- お役立ち記事
- DX for Tube Benders Reduces Machining Time and Improves Quality
DX for Tube Benders Reduces Machining Time and Improves Quality
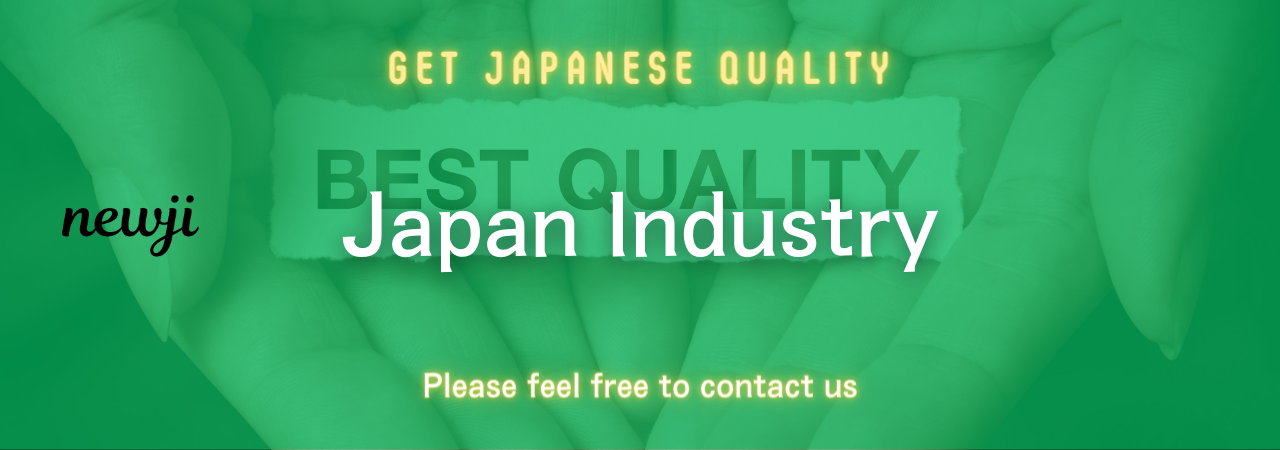
目次
Introduction to DX for Tube Bending
Digital transformation, commonly known as DX, is changing the way various industries operate.
One sector that benefits significantly from DX is the tube bending industry.
Tube benders, responsible for shaping and bending metallic tubes, are now more efficient and precise due to technological advancements.
This article will explore how DX for tube benders can reduce machining time and improve quality.
What is Tube Bending?
Tube bending is a manufacturing process where tubes of different materials are formed into specific shapes and angles.
This operation is crucial in industries such as automotive, aerospace, and construction.
However, traditional tube bending methods can be time-consuming and prone to errors.
This is where digital transformation steps in to make a big difference.
How DX Improves Tube Bending
Automation
One of the key advantages of digital transformation is automation.
Modern tube bending machines can operate autonomously with minimal human intervention.
Automated machines are equipped with advanced software that can accurately control the bending process.
This means that the time taken to bend a tube can be drastically reduced.
Additionally, automation ensures that each tube is bent to precise specifications, leaving no room for human error.
Data Analytics
Data analytics is another significant aspect of DX in tube bending.
By collecting and analyzing data from various stages of the bending process, manufacturers can identify areas for improvement.
For example, data can reveal the most efficient bending angles or the optimal speed for different materials.
With this information, operators can fine-tune their machines to perform more efficiently, thereby reducing machining time and improving the overall quality of the finished product.
Real-Time Monitoring
Digital transformation also enables real-time monitoring of the tube bending process.
Sensors and cameras can be integrated into the bending machines to provide live feedback on the bending operation.
This real-time data allows operators to make immediate adjustments if any issues arise, ensuring that the bending process remains efficient and accurate.
Moreover, real-time monitoring helps in maintaining consistent quality, as any defects can be promptly identified and corrected.
Enhanced Precision
Advanced software and algorithms used in modern tube bending machines ensure enhanced precision in the bending process.
Traditional methods often rely on manual measurements, which can lead to inconsistencies.
DX eliminates this issue by using precise digital measurements and controls.
Consequently, the tubes are bent exactly as required, resulting in higher-quality products that meet stringent industry standards.
Reducing Machining Time
Streamlined Workflow
One of the primary benefits of DX is the streamlined workflow it offers.
With automation and real-time monitoring, the tube bending process becomes much faster.
Operators can set up and execute bending operations with just a few clicks, reducing the setup time significantly.
Furthermore, the ability to quickly switch between different bending tasks means that multiple projects can be completed in a shorter timeframe.
Minimized Errors
Errors in the tube bending process can lead to costly rework and wasted materials.
By utilizing digital tools, these errors can be minimized.
Automated machines ensure that each tube is bent precisely according to the programmed specifications, reducing the likelihood of mistakes.
As a result, the time spent on quality checks and corrections is significantly reduced, further speeding up the machining process.
Optimized Maintenance
Digital transformation also plays a crucial role in the maintenance of tube bending machines.
Predictive maintenance, powered by data analytics, allows manufacturers to identify potential issues before they become critical.
This proactive approach helps in scheduling timely maintenance, reducing downtime, and keeping the machines running smoothly.
Consequently, the overall productivity of the tube bending process is increased, and machining time is further reduced.
Improving Quality
Consistent Results
One of the standout features of DX in tube bending is the ability to produce consistent results.
The use of advanced software and real-time monitoring ensures that each tube is bent with the same level of precision.
This consistency is crucial in industries where even minor deviations can lead to significant issues.
By maintaining consistent quality, manufacturers can meet the strict demands of their clients and build a reputation for reliability.
Enhanced Traceability
Traceability is essential in the manufacturing industry, as it allows for tracking the production history of each component.
With digital transformation, traceability is enhanced as all the data related to the bending process is recorded and stored.
This information includes the bending angles, material specifications, and machine settings used for each batch of tubes.
In case of any quality issues, manufacturers can quickly trace back to the root cause, making it easier to implement corrective actions and improve overall quality.
Compliance with Standards
Many industries have specific standards and regulations that must be met to ensure the safety and reliability of products.
DX helps tube bending manufacturers comply with these standards by providing precise control over the bending process.
Automated machines and real-time monitoring ensure that each tube meets the required specifications, reducing the risk of non-compliance.
This not only improves the quality of the products but also enhances the manufacturer’s credibility in the market.
Conclusion
Digital transformation is revolutionizing the tube bending industry by reducing machining time and improving quality.
Automation, data analytics, and real-time monitoring are some of the key aspects of DX that contribute to these improvements.
By adopting digital tools, tube bending manufacturers can streamline their workflows, minimize errors, and produce consistently high-quality products.
As technology continues to advance, the benefits of digital transformation in tube bending will only increase, making it an essential investment for any manufacturer looking to stay competitive in the market.
資料ダウンロード
QCD調達購買管理クラウド「newji」は、調達購買部門で必要なQCD管理全てを備えた、現場特化型兼クラウド型の今世紀最高の購買管理システムとなります。
ユーザー登録
調達購買業務の効率化だけでなく、システムを導入することで、コスト削減や製品・資材のステータス可視化のほか、属人化していた購買情報の共有化による内部不正防止や統制にも役立ちます。
NEWJI DX
製造業に特化したデジタルトランスフォーメーション(DX)の実現を目指す請負開発型のコンサルティングサービスです。AI、iPaaS、および先端の技術を駆使して、製造プロセスの効率化、業務効率化、チームワーク強化、コスト削減、品質向上を実現します。このサービスは、製造業の課題を深く理解し、それに対する最適なデジタルソリューションを提供することで、企業が持続的な成長とイノベーションを達成できるようサポートします。
オンライン講座
製造業、主に購買・調達部門にお勤めの方々に向けた情報を配信しております。
新任の方やベテランの方、管理職を対象とした幅広いコンテンツをご用意しております。
お問い合わせ
コストダウンが利益に直結する術だと理解していても、なかなか前に進めることができない状況。そんな時は、newjiのコストダウン自動化機能で大きく利益貢献しよう!
(Β版非公開)