- お役立ち記事
- Importance and Implementation of Supplier Audits in Manufacturing
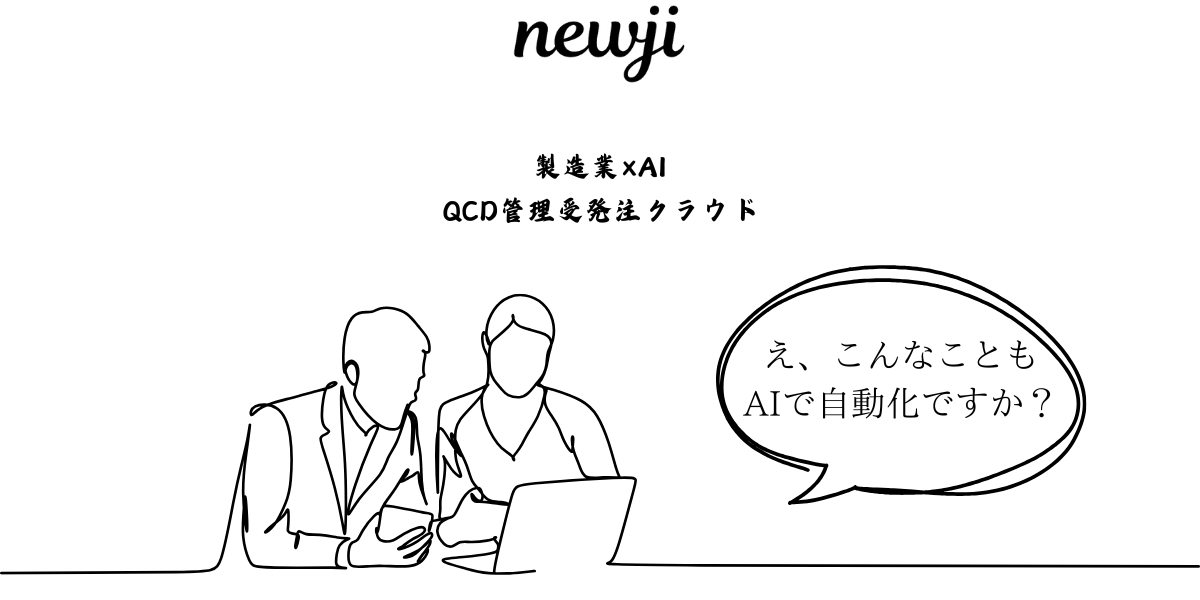
Importance and Implementation of Supplier Audits in Manufacturing
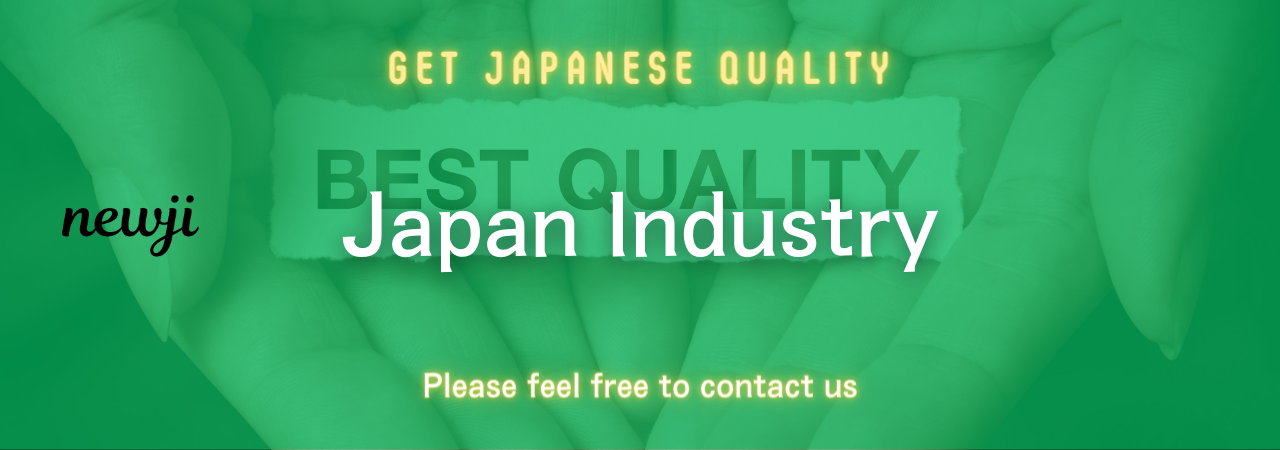
In the world of manufacturing, maintaining high-quality standards is crucial for success.
One effective way to ensure these standards are met is through supplier audits.
In this article, we will explore the importance of supplier audits in manufacturing, the steps to implement them, and best practices for making the process efficient and effective.
目次
What Are Supplier Audits?
A supplier audit is a thorough evaluation of a supplier’s processes, systems, and capabilities.
The goal is to ensure that these suppliers meet the necessary quality standards and comply with regulatory requirements.
This process can help manufacturers identify potential risks, inefficiencies, and opportunities for improvement within their supply chain.
Why Are Supplier Audits Important?
Supplier audits hold great significance in the manufacturing industry for several reasons.
First, they help maintain product quality.
When suppliers adhere to high standards, the likelihood of producing defects decreases.
This, in turn, results in fewer recalls and customer complaints.
Another reason is cost reduction.
Identifying issues early in the supply chain can prevent expensive problems later.
For instance, detecting a process flaw that might cause batch failures can save substantial amounts on rework and scrap costs.
Moreover, compliance with industry standards and regulations is imperative.
Supplier audits ensure that suppliers comply with these rules, reducing the risk of legal consequences and protecting the company’s reputation.
Supplier audits also foster better relationships within the supply chain.
When suppliers understand that the manufacturer values quality and accountability, they are more likely to strive for continual improvement.
This mutual respect can lead to more collaborative and productive partnerships.
Steps to Implement Supplier Audits
Implementing supplier audits requires a structured approach to ensure thoroughness and effectiveness.
Below, we outline the key steps to take.
Step 1: Set Clear Objectives
Before initiating a supplier audit, it is critical to define what you aim to achieve.
Setting clear objectives guides the entire audit process and helps maintain focus on the ultimate goals.
Common objectives might include evaluating the supplier’s quality management system, assessing compliance with industry standards, and identifying areas for process improvement.
Step 2: Develop an Audit Plan
The next step is to create a detailed audit plan.
This plan should outline the scope of the audit, key areas to be evaluated, and the criteria for assessment.
It is also essential to schedule the audit, allowing sufficient time for each evaluation phase without disrupting the supplier’s operations.
Step 3: Select the Audit Team
Selecting the right audit team is crucial for a successful supplier audit.
The team should consist of individuals with relevant expertise and experience.
Team members should possess a deep understanding of the supplier’s operations and the standards they need to meet.
Additionally, ensure to include individuals with proficiency in quality management and regulatory compliance.
Step 4: Conduct the Audit
With the plan in place and the team ready, it is time to conduct the audit.
This process involves several stages, including document review, process observation, and interviews with key personnel.
During the audit, take detailed notes and gather evidence to support your findings.
Step 5: Report Findings
Once the audit is complete, the next step is to compile a comprehensive report of the findings.
This report should be clear, concise, and well-structured, highlighting both strengths and areas needing improvement.
It is also important to provide actionable recommendations for each identified issue to facilitate improvement.
Step 6: Follow-Up
The audit process does not end with the report.
Follow-up actions are necessary to ensure that the supplier takes corrective measures.
Schedule follow-up audits to verify that the recommended improvements have been implemented and are effective.
Best Practices for Supplier Audits
To optimize the supplier audit process, consider the following best practices.
Maintain Effective Communication
Open and transparent communication is vital throughout the audit process.
Ensure that the supplier is aware of the audit’s purpose, scope, and schedule well in advance.
During the audit, maintain a collaborative approach and keep the supplier informed of any findings and next steps.
Use a Risk-Based Approach
Not all suppliers carry the same level of risk.
A risk-based approach focuses resources on critical suppliers whose performance has a significant impact on the final product.
Prioritize audits for suppliers with higher risk levels to maximize the audit’s effectiveness.
Leverage Technology
Modern technologies can significantly enhance the audit process.
Utilize digital tools and software to streamline data collection, analytics, and reporting.
Technology can facilitate real-time tracking of audit progress and ensure consistency in the evaluation process.
Train Audit Teams Regularly
Continuous training is essential to ensure that audit teams remain updated on the latest standards, regulations, and best practices.
Regular training sessions enhance the team’s skills and knowledge, making them more effective in conducting thorough and accurate audits.
Engage in Continuous Improvement
Supplier audits should be part of a continuous improvement strategy.
Encourage suppliers to engage in regular self-assessments and provide feedback from the audit process.
This collaborative effort promotes a culture of quality and continuous improvement across the supply chain.
Conclusion
Supplier audits are pivotal in ensuring high-quality standards in manufacturing.
They help maintain product quality, reduce costs, ensure compliance, and strengthen supplier relationships.
By setting clear objectives, developing a robust audit plan, selecting a skilled audit team, and following best practices, manufacturers can implement effective supplier audits.
This structured approach not only improves the overall quality of products but also fosters a culture of continuous improvement and accountability within the supply chain.
資料ダウンロード
QCD調達購買管理クラウド「newji」は、調達購買部門で必要なQCD管理全てを備えた、現場特化型兼クラウド型の今世紀最高の購買管理システムとなります。
ユーザー登録
調達購買業務の効率化だけでなく、システムを導入することで、コスト削減や製品・資材のステータス可視化のほか、属人化していた購買情報の共有化による内部不正防止や統制にも役立ちます。
NEWJI DX
製造業に特化したデジタルトランスフォーメーション(DX)の実現を目指す請負開発型のコンサルティングサービスです。AI、iPaaS、および先端の技術を駆使して、製造プロセスの効率化、業務効率化、チームワーク強化、コスト削減、品質向上を実現します。このサービスは、製造業の課題を深く理解し、それに対する最適なデジタルソリューションを提供することで、企業が持続的な成長とイノベーションを達成できるようサポートします。
オンライン講座
製造業、主に購買・調達部門にお勤めの方々に向けた情報を配信しております。
新任の方やベテランの方、管理職を対象とした幅広いコンテンツをご用意しております。
お問い合わせ
コストダウンが利益に直結する術だと理解していても、なかなか前に進めることができない状況。そんな時は、newjiのコストダウン自動化機能で大きく利益貢献しよう!
(Β版非公開)