- お役立ち記事
- Unlocking Efficiency in Japanese Manufacturing: The Role of Production Management Systems
Unlocking Efficiency in Japanese Manufacturing: The Role of Production Management Systems
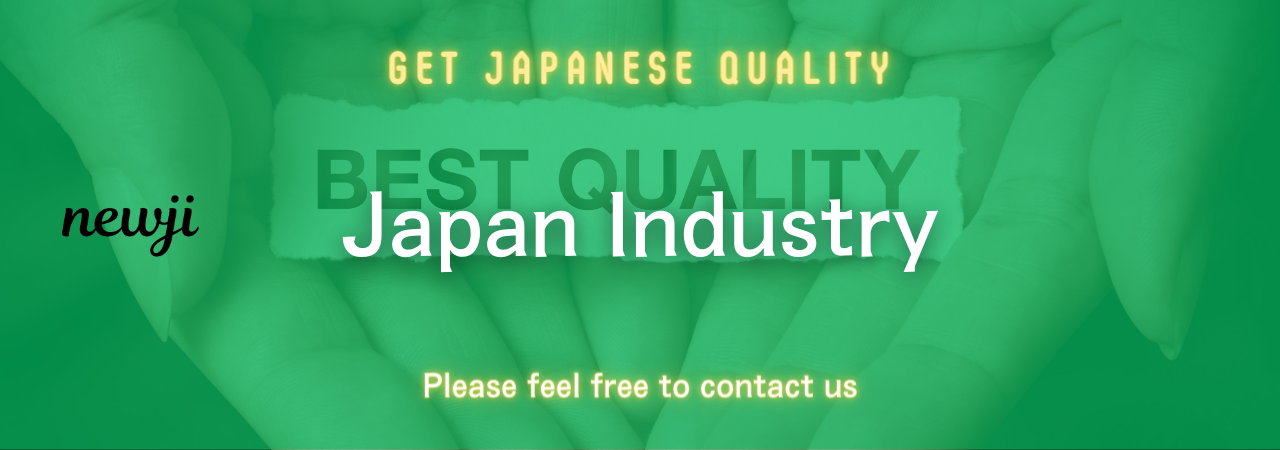
目次
Understanding Production Management Systems
Production Management Systems (PMS) are essential for enhancing efficiency in manufacturing environments. These systems encompass all processes involved in the production cycle, including planning, scheduling, resource allocation, and monitoring. Implementing a PMS means digitizing and automating these processes, thus enabling real-time data acquisition and analysis.
If you’re dealing with Japanese suppliers, understanding their approach to PMS can be highly beneficial. Japanese manufacturers are known for their meticulous planning, attention to detail, and exceptional quality standards. Leveraging their advanced PMS can offer multiple advantages such as reduced waste, improved workflow, and faster production times.
The Core Components of a Production Management System
Planning and Scheduling
The planning stage involves both long-term and short-term strategies. Long-term planning focuses on capacity planning, while short-term planning deals with production schedules. Efficient planning ensures that raw materials and components are available precisely when needed, reducing inventory costs and avoiding stockouts.
Japanese manufacturers often utilize Just-In-Time (JIT) production methods, which minimize inventory and ensure a seamless flow of materials. This practice improves efficiency and cuts down on waste, key principles of lean manufacturing.
Resource Allocation
Resource Allocation is crucial in maximizing the efficiency of the production process. This component involves assigning the right materials, labor, and machinery for the task. Japanese manufacturers excel in optimizing resource allocation, often using sophisticated algorithms and real-time data to make informed decisions.
Quality Control
Quality Control (QC) is a pivotal aspect of any PMS. QC ensures that products meet specified standards and comply with regulations. Japan’s reputation for high-quality manufacturing is partly due to robust QC systems, incorporating methods such as Kaizen (continuous improvement) and Six Sigma to identify and eliminate defects.
Monitoring and Reporting
Monitoring and reporting allow managers to track the production process in real-time. This real-time capability is essential for making quick adjustments to improve efficiency. Modern PMS often feature dashboards that provide visual representations of key performance indicators (KPIs). These tools enable managers to spot inefficiencies rapidly and take prompt corrective action.
Advantages of Using Production Management Systems
Enhanced Efficiency
One of the significant advantages of using a PMS is the enhanced efficiency it brings to the production process. Automation and real-time monitoring free up human resources for more complex tasks. This results in faster production times and the ability to fulfill orders more promptly.
Improved Quality
By implementing robust QC measures within a PMS, manufacturers can maintain high quality standards, significantly reducing the risk of defects. This leads to higher customer satisfaction and fewer returns.
Cost Reduction
Efficient resource allocation and reduced waste directly lead to cost savings. Moreover, advanced planning and JIT production methods can minimize holding costs and reduce overall operational expenditure.
Challenges and Solutions
Initial Investment Costs
One of the main drawbacks of implementing a PMS is the high initial investment cost. Both software and hardware can be expensive, and there is also a need for training staff to use the new system effectively. However, the long-term benefits often outweigh these early expenditures.
Complexity and Resistance to Change
Implementing a new PMS can be complex and met with resistance from staff accustomed to traditional methods. Overcoming this challenge requires a strategic change management plan that includes adequate training and a focus on the long-term benefits for both staff and the organization.
Best Practices for Implementing PMS
Collaborative Approach
A collaborative approach involving input from various departments is crucial for successful PMS implementation. This ensures that the system meets the needs of all stakeholders involved in the production cycle.
Custom Solutions
Different manufacturing processes have unique requirements. Therefore, customizing the PMS to cater specifically to your needs will yield better results. Custom solutions can address specific challenges and optimize your particular workflow, making the system more effective.
Continuous Improvement
Adopting a philosophy of continuous improvement, such as Kaizen, ensures that the PMS remains efficient and up-to-date. Regular reviews and feedback loops can help identify areas for improvement and adapt the system accordingly.
Supplier Negotiation Techniques
Negotiating with Japanese suppliers can be a unique experience. Understanding cultural nuances and building long-term relationships are vital in achieving favorable terms.
Cultural Sensitivity
Japanese business culture emphasizes respect, trust, and long-term relationships. Being culturally sensitive can significantly impact negotiation outcomes. Simple gestures, such as addressing your Japanese counterparts formally and understanding hierarchical structures, can make a significant difference.
Building Trust
Trust is a cornerstone of Japanese business relationships. Demonstrating reliability and integrity can go a long way in establishing a solid partnership. This involves being transparent about your business needs and consistently delivering on your promises.
Mutual Benefits
Negotiations with Japanese suppliers are often more successful when they focus on mutual benefits. Instead of hard bargaining, seek a win-win situation where both parties benefit. This approach aligns with the Japanese preference for harmony and long-term collaboration.
Market Conditions and Trends
Keeping an eye on market conditions and emerging trends can help you stay ahead in the field of procurement and purchasing.
Sustainability
Sustainability is increasingly becoming a significant consideration in manufacturing. Japanese suppliers are often leaders in this area, integrating environmentally friendly practices and materials into their processes. Partnering with these suppliers can enhance your company’s sustainability credentials and appeal to eco-conscious consumers.
Technology Integration
The integration of new technologies, such as IoT and AI, into PMS is revolutionizing manufacturing. Japanese manufacturers are at the forefront of this trend, developing and adopting cutting-edge technologies to improve efficiency and quality.
Global Supply Chains
Understanding global supply chain dynamics is essential for effective procurement. Japanese suppliers often have robust and resilient supply chains, enabling them to deliver consistently high-quality products, even in the face of global disruptions.
Conclusion
Unlocking efficiency in Japanese manufacturing through effective use of Production Management Systems offers numerous benefits, from enhanced efficiency and improved quality to cost reductions. By understanding the intricacies of Japanese business culture, employing best practices, and staying abreast of market trends, companies can fully leverage the capabilities of PMS for optimal results. In doing so, businesses not only enhance their own operations but also contribute to the preservation and advancement of the technical skills inherent in Japanese manufacturing.
資料ダウンロード
QCD調達購買管理クラウド「newji」は、調達購買部門で必要なQCD管理全てを備えた、現場特化型兼クラウド型の今世紀最高の購買管理システムとなります。
ユーザー登録
調達購買業務の効率化だけでなく、システムを導入することで、コスト削減や製品・資材のステータス可視化のほか、属人化していた購買情報の共有化による内部不正防止や統制にも役立ちます。
NEWJI DX
製造業に特化したデジタルトランスフォーメーション(DX)の実現を目指す請負開発型のコンサルティングサービスです。AI、iPaaS、および先端の技術を駆使して、製造プロセスの効率化、業務効率化、チームワーク強化、コスト削減、品質向上を実現します。このサービスは、製造業の課題を深く理解し、それに対する最適なデジタルソリューションを提供することで、企業が持続的な成長とイノベーションを達成できるようサポートします。
オンライン講座
製造業、主に購買・調達部門にお勤めの方々に向けた情報を配信しております。
新任の方やベテランの方、管理職を対象とした幅広いコンテンツをご用意しております。
お問い合わせ
コストダウンが利益に直結する術だと理解していても、なかなか前に進めることができない状況。そんな時は、newjiのコストダウン自動化機能で大きく利益貢献しよう!
(Β版非公開)