- お役立ち記事
- How Japan’s Mastery of the Flywheel Revolutionizes Modern Manufacturing
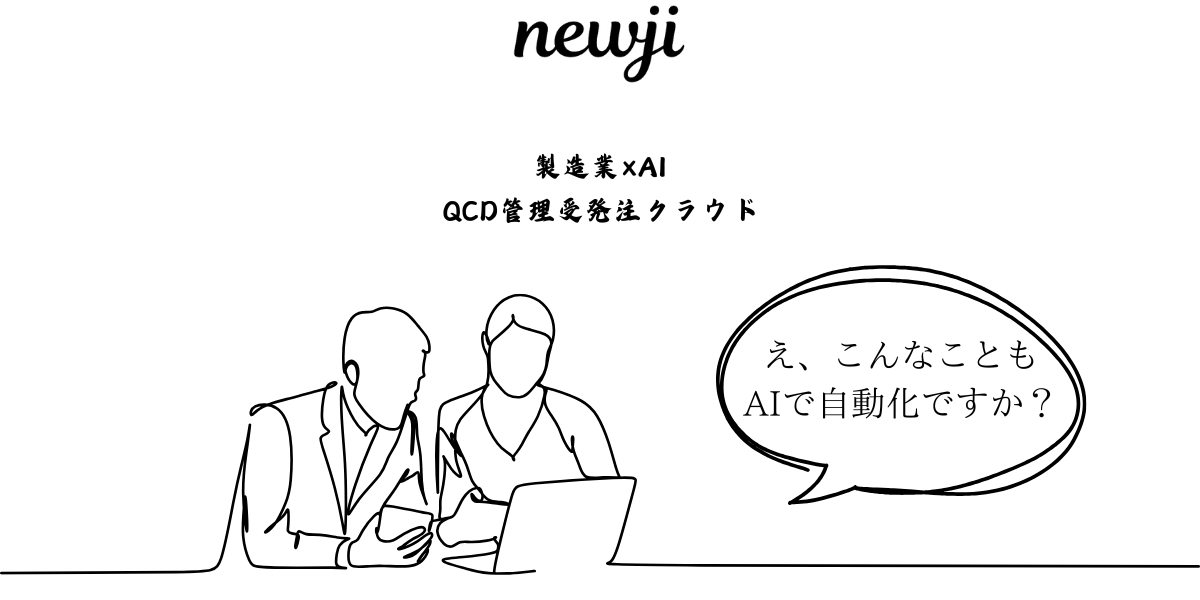
How Japan’s Mastery of the Flywheel Revolutionizes Modern Manufacturing
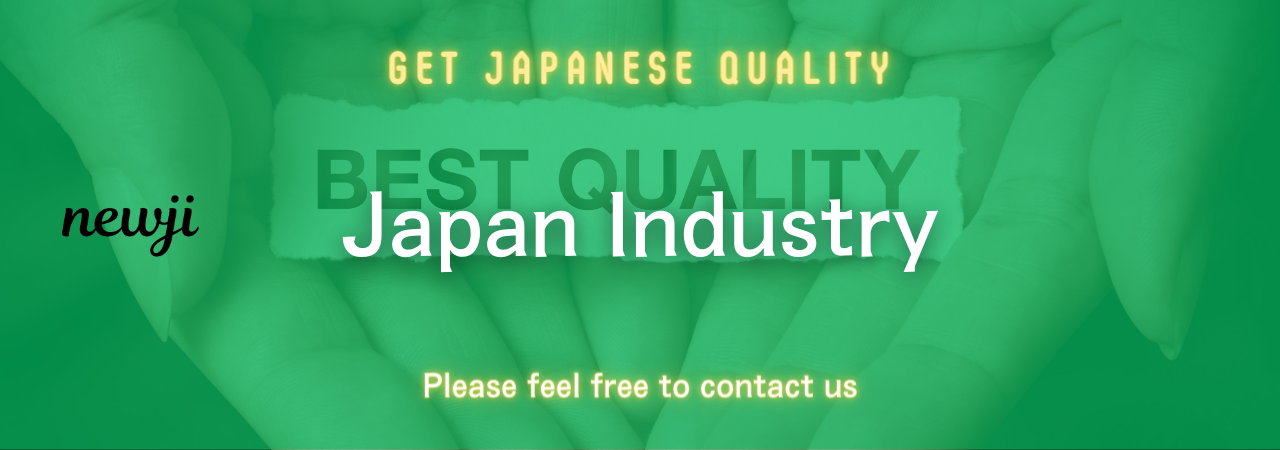
目次
Introduction
Japan has long been a global leader in high-precision manufacturing and technological innovation.
Among the pivotal elements that have contributed to Japan’s manufacturing prowess is its mastery of the flywheel.
The flywheel, when integrated into manufacturing systems, offers significant improvements in efficiency, energy savings, and overall operational effectiveness.
In this article, we will explore how Japan’s expertise in flywheel technology revolutionizes modern manufacturing.
We’ll delve into the practical applications of flywheels, discuss their advantages and disadvantages, and examine key strategies for successful supplier negotiations in the Japanese market.
Historical Context of Flywheel Technology in Japan
Japanese manufacturing has a tradition of incorporating incremental improvements for maximum efficiency, known as “Kaizen.”
The flywheel principle, which stores mechanical energy to smooth out energy supply and improve system stability, aligns perfectly with this approach.
Flywheels have been utilized in various applications ranging from transportation to industrial machinery, but their integration into manufacturing systems has been particularly transformative in Japan.
From the Toyota Production System (TPS) to advanced robotic assemblies, flywheels are integral to many cutting-edge processes.
Understanding Flywheel Technology
Basic Principles of Flywheels
At its core, a flywheel is a mechanical device designed to store kinetic energy.
When energy input is applied, the flywheel spins and stores that energy as rotational kinetic energy.
The stored energy can be released when needed to provide a steady and reliable power supply.
Types of Flywheels
1. **Conventional Flywheels:** These are made of steel or cast iron and are typically heavier, designed for systems requiring large amounts of stored energy over short durations.
2. **Advanced Composite Flywheels:** These are constructed from materials like carbon fiber and glass-reinforced plastic, allowing for higher rotational speeds and improved energy density.
3. **Magnetic Bearing Flywheels:** Utilizing magnetic bearings, these flywheels eliminate frictional losses, increasing their overall efficiency.
Advantages of Flywheel Integration in Manufacturing
Energy Efficiency
Flywheels assist in smoothing out fluctuations in power supply, ensuring that manufacturing processes receive consistent energy.
This is particularly advantageous in industries where precision and consistency are crucial.
Reduced Operational Costs
By storing energy during periods of low demand and releasing it during peak usage, flywheels can help reduce energy consumption and operational costs.
This is especially valuable in energy-intensive manufacturing environments.
Improved Reliability and Stability
The energy stored in flywheels can be used as a backup during power outages or system failures, thus ensuring the continuity of operations.
This reliability is crucial in environments where downtime can be costly.
Reduction in Carbon Footprint
Flywheels contribute to greener manufacturing by enabling more efficient energy use and reducing dependence on fossil fuels.
This aligns with global sustainability goals and enhances a company’s environmental standing.
Challenges and Disadvantages of Flywheel Technology
High Initial Investment
The cost of installing advanced flywheel systems can be prohibitive, particularly for small to mid-sized enterprises.
The return on investment (ROI) may not be immediately apparent, making it a challenging decision for some manufacturers.
Maintenance and Safety Concerns
Despite their efficiency, flywheels require regular maintenance to ensure optimal performance.
Additionally, the high rotational speeds of advanced composite flywheels can pose safety risks if not properly managed.
Space Requirements
Flywheels, especially conventional ones, require substantial space for installation.
This can be a limiting factor for facilities with constrained physical footprints.
System Integration Complexity
Integrating flywheel technology into existing manufacturing systems can be complex and may require significant modifications to current infrastructure.
This complexity can deter some companies from adopting the technology.
Best Practices for Implementing Flywheel Technology
Thorough Cost-Benefit Analysis
Before implementing flywheel technology, conduct a detailed cost-benefit analysis.
Consider both the initial capital and long-term savings.
Engage financial experts to develop a clear ROI timeline.
Selecting the Right Type of Flywheel
Different manufacturing processes may benefit from different types of flywheels.
Evaluate your specific needs to choose the appropriate type.
For instance, magnetic bearing flywheels might be ideal for high-speed operations, whereas conventional flywheels may suffice for simpler applications.
Partnering with Experienced Suppliers
Work with suppliers who have a proven track record in flywheel technology.
Japanese suppliers, given their expertise, can offer valuable insights and innovations to ensure successful integration into your systems.
Robust Maintenance Protocols
Develop and implement robust maintenance protocols to ensure the long-term reliability and safety of flywheel systems.
Regular inspections and preventive maintenance can mitigate potential risks.
Training and Development
Invest in training for your staff to handle and maintain flywheel systems efficiently.
Proper training can enhance operational efficiency and ensure safer handling of the technology.
Negotiating with Japanese Suppliers
Cultural Considerations
Understanding Japanese business culture is critical.
Emphasis on respect, patience, and building long-term relationships is paramount.
Punctuality and showing genuine interest in their technology can go a long way in negotiations.
Thorough Preparation
Japanese suppliers value thorough preparation and data-driven discussions.
Ensure you have detailed information and clear objectives before entering negotiations.
Focusing on Quality and Innovation
Japanese suppliers pride themselves on high-quality products and cutting-edge technology.
Highlight your commitment to quality and a willingness to invest in innovative solutions during negotiations.
Building Trust
Trust is a cornerstone of Japanese business practices.
Taking the time to build a strong, trust-based relationship can lead to more favorable terms and long-term partnerships.
Leveraging Local Expertise
Engage local consultants or business advisors who understand both Western and Japanese business practices.
They can help bridge cultural gaps and improve negotiation outcomes.
Market Conditions and Future Trends
Growing Demand for Energy Efficiency
With a global push towards sustainability, the demand for energy-efficient solutions like flywheels is expected to rise.
Manufacturers that adopt these technologies early will have a competitive edge.
Advancements in Material Science
Ongoing research in material science is likely to yield even more advanced flywheel technologies with enhanced energy density and safety profiles.
Staying informed about these advancements can help you make informed procurement decisions.
Integration with Smart Manufacturing
The rise of Industry 4.0 and smart manufacturing technologies presents new opportunities for integrating flywheels with other advanced systems.
IoT-enabled flywheels, for example, can offer real-time monitoring and predictive maintenance capabilities.
Government Policies and Incentives
Be aware of government policies and incentives promoting energy-efficient technologies.
In some regions, adopting flywheel technology may qualify you for tax breaks or subsidies, enhancing ROI.
Conclusion
Japan’s mastery of flywheel technology is a testament to its commitment to innovation and efficiency in manufacturing.
By understanding the principles, advantages, challenges, and best practices of this technology, manufacturers worldwide can harness its benefits to revolutionize their operations.
Negotiating effectively with Japanese suppliers, staying informed about market conditions, and adopting forward-thinking strategies will be key to leveraging flywheel technology for a sustainable and efficient future in manufacturing.
資料ダウンロード
QCD調達購買管理クラウド「newji」は、調達購買部門で必要なQCD管理全てを備えた、現場特化型兼クラウド型の今世紀最高の購買管理システムとなります。
ユーザー登録
調達購買業務の効率化だけでなく、システムを導入することで、コスト削減や製品・資材のステータス可視化のほか、属人化していた購買情報の共有化による内部不正防止や統制にも役立ちます。
NEWJI DX
製造業に特化したデジタルトランスフォーメーション(DX)の実現を目指す請負開発型のコンサルティングサービスです。AI、iPaaS、および先端の技術を駆使して、製造プロセスの効率化、業務効率化、チームワーク強化、コスト削減、品質向上を実現します。このサービスは、製造業の課題を深く理解し、それに対する最適なデジタルソリューションを提供することで、企業が持続的な成長とイノベーションを達成できるようサポートします。
オンライン講座
製造業、主に購買・調達部門にお勤めの方々に向けた情報を配信しております。
新任の方やベテランの方、管理職を対象とした幅広いコンテンツをご用意しております。
お問い合わせ
コストダウンが利益に直結する術だと理解していても、なかなか前に進めることができない状況。そんな時は、newjiのコストダウン自動化機能で大きく利益貢献しよう!
(Β版非公開)