- お役立ち記事
- Preparation of Defective Measures Instructions and Response Procedures in Manufacturing
Preparation of Defective Measures Instructions and Response Procedures in Manufacturing
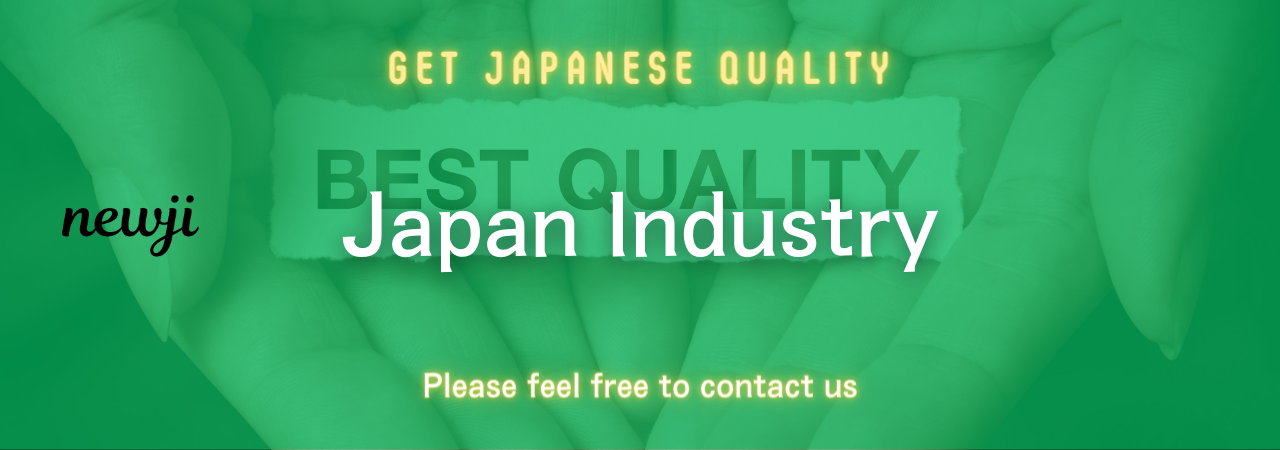
In the dynamic environment of manufacturing, ensuring consistent quality is crucial.
Defects can occur at various stages of production, and addressing them swiftly and effectively can save valuable time and resources.
Having well-prepared instructions and response procedures for handling defects is essential to maintaining the integrity of the manufacturing process.
目次
Understanding the Importance of Defective Measures
Defective products can have a significant impact on the credibility and financial health of a company.
They can lead to costly recalls, damage to brand reputation, and loss of customer trust.
Therefore, it is imperative to have a clear strategy in place to identify, address, and prevent defects.
Minimizing Errors through Detailed Instructions
Detailed instructions are the first line of defense against defects.
Instructions must be comprehensive and easy to understand, ensuring that every worker in the production line is on the same page.
Conducting a Thorough Risk Assessment
Before creating defect response procedures, conduct a thorough risk assessment.
Identify potential points in the production process where defects are likely to occur.
Analyzing past incidents can provide invaluable insights into common issues that need to be addressed.
Developing Response Procedures
When a defect is identified, having a streamlined response procedure is crucial.
Effective response procedures involve a clear chain of actions that need to be taken to mitigate the defect and prevent recurrence.
Immediate Isolation of Defective Products
The first step in any response procedure should be to isolate the defective product immediately.
This prevents the defective product from proceeding further down the production line or reaching customers.
Root Cause Analysis
Conduct a root cause analysis to determine why the defect occurred.
Identifying the underlying cause is critical to preventing similar defects in the future.
Implementing Corrective Actions
Once the root cause is identified, formulate and implement corrective actions.
These actions should address both immediate and long-term solutions to prevent recurrence.
Training and Communication
Effective communication and training are key components in preventing defects and ensuring proper response when they occur.
Regular Training Sessions
Conduct regular training sessions for all employees involved in the production process.
These sessions should cover defect identification, reporting procedures, and response actions.
Open Lines of Communication
Maintain open lines of communication between all levels of the organization.
Encourage workers to report any observed defects or potential issues without fear of retribution.
Utilizing Technology
Technology plays a vital role in modern manufacturing and can significantly aid in defect management.
Automated Quality Control Systems
Implement automated quality control systems that can detect defects in real-time.
These systems can inspect products at various stages of production, ensuring any defects are identified and addressed promptly.
Data Analysis
Use data analysis tools to monitor and analyze production metrics.
Data-driven insights can help in identifying trends and patterns that may indicate potential defects.
Continuous Improvement
The approach to handling defects should be dynamic and continuously evolving.
Always strive for continuous improvement in response procedures and quality control measures.
Regular Audits and Reviews
Conduct regular audits and reviews of the entire production process.
Evaluate the effectiveness of defect response procedures and make necessary adjustments.
Incorporating Feedback
Incorporate feedback from employees at all levels.
Workers on the production line often have valuable insights into potential issues and practical solutions.
Conclusion
Preparing defective measures instructions and response procedures is not a one-time task.
It requires continuous effort, constant vigilance, and a commitment to quality.
By implementing detailed instructions, conducting thorough risk assessments, and fostering open communication, manufacturing entities can effectively minimize and manage defects.
Leveraging technology and fostering a culture of continuous improvement can further enhance the robustness of defect response strategies.
Ultimately, a proactive approach to defect management ensures the production of high-quality products, bolstering customer trust and confidence.
資料ダウンロード
QCD調達購買管理クラウド「newji」は、調達購買部門で必要なQCD管理全てを備えた、現場特化型兼クラウド型の今世紀最高の購買管理システムとなります。
ユーザー登録
調達購買業務の効率化だけでなく、システムを導入することで、コスト削減や製品・資材のステータス可視化のほか、属人化していた購買情報の共有化による内部不正防止や統制にも役立ちます。
NEWJI DX
製造業に特化したデジタルトランスフォーメーション(DX)の実現を目指す請負開発型のコンサルティングサービスです。AI、iPaaS、および先端の技術を駆使して、製造プロセスの効率化、業務効率化、チームワーク強化、コスト削減、品質向上を実現します。このサービスは、製造業の課題を深く理解し、それに対する最適なデジタルソリューションを提供することで、企業が持続的な成長とイノベーションを達成できるようサポートします。
オンライン講座
製造業、主に購買・調達部門にお勤めの方々に向けた情報を配信しております。
新任の方やベテランの方、管理職を対象とした幅広いコンテンツをご用意しております。
お問い合わせ
コストダウンが利益に直結する術だと理解していても、なかなか前に進めることができない状況。そんな時は、newjiのコストダウン自動化機能で大きく利益貢献しよう!
(Β版非公開)