- お役立ち記事
- Optimizing Data Collection in Manufacturing Processes with IoT Devices
Optimizing Data Collection in Manufacturing Processes with IoT Devices
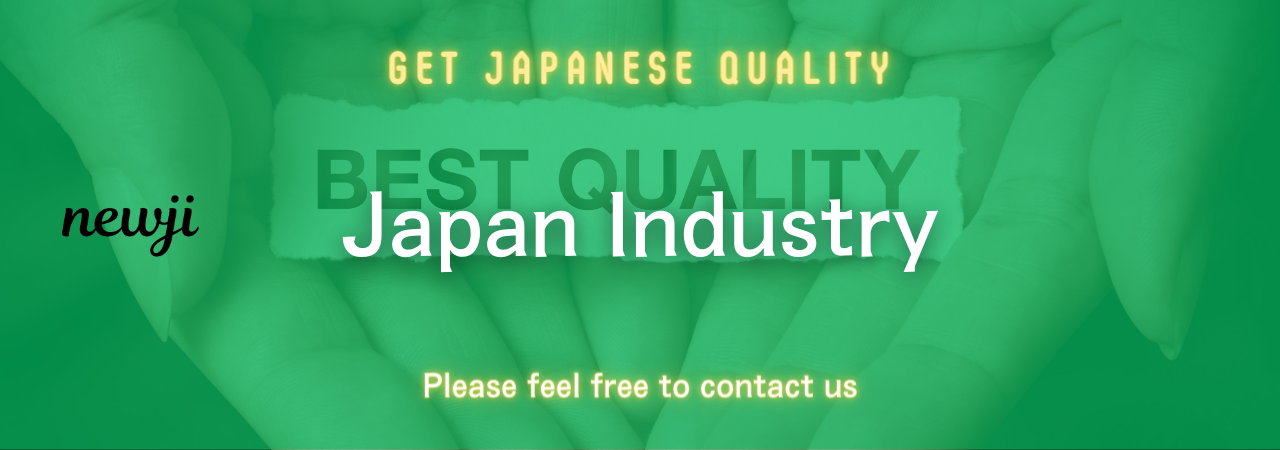
In today’s fast-paced manufacturing world, efficiency and accuracy are more important than ever. One way to achieve these goals is by optimizing data collection in manufacturing processes. With the advent of the Internet of Things (IoT) devices, manufacturers now have powerful tools at their disposal to gather and analyze data in real-time. This not only helps in making informed decisions but also enhances productivity and reduces costs.
目次
What is IoT?
IoT, or the Internet of Things, refers to a network of interconnected devices that communicate with each other via the internet. These devices can range from simple sensors to complex machinery, all equipped with the ability to collect and exchange data. By integrating IoT devices into manufacturing processes, businesses can monitor various aspects of production in real-time, leading to more efficient operations.
The Importance of Data Collection in Manufacturing
Data collection plays a crucial role in manufacturing for several reasons.
1. Improved Decision Making
Accurate and timely data allows managers to make informed decisions. This can range from adjusting production schedules to ordering materials before they run out. With real-time insights, companies can respond to issues promptly, reducing downtime and increasing efficiency.
2. Enhanced Quality Control
Monitoring production processes through IoT devices ensures that products meet quality standards. By tracking parameters like temperature, humidity, and machine performance, it’s easier to spot inconsistencies and make adjustments before defective products are produced.
3. Predictive Maintenance
Data from IoT devices can forecast when machinery is likely to fail, allowing for proactive maintenance. This reduces unexpected breakdowns and extends the lifespan of equipment. Timely maintenance not only saves money but also prevents production halts.
How IoT Devices Enhance Data Collection
IoT devices offer several advantages over traditional data collection methods.
1. Real-Time Monitoring
One of the significant benefits of IoT devices is real-time monitoring. Traditional methods often rely on periodic checks, which can miss critical issues. IoT devices continuously monitor production parameters, providing instant feedback.
2. Automation
IoT devices automate the data collection process. This reduces the reliance on manual entry and minimizes the chances of human error. Automation ensures that data is accurate and consistently recorded.
3. Data Analytics
The data collected by IoT devices can be analyzed to derive actionable insights. Advanced analytics can identify trends, optimize production schedules, and improve overall efficiency. This data-driven approach helps in making strategic decisions that benefit the business.
Examples of IoT Devices in Manufacturing
There are various types of IoT devices used in manufacturing.
1. Sensors
Sensors are the most common type of IoT device. They can measure a wide range of parameters, such as temperature, pressure, and humidity. These sensors provide real-time data that is crucial for maintaining optimal production conditions.
2. Smart Machines
Smart machines are equipped with IoT capabilities, allowing them to communicate with other devices and systems. This integration enables automated production lines, reducing the need for manual intervention and increasing efficiency.
3. Wearable Devices
Wearable IoT devices, such as smartwatches and RFID tags, are used to monitor employee movement and safety. These devices ensure that workers are following safety protocols and can alert them to potential hazards.
Challenges in Implementing IoT for Data Collection
While IoT devices offer many benefits, there are also challenges in their implementation.
1. Security Concerns
One of the primary concerns is data security. With devices connected to the internet, there is a risk of cyber-attacks. It’s essential to implement robust security measures to protect sensitive data.
2. High Initial Costs
The initial cost of implementing IoT devices can be high. This includes the expense of the devices themselves, as well as the cost of integrating them into existing systems. However, the long-term benefits often outweigh these initial costs.
3. Data Management
Collecting vast amounts of data is one thing, but managing and analyzing it is another. Companies need efficient data management systems to handle the influx of information. This might require additional investments in software and personnel.
Steps to Implement IoT in Manufacturing
Implementing IoT devices in manufacturing processes involves several steps.
1. Identify Needs
The first step is to identify the specific needs of the manufacturing process. Determine which areas will benefit most from IoT integration. This could be anything from quality control to supply chain management.
2. Choose the Right Devices
Once the needs are identified, select the appropriate IoT devices. Consider factors like compatibility with existing systems, ease of use, and scalability. Choose devices that offer the best return on investment.
3. Integration
Integrate the chosen IoT devices into the existing manufacturing processes. This might involve modifying current systems and training personnel. Ensure that the devices are correctly connected and communicating with other systems.
4. Monitor and Evaluate
After the IoT devices are implemented, continuously monitor their performance. Evaluate the data collected to ensure that the devices are meeting the expected outcomes. Make adjustments as necessary to optimize their performance.
Future Trends in IoT for Manufacturing
The future of IoT in manufacturing holds exciting possibilities.
1. Artificial Intelligence
The integration of artificial intelligence (AI) with IoT devices will enhance data analysis capabilities. AI can process large datasets quickly and provide more accurate predictions, further improving decision-making processes.
2. Enhanced Connectivity
With advancements in 5G technology, the connectivity of IoT devices will improve significantly. Faster and more reliable connections will enable even more efficient data collection and analysis.
3. Blockchain Technology
Blockchain technology can be used to secure data collected by IoT devices. This will address security concerns and ensure that the data is tamper-proof.
In conclusion, optimizing data collection in manufacturing processes with IoT devices can lead to significant improvements in efficiency, quality, and cost savings. By understanding the benefits and challenges, and following a systematic implementation process, manufacturers can harness the power of IoT to stay competitive in the ever-evolving industrial landscape. As technology continues to advance, the potential for IoT in manufacturing will only grow, paving the way for smarter, more connected production environments.
資料ダウンロード
QCD調達購買管理クラウド「newji」は、調達購買部門で必要なQCD管理全てを備えた、現場特化型兼クラウド型の今世紀最高の購買管理システムとなります。
ユーザー登録
調達購買業務の効率化だけでなく、システムを導入することで、コスト削減や製品・資材のステータス可視化のほか、属人化していた購買情報の共有化による内部不正防止や統制にも役立ちます。
NEWJI DX
製造業に特化したデジタルトランスフォーメーション(DX)の実現を目指す請負開発型のコンサルティングサービスです。AI、iPaaS、および先端の技術を駆使して、製造プロセスの効率化、業務効率化、チームワーク強化、コスト削減、品質向上を実現します。このサービスは、製造業の課題を深く理解し、それに対する最適なデジタルソリューションを提供することで、企業が持続的な成長とイノベーションを達成できるようサポートします。
オンライン講座
製造業、主に購買・調達部門にお勤めの方々に向けた情報を配信しております。
新任の方やベテランの方、管理職を対象とした幅広いコンテンツをご用意しております。
お問い合わせ
コストダウンが利益に直結する術だと理解していても、なかなか前に進めることができない状況。そんな時は、newjiのコストダウン自動化機能で大きく利益貢献しよう!
(Β版非公開)