- お役立ち記事
- Optimizing System Design in Manufacturing with MBSE (Model-Based Systems Engineering)
Optimizing System Design in Manufacturing with MBSE (Model-Based Systems Engineering)
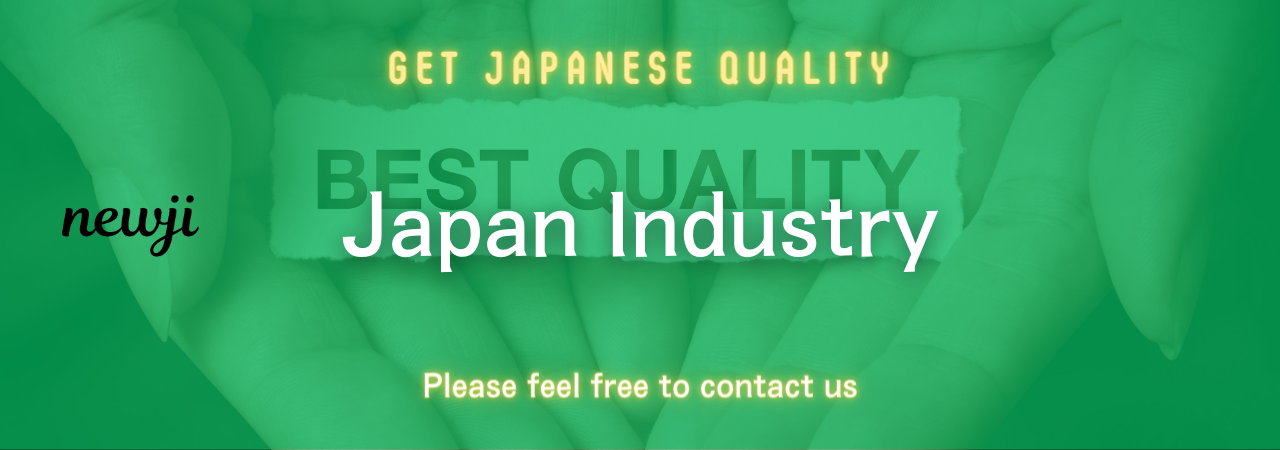
In today’s competitive business environment, companies strive to manufacture high-quality products efficiently and cost-effectively. One critical factor that can significantly impact a company’s ability to achieve these goals is system design.
Model-Based Systems Engineering (MBSE) offers a powerful approach to optimizing system design in manufacturing. It leverages models to support the entire lifecycle of a product, from initial concept through to production and operation.
目次
What is MBSE?
Model-Based Systems Engineering (MBSE) is a methodology that uses models to represent the systems being developed. Unlike traditional engineering methods that rely heavily on document-based processes, MBSE utilizes virtual models to capture, analyze, simulate, and communicate the various aspects of a system.
By creating detailed models, engineers can explore different designs, predict system interactions, and identify potential issues early in the development process. This precision helps to ensure that the end product will meet all required specifications and performance metrics.
Why MBSE Matters in Manufacturing
Manufacturing systems are incredibly complex, involving numerous components, processes, and stakeholders. Managing this complexity effectively is crucial for ensuring product quality, minimizing production costs, and reducing time-to-market.
MBSE provides a structured way to handle this complexity.
Improved Collaboration
Traditional document-based methods can sometimes lead to communication gaps and misunderstandings between different teams. MBSE, on the other hand, offers a shared, visual representation of the system, which makes it easier for engineers, designers, and other stakeholders to collaborate effectively.
Early Problem Detection
By using MBSE, engineers can simulate and analyze systems during the design phase. This allows them to identify and resolve any issues before production begins, reducing the risk of costly rework and delays.
Customization and Flexibility
Manufacturers often need to customize products to meet specific customer requirements. MBSE allows for easy modifications to the system model, enabling quick and efficient adaptations without disrupting the entire production process.
How to Implement MBSE in Manufacturing
Implementing MBSE in the manufacturing industry requires careful planning and execution. Here are some steps to guide you through the process:
1. Define Clear Objectives
Before you start, clearly define what you hope to achieve with MBSE. Your objectives might include improving product quality, reducing production costs, or shortening time-to-market. Having clear goals will help guide your implementation efforts.
2. Train Your Team
MBSE is a specialized methodology that requires specific skills and knowledge. Invest in training programs to ensure that your team is well-versed in MBSE principles and tools. This could involve workshops, online courses, or even hiring MBSE experts.
3. Choose the Right Tools
A variety of MBSE tools are available on the market, each with its own strengths and weaknesses. Select a tool that best meets your objectives and is compatible with your existing systems and processes.
4. Start with a Pilot Project
Rather than implementing MBSE across your entire organization all at once, start with a smaller pilot project. This will allow you to test the methodology and tools, make any necessary adjustments, and demonstrate the value of MBSE to stakeholders.
5. Integrate with Existing Processes
For MBSE to be effective, it needs to be integrated with your existing development processes. Work closely with your team to ensure that MBSE is seamlessly incorporated into your workflows, rather than being treated as an isolated activity.
Benefits of Using MBSE in Manufacturing
Employing MBSE in manufacturing offers several significant advantages:
Enhanced Efficiency
MBSE streamlines the system design process, leading to shorter development cycles and faster time-to-market. This efficiency is critical in a competitive manufacturing environment where speed can often be the key to success.
Higher Quality Products
With its precise modeling and simulation capabilities, MBSE helps ensure that products are of the highest possible quality. It allows for thorough testing and validation before production begins, reducing the likelihood of defects and failures.
Cost Savings
By identifying and addressing potential issues early on, MBSE helps avoid costly rework and production delays. This not only saves money but also ensures that resources are used more effectively.
Better Risk Management
MBSE provides a comprehensive view of the entire system, allowing for more effective risk assessment and management. Engineers can identify potential risks at an early stage and take preventative measures to mitigate them.
The Future of MBSE in Manufacturing
As manufacturing systems become more complex and the demand for customized products increases, the importance of MBSE will continue to grow. Advances in technology, such as automation and artificial intelligence, will further enhance the capabilities of MBSE, making it an even more powerful tool for optimizing system design.
Companies that adopt MBSE today will be well-positioned to take advantage of these developments and stay ahead in the competitive manufacturing landscape.
Conclusion
Model-Based Systems Engineering offers a transformative approach to optimizing system design in manufacturing. By using detailed models to capture, analyze, and simulate systems, MBSE improves collaboration, detects problems early, and allows for greater customization and flexibility.
Implementing MBSE requires careful planning, training, and integration with existing processes, but the benefits in terms of efficiency, product quality, cost savings, and risk management make it well worth the effort.
As manufacturing continues to evolve, MBSE will play an increasingly critical role in helping companies stay competitive and meet the changing demands of the market.
資料ダウンロード
QCD調達購買管理クラウド「newji」は、調達購買部門で必要なQCD管理全てを備えた、現場特化型兼クラウド型の今世紀最高の購買管理システムとなります。
ユーザー登録
調達購買業務の効率化だけでなく、システムを導入することで、コスト削減や製品・資材のステータス可視化のほか、属人化していた購買情報の共有化による内部不正防止や統制にも役立ちます。
NEWJI DX
製造業に特化したデジタルトランスフォーメーション(DX)の実現を目指す請負開発型のコンサルティングサービスです。AI、iPaaS、および先端の技術を駆使して、製造プロセスの効率化、業務効率化、チームワーク強化、コスト削減、品質向上を実現します。このサービスは、製造業の課題を深く理解し、それに対する最適なデジタルソリューションを提供することで、企業が持続的な成長とイノベーションを達成できるようサポートします。
オンライン講座
製造業、主に購買・調達部門にお勤めの方々に向けた情報を配信しております。
新任の方やベテランの方、管理職を対象とした幅広いコンテンツをご用意しております。
お問い合わせ
コストダウンが利益に直結する術だと理解していても、なかなか前に進めることができない状況。そんな時は、newjiのコストダウン自動化機能で大きく利益貢献しよう!
(Β版非公開)