- お役立ち記事
- DX in the polishing process determines the quality and accuracy of the final finish
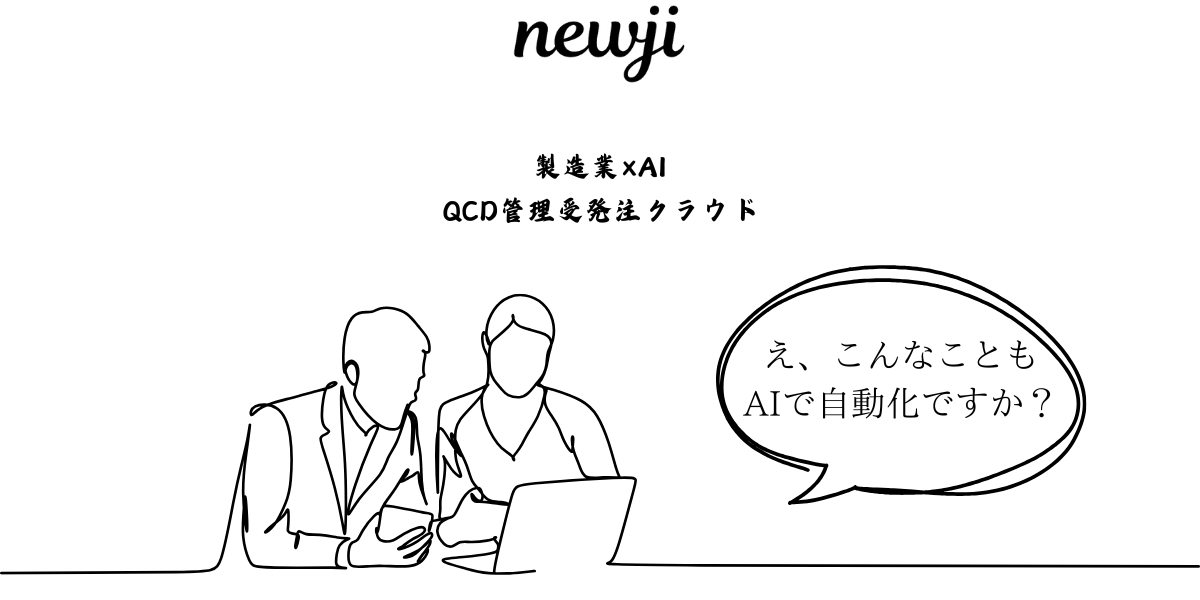
DX in the polishing process determines the quality and accuracy of the final finish
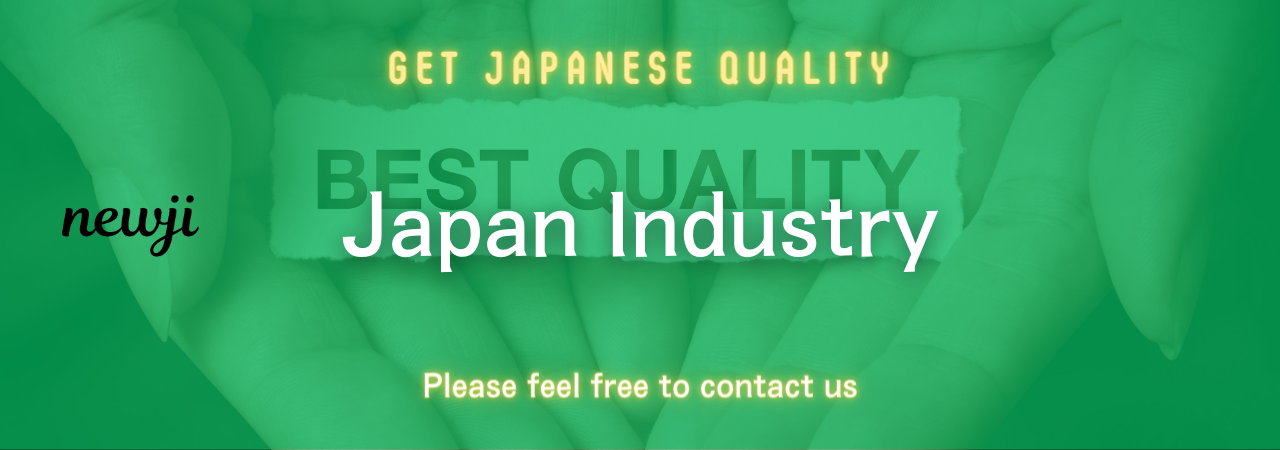
In the world of manufacturing, few steps are as critical as the polishing process.
This finishing touch is what transforms a rough product into a gleaming, market-ready piece.
However, achieving such impeccable results isn’t just about elbow grease.
Enter the world of DX, or digital transformation, in the polishing process.
This powerful integration of digital technologies into every facet of polishing can remarkably influence the final quality and accuracy of the finish.
目次
What is Digital Transformation (DX) in Polishing?
Digital transformation refers to the adoption of digital technologies to change traditional methods and processes. In the context of polishing, this means incorporating advanced technologies such as artificial intelligence (AI), machine learning, and the Internet of Things (IoT) to refine and perfect the process.
By utilizing DX, manufacturers can enhance precision, increase efficiency, and reduce waste.
For instance, AI can analyze data from previous polishing tasks to determine the optimal methods for new projects.
IoT devices can monitor equipment in real-time, ensuring that it operates at peak efficiency and flags any potential issues before they become problematic.
Advantages of DX in the Polishing Process
Enhanced Precision
One of the most significant advantages of integrating DX into polishing is the enhanced precision it offers.
Traditional polishing methods can be inconsistent, with human error leading to variations in the final product.
With DX, machines can be calibrated to achieve uniform results every time.
Sensors and monitoring devices continuously check and adjust the polishing parameters, ensuring the surface finish remains consistent.
Increased Efficiency
Efficiency is another critical benefit of DX in the polishing process.
Automated systems can polish products much faster than manual methods.
Additionally, by analyzing performance data, manufacturers can identify bottlenecks and optimize processes to further enhance productivity.
Machine learning algorithms can predict when maintenance is needed, reducing downtime and ensuring that the equipment operates smoothly.
This predictive maintenance saves time and reduces costs associated with unexpected equipment failures.
Reduced Waste
Waste reduction is another area where DX shines.
Traditional polishing can generate a significant amount of material waste, either due to imprecision or unnecessary steps.
However, digital systems can minimize waste by optimizing the polishing process.
IoT sensors can monitor the amount of material being removed during polishing, ensuring that it is only as much as needed to achieve the desired finish.
This not only conserves resources but also reduces costs.
Implementing DX in the Polishing Process
Implementing DX in the polishing process involves several key steps.
Assessing Current Processes
The first step is to assess the current polishing methods and identify areas where digital technologies can make a difference. This could involve mapping out the entire process, from start to finish, and pinpointing where inefficiencies or inconsistencies occur.
Choosing the Right Technologies
Next, it’s essential to choose the right technologies for your specific needs. For some manufacturers, AI and machine learning might be the most beneficial, while others might benefit more from IoT and real-time monitoring.
It’s crucial to work with experts who can help identify and integrate the right technologies for your business.
Training and Development
Once the technologies are chosen, training employees to use them effectively is essential. This involves not only technical training but also helping employees understand the benefits of the new systems and how they can improve their workflow.
Continuous Improvement
Finally, it’s important to remember that DX is an ongoing process.
Regularly reviewing and refining the digital systems ensures they continue to meet the changing needs of the business.
By continuously seeking out new technologies and methods, manufacturers can stay ahead of the competition and maintain the highest standards of quality.
Case Studies of Successful DX Implementation
Several companies have successfully integrated DX into their polishing processes with outstanding results.
Automotive Industry
In the automotive industry, one leading manufacturer implemented AI-driven polishing robots in its production line.
These robots analyze each vehicle part in real-time, adjusting their polishing techniques to ensure a flawless finish.
As a result, the company saw a significant reduction in defects and rework, as well as faster production times.
Electronics Manufacturing
An electronics manufacturer incorporated IoT sensors into their polishing machines. These sensors monitored the equipment’s performance and flagged any irregularities before they could become issues. By doing so, the company reduced downtime, increased production efficiency, and achieved a more consistent finish on their products.
Medical Device Production
A medical device company adopted machine learning algorithms to optimize its polishing process. These algorithms analyzed data from previous polishing runs to determine the best techniques for new products. The result was a significant improvement in the quality and accuracy of the final finish, meeting the stringent standards required in the medical field.
The Future of DX in Polishing
As technology continues to evolve, the potential for DX in the polishing process will only grow.
Emerging technologies such as augmented reality (AR) and virtual reality (VR) could provide real-time feedback and guidance to operators, further enhancing precision and efficiency.
Additionally, advancements in AI and machine learning will allow for even more sophisticated analysis and optimization of the polishing process.
These technologies will enable manufacturers to achieve a level of quality and accuracy that was previously unattainable.
In conclusion, the integration of digital transformation into the polishing process is revolutionizing the manufacturing industry.
By leveraging advanced technologies, manufacturers can enhance precision, increase efficiency, and reduce waste.
Implementing DX involves assessing current processes, choosing the right technologies, training employees, and continuously seeking improvement.
資料ダウンロード
QCD調達購買管理クラウド「newji」は、調達購買部門で必要なQCD管理全てを備えた、現場特化型兼クラウド型の今世紀最高の購買管理システムとなります。
ユーザー登録
調達購買業務の効率化だけでなく、システムを導入することで、コスト削減や製品・資材のステータス可視化のほか、属人化していた購買情報の共有化による内部不正防止や統制にも役立ちます。
NEWJI DX
製造業に特化したデジタルトランスフォーメーション(DX)の実現を目指す請負開発型のコンサルティングサービスです。AI、iPaaS、および先端の技術を駆使して、製造プロセスの効率化、業務効率化、チームワーク強化、コスト削減、品質向上を実現します。このサービスは、製造業の課題を深く理解し、それに対する最適なデジタルソリューションを提供することで、企業が持続的な成長とイノベーションを達成できるようサポートします。
オンライン講座
製造業、主に購買・調達部門にお勤めの方々に向けた情報を配信しております。
新任の方やベテランの方、管理職を対象とした幅広いコンテンツをご用意しております。
お問い合わせ
コストダウンが利益に直結する術だと理解していても、なかなか前に進めることができない状況。そんな時は、newjiのコストダウン自動化機能で大きく利益貢献しよう!
(Β版非公開)