- お役立ち記事
- Clutch Types and Quality Improvement in OEM Manufacturing
Clutch Types and Quality Improvement in OEM Manufacturing
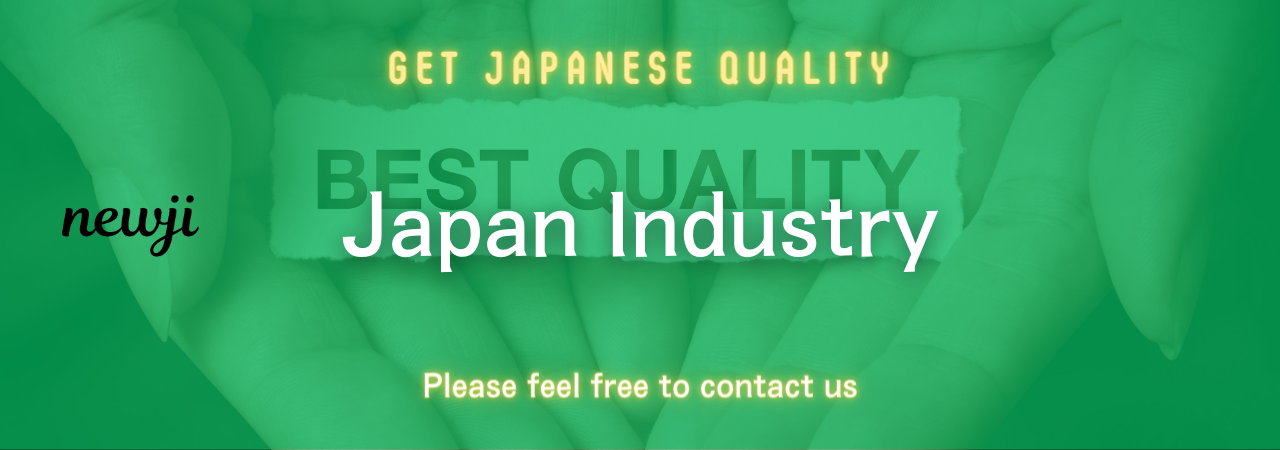
Clutch systems play a critical role in the performance and efficiency of various types of vehicles and machinery.
They are engineered to control the connection between the engine and transmission.
Original Equipment Manufacturers (OEMs) are keenly aware of the importance of using high-quality clutch systems to enhance overall product quality and customer satisfaction.
目次
Types of Clutches
Clutches come in various types, each engineered for specific applications and operating conditions.
Understanding their differences is crucial for selecting the best option for a particular vehicle or machinery.
Friction Clutches
Friction clutches are the most commonly used clutch type.
They operate by having frictional material pressed against a rotating shaft to engage or disengage the connection between the engine and transmission.
These are subdivided into several categories:
Single-Plate Clutch: A single friction plate is used, which makes it simple and cost-effective.
This type is common in most manual transmission vehicles.
Multi-Plate Clutch: Multiple friction plates are used, allowing for greater surface contact and torque transfer.
These are often found in high-performance cars and motorcycles.
Cone-Clutch: This variant uses conical friction surfaces and is primarily used in older vehicles and some machinery.
Centrifugal Clutches
Centrifugal clutches use centrifugal force to engage the clutch.
As the engine speed increases, the centrifugal force pushes weighted shoes outward to engage the drum, facilitating a smooth and automatic engagement.
These clutches are commonly found in scooters, go-karts, and lawnmowers.
Hydraulic Clutches
Hydraulic clutches use hydraulic fluid to transfer pressure from the clutch pedal to the clutch mechanism.
This type offers smoother and easier operation and is often found in modern vehicles.
The hydraulic system also tends to last longer compared to its mechanical counterparts.
Electromagnetic Clutches
These clutches operate using an electromagnetic field to engage and disengage the clutch.
While less common in automotive applications, they are frequently used in machinery and industrial applications.
They offer the advantage of precise control and quick response times.
Quality Improvement in OEM Manufacturing
OEM manufacturing involves producing components that meet the original specifications set by the manufacturer.
Quality improvement is a continual process that ensures the components perform optimally and maintain a high level of reliability.
Several techniques and strategies are employed to achieve quality improvement in clutch manufacturing.
Material Selection
One of the critical factors in achieving high-quality clutches is the selection of materials.
Modern clutches use advanced materials like ceramics, sintered metals, and high-friction composites to improve durability and performance.
These materials can withstand higher temperatures and more robust operating conditions, thereby increasing the lifespan of the clutch.
Precision Manufacturing
Precision in manufacturing is essential to ensure that the clutch components fit and work perfectly together.
Using Computerized Numerical Control (CNC) machinery and advanced manufacturing techniques, manufacturers can achieve high levels of accuracy and consistency.
This reduces the likelihood of defects and improves overall product quality.
Testing and Validation
Robust testing and validation are imperative in ensuring clutch quality.
Various tests, including load testing, life cycle testing, and environmental testing, are conducted to identify any weaknesses or potential points of failure.
These tests help ensure that the final product meets the desired performance and durability standards.
Continuous Improvement Processes
The Kaizen principle, which stands for continuous improvement, plays a vital role in OEM manufacturing.
It involves constantly reviewing and improving manufacturing processes to enhance quality and efficiency.
This may involve updating machinery, improving worker skills, or optimizing the workflow.
By fostering a culture of continuous improvement, OEM manufacturers can maintain high standards and adapt to changing market demands.
Supplier Quality Management
OEMs often rely on multiple suppliers for their raw materials and components.
Ensuring high quality from suppliers is critical to the overall manufacturing process.
Several strategies, such as supplier audits, quality agreements, and performance monitoring, can be employed to maintain supplier quality.
Developing strong relationships with suppliers and working collaboratively to address any issues can significantly enhance the quality of the final product.
Customer Feedback and Field Data
Customer feedback and field data are invaluable for quality improvement.
Listening to customers can provide insights into any issues they may be experiencing and identify areas for improvement.
Field data helps to understand how the product performs in real-world conditions.
By analyzing this information, manufacturers can make informed decisions on how to enhance product quality.
Conclusion
The types of clutches and the steps involved in enhancing quality in OEM manufacturing are pivotal for ensuring exceptional performance and customer satisfaction.
By understanding the various types of clutches and implementing robust quality improvement strategies, OEM manufacturers can produce reliable and efficient products.
Incorporating advanced materials, precision manufacturing, rigorous testing, and continuous improvement processes can significantly contribute to the quality and longevity of clutches in vehicles and machinery.
Ensuring quality from suppliers and leveraging customer feedback are also essential components of a comprehensive quality improvement strategy.
Through these efforts, OEM manufacturers can consistently meet and exceed the expectations of their customers.
資料ダウンロード
QCD調達購買管理クラウド「newji」は、調達購買部門で必要なQCD管理全てを備えた、現場特化型兼クラウド型の今世紀最高の購買管理システムとなります。
ユーザー登録
調達購買業務の効率化だけでなく、システムを導入することで、コスト削減や製品・資材のステータス可視化のほか、属人化していた購買情報の共有化による内部不正防止や統制にも役立ちます。
NEWJI DX
製造業に特化したデジタルトランスフォーメーション(DX)の実現を目指す請負開発型のコンサルティングサービスです。AI、iPaaS、および先端の技術を駆使して、製造プロセスの効率化、業務効率化、チームワーク強化、コスト削減、品質向上を実現します。このサービスは、製造業の課題を深く理解し、それに対する最適なデジタルソリューションを提供することで、企業が持続的な成長とイノベーションを達成できるようサポートします。
オンライン講座
製造業、主に購買・調達部門にお勤めの方々に向けた情報を配信しております。
新任の方やベテランの方、管理職を対象とした幅広いコンテンツをご用意しております。
お問い合わせ
コストダウンが利益に直結する術だと理解していても、なかなか前に進めることができない状況。そんな時は、newjiのコストダウン自動化機能で大きく利益貢献しよう!
(Β版非公開)