- お役立ち記事
- Scale-Up Technology and Its Practical Application in Manufacturing
Scale-Up Technology and Its Practical Application in Manufacturing
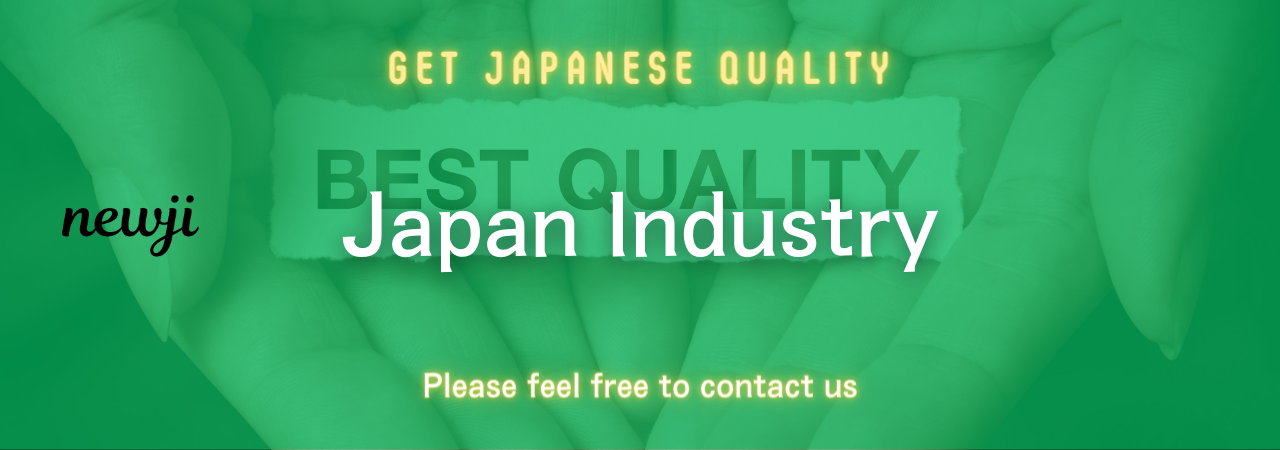
目次
Understanding Scale-Up Technology
Scale-up technology is a crucial process in manufacturing that allows smaller production models to be expanded to larger, industrial-size outputs. This means taking a small, laboratory-scale operation and turning it into a high-volume production system.
This technology is essential for companies aiming to meet high demand while maintaining product quality and efficiency.
The Importance of Scale-Up in Manufacturing
Scaling up isn’t just about making more of a product. It’s about ensuring that the larger-scale production retains the qualities and specifications of the original small-scale model.
This process ensures consistency, reduces costs, and enhances productivity for businesses that need to deliver large quantities of goods to their customers.
Failing to properly scale up can lead to issues such as inconsistent product quality, production delays, and increased operational costs.
Key Steps in the Scale-Up Process
Research and Development
The first step in the scale-up process involves thorough research and development (R&D). This phase focuses on understanding the product’s composition, behavior, and the potential challenges that may arise during large-scale production.
Scientists and engineers work together to test different variables and conditions to ensure the product can be replicated on a larger scale without losing its properties.
Feasibility Studies
After R&D, feasibility studies are conducted to assess the practical aspects of scaling up. This includes evaluating the economic, technical, and operational factors influencing the process.
Feasibility studies help determine whether the project is viable and identify potential risks and challenges. This step is crucial for minimizing potential setbacks during the scale-up phase.
Pilot-Scale Production
Before transitioning to full-scale production, businesses often implement a pilot-scale production phase. This involves producing a smaller but significant quantity of the product to simulate the conditions of large-scale manufacturing.
Pilot production helps identify any last-minute adjustments needed and ensures that the process will function correctly on a larger scale. It’s a vital step for detecting and resolving any unforeseen issues.
Optimization and Validation
Once pilot-scale production is successful, the next step is to optimize and validate the process. This involves fine-tuning the production parameters and ensuring that the system operates at peak efficiency.
Optimization helps reduce waste, improve product quality, and enhance the overall efficiency of the manufacturing process. Validation ensures that the scaled-up process consistently meets the desired standards and specifications.
Full-Scale Production
The final step is transitioning to full-scale production. At this stage, all the data and insights gathered during the previous steps are applied to produce large quantities of the product.
Full-scale production must be monitored closely to ensure that everything runs smoothly and any issues are promptly addressed.
Challenges in Scale-Up Technology
While the scale-up process is essential, it’s not without its challenges. One of the main challenges is maintaining product quality. Small variations in the process can lead to significant differences in the final product, so rigorous quality control measures must be in place.
Another challenge is managing costs. Scaling up can be expensive, and businesses must ensure that the process remains cost-effective. This requires careful planning and optimization of resources.
Additionally, the transition from small to large-scale production can create technical challenges. Equipment limitations, process control, and scalability issues need to be addressed to prevent disruptions in production.
The Role of Innovation in Scale-Up Technology
Innovation plays a vital role in overcoming the challenges of scale-up technology. Advances in automation, process control, and digitalization have significantly improved the efficiency and reliability of the scale-up process.
Automation
Automation technologies can streamline production processes, reduce human error, and improve consistency. Automated systems can handle large volumes of data, monitor production parameters, and make real-time adjustments to maintain quality and efficiency.
Process Control
Advanced process control systems enable precise control over production variables. This helps ensure that the scaled-up process operates within the desired parameters, reducing variability and enhancing product quality.
Digitalization
Digital technologies, such as data analytics and simulation models, allow businesses to predict and optimize the scale-up process. These tools provide valuable insights, enabling proactive decision-making and minimizing risks.
Practical Applications of Scale-Up Technology
Scale-up technology has practical applications across various industries. In pharmaceuticals, for instance, it allows the transition from laboratory synthesis of new drugs to mass production, ensuring that medications are available to meet public demand.
In the food and beverage industry, scale-up technology ensures that recipes developed in test kitchens can be replicated consistently in large production facilities. This maintains the flavors and quality that customers expect.
In the chemical industry, scale-up technology enables the bulk production of chemicals and materials, ensuring that they meet the required specifications for various applications.
Conclusion
Scale-up technology is a critical aspect of modern manufacturing. It ensures that businesses can meet high demand while maintaining product quality and efficiency.
By following a structured scale-up process, conducting thorough feasibility studies, and leveraging innovative technologies, companies can effectively transition from small-scale to large-scale production.
Despite the challenges, proper planning and optimization can lead to successful scale-up, providing significant benefits in terms of productivity, cost-effectiveness, and customer satisfaction.
資料ダウンロード
QCD調達購買管理クラウド「newji」は、調達購買部門で必要なQCD管理全てを備えた、現場特化型兼クラウド型の今世紀最高の購買管理システムとなります。
ユーザー登録
調達購買業務の効率化だけでなく、システムを導入することで、コスト削減や製品・資材のステータス可視化のほか、属人化していた購買情報の共有化による内部不正防止や統制にも役立ちます。
NEWJI DX
製造業に特化したデジタルトランスフォーメーション(DX)の実現を目指す請負開発型のコンサルティングサービスです。AI、iPaaS、および先端の技術を駆使して、製造プロセスの効率化、業務効率化、チームワーク強化、コスト削減、品質向上を実現します。このサービスは、製造業の課題を深く理解し、それに対する最適なデジタルソリューションを提供することで、企業が持続的な成長とイノベーションを達成できるようサポートします。
オンライン講座
製造業、主に購買・調達部門にお勤めの方々に向けた情報を配信しております。
新任の方やベテランの方、管理職を対象とした幅広いコンテンツをご用意しております。
お問い合わせ
コストダウンが利益に直結する術だと理解していても、なかなか前に進めることができない状況。そんな時は、newjiのコストダウン自動化機能で大きく利益貢献しよう!
(Β版非公開)