- お役立ち記事
- “Revolutionizing Vietnam Plastic Processing: Insights from Japanese Manufacturing Excellence”
“Revolutionizing Vietnam Plastic Processing: Insights from Japanese Manufacturing Excellence”
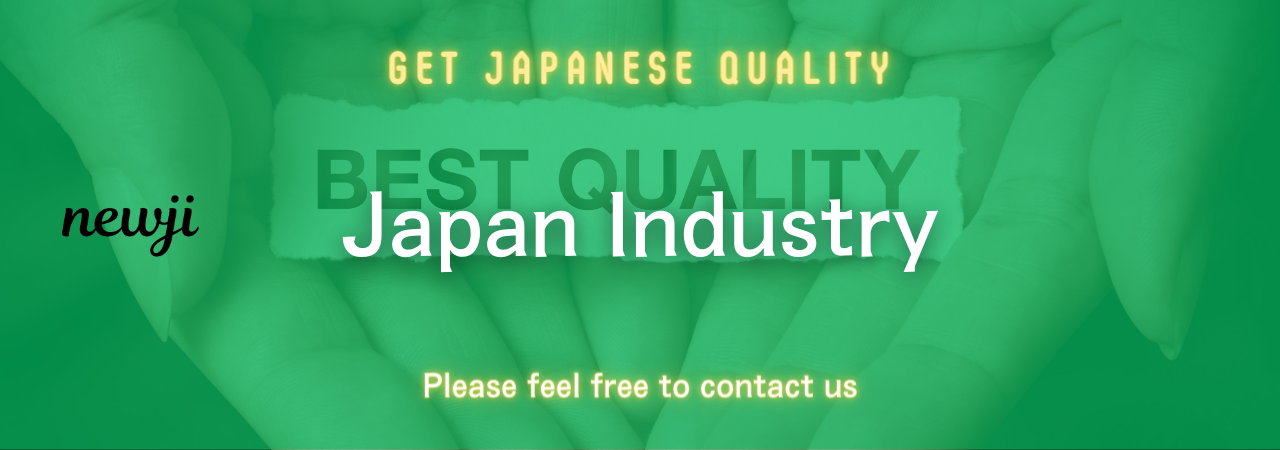
Vietnam’s plastic processing industry has seen tremendous growth over recent years, driven by increasing domestic demand and export opportunities.
However, amid this rapid development, there’s a critical need to adopt and integrate best practices from leading manufacturing nations.
One such exemplar is Japan, renowned for its advanced manufacturing techniques, meticulous quality control, and efficient production management.
目次
Understanding the Vietnamese Plastic Processing Industry
Vietnam’s plastic processing industry plays a pivotal role in the country’s economic fabric.
This sector feeds into various industries such as packaging, automotive, electronics, and building materials.
Vietnamese manufacturers have been striving to meet global standards, but challenges such as quality consistency, efficiency, and technological upgrades remain prevalent.
Challenges in the Industry
Vietnamese plastic processing companies face several challenges:
– Quality and Consistency: Maintaining uniform quality across large production batches.
– Technological Upgrades: High costs and a lack of technical know-how impede the adoption of cutting-edge technology.
– Skilled Workforce: A shortage of skilled labor for specialized manufacturing tasks.
– Supply Chain Efficiency: Inefficiencies and delays in the supply chain affect overall productivity.
Opportunities for Growth
Despite these challenges, there are remarkable opportunities for growth:
– Increased Demand: Rising domestic consumption and export potential.
– Government Support: Favorable policies and incentives for industrial modernization.
– Foreign Investment: Attracting global companies to set up operations in Vietnam.
– Technological Integration: Potential to adopt advanced technologies to enhance efficiency and quality.
Learning from Japanese Manufacturing Excellence
Japan has been a pioneer in the manufacturing arena, particularly in plastic processing.
The methods, practices, and technologies developed and perfected in Japan can significantly benefit Vietnamese manufacturers.
Japanese manufacturing emphasizes precision, efficiency, and quality.
These principles form the foundation of their success and can be adapted to the Vietnamese context for substantial improvements.
Technological Advancements
Japan’s advancements in plastic processing technology are a benchmark for the industry.
These include:
– Precision Injection Molding: Ensuring exact specifications and reducing waste.
– Automation and Robotics: Enhancing productivity and minimizing human error.
– Advanced Materials: Developing and using high-performance plastics for specialized applications.
– Real-Time Monitoring: Utilizing IoT and AI for real-time process monitoring and quality control.
Quality Control
Japan’s rigorous quality control systems ensure minimal defects and high consistency.
Implementing similar quality control protocols can drastically improve the output quality of Vietnamese manufacturers.
– Kaizen: The philosophy of continuous improvement, focusing on small, incremental changes over time.
– TQM (Total Quality Management): A comprehensive approach that involves all employees in quality control processes.
Advantages and Disadvantages of Adopting Japanese Practices
While there are numerous benefits to adopting Japanese manufacturing practices, there are also potential challenges that need to be addressed.
Advantages
– Enhanced Quality: Improved precision and consistency in production.
– Increased Efficiency: Streamlined processes and reduced downtime.
– Technological Leadership: Staying ahead with cutting-edge technologies.
– Competitive Edge: Ability to meet global standards and attract international clients.
Disadvantages
– High Initial Costs: Significant investment required for technological upgrades and training.
– Cultural Adaptation: Adapting Japanese practices to the local context and workforce culture.
– Skill Development: Need for extensive training and skill development programs.
– Resistance to Change: Overcoming resistance from within the organization.
Supplier Negotiation Techniques
Effective negotiation with suppliers is crucial for fostering long-term, mutually beneficial relationships.
Drawing lessons from Japanese strategies, the following techniques can be employed.
Building Trust
– Long-Term Relationships: Focus on developing long-term partnerships rather than one-off transactions.
– Transparency: Maintain open and honest communication regarding expectations and capabilities.
– Reliability: Ensure timely payments and fulfill commitments to build a reputation for reliability.
Value Addition
– Quality Over Cost: Prioritize quality and value addition over simply reducing costs.
– Collaborative Problem Solving: Work together with suppliers to solve issues and improve processes.
– Innovation: Encourage suppliers to innovate and improve their offerings.
Market Conditions
Understanding the current market conditions is essential for making informed procurement decisions.
Global Trends
– Increasing Demand for Sustainability: Growing focus on eco-friendly materials and sustainable practices.
– Technological Advancements: Rapid pace of technological innovation, offering new opportunities and challenges.
– Trade Policies: Evolving trade policies and tariffs impacting global supply chains.
Local Dynamics
– Economic Growth: Strong economic growth driving domestic demand.
– Government Policies: Supportive policies fostering industrial development.
– Competitive Landscape: Increasing competition from local and international players.
Best Practices for Vietnamese Manufacturers
Adopting best practices can significantly enhance productivity, efficiency, and quality in the manufacturing process.
Embrace Continuous Improvement
– Implement Kaizen: Encourage a culture of continuous improvement at all levels.
– Regular Training: Conduct regular training sessions for employees to improve skills and knowledge.
– Feedback Loops: Establish feedback mechanisms to identify areas for improvement.
Invest in Technology
– Automation: Invest in automation technologies to enhance productivity and reduce errors.
– Advanced Materials: Invest in research and development to adopt advanced materials.
– Real-Time Monitoring: Utilize IoT and AI for real-time monitoring and quality control.
Quality Control Systems
– TQM: Implement Total Quality Management systems to ensure high standards.
– Regular Audits: Conduct regular audits to identify and rectify any quality issues.
– Supplier Quality Management: Work closely with suppliers to maintain quality standards.
Supply Chain Optimization
– Efficient Logistics: Streamline logistics to reduce delays and improve efficiency.
– Inventory Management: Implement effective inventory management systems to avoid stockouts and overstocking.
– Collaboration: Foster strong collaboration with suppliers and partners for better coordination.
Conclusion
The integration of Japanese manufacturing excellence into Vietnam’s plastic processing industry holds significant potential for transforming the sector.
By adopting best practices in technology, quality control, and supplier management, Vietnamese manufacturers can overcome existing challenges and capitalize on growth opportunities.
By emphasizing continuous improvement, investing in advanced technologies, and fostering strong supplier relationships, Vietnam’s plastic processing industry can not only meet but exceed global standards.
The journey towards revolutionizing the industry is paved with learning, adaptability, and a commitment to excellence.
With the right strategies and practices, inspired by Japanese manufacturing success, Vietnamese manufacturers can achieve remarkable progress and a competitive edge in the global market.
資料ダウンロード
QCD調達購買管理クラウド「newji」は、調達購買部門で必要なQCD管理全てを備えた、現場特化型兼クラウド型の今世紀最高の購買管理システムとなります。
ユーザー登録
調達購買業務の効率化だけでなく、システムを導入することで、コスト削減や製品・資材のステータス可視化のほか、属人化していた購買情報の共有化による内部不正防止や統制にも役立ちます。
NEWJI DX
製造業に特化したデジタルトランスフォーメーション(DX)の実現を目指す請負開発型のコンサルティングサービスです。AI、iPaaS、および先端の技術を駆使して、製造プロセスの効率化、業務効率化、チームワーク強化、コスト削減、品質向上を実現します。このサービスは、製造業の課題を深く理解し、それに対する最適なデジタルソリューションを提供することで、企業が持続的な成長とイノベーションを達成できるようサポートします。
オンライン講座
製造業、主に購買・調達部門にお勤めの方々に向けた情報を配信しております。
新任の方やベテランの方、管理職を対象とした幅広いコンテンツをご用意しております。
お問い合わせ
コストダウンが利益に直結する術だと理解していても、なかなか前に進めることができない状況。そんな時は、newjiのコストダウン自動化機能で大きく利益貢献しよう!
(Β版非公開)