- お役立ち記事
- Digital human resource development for the future of manufacturing! Essential Skills for Competitiveness!
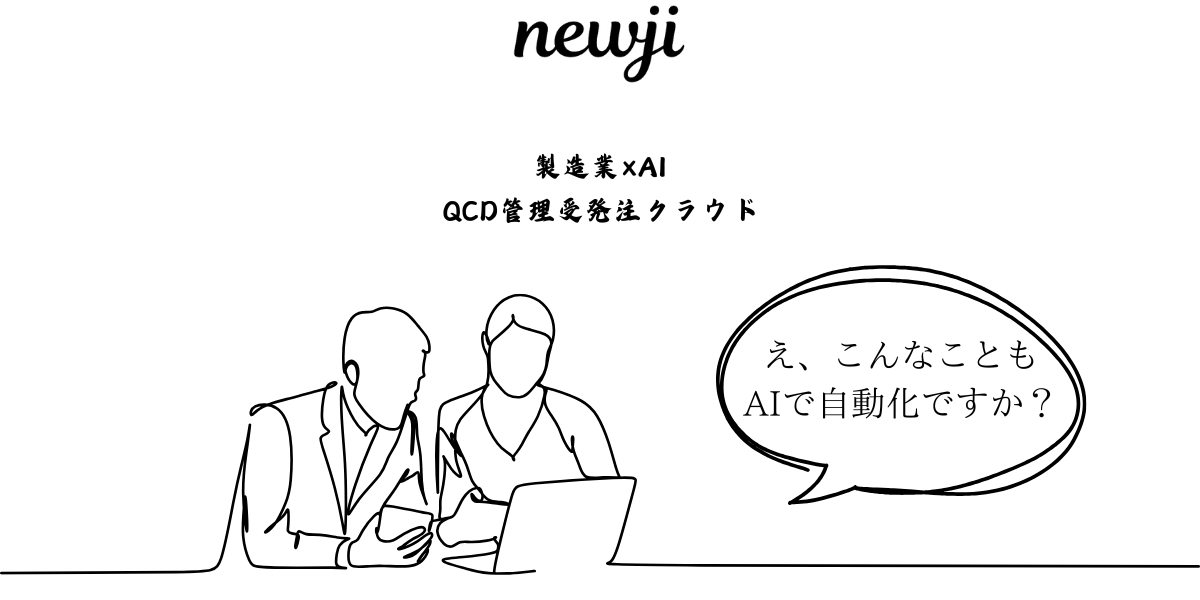
Digital human resource development for the future of manufacturing! Essential Skills for Competitiveness!
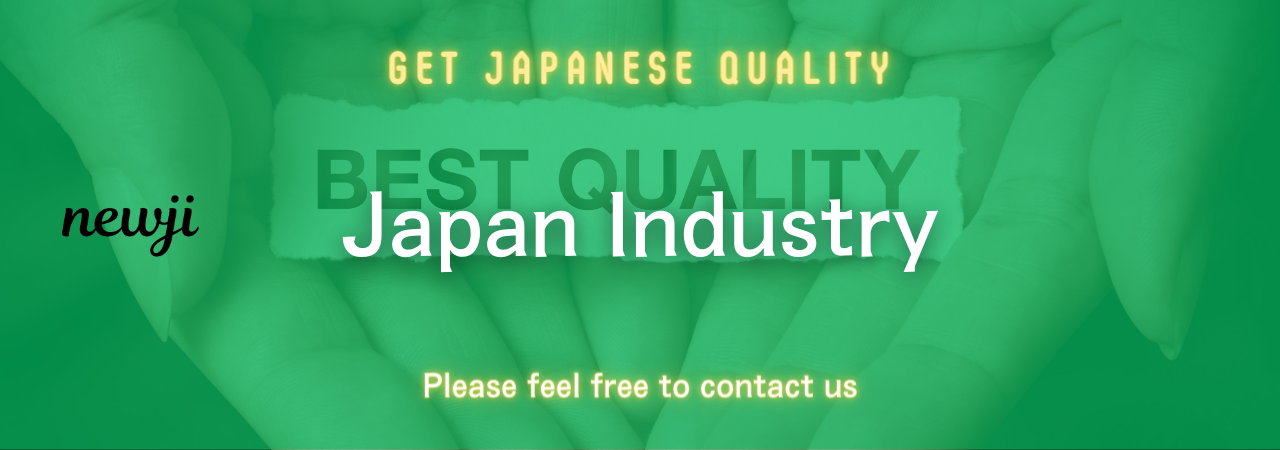
目次
The Importance of Digital Human Resource Development
In today’s fast-paced manufacturing world, staying competitive means continuously adopting the latest technologies and skills.
Traditional methods are no longer sufficient.
Digital human resource development is crucial for companies that want to lead in the industry.
By investing in the right skills and knowledge, manufacturers can boost their productivity, efficiency, and overall performance.
Understanding the importance of digital HR development is the first step toward achieving future success.
Key Skills for the Digital Manufacturing Workplace
To stay ahead in the competitive landscape, it’s essential to identify and develop specific skill sets.
Here are some of the key skills necessary for the future of manufacturing:
1. Data Analysis
Data is the new oil in the manufacturing sector.
Being able to analyze data helps in making informed decisions.
Data analysts scrutinize large datasets to identify patterns, solve problems, and predict future outcomes.
Developing data analysis skills ensures that employees can transform raw data into actionable insights.
2. Programming and Coding
As automation becomes a vital part of manufacturing, programming and coding skills are increasingly in demand.
From operating machinery to maintaining software systems, understanding coding languages like Python, Java, and C++ is becoming essential.
Encouraging employees to learn code can lead to more efficient production processes and less downtime due to technical issues.
3. Cybersecurity
With the rise of digital technologies comes the increased risk of cyber threats.
Protecting sensitive information and intellectual property is crucial.
Training employees in cybersecurity best practices helps safeguard against data breaches and cyber-attacks.
This involves understanding firewalls, encryption, secure communication protocols, and regular system updates.
4. Advanced Manufacturing Technologies
Robotics, 3D printing, and Internet of Things (IoT) are some examples of advanced manufacturing technologies.
These technologies enhance the precision and efficiency of production lines.
Technical knowledge of these innovations enables employees to implement and manage them effectively.
Staying abreast of advancements ensures the company remains competitive and adaptive to changes.
5. Soft Skills
While technical skills are essential, soft skills hold equal importance in the digital landscape.
Effective communication, problem-solving, and teamwork facilitate smoother operations and better project management.
Encouraging a culture of continuous learning and empathy can lead to an engaged and productive workforce.
Implementing Digital HR Development Strategies
Creating an effective digital HR development plan involves several strategies.
Here are a few steps manufacturers can take to foster a digitally proficient workforce:
1. Continuous Learning and Training Programs
Offering ongoing training programs ensures employees stay current with the latest technologies.
These can be in the form of workshops, online courses, or on-the-job training.
Such initiatives not only improve skills but also boost employee morale and retention.
2. Collaboration with Educational Institutions
Partnering with universities and educational institutions can provide access to cutting-edge research and emerging talent.
Collaborative projects and internships bridge the gap between academic knowledge and practical application.
This symbiotic relationship benefits both the company and the students involved.
3. Leverage E-Learning Platforms
E-learning platforms offer flexible and accessible ways to learn new skills.
Employees can benefit from diverse courses tailored to various aspects of digital manufacturing.
Using these platforms can streamline training processes and ensure that the knowledge imparted is up-to-date and relevant.
4. Encouraging Innovation and Creativity
Fostering a culture of innovation helps employees feel empowered to think outside the box.
Creating platforms for idea-sharing and creative problem-solving can lead to groundbreaking advancements in manufacturing processes.
Encouraging innovation can turn challenges into opportunities.
Measuring the Impact of Digital HR Development
Realizing the benefits of digital HR development means implementing metrics to gauge its effectiveness.
Here are ways to measure its impact:
1. Employee Performance
Tracking employee performance before and after training sessions can provide insight into the effectiveness of the programs.
Improved efficiency, error reduction, and increased productivity are clear indicators of successful training.
2. Return on Investment (ROI)
Calculating the ROI of training programs is essential.
This involves comparing the costs of training against the benefits achieved, such as increased revenue or cost savings from improved productivity.
Positive ROI indicates that the training programs are yielding the desired results.
3. Employee Satisfaction and Retention
Satisfied and engaged employees are more likely to stay with the company long-term.
Regular feedback and surveys can provide insight into how employees feel about the training programs and their career growth.
High retention rates often correlate with effective digital HR development initiatives.
Conclusion
Digital human resource development is not merely an option but a necessity for the future of manufacturing.
The rapid advancement of technology necessitates the continuous updating of skills and knowledge.
From data analysis to cybersecurity, and from maintaining advanced manufacturing technologies to developing soft skills, a broad spectrum of competencies is required.
By investing in these areas and fostering a culture of continuous learning, manufacturers can ensure competitiveness, innovation, and success in the evolving digital landscape.
資料ダウンロード
QCD調達購買管理クラウド「newji」は、調達購買部門で必要なQCD管理全てを備えた、現場特化型兼クラウド型の今世紀最高の購買管理システムとなります。
ユーザー登録
調達購買業務の効率化だけでなく、システムを導入することで、コスト削減や製品・資材のステータス可視化のほか、属人化していた購買情報の共有化による内部不正防止や統制にも役立ちます。
NEWJI DX
製造業に特化したデジタルトランスフォーメーション(DX)の実現を目指す請負開発型のコンサルティングサービスです。AI、iPaaS、および先端の技術を駆使して、製造プロセスの効率化、業務効率化、チームワーク強化、コスト削減、品質向上を実現します。このサービスは、製造業の課題を深く理解し、それに対する最適なデジタルソリューションを提供することで、企業が持続的な成長とイノベーションを達成できるようサポートします。
オンライン講座
製造業、主に購買・調達部門にお勤めの方々に向けた情報を配信しております。
新任の方やベテランの方、管理職を対象とした幅広いコンテンツをご用意しております。
お問い合わせ
コストダウンが利益に直結する術だと理解していても、なかなか前に進めることができない状況。そんな時は、newjiのコストダウン自動化機能で大きく利益貢献しよう!
(Β版非公開)