- お役立ち記事
- Burr Prevention Measures in Injection Molding: Key to Improving Accuracy
Burr Prevention Measures in Injection Molding: Key to Improving Accuracy
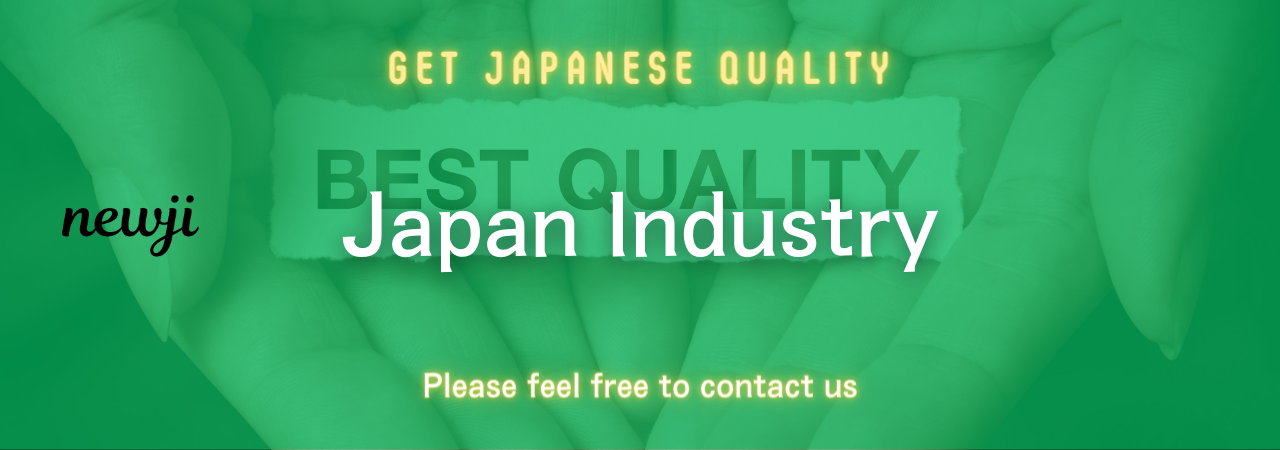
Injection molding is a popular manufacturing process that involves injecting molten material into a mold to create various products.
The efficiency and accuracy of this method have made it a preferred choice for producing everything from small plastic components to large automotive parts.
However, like any manufacturing process, injection molding comes with its share of challenges.
One of the most common issues faced is the formation of burrs.
Burrs are unwanted pieces of material that protrude from the edges of a molded part, and they can significantly reduce the quality and precision of the final product.
In this article, we’ll delve into various burr prevention measures in injection molding that can help improve the accuracy of your production process.
目次
Understanding Burrs in Injection Molding
What Are Burrs?
Burrs are unwanted, excess materials that appear on the edges or surface of a molded part.
They usually form during the molding process when the molten material leaks out of the mold cavity through small gaps or imperfections.
Once the material solidifies, it leaves behind these excess protrusions that need to be removed, a process known as deburring.
Failing to address burrs can affect the product’s overall quality, appearance, and functionality.
Why Are Burrs a Problem?
Burrs not only degrade the aesthetics of a product but also impact its performance.
For example, in electrical components, burrs can cause short circuits, leading to malfunction.
In mechanical parts, they can create misalignments, negatively affecting the product’s performance and longevity.
Moreover, the deburring process is time-consuming and adds to the overall cost of production.
Therefore, taking preventative measures to eliminate the formation of burrs is crucial for maintaining high-quality standards.
Key Burr Prevention Measures
Choosing the Right Material
Selecting the right material for your injection molding process is the first step in preventing burr formation.
Materials with lower viscosities tend to flow more consistently into the mold cavity, reducing the likelihood of material leakage.
Similarly, materials with good thermal stability are less likely to degrade and form burrs under high temperature and pressure conditions.
Mold Design Considerations
The design of the mold plays a significant role in minimizing burr formation.
Ensure that the mold cavity is well-engineered and free of gaps where the molten material could leak.
Use high-quality steel or other durable materials to construct the mold, as this will offer better resistance to wear and tear.
Additionally, incorporating appropriate venting systems can help manage air pressure and reduce the chances of burr development.
Precise Temperature Control
Maintaining precise temperature control during the injection molding process is critical for preventing burrs.
Both the mold and the molten material should be kept at the optimal temperature to ensure smooth flow and even cooling.
Overheating can cause the material to become too fluid, increasing the chances of leakage and burr formation.
Conversely, inadequate heating can cause improper filling of the mold cavity, leading to defects.
Proper Clamping Force
The clamping force applied to the mold must be sufficient to keep it tightly closed during the injection process.
A weak clamping force can create openings where molten material can escape, forming burrs.
Conversely, excessive force may damage the mold and lead to other complications.
Always ensure the clamping force is adequately calibrated for the specific material and mold to achieve optimal results.
Injection Speed and Pressure
Controlling the speed and pressure at which the molten material is injected into the mold is essential for burr prevention.
High injection speeds and pressures can cause the material to overflow, leading to burr formation.
On the other hand, low speeds and pressures may result in incomplete filling of the mold cavity, causing defects.
Fine-tuning these parameters can significantly improve the quality of the final product.
Regular Mold Maintenance
Regular maintenance of the mold is vital for ensuring its longevity and performance.
Inspect the mold for signs of wear and tear, such as cracks or deformations, which can create gaps where burrs might form.
Clean the mold regularly to remove any residue or build-up that might affect its precision.
Conducting periodic maintenance checks can help identify and rectify potential issues before they escalate into bigger problems.
Utilizing Advanced Injection Molding Techniques
Advanced injection molding techniques such as gas-assisted injection molding or co-injection molding can help minimize burr formation.
These methods allow for better material distribution and controlled cooling, reducing the likelihood of defects.
While these techniques may require a higher initial investment, the long-term benefits in terms of quality and efficiency can be substantial.
Implementing Quality Control Measures
Lastly, incorporating robust quality control measures can help identify and address burrs early in the production process.
Use automated inspection systems or manual checks to monitor the quality of molded parts.
Implementing real-time monitoring tools can provide immediate feedback, allowing for quick adjustments to production parameters.
Conclusion
Burr prevention is essential for improving the accuracy and quality of injection-molded products.
By selecting the right materials, optimizing mold design, maintaining precise temperature control, and adjusting injection parameters, manufacturers can significantly reduce burr formation.
Regular mold maintenance and the adoption of advanced injection molding techniques further contribute to achieving high-quality, burr-free products.
Lastly, robust quality control measures ensure that any defects are identified and rectified promptly.
Implementing these burr prevention strategies can lead to more efficient production processes, reduced costs, and higher customer satisfaction.
資料ダウンロード
QCD調達購買管理クラウド「newji」は、調達購買部門で必要なQCD管理全てを備えた、現場特化型兼クラウド型の今世紀最高の購買管理システムとなります。
ユーザー登録
調達購買業務の効率化だけでなく、システムを導入することで、コスト削減や製品・資材のステータス可視化のほか、属人化していた購買情報の共有化による内部不正防止や統制にも役立ちます。
NEWJI DX
製造業に特化したデジタルトランスフォーメーション(DX)の実現を目指す請負開発型のコンサルティングサービスです。AI、iPaaS、および先端の技術を駆使して、製造プロセスの効率化、業務効率化、チームワーク強化、コスト削減、品質向上を実現します。このサービスは、製造業の課題を深く理解し、それに対する最適なデジタルソリューションを提供することで、企業が持続的な成長とイノベーションを達成できるようサポートします。
オンライン講座
製造業、主に購買・調達部門にお勤めの方々に向けた情報を配信しております。
新任の方やベテランの方、管理職を対象とした幅広いコンテンツをご用意しております。
お問い合わせ
コストダウンが利益に直結する術だと理解していても、なかなか前に進めることができない状況。そんな時は、newjiのコストダウン自動化機能で大きく利益貢献しよう!
(Β版非公開)