- お役立ち記事
- Strategies and tools to help SMEs minimize purchasing management risks
Strategies and tools to help SMEs minimize purchasing management risks
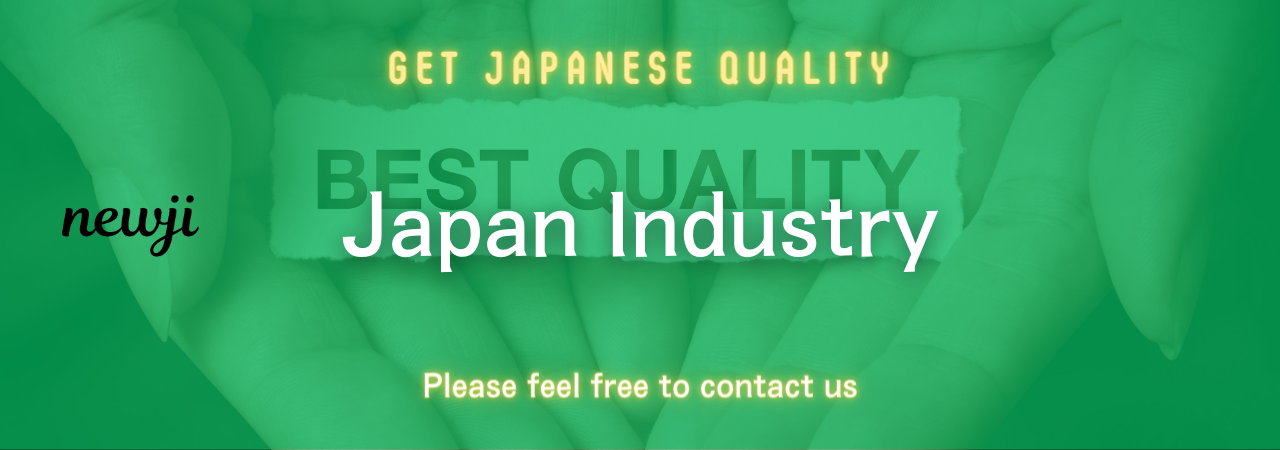
For small and medium-sized enterprises (SMEs), effective purchasing management is crucial to ensure smooth business operations.
However, it comes with its own set of risks, such as supplier reliability, inventory management, and cost control.
By using the right strategies and tools, SMEs can minimize these risks significantly.
In this article, we will explore effective strategies and essential tools to help SMEs manage purchasing risks.
目次
Understanding Purchasing Management Risks
Supplier Reliability
Supplier reliability is a significant factor in purchasing management.
SMEs depend heavily on their suppliers for timely delivery and quality products.
If a supplier fails to deliver on time, it disrupts the entire production line, leading to delays and financial losses.
Performing a thorough background check before engaging with new suppliers can help mitigate this risk.
Regular evaluations and establishing long-term relationships with reliable suppliers are also beneficial.
Inventory Management
Improper inventory management can result in either excess inventory or stockouts.
Excess inventory ties up capital and increases storage costs, while stockouts may cause sales losses and dissatisfaction amongst customers.
Implementing an efficient inventory management system ensures that inventory levels are optimized, minimizing these risks.
Cost Control
Fluctuations in material costs can negatively impact an SME’s profit margins.
Having a robust cost control mechanism in place helps in managing and predicting cost variations.
It is also essential to negotiate favorable terms with suppliers to keep costs in check.
Effective Strategies for Minimizing Purchasing Risks
Supplier Diversification
Relying on a single supplier for crucial materials or products is risky.
Diversifying supplier sources minimizes the risk if one supplier fails.
By having multiple suppliers, SMEs can maintain a steady supply chain and avoid disruptions.
Implementing Contractual Agreements
Clear and comprehensive contracts with suppliers reduce misunderstandings and disputes.
Contracts should outline quality standards, delivery timelines, and payment terms.
This ensures that both parties are mutually obliged to meet the agreed conditions, reducing potential risks.
Regular Supplier Evaluation
Regularly assessing supplier performance ensures they meet the established standards of quality and reliability.
Performance metrics like on-time delivery, quality consistency, and responsiveness to issues should be reviewed periodically.
This continuous monitoring helps predict and mitigate potential risks.
Adopting Lean Inventory Management
Lean inventory management techniques help in maintaining efficient inventory levels.
The Just-In-Time (JIT) method is particularly useful, where materials are ordered based on immediate production needs.
This minimizes excess inventory and reduces storage costs.
Negotiating Long-Term Agreements
Securing long-term agreements with suppliers can offer price stability and reliable supply.
Negotiating contracts that fix prices for a specified period helps in budgeting and financial planning.
It also encourages suppliers to maintain the agreed-upon quality and delivery standards.
Essential Tools for Effective Purchasing Management
Enterprise Resource Planning (ERP) Systems
ERP systems integrate various business processes and provide real-time data on inventory, suppliers, and costs.
Using an ERP system helps in efficient planning, minimizing risks associated with purchasing and inventory management.
Supplier Management Software
This software helps SMEs to keep detailed records of suppliers, including performance evaluations and contract terms.
It simplifies tracking supplier reliability and ensures timely communication, reducing risks of delays and quality issues.
Inventory Management Software
Inventory management software automates inventory tracking, ensuring optimal stock levels are maintained.
Such tools provide insights into inventory turnover ratios and help in forecasting demand accurately.
Spend Analysis Tools
These tools analyze spending patterns and help in identifying opportunities to cut costs.
They provide detailed reports on expenditures, helping SMEs make informed purchasing decisions and reducing unnecessary expenses.
Automated Procurement Systems
Automated procurement systems simplify the purchasing process, from requisition to payment.
They reduce manual errors, enhance transparency, and ensure compliance with procurement policies.
This helps in minimizing risks associated with purchasing.
Best Practices for Purchasing Management
Regular Training and Development
Providing regular training to the purchasing team helps them stay updated with industry standards and best practices.
Well-trained personnel are better equipped to identify and mitigate purchasing risks effectively.
Maintaining Strong Supplier Relationships
Building and maintaining strong relationships with suppliers fosters trust and reliability.
Regular communication and collaboration with suppliers help in resolving issues promptly and maintaining a steady supply chain.
Conducting Market Research
Regular market research provides insights into market trends and supplier capabilities.
Being informed about market conditions helps SMEs in making strategic purchasing decisions and mitigating risks.
Conclusion
Purchasing management is a critical function for SMEs, fraught with potential risks.
However, by implementing effective strategies such as supplier diversification, lean inventory management, and utilizing essential tools like ERP systems and supplier management software, these risks can be significantly minimized.
Understanding and regularly evaluating supplier reliability, cost control mechanisms, and inventory management practices are equally important.
Ultimately, a proactive approach to purchasing management ensures business continuity and competitiveness, empowering SMEs to thrive in a dynamic market.
資料ダウンロード
QCD調達購買管理クラウド「newji」は、調達購買部門で必要なQCD管理全てを備えた、現場特化型兼クラウド型の今世紀最高の購買管理システムとなります。
ユーザー登録
調達購買業務の効率化だけでなく、システムを導入することで、コスト削減や製品・資材のステータス可視化のほか、属人化していた購買情報の共有化による内部不正防止や統制にも役立ちます。
NEWJI DX
製造業に特化したデジタルトランスフォーメーション(DX)の実現を目指す請負開発型のコンサルティングサービスです。AI、iPaaS、および先端の技術を駆使して、製造プロセスの効率化、業務効率化、チームワーク強化、コスト削減、品質向上を実現します。このサービスは、製造業の課題を深く理解し、それに対する最適なデジタルソリューションを提供することで、企業が持続的な成長とイノベーションを達成できるようサポートします。
オンライン講座
製造業、主に購買・調達部門にお勤めの方々に向けた情報を配信しております。
新任の方やベテランの方、管理職を対象とした幅広いコンテンツをご用意しております。
お問い合わせ
コストダウンが利益に直結する術だと理解していても、なかなか前に進めることができない状況。そんな時は、newjiのコストダウン自動化機能で大きく利益貢献しよう!
(Β版非公開)