- お役立ち記事
- Cycle Time Reduction Methods and Efficiency in Manufacturing
Cycle Time Reduction Methods and Efficiency in Manufacturing
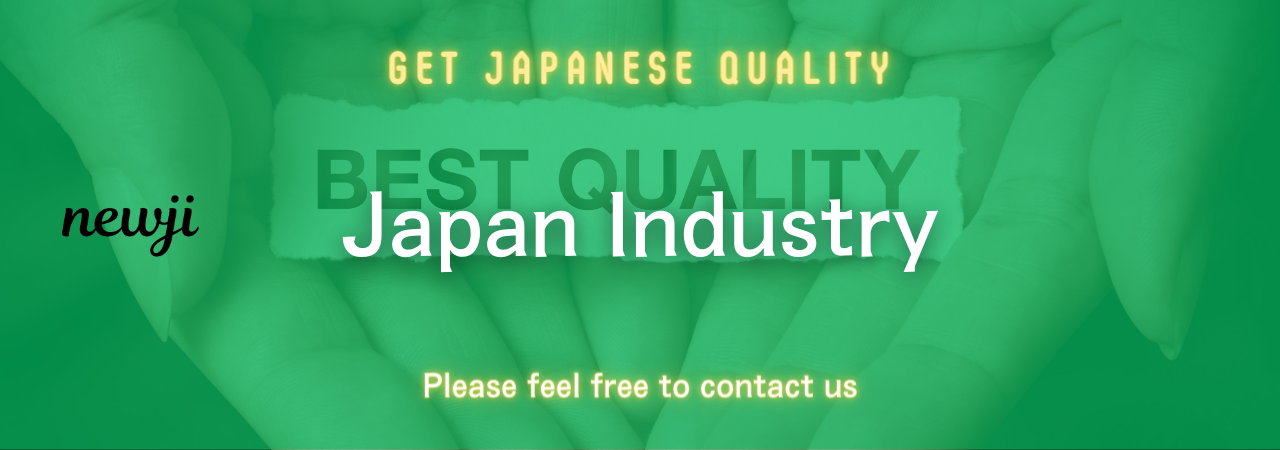
In the world of manufacturing, efficiency is key. One of the primary goals for any manufacturing process is to reduce cycle time without compromising on quality. But what exactly is cycle time, and how can you reduce it? Let’s dive into the topic, explore various methods, and understand how to boost efficiency.
目次
What Is Cycle Time?
Cycle time is the total time taken to complete one full cycle of a manufacturing process, from start to finish. This includes all steps required to produce a finished product. It is a critical metric because it directly impacts production capacity and overall efficiency.
Why Reducing Cycle Time Matters
Reducing cycle time has numerous benefits. The most obvious advantage is an increase in production speed, which can lead to higher output and reduced costs. Faster production lines can also respond more quickly to changes in market demand, helping businesses stay competitive. Furthermore, reducing cycle time often uncovers inefficiencies and areas for improvement within the production process.
Methods to Reduce Cycle Time
There are several methods and strategies you can employ to reduce cycle time in manufacturing. Let’s explore some of the most effective ones.
Lean Manufacturing
Lean manufacturing focuses on minimizing waste while maximizing productivity. It involves identifying and eliminating non-value-added activities. By streamlining processes and getting rid of unnecessary steps, you can significantly reduce cycle time.
Automation
Automating certain aspects of your manufacturing process can lead to substantial time savings. Machines can often perform repetitive tasks much faster and with greater accuracy than human workers. Investing in modern machinery and robotics can help you achieve a more efficient production line.
Process Standardization
Standardizing your production processes ensures that each operation is performed consistently. This minimizes variability and reduces the likelihood of errors or delays. Creating detailed standard operating procedures (SOPs) can help maintain consistent performance and reduce cycle time.
Quality Control
Implementing thorough quality control measures can prevent defects and rework. By catching errors early in the production process, you can avoid costly delays. Continuous monitoring and quality checks contribute to smoother operations and reduced cycle time.
Training and Employee Empowerment
Skilled and knowledgeable workers can perform tasks more efficiently. Providing ongoing training and encouraging employees to suggest improvements can lead to faster and more efficient production processes. Empowering employees to take ownership of their work can result in valuable insights and innovative solutions for reducing cycle time.
Technology and Data Analysis
Utilizing advanced technologies and data analytics can provide insights into your production processes. By analyzing data, you can identify bottlenecks, inefficiencies, and areas for improvement. Implementing technology solutions like Manufacturing Execution Systems (MES) can help optimize workflows and reduce cycle time.
Implementing Cycle Time Reduction Strategies
While knowing the methods is a great start, implementing these strategies requires a systematic approach. Here are some steps to follow.
Assess Your Current Processes
Before you make changes, you need to understand your current cycle time and the factors contributing to it. Conduct a thorough assessment of your production processes, identify bottlenecks, and gather data on current cycle times.
Set Clear Goals
Establish specific and measurable goals for cycle time reduction. For example, you might aim to reduce cycle time by 20% within six months. Clear goals provide direction and a benchmark for measuring progress.
Develop an Action Plan
Create a detailed action plan that outlines the steps you’ll take to achieve your goals. Prioritize initiatives based on their potential impact and feasibility. Assign responsibilities and set timelines to ensure accountability.
Implement Changes Gradually
Implementing too many changes at once can lead to confusion and disruptions. Start with one or two high-impact initiatives and monitor their effects. Gradually introduce additional changes based on the results and feedback.
Measure and Adjust
Regularly monitor your progress and measure the impact of implemented changes on cycle time. Use data to assess the effectiveness of your strategies and make adjustments as needed. Continuous improvement is key to long-term success.
Benefits of Reduced Cycle Time
Successfully reducing cycle time in your manufacturing processes comes with several significant benefits.
Increased Production Capacity
Shorter cycle times mean you can produce more units in the same amount of time. This increase in production capacity can lead to higher revenue and market share.
Cost Savings
Efficient production processes reduce the time and resources required to produce each unit. Lower operational costs can result in significant savings for your business.
Improved Quality
Many cycle time reduction strategies, such as quality control and process standardization, also enhance product quality. Higher quality products can lead to greater customer satisfaction and reduced returns or rework.
Enhanced Competitiveness
Companies that can produce efficiently have a competitive edge. Faster production times enable quicker responses to market demand and changing customer needs. Staying competitive in the market is crucial for long-term success.
Employee Satisfaction
Streamlined processes and reduced cycle times can lead to a more organized and less stressful work environment. Employees may feel more valued and empowered, resulting in higher job satisfaction and productivity.
Conclusion
Reducing cycle time in manufacturing is a critical goal for businesses aiming to enhance efficiency and competitiveness. By implementing strategies such as lean manufacturing, automation, process standardization, and continuous improvement, you can achieve significant cycle time reductions.
Remember to set clear goals, develop an action plan, and continuously monitor progress. The benefits of reduced cycle time extend beyond increased production capacity to include cost savings, improved quality, and enhanced employee satisfaction.
Start with a thorough assessment of your current processes, and take gradual steps to implement changes. The journey towards reduced cycle time requires effort and commitment, but the rewards are well worth it.
資料ダウンロード
QCD調達購買管理クラウド「newji」は、調達購買部門で必要なQCD管理全てを備えた、現場特化型兼クラウド型の今世紀最高の購買管理システムとなります。
ユーザー登録
調達購買業務の効率化だけでなく、システムを導入することで、コスト削減や製品・資材のステータス可視化のほか、属人化していた購買情報の共有化による内部不正防止や統制にも役立ちます。
NEWJI DX
製造業に特化したデジタルトランスフォーメーション(DX)の実現を目指す請負開発型のコンサルティングサービスです。AI、iPaaS、および先端の技術を駆使して、製造プロセスの効率化、業務効率化、チームワーク強化、コスト削減、品質向上を実現します。このサービスは、製造業の課題を深く理解し、それに対する最適なデジタルソリューションを提供することで、企業が持続的な成長とイノベーションを達成できるようサポートします。
オンライン講座
製造業、主に購買・調達部門にお勤めの方々に向けた情報を配信しております。
新任の方やベテランの方、管理職を対象とした幅広いコンテンツをご用意しております。
お問い合わせ
コストダウンが利益に直結する術だと理解していても、なかなか前に進めることができない状況。そんな時は、newjiのコストダウン自動化機能で大きく利益貢献しよう!
(Β版非公開)