- お役立ち記事
- Unveiling the Role of Differentials in Japanese Manufacturing: From Engineering to Automotive Excellence
Unveiling the Role of Differentials in Japanese Manufacturing: From Engineering to Automotive Excellence
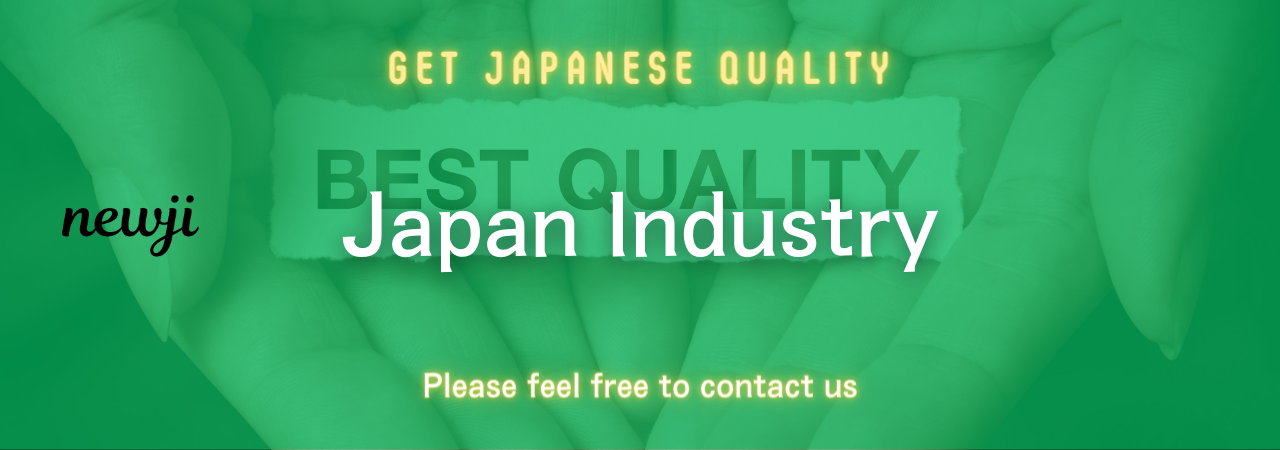
目次
Introduction
In the dynamic landscape of global manufacturing, Japan has consistently stood out as a pioneer in both technological innovations and quality control. This remarkable feat is partly due to the integral role that differentials play in Japanese manufacturing, particularly in the automotive sector. Differentials are crucial components that ensure the smooth transfer of torque and the seamless operation of vehicles. This article delves into the nuances of differentials in Japanese manufacturing, explores their applications, and highlights the best practices in procurement, purchasing, and supplier management from the Japanese market.
Understanding Differentials and Their Importance
What is a Differential?
A differential is a mechanical device that splits the engine torque two ways, allowing each output to spin at different speeds. In automotive applications, the differential distributes the torque to the wheels, which can turn at varying speeds while the vehicle is in motion. This function is essential when navigating curves, as the outer wheels need to travel a greater distance than the inner wheels.
Role in Automotive Excellence
The precision and reliability of differentials are paramount in the automotive industry, where performance, safety, and efficiency are critical parameters. Japanese manufacturers have mastered the art of engineering high-quality differentials that offer optimal performance. By focusing on meticulous design, cutting-edge technology, and exhaustive quality control, Japanese firms ensure their automotive components consistently meet and exceed global standards.
Advantages of Purchasing from Japanese Suppliers
Quality Control and Precision Engineering
Japanese suppliers are renowned for their stringent quality control measures and precise engineering capabilities. These attributes ensure that the differentials produced are of superior quality and reliability. Japanese firms often employ advanced manufacturing techniques, such as robotics and automation, to achieve unparalleled accuracy in production.
Stringent quality management systems, based on methodologies such as Six Sigma and Total Quality Management (TQM), are ingrained in the Japanese manufacturing ethos. This commitment to quality permeates every aspect of the production process, from material selection to final inspection.
Innovation and Technological Advancements
Japan has been at the forefront of technological advancements in the manufacturing sector. The country’s commitment to research and development has led to numerous innovations in differential design and functionality. For instance, Japan was one of the first countries to integrate electronically controlled differentials (e-diffs) in mainstream automotive production. These advancements offer improved vehicle handling and stability, enhancing overall driving experience.
Reliability and Longevity
The emphasis on quality and innovation ensures that Japanese-manufactured differentials are both reliable and durable. Longevity is a crucial factor in automotive components, and Japanese suppliers excel in producing parts that withstand the test of time and adverse conditions. This reliability translates into reduced maintenance costs and fewer replacements, offering long-term benefits to the buyer.
Challenges and Considerations
Cost Implications
One of the primary drawbacks of procuring from Japanese suppliers is the cost factor. Japanese components, given their high quality and precision, often come at a premium. Businesses must weigh the initial investment against the long-term benefits of reliability and reduced maintenance costs. While the upfront cost may be higher, the longevity and performance of Japanese differentials often result in lower total cost of ownership (TCO).
Lead Times and Logistics
Another challenge is the logistics and lead times involved in sourcing from Japan. The geographical distance and potential customs delays can impact the supply chain, making it essential to have robust logistics planning. Companies must factor in these considerations to ensure seamless operations and avoid disruptions.
Cultural and Communication Barriers
Dealing with Japanese suppliers may also entail navigating cultural and communication differences. Understanding the Japanese business etiquette and communication style is crucial for building strong supplier relationships. Language barriers and time zone differences can pose additional challenges, which must be mitigated through effective communication strategies and cultural awareness.
Best Practices for Procurement and Purchasing
Supplier Selection and Evaluation
When selecting Japanese suppliers, it is important to conduct a thorough evaluation based on several criteria. Quality, reliability, and technological capabilities should be at the forefront of the selection process. Conducting site visits and audits can provide deeper insights into the supplier’s operations and adherence to quality standards.
Negotiation Techniques
Negotiating with Japanese suppliers requires a strategic approach. It is essential to be well-prepared and demonstrate a clear understanding of the product and market conditions. Building a rapport and establishing trust are key elements in negotiation, as Japanese business culture values long-term relationships. Being transparent and honest in negotiations can foster mutual respect and lead to more favorable terms.
Risk Management
Risk management is a critical aspect of procurement. Diversifying the supplier base while maintaining strong relationships with key Japanese suppliers can help mitigate risks. It is also advisable to have contingency plans in place for potential disruptions in the supply chain. Regularly monitoring market conditions and staying abreast of geopolitical developments can aid in proactive risk management.
Case Studies of Japanese Excellence
Automotive Giants
Japanese automotive giants such as Toyota, Honda, and Nissan exemplify the excellence in differential manufacturing. Toyota, for instance, has pioneered the use of advanced materials and manufacturing processes in their differentials, resulting in highly efficient and reliable vehicles. Honda’s integration of cutting-edge e-diff technology has set new benchmarks in vehicle performance and safety.
Small and Medium Enterprises (SMEs)
In addition to large corporations, numerous Japanese SMEs have made significant contributions to the field. Companies like Musashi Seimitsu Industry Co., Ltd., and GKN Driveline have specialized in high-precision differential components, catering to both domestic and international markets. These SMEs exemplify the high standards of Japanese engineering and offer niche solutions tailored to specific customer needs.
The Future of Differentials in Japanese Manufacturing
Electrification and Autonomous Vehicles
As the automotive industry shifts towards electrification and autonomous driving, the role of differentials is evolving. Japanese manufacturers are at the forefront of developing innovative solutions to meet the requirements of electric and autonomous vehicles. Electronic differentials, advanced sensors, and integrated control systems are some of the areas where Japanese expertise is leading the way.
Sustainability and Environmental Considerations
Sustainability is becoming a key focus in manufacturing. Japanese firms are increasingly adopting environmentally friendly practices and materials in the production of differentials. This shift not only aligns with global sustainability goals but also enhances the market appeal of Japanese products.
Collaborative Innovation
Collaboration between academia, industry, and government is driving innovation in Japan. Joint research initiatives and partnerships are fostering the development of next-generation differential technologies. This collaborative approach ensures that Japan remains at the cutting edge of automotive engineering and continues to set global standards.
Conclusion
The role of differentials in Japanese manufacturing is a testament to the country’s engineering prowess and commitment to quality. From the automotive giants to specialized SMEs, Japanese firms have consistently delivered high-performance, reliable, and innovative differential solutions. While there are challenges and considerations in procuring from Japan, the advantages far outweigh the drawbacks.
Understanding the market dynamics, adopting best practices in procurement, and building strong supplier relationships can unlock the immense potential of sourcing from Japanese suppliers. As the industry evolves towards electrification and sustainability, Japanese expertise in differential manufacturing is poised to play a pivotal role in shaping the future of automotive excellence.
資料ダウンロード
QCD調達購買管理クラウド「newji」は、調達購買部門で必要なQCD管理全てを備えた、現場特化型兼クラウド型の今世紀最高の購買管理システムとなります。
ユーザー登録
調達購買業務の効率化だけでなく、システムを導入することで、コスト削減や製品・資材のステータス可視化のほか、属人化していた購買情報の共有化による内部不正防止や統制にも役立ちます。
NEWJI DX
製造業に特化したデジタルトランスフォーメーション(DX)の実現を目指す請負開発型のコンサルティングサービスです。AI、iPaaS、および先端の技術を駆使して、製造プロセスの効率化、業務効率化、チームワーク強化、コスト削減、品質向上を実現します。このサービスは、製造業の課題を深く理解し、それに対する最適なデジタルソリューションを提供することで、企業が持続的な成長とイノベーションを達成できるようサポートします。
オンライン講座
製造業、主に購買・調達部門にお勤めの方々に向けた情報を配信しております。
新任の方やベテランの方、管理職を対象とした幅広いコンテンツをご用意しております。
お問い合わせ
コストダウンが利益に直結する術だと理解していても、なかなか前に進めることができない状況。そんな時は、newjiのコストダウン自動化機能で大きく利益貢献しよう!
(Β版非公開)