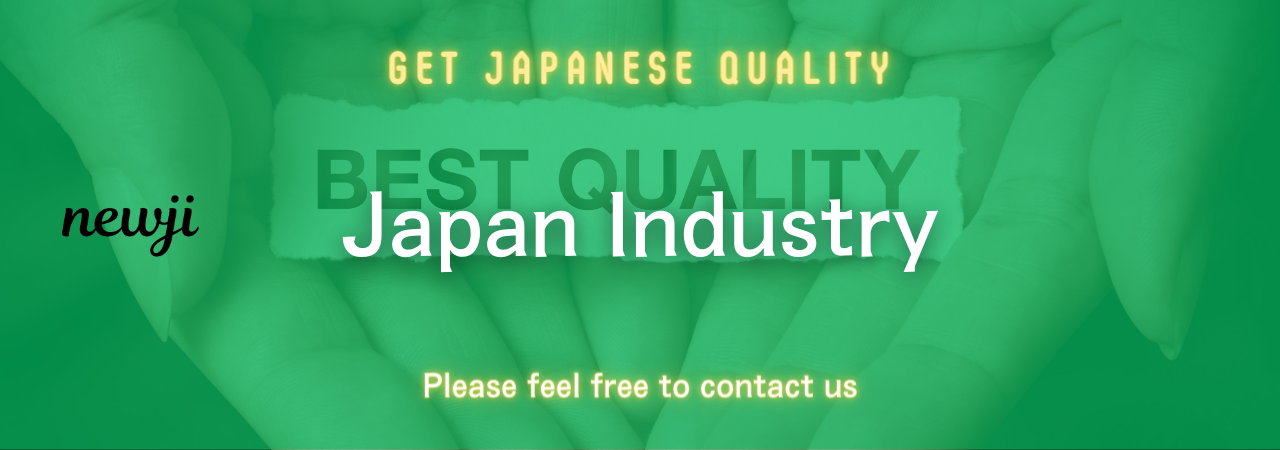
Digital transformation, or DX, in the spinning process is revolutionizing the textile industry. By leveraging advanced technologies, this transformation is enabling the production of high-quality yarns like never before. Understanding the intricate details of this evolution is crucial for manufacturers aiming to stay at the forefront of the industry.
目次
What is DX in Spinning?
Digital transformation in spinning refers to the integration of digital technologies into the various stages of the spinning process. From fiber preparation to the final winding of yarn, digital tools and data analytics are being employed to enhance efficiency, quality, and cost-effectiveness. The goal is to create a seamless, automated, and intelligent production line that maximizes productivity and minimizes defects.
How Technology Enhances Yarn Quality
IoT and Smart Sensors
The Internet of Things (IoT) and smart sensors play a pivotal role in DX for spinning. Smart sensors placed throughout the production line collect real-time data on various parameters such as temperature, humidity, and fiber tension. This data is then analyzed to optimize the spinning conditions. By maintaining optimal environmental conditions and monitoring fiber quality, manufacturers can significantly reduce the occurrence of defects and inconsistencies in yarn quality.
Automation and Robotics
Automation and robotics are transforming the labor-intensive spinning process into a highly efficient and consistent operation. Automated machines handle tasks such as carding, drawing, and roving with precision and speed that are impossible to achieve manually. Robotics systems can also perform continuous monitoring and adjustments, ensuring that the spinning process remains within the set parameters for producing high-quality yarns.
Machine Learning and AI
Machine learning and artificial intelligence (AI) are integral to predictive maintenance and quality control in spinning. These technologies analyze historical and real-time data to predict potential equipment failures and quality issues before they occur. By addressing problems proactively, manufacturers can prevent downtime and maintain a steady production of superior yarns. AI algorithms can also fine-tune the spinning process, making adjustments based on the type of fiber and desired yarn characteristics.
Advanced Materials and Nanotechnology
The introduction of advanced materials and nanotechnology is another aspect of DX in spinning. These innovations allow for the creation of yarns with enhanced strength, flexibility, and other desirable properties. For instance, nanotechnology can be used to apply coatings that make yarns more resistant to wear and tear. By leveraging such technologies, manufacturers can produce high-quality yarns that meet the specific needs of various applications, from fashion to industrial uses.
Benefits of DX in Spinning
Improved Yarn Quality
The most significant benefit of DX in spinning is the dramatic improvement in yarn quality. With precise control over every aspect of the production process, manufacturers can produce yarns with consistent thickness, strength, and texture. This consistency is critical for ensuring that the final textile products are of the highest quality.
Enhanced Efficiency and Productivity
Digital transformation streamlines the spinning process, reducing the time and labor required for production. Automation eliminates bottlenecks and minimizes human errors, resulting in higher efficiency and productivity. Manufacturers can produce more yarn in less time without compromising on quality, leading to increased profitability.
Cost Savings
By optimizing the spinning process through technology, manufacturers can achieve significant cost savings. Reduced wastage, lower energy consumption, and fewer defects mean lower production costs. Additionally, predictive maintenance helps in avoiding costly breakdowns and repairs, further enhancing the cost-effectiveness of the production process.
Flexibility and Customization
Digital transformation offers greater flexibility and customization in yarn production. Manufacturers can easily adjust the production parameters to create yarns with specific properties. This capability is particularly beneficial for meeting the diverse requirements of different industries. Whether it’s producing ultra-soft yarns for high-end fashion or durable yarns for industrial use, DX makes it possible to cater to varied demands with precision.
Challenges and Future Prospects
Initial Investment and Training
One of the primary challenges of implementing DX in spinning is the initial investment in advanced technologies. Upgrading existing machinery or purchasing new equipment can be costly. Additionally, staff need to be trained to operate and maintain the new systems. However, the long-term benefits in terms of efficiency, quality, and cost savings often outweigh the initial expenditure.
Integration and Compatibility
Integrating new technologies with existing systems can be complex. Ensuring compatibility between different machines and software platforms is crucial for a smooth transition to a digitally transformed production line. Manufacturers may need to work closely with technology providers to address these integration challenges.
Future Innovations
The future of DX in spinning holds immense potential. Continuous advancements in AI, IoT, and nanotechnology will further enhance the capabilities of spinning processes. Innovations such as real-time quality control, fully automated production lines, and smart materials will redefine the standards of yarn quality. As these technologies become more accessible and affordable, even small and medium-sized manufacturers will be able to leverage DX for competitive advantage.
In conclusion, digital transformation in the spinning process is paving the way for the production of extremely high-quality yarns. Through the integration of IoT, automation, AI, and advanced materials, manufacturers can achieve unparalleled efficiency, consistency, and customization in yarn production. While there are challenges to overcome, the benefits of DX make it an invaluable asset for the textile industry, promising a future of superior quality and innovative textile products.
資料ダウンロード
QCD調達購買管理クラウド「newji」は、調達購買部門で必要なQCD管理全てを備えた、現場特化型兼クラウド型の今世紀最高の購買管理システムとなります。
ユーザー登録
調達購買業務の効率化だけでなく、システムを導入することで、コスト削減や製品・資材のステータス可視化のほか、属人化していた購買情報の共有化による内部不正防止や統制にも役立ちます。
NEWJI DX
製造業に特化したデジタルトランスフォーメーション(DX)の実現を目指す請負開発型のコンサルティングサービスです。AI、iPaaS、および先端の技術を駆使して、製造プロセスの効率化、業務効率化、チームワーク強化、コスト削減、品質向上を実現します。このサービスは、製造業の課題を深く理解し、それに対する最適なデジタルソリューションを提供することで、企業が持続的な成長とイノベーションを達成できるようサポートします。
オンライン講座
製造業、主に購買・調達部門にお勤めの方々に向けた情報を配信しております。
新任の方やベテランの方、管理職を対象とした幅広いコンテンツをご用意しております。
お問い合わせ
コストダウンが利益に直結する術だと理解していても、なかなか前に進めることができない状況。そんな時は、newjiのコストダウン自動化機能で大きく利益貢献しよう!
(Β版非公開)