- お役立ち記事
- DX in Plating Process Improves Uniformity, Adhesion, and Working Environment
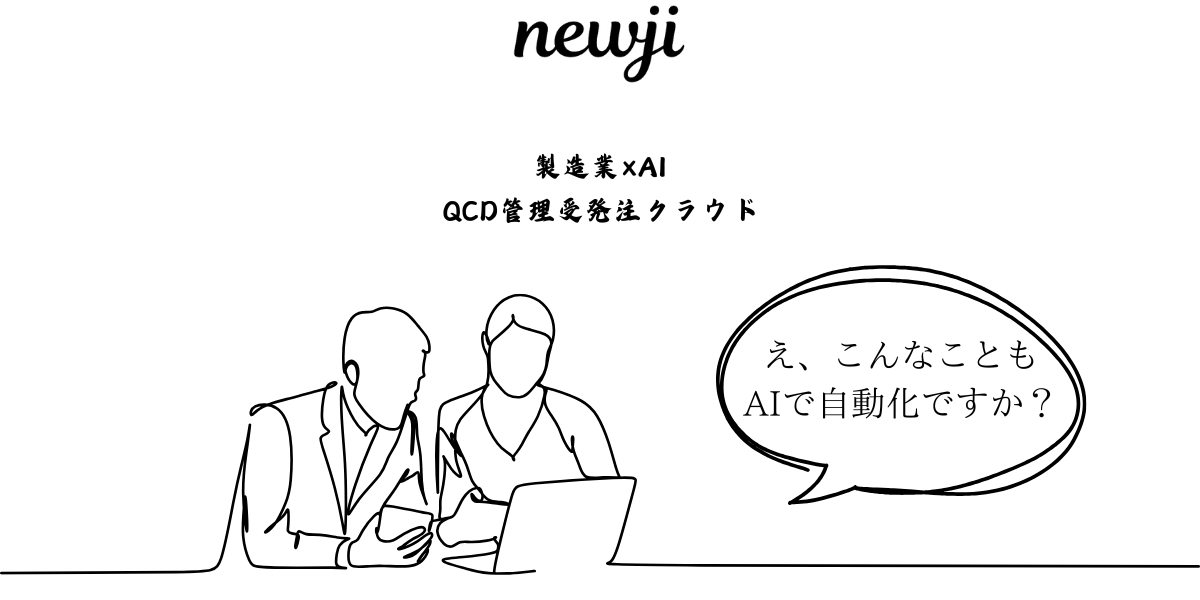
DX in Plating Process Improves Uniformity, Adhesion, and Working Environment
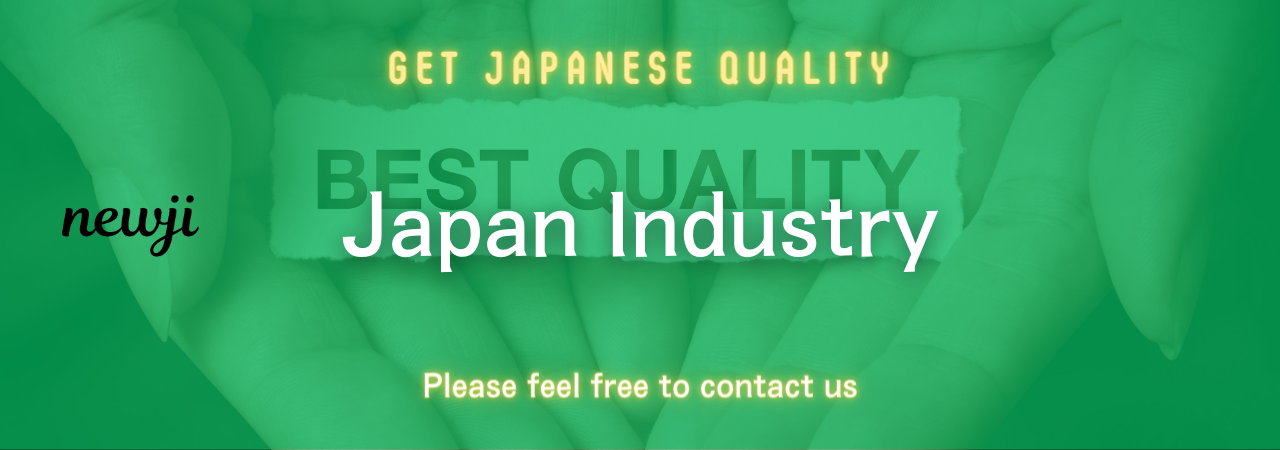
In today’s rapidly evolving manufacturing world, digital transformation (DX) is making significant strides in various processes, including plating.
The plating process is crucial in many industries, offering corrosion resistance, enhancing appearance, and providing wear resistance to metal parts.
By implementing DX in the plating process, companies can achieve improved uniformity, better adhesion, and enhanced working environments.
目次
The Role of Digital Transformation in Plating
Digital transformation refers to the integration of digital technology into all aspects of a business.
This transformation leads to fundamental changes in how businesses operate and deliver value to customers.
In the plating industry, DX involves the use of advanced technologies such as automation, data analytics, and the Internet of Things (IoT) to optimize the plating process.
Automation Enhances Consistency
One of the primary benefits of digital transformation in plating is enhanced process consistency through automation.
Automated systems allow for precise control over various plating parameters like temperature, voltage, and concentration of chemical solutions.
By maintaining consistent parameters, automated systems reduce variations in the plating process, resulting in improved uniformity of the plated layer.
Additionally, automation minimizes human error, which can significantly impact the quality of the plating.
With automated plating systems, companies can achieve a higher level of repeatability and reliability, ensuring that each batch of plated parts meets the required standards.
Data Analytics for Process Optimization
Data analytics plays a critical role in optimizing the plating process.
By collecting and analyzing data from various stages of the plating process, companies can identify trends, patterns, and potential issues.
This information allows for informed decision-making and continuous process improvement.
For instance, data analytics can help identify the optimal combination of plating parameters to achieve the best adhesion and uniformity.
By understanding the relationships between different variables, companies can fine-tune their processes to maximize performance and minimize defects.
Predictive analytics also enables proactive maintenance of plating equipment.
By analyzing data from sensors and monitoring systems, companies can predict potential equipment failures and schedule maintenance before issues arise.
This predictive maintenance approach reduces downtime and ensures a smooth, uninterrupted plating process.
Enhanced Adhesion Through Digital Transformation
Adhesion is a critical factor in the plating process, as it determines the durability and performance of the plated layer.
Digital transformation offers several ways to improve adhesion in plating operations.
Surface Preparation and Treatment
Proper surface preparation is essential for achieving strong adhesion in plating.
Through digital transformation, companies can use advanced technologies such as laser surface texturing and plasma treatment to prepare surfaces more effectively.
These technologies create micro-scale surface features that enhance the mechanical interlocking between the substrate and the plated layer.
Furthermore, digital tools can monitor and control surface treatment processes with high precision.
For example, IoT-enabled sensors can measure parameters such as surface roughness and cleanliness in real-time.
By ensuring optimal surface conditions, companies can achieve better adhesion and reduce the risk of coating failure.
Real-Time Monitoring and Adjustments
Real-time monitoring is another key aspect of digital transformation that improves adhesion in the plating process.
With the help of IoT sensors and advanced monitoring systems, companies can continuously track various parameters such as current density, bath composition, and temperature.
If any deviations from the desired conditions are detected, the system can automatically adjust the parameters to maintain optimal plating conditions.
This real-time adjustment ensures that the plated layer adheres well to the substrate throughout the process.
Improving the Working Environment With DX
Digital transformation not only enhances the technical aspects of the plating process but also significantly improves the working environment for employees.
Enhanced Safety Measures
The plating process involves handling hazardous chemicals and working with electrical equipment, which pose safety risks to workers.
DX introduces advanced safety measures that can mitigate these risks.
For instance, automated systems can handle dangerous chemicals, reducing the need for human intervention and minimizing exposure to harmful substances.
IoT-enabled sensors can also monitor environmental conditions such as air quality and chemical concentrations in real-time.
If unsafe levels are detected, the system can trigger alarms and initiate corrective actions, ensuring a safer working environment for employees.
Reducing Manual Labor
Automation and digital tools reduce the manual labor required in the plating process.
Employees no longer need to perform repetitive and physically demanding tasks, which can lead to fatigue and injuries.
Instead, they can focus on more value-added activities such as process optimization and quality control.
Additionally, digital transformation enables remote monitoring and control of plating operations.
Employees can oversee the process from a centralized control room or even remotely, reducing the need for direct exposure to the working environment.
Conclusion
Digital transformation is revolutionizing the plating process, offering significant improvements in uniformity, adhesion, and working environment.
By leveraging advanced technologies such as automation, data analytics, and IoT, companies can achieve higher levels of consistency and quality in their plated products.
Furthermore, DX enhances safety and reduces manual labor, creating a more efficient and employee-friendly working environment.
As industries continue to embrace digital transformation, the future of plating looks brighter than ever.
資料ダウンロード
QCD調達購買管理クラウド「newji」は、調達購買部門で必要なQCD管理全てを備えた、現場特化型兼クラウド型の今世紀最高の購買管理システムとなります。
ユーザー登録
調達購買業務の効率化だけでなく、システムを導入することで、コスト削減や製品・資材のステータス可視化のほか、属人化していた購買情報の共有化による内部不正防止や統制にも役立ちます。
NEWJI DX
製造業に特化したデジタルトランスフォーメーション(DX)の実現を目指す請負開発型のコンサルティングサービスです。AI、iPaaS、および先端の技術を駆使して、製造プロセスの効率化、業務効率化、チームワーク強化、コスト削減、品質向上を実現します。このサービスは、製造業の課題を深く理解し、それに対する最適なデジタルソリューションを提供することで、企業が持続的な成長とイノベーションを達成できるようサポートします。
オンライン講座
製造業、主に購買・調達部門にお勤めの方々に向けた情報を配信しております。
新任の方やベテランの方、管理職を対象とした幅広いコンテンツをご用意しております。
お問い合わせ
コストダウンが利益に直結する術だと理解していても、なかなか前に進めることができない状況。そんな時は、newjiのコストダウン自動化機能で大きく利益貢献しよう!
(Β版非公開)