- お役立ち記事
- Importance of design purchasing information and appropriate management techniques in manufacturing
Importance of design purchasing information and appropriate management techniques in manufacturing
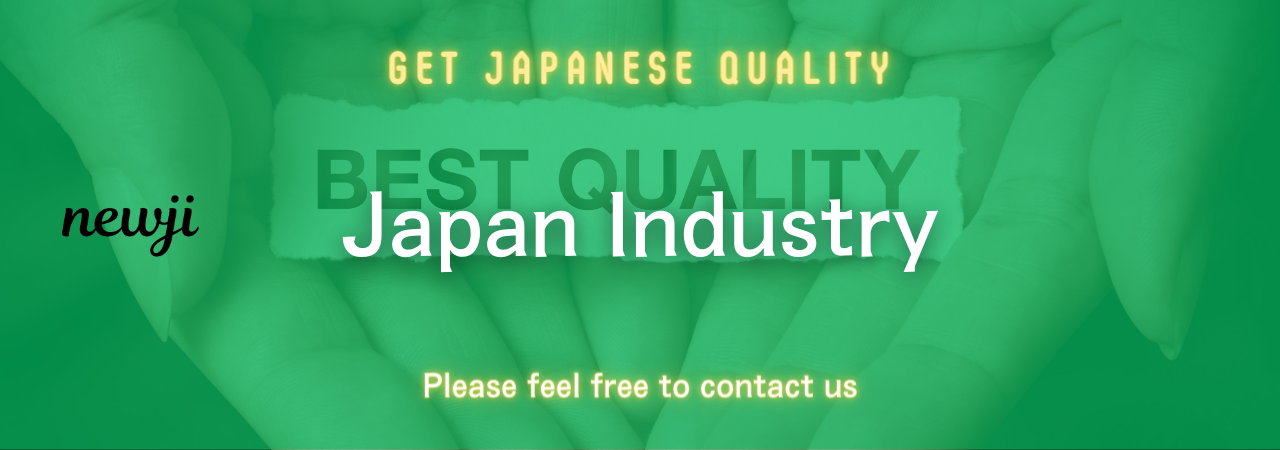
In the world of manufacturing, having the right design purchasing information and using the appropriate management techniques is incredibly important.
These practices can lead to smoother operations, higher-quality products, and better overall business performance.
Let’s dive into why this is so important and how you can ensure your company is managing this information effectively.
目次
Understanding Design Purchasing Information
Design purchasing information refers to all the details related to the procurement of materials and components based on specific design requirements.
This can include detailed specifications, drawings, material lists, and more.
Without precise and clear design purchasing information, it’s easy for mistakes to be made.
Parts might not fit together correctly, materials may be unsuitable for the end product, or production processes could be disrupted.
Key Elements of Design Purchasing Information
To ensure that the purchasing process goes smoothly, several critical elements should be included in the design purchasing information:
– **Detailed Specifications**: This includes the exact dimensions, tolerances, and material types.
– **Quality Standards**: Any quality certifications or standards that materials or components must meet.
– **Quantity Estimates**: Accurate estimates of the quantity of materials needed for production.
– **Supplier Information**: Details of preferred or approved suppliers.
The Role of Effective Management Techniques
Having the right information is only half the battle.
Effective management techniques are needed to handle and utilize that information efficiently.
Good management practices ensure that materials and components are purchased on time, within budget, and meet the required quality standards.
Inventory Management
Effective inventory management is crucial in manufacturing.
It ensures that materials are available when needed without overstocking, which can tie up capital and storage space.
Techniques such as Just-In-Time (JIT) inventory can help manufacturers reduce waste and improve efficiency.
Supplier Relationship Management
Building and maintaining strong relationships with suppliers is another key component.
Good communication ensures that suppliers understand your requirements and can deliver high-quality materials on time.
Regular performance reviews and open dialogue can help resolve issues quickly and improve the overall supply chain.
Quality Control Processes
Quality control is essential to ensure that purchased materials meet the necessary standards.
Implementing robust quality checks at various stages of the purchasing and production process can help catch issues early and prevent defective products from reaching customers.
Benefits of Proper Design Purchasing Information and Management
When these elements are correctly managed, several benefits can be realized:
Cost Efficiency
Properly managed purchasing information and techniques can lead to significant cost savings.
Accurate information and good inventory management reduce the risk of overbuying or buying unnecessary materials, saving money.
Improved Product Quality
Using the correct materials and components ensures that the end products meet quality standards and function correctly.
Strong quality control processes help maintain these standards consistently.
Reduced Production Delays
Having the right materials available when needed prevents production delays.
This allows for smoother operations and helps meet production deadlines.
Challenges and Solutions
While the importance of managing design purchasing information and techniques is clear, there can be challenges in implementing these practices.
Keeping Information Up-To-Date
In a fast-paced manufacturing environment, design and material requirements can change quickly.
It’s critical to have a system in place for keeping all purchasing information current.
Regular reviews and updates to your databases and purchasing records are essential.
Ensuring Communication Across Departments
Effective communication between design, purchasing, and production departments is vital.
Miscommunications can lead to errors and delays.
Implementing integrated software solutions or regular cross-department meetings can help keep everyone on the same page.
Training Employees
Employees need to be properly trained in both the importance of design purchasing information and the management techniques used.
Regular training sessions and clear documentation can help ensure that everyone understands their role and responsibilities.
Conclusion
In the manufacturing industry, the importance of design purchasing information and appropriate management techniques cannot be overstated.
From ensuring cost efficiency to maintaining high product quality, these practices are integral to smooth and successful operations.
By focusing on detailed and accurate purchasing information, effective management techniques, and overcoming potential challenges, manufacturers can achieve significant improvements in their processes and outcomes.
Implementing these practices requires effort and commitment, but the benefits to the business, customers, and overall product quality make it well worth it.
資料ダウンロード
QCD調達購買管理クラウド「newji」は、調達購買部門で必要なQCD管理全てを備えた、現場特化型兼クラウド型の今世紀最高の購買管理システムとなります。
ユーザー登録
調達購買業務の効率化だけでなく、システムを導入することで、コスト削減や製品・資材のステータス可視化のほか、属人化していた購買情報の共有化による内部不正防止や統制にも役立ちます。
NEWJI DX
製造業に特化したデジタルトランスフォーメーション(DX)の実現を目指す請負開発型のコンサルティングサービスです。AI、iPaaS、および先端の技術を駆使して、製造プロセスの効率化、業務効率化、チームワーク強化、コスト削減、品質向上を実現します。このサービスは、製造業の課題を深く理解し、それに対する最適なデジタルソリューションを提供することで、企業が持続的な成長とイノベーションを達成できるようサポートします。
オンライン講座
製造業、主に購買・調達部門にお勤めの方々に向けた情報を配信しております。
新任の方やベテランの方、管理職を対象とした幅広いコンテンツをご用意しております。
お問い合わせ
コストダウンが利益に直結する術だと理解していても、なかなか前に進めることができない状況。そんな時は、newjiのコストダウン自動化機能で大きく利益貢献しよう!
(Β版非公開)