- お役立ち記事
- Application and Effectiveness of Quality Function Deployment (QFD) in Quality Control in Manufacturing
Application and Effectiveness of Quality Function Deployment (QFD) in Quality Control in Manufacturing
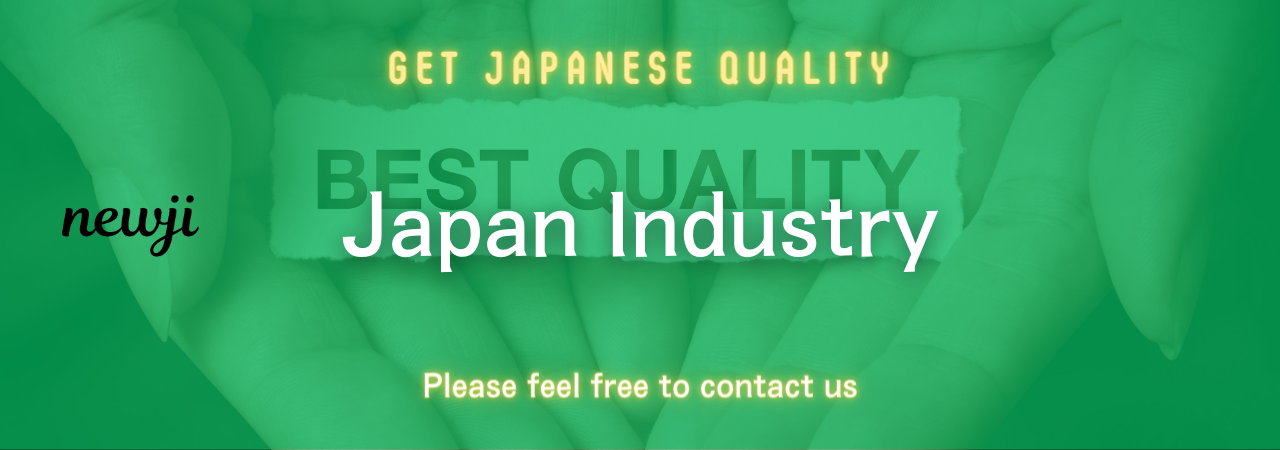
Quality Function Deployment (QFD) plays an essential role in quality control within the manufacturing sector. It’s a systematic approach that ensures customer requirements are met throughout the product development process. By prioritizing customer needs and translating those needs into specific technical requirements, QFD enhances product quality and customer satisfaction. This article delves into the application and effectiveness of QFD within manufacturing, highlighting its benefits and implementation strategies.
目次
Understanding Quality Function Deployment (QFD)
Quality Function Deployment is a method that transforms customer needs into engineering characteristics, ensuring the end product meets customer expectations. It involves creating detailed charts that map customer requirements to specific technical attributes. This visual representation aids manufacturers in understanding the voice of the customer and aligning their processes to deliver high-quality products.
The Purpose of QFD
The primary goal of QFD is to maximize customer satisfaction by ensuring that their needs are comprehensively understood and addressed during product development. By prioritizing customer values, manufacturers can reduce the risk of product failures and improve overall quality.
Application of QFD in Manufacturing
The application of QFD in manufacturing involves several key steps. These steps help in systematically incorporating customer requirements into the product design and production process.
1. Identifying Customer Needs
The initial phase of QFD involves gathering detailed information about customer needs and preferences. This can be achieved through surveys, interviews, focus groups, and market research. Understanding what customers want is crucial for developing products that meet or exceed their expectations.
2. Creating the House of Quality
The House of Quality is a fundamental element of QFD. It’s a matrix that helps translate customer requirements into technical specifications. Here’s how it works:
– List customer needs on the left side of the matrix.
– List corresponding technical requirements along the top.
– Rate the correlation between customer needs and technical requirements.
– Identify areas where improvements can be made to enhance product quality.
3. Prioritizing Requirements
Not all customer needs carry the same weight. Some are more critical to customer satisfaction than others. Through QFD, manufacturers can prioritize these needs and focus their resources on the most important attributes. This ensures that essential features are addressed rigorously during product development.
4. Translating Requirements to Production
Once the critical customer needs are identified and prioritized, the next step is to translate these requirements into specific actions within the production process. This involves:
– Developing technical specifications that meet customer needs.
– Designing production processes that align with these specifications.
– Implementing quality control measures to ensure consistent adherence to technical requirements.
5. Continuous Feedback and Improvement
QFD is not a one-time activity. It involves continuous feedback and improvement. Manufacturers should constantly gather customer feedback and incorporate it into their processes. This ongoing cycle of feedback and improvement helps maintain product quality and customer satisfaction over time.
Effectiveness of QFD in Quality Control
The effectiveness of QFD in quality control can be measured by various factors, including customer satisfaction, product reliability, and overall production efficiency. Let’s explore how QFD enhances each of these aspects.
Customer Satisfaction
By focusing on customer needs from the outset, QFD ensures that the end product aligns with what customers truly want. This alignment leads to higher customer satisfaction, as products are designed with the user’s expectations in mind. Meeting or exceeding customer expectations translates into increased customer loyalty and positive word-of-mouth.
Product Reliability
QFD emphasizes a thorough understanding of customer requirements and translates these into specific, measurable technical specifications. This detailed approach reduces the likelihood of errors and defects in the final product. As a result, products developed using QFD are generally more reliable and meet higher quality standards.
Production Efficiency
By clearly defining technical requirements early in the process, QFD helps streamline production. It reduces the trial-and-error phase typically associated with product development. This leads to more efficient production processes and minimizes wastage, saving time and resources. Consequently, manufacturers can bring high-quality products to market faster and more cost-effectively.
Benefits of Implementing QFD in Manufacturing
There are numerous benefits associated with implementing QFD in manufacturing. These benefits highlight why many companies adopt this approach to quality control.
Enhanced Communication and Collaboration
QFD fosters better communication and collaboration across different departments within a manufacturing organization. By involving various stakeholders—such as marketing, design, engineering, and production—QFD ensures that everyone is on the same page regarding customer needs and technical requirements.
Reduced Time to Market
With QFD, manufacturers can streamline their product development processes. By reducing the trial-and-error phase and focusing on precise technical specifications, QFD enhances production efficiency, ultimately reducing the time required to bring a new product to market.
Improved Product Quality
The structured approach of QFD ensures that customer needs are systematically taken into account throughout the product development process. This focus on quality from the very beginning results in products that meet higher standards and are more likely to satisfy customer expectations.
Cost Savings
Implementing QFD can lead to significant cost savings. By reducing the risk of product failures and minimizing defects, QFD helps avoid costly rework and recalls. Additionally, streamlined production processes further contribute to reduced manufacturing costs.
Conclusion
Incorporating Quality Function Deployment (QFD) into quality control processes within manufacturing is a proven strategy for enhancing product quality and customer satisfaction. By systematically translating customer needs into technical specifications, prioritizing requirements, and aligning production processes, manufacturers can develop high-quality products that meet or exceed customer expectations. The benefits of QFD—improved communication, faster time to market, enhanced product quality, and cost savings—make it an invaluable tool for any manufacturing organization committed to excellence. Embracing QFD is a proactive step towards achieving superior quality control and maintaining a competitive edge in the market.
資料ダウンロード
QCD調達購買管理クラウド「newji」は、調達購買部門で必要なQCD管理全てを備えた、現場特化型兼クラウド型の今世紀最高の購買管理システムとなります。
ユーザー登録
調達購買業務の効率化だけでなく、システムを導入することで、コスト削減や製品・資材のステータス可視化のほか、属人化していた購買情報の共有化による内部不正防止や統制にも役立ちます。
NEWJI DX
製造業に特化したデジタルトランスフォーメーション(DX)の実現を目指す請負開発型のコンサルティングサービスです。AI、iPaaS、および先端の技術を駆使して、製造プロセスの効率化、業務効率化、チームワーク強化、コスト削減、品質向上を実現します。このサービスは、製造業の課題を深く理解し、それに対する最適なデジタルソリューションを提供することで、企業が持続的な成長とイノベーションを達成できるようサポートします。
オンライン講座
製造業、主に購買・調達部門にお勤めの方々に向けた情報を配信しております。
新任の方やベテランの方、管理職を対象とした幅広いコンテンツをご用意しております。
お問い合わせ
コストダウンが利益に直結する術だと理解していても、なかなか前に進めることができない状況。そんな時は、newjiのコストダウン自動化機能で大きく利益貢献しよう!
(Β版非公開)