- お役立ち記事
- Providing Reliable Sealing Components in OEM Seal Manufacturing
Providing Reliable Sealing Components in OEM Seal Manufacturing
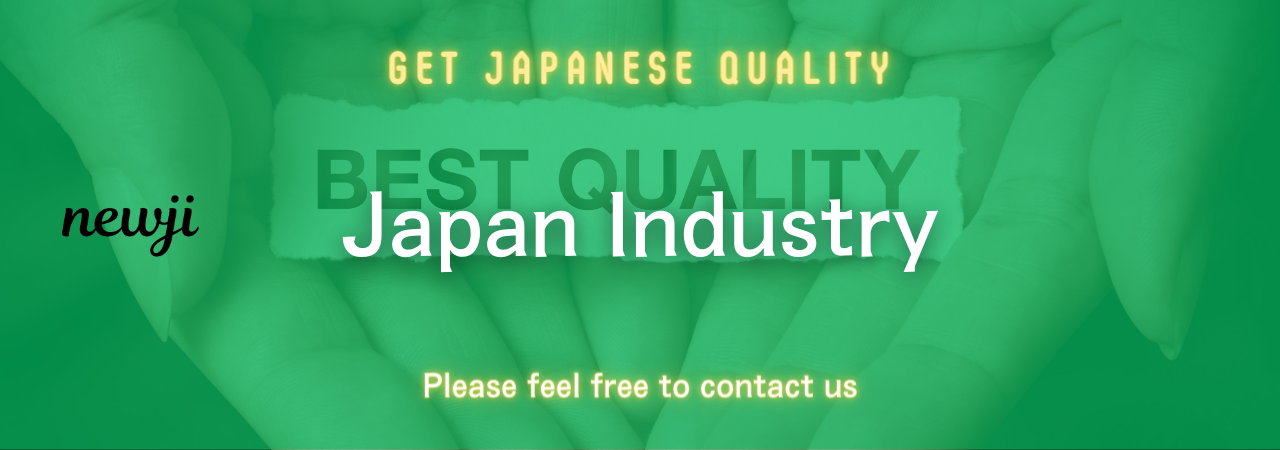
When it comes to manufacturing, one of the most critical aspects is ensuring that machinery and products operate smoothly and efficiently.
A crucial component in achieving this is the quality of sealing solutions used.
Sealing components are used to prevent leaks, protect from contaminants, and ensure the longevity of the machinery.
In Original Equipment Manufacturer (OEM) seal manufacturing, reliability is not just an advantage; it’s a necessity.
目次
Understanding OEM Seals
OEM seals are specialized components designed to fit and function within specific equipment.
These seals are often custom-made to match precise specifications, ensuring compatibility and optimal performance.
The primary purpose of these seals is to provide a barrier that keeps substances such as fluids, gases, or even dust, inside, containing them within a designated area.
Materials Used in OEM Seals
The effectiveness of an OEM seal largely depends on its material.
Materials commonly used in OEM seals include rubber, silicone, PTFE (Teflon), and metal.
Each material offers unique properties suited for different applications:
– **Rubber:** Known for flexibility and resilience, rubber seals are ideal for preventing leaks in dynamic applications.
– **Silicone:** With high thermal stability, silicone seals are used in environments with extreme temperature variations.
– **PTFE (Teflon):** Offers excellent chemical resistance, making it suitable for seals in harsh chemical environments.
– **Metal:** Metal seals are robust and durable, perfect for high-pressure and high-temperature applications.
The Importance of Quality in OEM Seal Manufacturing
Quality is paramount in OEM seal manufacturing.
Poor-quality seals can lead to leaks, contamination, and, ultimately, machinery failure.
Ensuring the reliability of seals involves several factors.
Precision Engineering
One of the most crucial aspects of OEM seal manufacturing is precision engineering.
Seals must be crafted to exact specifications to ensure a perfect fit and optimal function.
This requires advanced machinery and skilled engineers who understand the intricate details of the equipment for which the seals are being designed.
Material Selection
Selecting the right material is equally important.
Manufacturers must consider the operating environment, the type of substances being sealed, and the expected stress and strain on the seals.
Using high-quality, appropriate materials can greatly enhance the reliability and durability of the seals.
Testing and Quality Control
Before OEM seals are approved for use, they must undergo rigorous testing.
This includes stress testing, leak testing, and compatibility testing with the intended equipment.
Quality control processes must be stringent, ensuring that each seal meets the highest standards before it reaches the customer.
Applications of OEM Seals
OEM seals are used across various industries, each with unique requirements and challenges.
Some common applications include:
Automotive Industry
In the automotive industry, OEM seals are essential for engines, transmissions, and other critical components.
These seals help prevent oil leaks, maintain pressure, and protect against contaminants.
Given the high-stress environment of automotive applications, the seals must be exceptionally durable and reliable.
Aerospace Industry
The aerospace industry demands the highest standards of reliability and precision.
OEM seals in this field must withstand extreme temperatures, high pressures, and harsh environmental conditions.
They are used in engines, hydraulic systems, and other vital components to ensure the safety and efficiency of aircraft.
Medical Devices
OEM seals in medical devices play a crucial role in maintaining sterility and functionality.
These seals are often used in surgical instruments, diagnostic equipment, and fluid delivery systems.
Given the critical nature of medical applications, the seals must meet stringent regulatory requirements and be made from biocompatible materials.
Challenges in OEM Seal Manufacturing
While OEM seal manufacturing is essential, it comes with its challenges.
Understanding and addressing these challenges is key to providing reliable sealing solutions.
Customization and Specification
One of the biggest challenges is creating seals that meet specific and often unique requirements.
Customization requires in-depth knowledge of both the sealing materials and the machinery they will serve.
Manufacturers must work closely with clients to understand their needs and design solutions that fit perfectly.
Quality Assurance
Maintaining consistent quality across all produced seals is another significant challenge.
Establishing robust quality assurance processes is necessary to ensure that every seal performs reliably.
This includes regular inspections, testing, and continuous improvement efforts.
Environmental Considerations
As industries become more environmentally conscious, OEM seal manufacturers face the challenge of developing eco-friendly seals.
This might involve using sustainable materials, reducing waste, and improving the energy efficiency of manufacturing processes.
The Future of OEM Seal Manufacturing
As technology advances, so does the field of OEM seal manufacturing.
Innovations in materials science, precision engineering, and testing methods promise even more reliable and efficient seals in the future.
Advanced Materials
Research is continually being conducted to develop advanced materials that offer superior performance.
These materials might include new polymers, composites, and metals with enhanced properties, such as greater temperature resistance, flexibility, and durability.
Automation and Precision
Automated manufacturing processes and advanced robotics are set to revolutionize OEM seal production.
These technologies enable higher precision and consistency, reducing the likelihood of defects and improving overall quality.
Smart Seals
The concept of smart seals is emerging, where seals are integrated with sensors and monitoring systems.
These smart seals can provide real-time data on their condition, performance, and any potential issues.
This proactive approach allows for timely maintenance and reduces the risk of failure.
Conclusion
OEM seal manufacturing is a critical aspect of many industries, ensuring the reliability and efficiency of machinery and equipment.
By focusing on quality, precision, and innovation, manufacturers can provide sealing solutions that meet the highest standards.
As the field continues to evolve, the future holds exciting possibilities for more advanced and reliable OEM seals, keeping industries running smoothly and safely.
資料ダウンロード
QCD調達購買管理クラウド「newji」は、調達購買部門で必要なQCD管理全てを備えた、現場特化型兼クラウド型の今世紀最高の購買管理システムとなります。
ユーザー登録
調達購買業務の効率化だけでなく、システムを導入することで、コスト削減や製品・資材のステータス可視化のほか、属人化していた購買情報の共有化による内部不正防止や統制にも役立ちます。
NEWJI DX
製造業に特化したデジタルトランスフォーメーション(DX)の実現を目指す請負開発型のコンサルティングサービスです。AI、iPaaS、および先端の技術を駆使して、製造プロセスの効率化、業務効率化、チームワーク強化、コスト削減、品質向上を実現します。このサービスは、製造業の課題を深く理解し、それに対する最適なデジタルソリューションを提供することで、企業が持続的な成長とイノベーションを達成できるようサポートします。
オンライン講座
製造業、主に購買・調達部門にお勤めの方々に向けた情報を配信しております。
新任の方やベテランの方、管理職を対象とした幅広いコンテンツをご用意しております。
お問い合わせ
コストダウンが利益に直結する術だと理解していても、なかなか前に進めることができない状況。そんな時は、newjiのコストダウン自動化機能で大きく利益貢献しよう!
(Β版非公開)