- お役立ち記事
- Introduction and benefits of PdM: Preventive maintenance and efficient maintenance of production equipment
Introduction and benefits of PdM: Preventive maintenance and efficient maintenance of production equipment
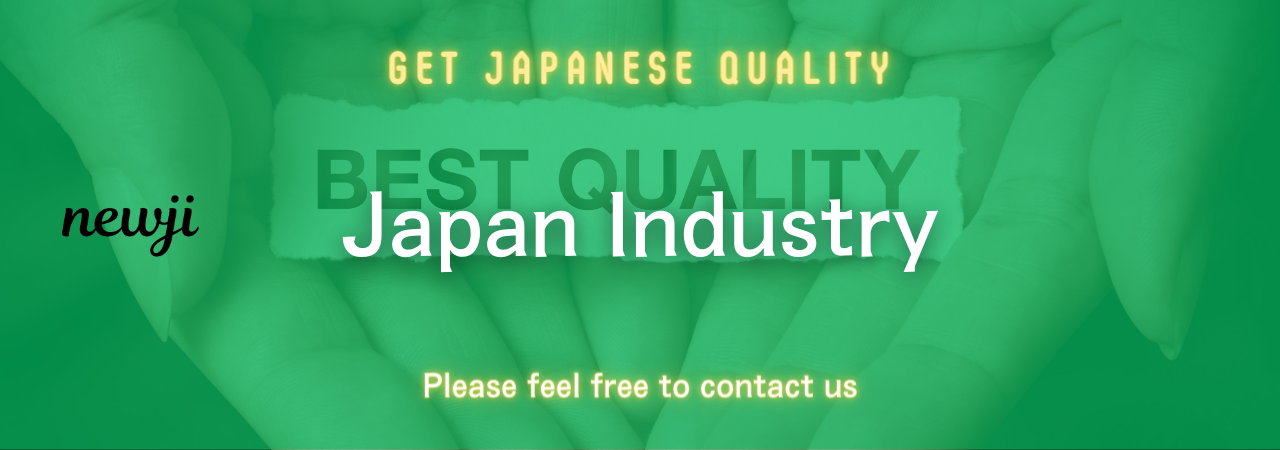
Predictive Maintenance (PdM) is transforming the way we maintain production equipment.
It uses technology to predict when equipment might fail, allowing us to fix it before it actually breaks down.
This proactive approach offers numerous benefits over traditional maintenance methods.
目次
What is Predictive Maintenance (PdM)?
Predictive Maintenance is a type of maintenance that uses data and technology to predict equipment failures.
Sensors and software tools collect data on various aspects of the equipment.
This data is then analyzed to forecast when a machine might fail or need servicing.
Unlike traditional maintenance, which is often reactive, PdM allows manufacturers to address issues before they escalate.
This proactive approach not only saves time but also reduces costs associated with equipment downtime.
How Does Predictive Maintenance Work?
Data Collection
The first step in PdM is data collection.
Sensors are installed on the equipment to gather data on things like temperature, vibration, and pressure.
These sensors continuously monitor the equipment’s performance and send this data to a central system.
Data Analysis
Once the data is collected, it needs to be analyzed.
Specialized software tools use algorithms to analyze the data and identify patterns.
These patterns help predict when a machine might fail.
The software can also provide insights into why the equipment is likely to fail, allowing for more targeted maintenance actions.
Actionable Insights
The final step in the PdM process is turning the analysis into actionable insights.
Maintenance teams receive alerts and recommendations based on the data analysis.
They can then schedule maintenance activities at convenient times, minimizing disruption to production schedules.
Benefits of Predictive Maintenance
Reduced Downtime
One of the biggest benefits of PdM is reduced downtime.
By identifying potential issues before they become major problems, companies can schedule maintenance during non-productive hours.
This means less unexpected downtime and more consistent production rates.
Cost Savings
PdM can also lead to significant cost savings.
Traditional maintenance approaches often involve frequent inspections and part replacements, which can be costly.
With PdM, maintenance activities are only performed when necessary, reducing the need for unnecessary part replacements and labor costs.
Extended Equipment Lifespan
Another advantage of PdM is the extended lifespan of the equipment.
Regular and targeted maintenance helps keep machines in optimal condition for a longer period.
This means companies can get more value out of their investments in production equipment.
Improved Safety
Predictive Maintenance also improves safety.
By preventing equipment failures, PdM reduces the risk of accidents and injuries in the workplace.
This creates a safer environment for employees and can also help companies comply with safety regulations.
PdM in Different Industries
Manufacturing
In the manufacturing sector, PdM plays a crucial role in ensuring that production lines run smoothly.
Equipment failures can be costly and disruptive.
By implementing PdM, manufacturers can maintain high levels of efficiency and product quality.
Energy
The energy industry also benefits from PdM.
Power plants and other energy facilities use PdM to monitor critical equipment such as turbines and generators.
This helps prevent unexpected failures that could lead to power outages and other serious issues.
Transportation
In the transportation industry, PdM is used to keep vehicles and infrastructure in good working condition.
For example, trains and airplanes are equipped with sensors that monitor various components.
This data helps maintenance teams address potential issues before they disrupt services.
Implementing Predictive Maintenance
Choosing the Right Tools
The first step in implementing PdM is choosing the right tools.
This includes selecting the appropriate sensors and software for data collection and analysis.
It’s important to choose tools that are compatible with the specific equipment and processes in your facility.
Training Your Team
Next, you’ll need to train your maintenance team on how to use the new tools and technology.
This includes understanding how to set up and monitor sensors, as well as how to interpret the data and take appropriate actions.
Starting Small
It’s often a good idea to start small when implementing PdM.
Begin with a pilot project on a single piece of equipment or a small production line.
This allows you to test the technology and make any necessary adjustments before rolling it out on a larger scale.
Conclusion
Predictive Maintenance offers a range of benefits that can significantly improve the efficiency and cost-effectiveness of maintaining production equipment.
From reducing downtime and costs to extending equipment lifespan and improving safety, PdM is a valuable tool for any industry.
By following the steps outlined above, companies can successfully implement PdM and enjoy its many advantages.
資料ダウンロード
QCD調達購買管理クラウド「newji」は、調達購買部門で必要なQCD管理全てを備えた、現場特化型兼クラウド型の今世紀最高の購買管理システムとなります。
ユーザー登録
調達購買業務の効率化だけでなく、システムを導入することで、コスト削減や製品・資材のステータス可視化のほか、属人化していた購買情報の共有化による内部不正防止や統制にも役立ちます。
NEWJI DX
製造業に特化したデジタルトランスフォーメーション(DX)の実現を目指す請負開発型のコンサルティングサービスです。AI、iPaaS、および先端の技術を駆使して、製造プロセスの効率化、業務効率化、チームワーク強化、コスト削減、品質向上を実現します。このサービスは、製造業の課題を深く理解し、それに対する最適なデジタルソリューションを提供することで、企業が持続的な成長とイノベーションを達成できるようサポートします。
オンライン講座
製造業、主に購買・調達部門にお勤めの方々に向けた情報を配信しております。
新任の方やベテランの方、管理職を対象とした幅広いコンテンツをご用意しております。
お問い合わせ
コストダウンが利益に直結する術だと理解していても、なかなか前に進めることができない状況。そんな時は、newjiのコストダウン自動化機能で大きく利益貢献しよう!
(Β版非公開)