- お役立ち記事
- Revolutionizing Japanese Manufacturing: The Future of 3D Printing Technology
Revolutionizing Japanese Manufacturing: The Future of 3D Printing Technology
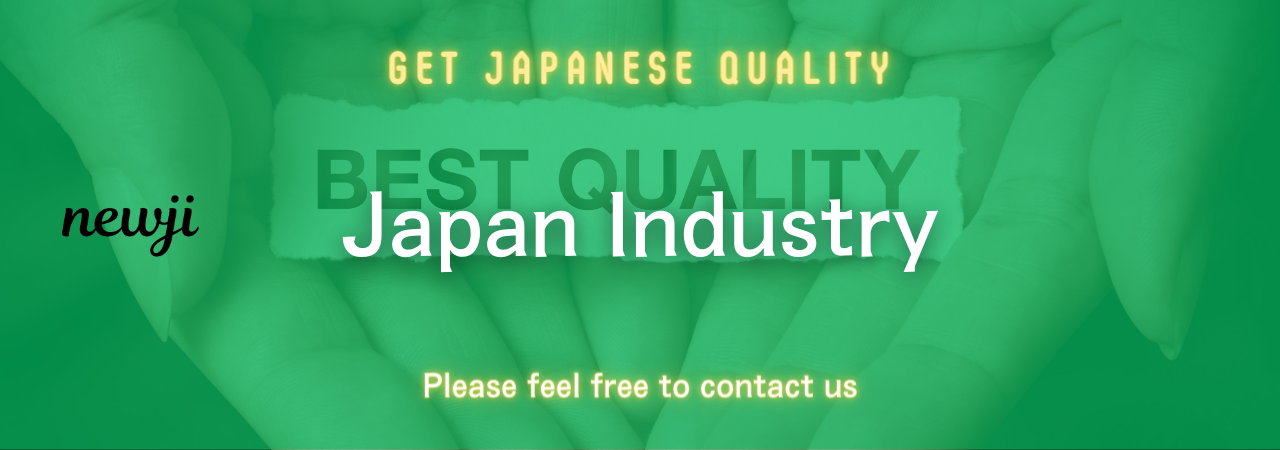
目次
Introduction to 3D Printing Technology in Japanese Manufacturing
3D printing, also known as additive manufacturing, has rapidly evolved over the last few decades and has become an integral part of the manufacturing landscape. With its potential to revolutionize the production processes and supply chains, it comes as no surprise that Japanese manufacturing companies, known for their high-precision and quality-driven methodologies, are adopting this technology.
In this article, we will delve into how 3D printing is being utilized in Japanese manufacturing, its advantages and disadvantages, negotiation techniques with suppliers, market conditions, and best practices for successful implementation.
The Evolution of 3D Printing Technology
3D printing started as a prototyping tool but has significantly evolved into a full-fledged manufacturing process.
Technological advancements in material science, software, and hardware have expanded its applications from simple models to complex parts used in various industries such as automotive, aerospace, and healthcare.
Early Adoption and Integration in Japan
Japan has always been at the forefront of technological innovations.
The country’s initial foray into 3D printing was primarily for rapid prototyping to cut down the time and cost associated with traditional mold-making processes.
Japanese firms like Denso and Toyota quickly saw the benefits of integrating 3D printing for the production of functional prototypes and now increasingly for end-use parts.
Applications of 3D Printing in Japanese Manufacturing
3D printing technology offers an array of applications within various manufacturing sectors in Japan. Below are some notable uses:
Prototyping and Rapid Development
Japanese manufacturers have leveraged 3D printing to reduce the lead-time required for prototyping.
This process allows engineers to quickly iterate designs, identifying flaws and improvements without the long waits associated with conventional methods.
Tooling and Manufacturing Aids
The creation of custom tooling and manufacturing aids is another critical application.
3D printed jigs, fixtures, and specialized tools can streamline assembly and production processes, enhancing overall efficiency and reducing labor costs.
End-Use Components
While traditional manufacturing methods like injection molding and CNC machining are still predominant, 3D printing is gaining traction for small batch production and highly complex parts.
Industries such as aerospace and medical devices are examples where the ability to produce lightweight, customized, and intricate components is particularly advantageous.
Spare Parts and On-Demand Manufacturing
The ability to produce spare parts on-demand addresses logistical challenges and reduces inventory costs.
This is especially important for industries like railways and aerospace, where downtime due to part unavailability can be extremely costly.
Advantages of Adopting 3D Printing in Japan
There are several benefits that Japanese manufacturers can reap from incorporating 3D printing into their processes:
Customization and Flexibility
3D printing allows for the production of custom parts tailored to specific needs, offering a level of flexibility that is unmatched by traditional methods. This is particularly useful for the medical field where custom prosthetics and implants are often required.
Reduced Lead Times
Traditional manufacturing methods can be time-consuming, particularly when it comes to mold creation and setup.
3D printing bypasses these steps, drastically reducing lead times and accelerating the development cycle.
Cost Efficiency
For small production runs and complex designs, 3D printing can be more cost-effective than traditional methods.
The reduced need for tooling and the ability to produce parts on-demand are significant cost savers.
Challenges and Disadvantages
Despite its numerous advantages, 3D printing also comes with its set of challenges and limitations that need to be addressed:
Material Limitations
While the range of 3D printable materials has expanded, it is still limited compared to traditional manufacturing materials.
Achieving the required mechanical properties, surface finish, and durability can be challenging for some applications.
Production Speed
For large-scale production, 3D printing can still be slower compared to traditional manufacturing methods like injection molding and machining.
This makes it less suitable for high-volume production runs.
Post-Processing Requirements
Many 3D printed parts require extensive post-processing, such as sanding, polishing, or additional machining, to meet functional and aesthetic requirements.
This adds extra time and cost to the overall production process.
Negotiation Techniques with Japanese Suppliers
Successful collaboration with Japanese suppliers requires an understanding of cultural nuances and negotiation techniques:
Building Trust and Relationships
Trust is a cornerstone of Japanese business culture.
Building long-term relationships based on mutual respect and trust can lead to more favorable terms and successful collaborations.
Emphasizing Quality and Precision
Japanese suppliers are known for their commitment to quality.
Emphasizing your own company’s dedication to maintaining high-quality standards can pave the way for successful negotiations.
Clear and Detailed Communication
Providing clear, detailed specifications and requirements is essential.
Japanese suppliers appreciate precision and clarity, which helps in avoiding misunderstandings and ensuring successful outcomes.
Understanding Hierarchical Structures
Japanese companies often have hierarchical organizational structures.
Understanding and respecting these hierarchies during negotiations can lead to more effective communication and collaboration.
Current Market Conditions
The landscape of 3D printing in Japan is influenced by various market factors:
Technological Advancements
The continuous development of 3D printing technology, including advancements in materials and speed, is driving its adoption in various sectors.
Japan, with its strong focus on research and development, is poised to be at the forefront of these innovations.
Government Support and Initiatives
The Japanese government has been supportive of 3D printing through various initiatives and grants aimed at boosting technological advancement and manufacturing capabilities.
Such support provides companies with the resources to invest in and adopt 3D printing technology.
Growing Demand for Customization
Consumer demand for personalized and customized products is on the rise.
This trend is driving the adoption of 3D printing, which offers the ability to create tailor-made solutions efficiently.
Best Practices for Implementing 3D Printing
To successfully incorporate 3D printing into their processes, Japanese manufacturers can follow these best practices:
Assessing the Needs and Goals
Understand the specific needs and goals of your production process.
Identify where 3D printing can add the most value, whether it’s in prototyping, tooling, or end-use parts.
Investing in Training and Skill Development
Invest in training and skill development for your workforce to fully harness the potential of 3D printing technology.
This includes understanding the operation, maintenance, and optimization of 3D printers.
Collaborating with Experts
Collaborate with experts and consultants who have extensive experience in 3D printing.
This can help in overcoming initial challenges and accelerating the adoption process.
Focusing on Quality Control
Implement stringent quality control measures to ensure that 3D printed parts meet the desired standards.
Regularly monitor and evaluate the production process to maintain consistency and quality.
Exploring Material Options
Continuously explore new materials that can be used in 3D printing.
Conduct testing and validation to determine their suitability for your specific applications.
Conclusion: The Future of 3D Printing in Japan
As Japan continues to lead in manufacturing innovation, the integration of 3D printing technology holds immense promise.
From reducing lead times and costs to enabling customization and complex designs, 3D printing is set to revolutionize Japanese manufacturing.
By understanding its advantages and challenges, leveraging the right negotiation techniques, staying updated with market conditions, and following best practices, Japanese companies can fully harness the potential of 3D printing to stay competitive and drive future growth.
The future of 3D printing in Japan looks bright, with endless possibilities to enhance production efficiency, quality, and innovation.
資料ダウンロード
QCD調達購買管理クラウド「newji」は、調達購買部門で必要なQCD管理全てを備えた、現場特化型兼クラウド型の今世紀最高の購買管理システムとなります。
ユーザー登録
調達購買業務の効率化だけでなく、システムを導入することで、コスト削減や製品・資材のステータス可視化のほか、属人化していた購買情報の共有化による内部不正防止や統制にも役立ちます。
NEWJI DX
製造業に特化したデジタルトランスフォーメーション(DX)の実現を目指す請負開発型のコンサルティングサービスです。AI、iPaaS、および先端の技術を駆使して、製造プロセスの効率化、業務効率化、チームワーク強化、コスト削減、品質向上を実現します。このサービスは、製造業の課題を深く理解し、それに対する最適なデジタルソリューションを提供することで、企業が持続的な成長とイノベーションを達成できるようサポートします。
オンライン講座
製造業、主に購買・調達部門にお勤めの方々に向けた情報を配信しております。
新任の方やベテランの方、管理職を対象とした幅広いコンテンツをご用意しております。
お問い合わせ
コストダウンが利益に直結する術だと理解していても、なかなか前に進めることができない状況。そんな時は、newjiのコストダウン自動化機能で大きく利益貢献しよう!
(Β版非公開)