- お役立ち記事
- DX of the casting process dramatically improves product precision and yield
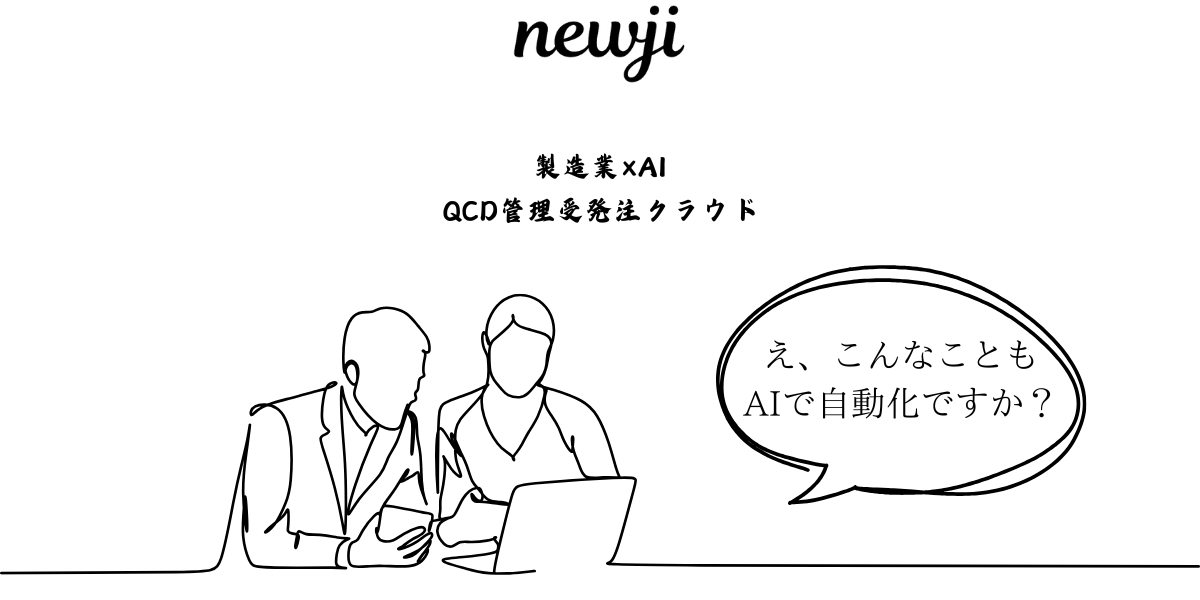
DX of the casting process dramatically improves product precision and yield
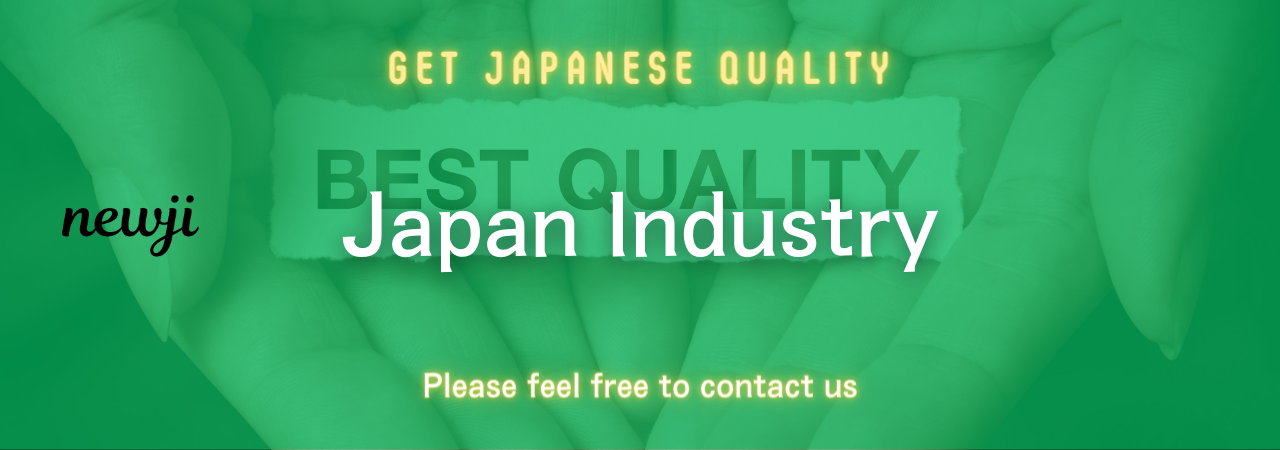
The digital transformation (DX) of the casting process is reshaping the manufacturing landscape, dramatically enhancing product precision and yield.
Digital transformation involves integrating digital technologies into all areas of a business to fundamentally change how it operates and delivers value to customers.
In the context of the casting process, DX brings about profound improvements in efficiency, accuracy, and overall production capability.
目次
Understanding Digital Transformation in Casting
To appreciate the impact of DX in casting, it’s essential to understand traditional casting methods and their limitations.
Casting is a manufacturing process where liquid material is poured into a mold to form a desired shape as it solidifies.
Despite being a time-honored technique, conventional casting has its challenges, such as human errors, material wastage, and inconsistent quality.
With digital transformation, these issues can be substantially mitigated, if not entirely eliminated.
Technology like computer-aided design (CAD), computer-aided manufacturing (CAM), 3D printing, and Internet of Things (IoT) sensors are integral to this shift.
These advancements enable precise control and monitoring of every step in the casting process.
The Role of Computer-Aided Design (CAD) in Casting
One of the key facets of digital transformation in casting is the adoption of CAD.
CAD software allows engineers and designers to create highly detailed and accurate 3D models of the parts they need to cast.
Using CAD, they can simulate the casting process, foresee potential issues, and optimize the design before any physical material is used.
This preemptive approach reduces the likelihood of defects, ensuring that the final products meet the required specifications.
CAD models can be directly fed into CAM systems, streamlining the transition from design to manufacturing.
This integration helps maintain design integrity, saves time, and reduces the risk of errors.
Enhancing Precision with 3D Printing
3D printing, also known as additive manufacturing, is another revolutionary technology in the digital transformation of casting.
It allows manufacturers to create complex, high-precision molds or patterns directly from CAD data.
The patterns used in traditional casting are typically made manually, which can introduce inconsistencies.
In contrast, 3D printing creates patterns and molds with exceptional accuracy, improving the overall quality of the cast products.
Moreover, 3D printing supports rapid prototyping, enabling faster design iterations and reducing the time from concept to production.
Manufacturers can quickly test new designs and make necessary adjustments, enhancing the efficiency of the development process.
Leveraging IoT for Real-Time Monitoring
The Internet of Things (IoT) plays a crucial role in the digital transformation of casting by facilitating real-time monitoring and control of the production process.
IoT sensors can be embedded in various stages of the casting workflow to collect data on temperature, pressure, and material flow.
This data is transmitted to central systems for analysis, providing insights into the process’s performance and identifying any deviations from the desired parameters.
Real-time monitoring ensures immediate corrective actions can be taken, minimizing the risk of defects and wastage.
Additionally, IoT enables predictive maintenance, helping to identify potential equipment failures before they occur.
By proactively managing maintenance, manufacturers can reduce downtime, extend the lifespan of machinery, and optimize their production schedules.
Big Data and Analytics for Continuous Improvement
Data generated by IoT devices and other digital tools can be leveraged through big data analytics to drive continuous improvement in the casting process.
By analyzing large volumes of data, manufacturers can uncover patterns and correlations that might be missed by human oversight.
This analysis can reveal inefficiencies, predict outcomes, and provide actionable insights for process optimization.
For example, data analytics can help determine the optimal temperature and timing for pouring liquid material to reduce defects.
Continuous learning from data enables manufacturers to make informed decisions, improve process consistency, and enhance product quality.
Benefits of Digital Transformation in Casting
The DX of the casting process offers numerous benefits that extend beyond precision and yield enhancement.
Improved Product Quality
By integrating digital technologies, manufacturers can achieve higher levels of accuracy and consistency in their products.
Reduced defects and deviations ensure that parts meet stringent quality standards.
Increased Efficiency
Automation and real-time monitoring streamline production workflows, reducing cycle times and eliminating bottlenecks.
This efficiency translates into faster delivery times and higher throughput.
Cost Savings
Minimized material waste, optimized use of resources, and reduced downtime contribute to significant cost savings over time.
While the initial investment in digital technologies can be substantial, the long-term return on investment is compelling.
Enhanced Flexibility
Digital tools like CAD and 3D printing offer greater design flexibility, allowing manufacturers to create complex and customized parts efficiently.
This adaptability is essential for meeting diverse customer requirements.
Improved Sustainability
DX in casting supports eco-friendly manufacturing practices.
Efficient use of materials and reduced waste align with sustainability goals, making the process more environmentally friendly.
The Future of Digital Transformation in Casting
The journey of digital transformation in casting is ongoing, with emerging technologies continually pushing the boundaries of what’s possible.
Artificial intelligence (AI) and machine learning are set to play significant roles in the future, further enhancing predictive capabilities and process automation.
Collaborative robots (cobots) may also become commonplace, working alongside human operators to improve safety and efficiency.
As these technologies evolve, the casting process will continue to become more precise, efficient, and adaptable, driving innovation in manufacturing.
In conclusion, the DX of the casting process represents a paradigm shift in manufacturing, offering unparalleled advancements in product precision and yield.
By embracing digital technologies, manufacturers can overcome traditional limitations, achieve higher quality standards, and stay competitive in a rapidly changing market.
As the industry continues to evolve, the fusion of digital tools and casting will pave the way for a more efficient, sustainable, and innovative future.
資料ダウンロード
QCD調達購買管理クラウド「newji」は、調達購買部門で必要なQCD管理全てを備えた、現場特化型兼クラウド型の今世紀最高の購買管理システムとなります。
ユーザー登録
調達購買業務の効率化だけでなく、システムを導入することで、コスト削減や製品・資材のステータス可視化のほか、属人化していた購買情報の共有化による内部不正防止や統制にも役立ちます。
NEWJI DX
製造業に特化したデジタルトランスフォーメーション(DX)の実現を目指す請負開発型のコンサルティングサービスです。AI、iPaaS、および先端の技術を駆使して、製造プロセスの効率化、業務効率化、チームワーク強化、コスト削減、品質向上を実現します。このサービスは、製造業の課題を深く理解し、それに対する最適なデジタルソリューションを提供することで、企業が持続的な成長とイノベーションを達成できるようサポートします。
オンライン講座
製造業、主に購買・調達部門にお勤めの方々に向けた情報を配信しております。
新任の方やベテランの方、管理職を対象とした幅広いコンテンツをご用意しております。
お問い合わせ
コストダウンが利益に直結する術だと理解していても、なかなか前に進めることができない状況。そんな時は、newjiのコストダウン自動化機能で大きく利益貢献しよう!
(Β版非公開)