- お役立ち記事
- Mastering Visual Inspection: Expert Techniques from Japanese Manufacturing
Mastering Visual Inspection: Expert Techniques from Japanese Manufacturing
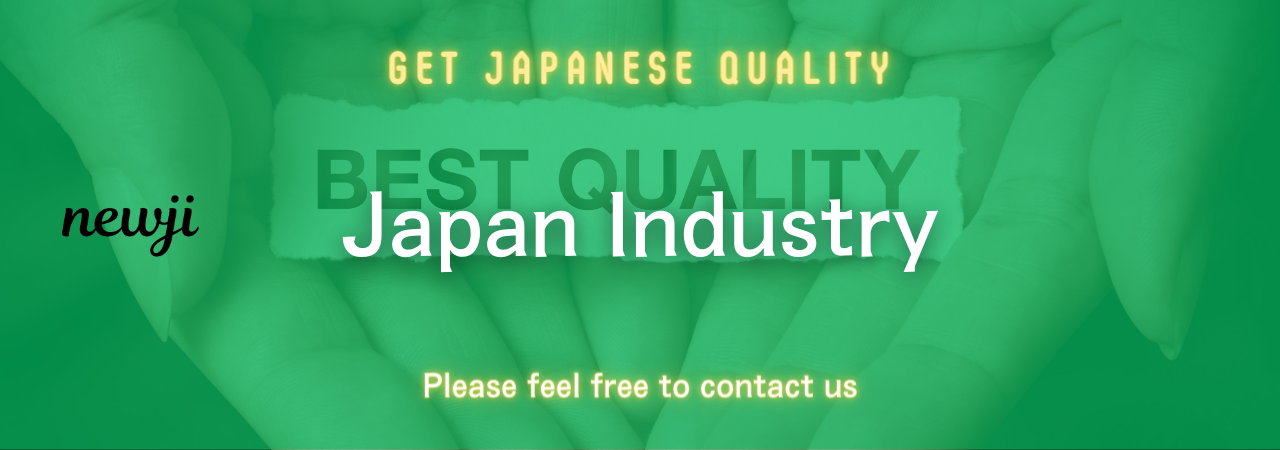
目次
Introduction to Visual Inspection
Visual inspection remains a cornerstone in the quality control process of manufacturing, particularly in Japan. The visual inspection process involves evaluating products using trained human or automated eyes to detect flaws that might be missed during other quality control stages. Japanese manufacturing has fine-tuned this process to an art form, borrowing from their cultural emphasis on meticulous attention to detail and relentless pursuit of perfection.
The Significance of Visual Inspection in Japanese Manufacturing
From automotive components to high-precision electronics, Japanese producers often rely on visual inspection as one of the final checks before products reach the market. The goal is to ensure that each item meets stringent quality standards. A product may undergo several rounds of inspection, each with increasing levels of scrutiny, to identify even the most minuscule of defects.
Advantages of Visual Inspection
Engaging human senses in inspection offers several advantages. Skilled inspectors can identify anomalies that would otherwise escape automated systems, such as subtle changes in color, texture, or form.
1. **Cost-Effectiveness:** For small to medium-sized production runs, visual inspection can be more cost-efficient than installing complex automated systems. Skilled inspectors can quickly adapt to different product lines without the need for extensive reprogramming.
2. **High Sensitivity:** Human senses, particularly vision and touch, are incredibly adept at detecting imperfections. This makes visual inspection particularly useful for products where surface quality is paramount, such as in the automotive and consumer electronics industries.
3. **Flexibility:** Visual inspection can easily be integrated into various stages of the production process. Whether it’s the initial quality check or the final assurance phase, adding visual inspection points can significantly improve overall quality assurance.
Disadvantages of Visual Inspection
However, visual inspection is not without its drawbacks. Understanding these can help in making better decisions on quality control strategies.
1. **Subjectivity:** One of the main disadvantages is the inherent subjectivity. Results can vary between inspectors, leading to inconsistency in quality assessments.
2. **Fatigue:** Human inspectors are prone to fatigue, which can result in missed defects. This is particularly concerning in high-volume production environments.
3. **Skill Dependency:** The efficacy of visual inspection relies heavily on the skill and experience of the inspector. Training and retaining skilled inspectors can be a challenging and resource-intensive endeavor.
Techniques for Effective Visual Inspection
The key to mastering visual inspection lies in the techniques employed during the process. Japanese manufacturers have developed several expert strategies to maximize the effectiveness of visual inspection.
Advanced Training Programs
In Japan, the training of visual inspectors is an elaborate process. Potential inspectors undergo rigorous training that includes theoretical knowledge, practical exercises, and real-time assessments.
– **Theoretical Training:** Inspectors are first given a solid understanding of the types of defects they might encounter, the processes that could cause these defects, and the quality standards specific to the products.
– **Practical Exercises:** Trainees are then subjected to various simulated inspection scenarios, where they practice identifying defects under controlled conditions. This stage helps to fine-tune their detection skills.
– **Real-Time Assessments:** Finally, trainees are evaluated in real-world settings to ensure they can perform under actual production conditions. Feedback from experienced inspectors helps polish their skills.
Lighting and Ergonomics
Proper lighting and ergonomic setups are crucial in visual inspection. Japanese manufacturers often use diffused lighting to eliminate shadows and reflections, making it easier to identify surface defects. Ergonomics are also carefully considered to reduce inspector fatigue and improve efficiency.
Standardized Procedures
To mitigate the subjectivity inherent in visual inspection, Japanese companies implement standardized procedures. Standard Operating Procedures (SOPs) and visual aids guide inspectors on what to look for and how to evaluate defects. This ensures greater consistency and reliability in inspections.
Supplier Negotiation Techniques
Dealing with Japanese suppliers in the field of visual inspection parts or services requires a nuanced approach. Here are some effective negotiation techniques:
Building Long-Term Relationships
Japanese business culture highly values long-term relationships over transactional interactions. Invest time in building trust and demonstrating a commitment to mutual growth. This often leads to more favorable terms and better service quality.
Understanding Quality Expectations
Japanese suppliers have high expectations regarding quality. Clearly communicate your quality requirements and understand theirs. This alignment ensures that the visual inspections meet the desired standards for both parties.
Data-Driven Negotiations
Utilize data to your advantage. Performance metrics, defect rates, and historical quality data are valuable tools in negotiating better terms. Japanese suppliers appreciate data-backed arguments, as they resonate with their detail-oriented and analytical nature.
Cultural Sensitivity
Understanding and respecting cultural nuances can greatly enhance negotiation outcomes. Politeness, humility, and patience are valued traits in Japanese business dealings. Avoid aggressive tactics, as they can be counterproductive.
Emphasizing Mutual Benefits
In negotiations, emphasize mutual benefits rather than a win-lose outcome. Demonstrate how a partnership can lead to shared growth and success. This approach aligns with the collaborative spirit of Japanese business practices.
Current Market Conditions
The current market conditions play a significant role in shaping visual inspection strategies. Several factors influence the adoption and effectiveness of visual inspection methods in Japan:
Technological Advancements
The advent of advanced technologies, such as AI and machine learning, has impacted visual inspection. While traditional methods are still prevalent, there is a growing trend toward integrating automated systems to complement human inspectors. This hybrid approach offers the best of both worlds, combining human intuition with the precision of machines.
Skilled Labor Shortage
Japan faces a shortage of skilled labor, particularly in the manufacturing sector. This has led companies to invest more in training programs and consider automation to fill the gaps. The skills required for effective visual inspection have become highly sought after, leading to competitive salaries and better working conditions for inspectors.
Global Competition
Global competition is intensifying, driving Japanese manufacturers to adopt more stringent quality control measures to maintain their reputation. Visual inspection remains a key strategy in their quality assurance arsenal, helping to differentiate their products in the market.
Best Practices in Visual Inspection
Adopting best practices in visual inspection can significantly enhance its effectiveness. Here are some tried-and-true methods followed by top Japanese manufacturers:
Continuous Improvement (Kaizen)
The philosophy of Kaizen, or continuous improvement, is deeply ingrained in Japanese manufacturing culture. Regularly review and refine visual inspection processes to identify areas for improvement. Encourage feedback from inspectors and incorporate their insights to enhance overall quality.
Integrated Quality Control Systems
Integrate visual inspection with other quality control systems for a holistic approach. By combining visual inspection with techniques like statistical process control (SPC) and Six Sigma, manufacturers can achieve a higher level of quality assurance.
Cross-Functional Teams
Form cross-functional teams comprising members from different departments. This collaborative approach ensures that insights from various perspectives are considered in the visual inspection process. It also helps in identifying potential issues that may arise in different stages of production.
Regular Calibration and Maintenance
For those incorporating automated visual inspection systems, regular calibration and maintenance are crucial. Ensure that cameras, sensors, and other equipment are in optimal condition to maintain accuracy. Periodic checks and updates to software algorithms keep the system functioning effectively.
Employee Well-Being
Promote the well-being of inspectors to enhance their performance. Implement measures to reduce fatigue, such as ergonomic workstations, regular breaks, and conducive working environments. A well-rested and motivated inspector is more likely to perform thorough and accurate inspections.
Conclusion
Mastering visual inspection requires a blend of skilled human inspectors, advanced training, and the strategic use of technology. Japanese manufacturing companies have set the gold standard in this area, leveraging their cultural emphasis on quality and meticulous attention to detail. By adopting their expert techniques and best practices, manufacturers worldwide can vastly improve their visual inspection processes, ensuring superior product quality and customer satisfaction.
Visual inspection, when executed effectively, can be a powerful tool in maintaining the highest standards of quality control. The insights and techniques shared in this article provide a comprehensive roadmap for mastering visual inspection, drawing from the excellence exemplified by Japanese manufacturers.
資料ダウンロード
QCD調達購買管理クラウド「newji」は、調達購買部門で必要なQCD管理全てを備えた、現場特化型兼クラウド型の今世紀最高の購買管理システムとなります。
ユーザー登録
調達購買業務の効率化だけでなく、システムを導入することで、コスト削減や製品・資材のステータス可視化のほか、属人化していた購買情報の共有化による内部不正防止や統制にも役立ちます。
NEWJI DX
製造業に特化したデジタルトランスフォーメーション(DX)の実現を目指す請負開発型のコンサルティングサービスです。AI、iPaaS、および先端の技術を駆使して、製造プロセスの効率化、業務効率化、チームワーク強化、コスト削減、品質向上を実現します。このサービスは、製造業の課題を深く理解し、それに対する最適なデジタルソリューションを提供することで、企業が持続的な成長とイノベーションを達成できるようサポートします。
オンライン講座
製造業、主に購買・調達部門にお勤めの方々に向けた情報を配信しております。
新任の方やベテランの方、管理職を対象とした幅広いコンテンツをご用意しております。
お問い合わせ
コストダウンが利益に直結する術だと理解していても、なかなか前に進めることができない状況。そんな時は、newjiのコストダウン自動化機能で大きく利益貢献しよう!
(Β版非公開)