- お役立ち記事
- Achieving both unmanned machining and high precision through DX of chucking processes
Achieving both unmanned machining and high precision through DX of chucking processes
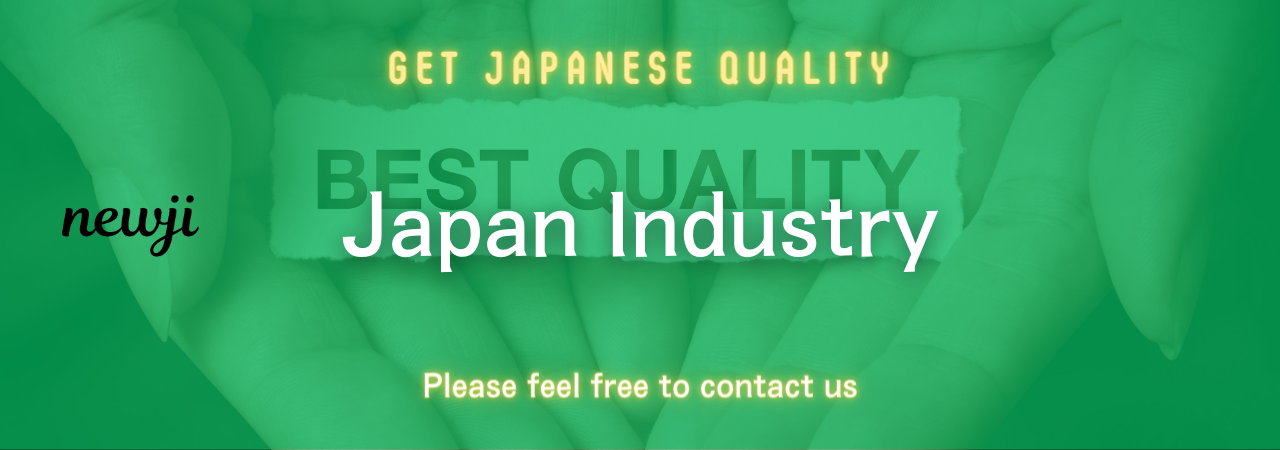
In today’s rapidly evolving industrial landscape, the integration of digital transformation (DX) with traditional machining processes has become essential.
One area where DX can significantly enhance efficiency and precision is in the chucking process.
Chucking is a critical step in machining where a workpiece is held securely in place.
Innovations in this domain can lead to both unmanned machining and high precision.
目次
Understanding Chucking Processes
Chucking involves the use of specialized devices to hold a workpiece steady during machining.
Traditional chucking methods are manual and labor-intensive, requiring skilled operators to ensure the workpiece is correctly positioned.
However, manual chucking can result in human errors, which can compromise the precision of the final product.
The Need for High Precision
In industries such as aerospace, automotive, and medical device manufacturing, precision is paramount.
Even a minor deviation can result in a product that does not meet required specifications.
As quality standards become increasingly stringent, achieving high precision in machining processes is more important than ever.
The Role of Unmanned Machining
Unmanned machining refers to automated operations where machines perform tasks without human intervention.
This not only reduces labor costs but also minimizes the risk of human error.
By integrating digital solutions into chucking processes, it becomes possible to achieve unmanned machining with high precision.
Integrating Digital Solutions
Digital transformation in chucking processes involves the use of advanced technologies such as sensors, artificial intelligence (AI), and the Internet of Things (IoT).
These technologies work together to monitor and control the chucking process, ensuring optimal performance and consistency.
Sensors for Real-Time Monitoring
Sensors play a crucial role in modern chucking systems.
These devices provide real-time data on various parameters such as pressure, temperature, and alignment.
By continuously monitoring these factors, sensors help in maintaining the stability of the chucking process, thus enhancing precision.
Artificial Intelligence for Predictive Maintenance
AI can analyze the data collected by sensors to predict potential issues before they become critical.
For example, if a sensor detects an unusual vibration, AI algorithms can determine whether this indicates a problem with the chuck or another component of the machine.
Predictive maintenance can prevent breakdowns and ensure uninterrupted operations.
Internet of Things for Enhanced Connectivity
IoT enables machines to communicate with each other and with central control systems.
This connectivity allows for seamless integration of various components involved in the chucking process.
It also facilitates remote monitoring and control, making it possible to manage the chucking process from anywhere.
Benefits of Digitally Transformed Chucking Processes
Integrating digital solutions into chucking processes offers several advantages.
Increased Precision
With real-time monitoring and control, digital chucking systems can achieve a higher level of precision than manual methods.
This is particularly important in industries where even the smallest error can have significant consequences.
Reduced Labor Costs
By automating the chucking process, companies can reduce their reliance on skilled operators.
This leads to lower labor costs and allows operators to focus on more complex tasks.
Minimized Human Error
Human errors are inevitable in manual processes.
Digital systems, on the other hand, are designed to operate consistently, reducing the likelihood of errors.
Enhanced Productivity
Digital chucking systems can operate continuously without the need for breaks.
This leads to increased productivity and faster turnaround times for machining operations.
Case Studies of Digital Transformation in Chucking Processes
Several companies have successfully integrated digital solutions into their chucking processes, achieving remarkable results.
Case Study 1: Aerospace Industry
An aerospace manufacturing company implemented a digital chucking system using IoT and AI technologies.
The system provided real-time data on the condition of the chuck and other components.
By using predictive maintenance, the company was able to reduce downtime by 30% and improve the precision of its components by 20%.
Case Study 2: Automotive Industry
An automotive parts manufacturer introduced sensors and AI into its chucking processes.
The sensors monitored pressure and alignment, while AI analyzed the data to detect any anomalies.
This allowed the company to detect and address issues before they affected the final product.
As a result, the company achieved a 25% increase in productivity and a 15% reduction in scrap rates.
Future Trends in Chucking Process Digital Transformation
The integration of digital solutions into chucking processes is still evolving.
Several emerging trends are likely to shape the future of this field.
Advanced AI Algorithms
As AI technology continues to advance, more sophisticated algorithms will emerge.
These algorithms will be able to analyze data more accurately and predict issues with even greater precision.
Increased Adoption of IoT
The adoption of IoT in industrial processes is expected to increase.
This will lead to greater connectivity and integration between different components of the chucking process.
Development of Smart Chucks
Engineers are working on developing smart chucks that can adjust themselves automatically based on real-time data.
These chucks will further enhance precision and reduce the need for manual intervention.
In conclusion, the digital transformation of chucking processes offers significant benefits, including increased precision, reduced labor costs, minimized human error, and enhanced productivity.
By integrating advanced technologies such as sensors, AI, and IoT, companies can achieve both unmanned machining and high precision.
As these technologies continue to evolve, the future of digitally transformed chucking processes looks promising, with the potential for even greater advancements.
資料ダウンロード
QCD調達購買管理クラウド「newji」は、調達購買部門で必要なQCD管理全てを備えた、現場特化型兼クラウド型の今世紀最高の購買管理システムとなります。
ユーザー登録
調達購買業務の効率化だけでなく、システムを導入することで、コスト削減や製品・資材のステータス可視化のほか、属人化していた購買情報の共有化による内部不正防止や統制にも役立ちます。
NEWJI DX
製造業に特化したデジタルトランスフォーメーション(DX)の実現を目指す請負開発型のコンサルティングサービスです。AI、iPaaS、および先端の技術を駆使して、製造プロセスの効率化、業務効率化、チームワーク強化、コスト削減、品質向上を実現します。このサービスは、製造業の課題を深く理解し、それに対する最適なデジタルソリューションを提供することで、企業が持続的な成長とイノベーションを達成できるようサポートします。
オンライン講座
製造業、主に購買・調達部門にお勤めの方々に向けた情報を配信しております。
新任の方やベテランの方、管理職を対象とした幅広いコンテンツをご用意しております。
お問い合わせ
コストダウンが利益に直結する術だと理解していても、なかなか前に進めることができない状況。そんな時は、newjiのコストダウン自動化機能で大きく利益貢献しよう!
(Β版非公開)