- お役立ち記事
- “Revolutionizing Japanese Manufacturing: A Successful Case of Supply Chain BPR”
“Revolutionizing Japanese Manufacturing: A Successful Case of Supply Chain BPR”
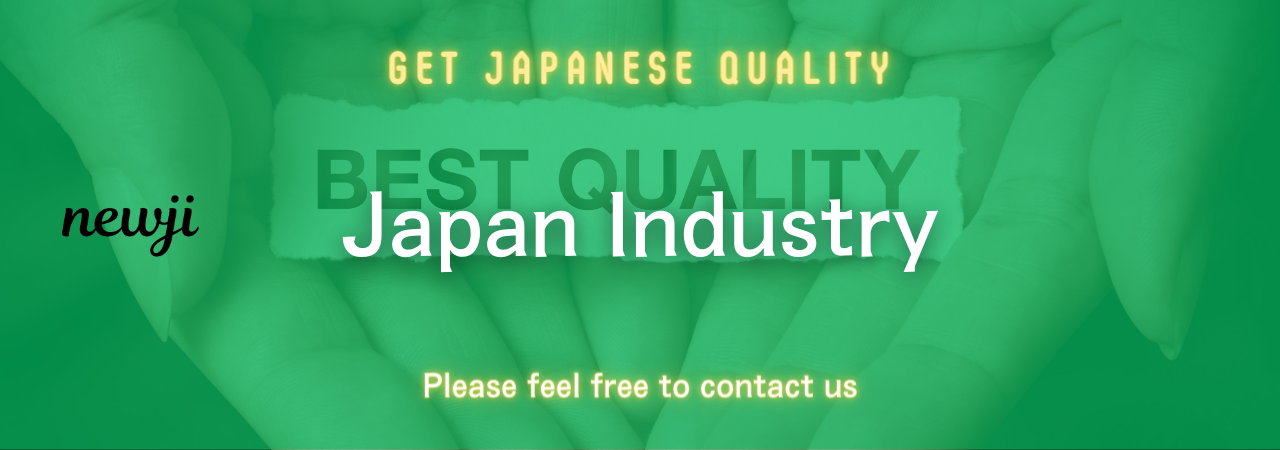
目次
Introduction to Supply Chain Business Process Re-engineering (BPR)
Business Process Re-engineering (BPR) is a radical redesign of an organization’s processes, aiming to improve efficiency, quality, and speed while reducing costs.
In the context of supply chain management, BPR endeavors to streamline end-to-end processes from procurement and purchasing through to final product delivery.
For manufacturing companies, this can mean faster production times, reduced waste, and ultimately, higher customer satisfaction.
The Importance of Supply Chain BPR in Japanese Manufacturing
Japanese manufacturing companies are renowned for their commitment to quality and efficiency, often exemplified by methodologies like Kaizen and Lean Manufacturing.
However, as global competition intensifies and market demands shift, even the most established companies must continuously innovate.
Incorporating BPR into supply chain management enables Japanese manufacturers to stay ahead.
By re-engineering their processes, these companies can better respond to changing market conditions, reduce costs, and maintain their reputation for high quality.
Case Study: Revolutionizing the Supply Chain of a Leading Japanese Manufacturer
Let’s delve into a successful case of supply chain BPR involving a prominent Japanese manufacturer specializing in automotive components.
Initially, the company’s supply chain was riddled with inefficiencies, including lengthy procurement cycles, high inventory levels, and frequent production delays.
Initial Analysis and Problem Identification
The first step in the BPR initiative was to conduct a thorough analysis of the existing supply chain.
A cross-functional team was established, comprising members from procurement, production, logistics, and quality control departments.
By auditing each process, the team identified several key issues:
1. **Long Lead Times:** Parts and raw materials often took weeks to arrive, causing delays in production.
2. **High Inventory Levels:** To buffer against these delays, the company maintained high inventory levels, leading to increased holding costs and potential obsolescence.
3. **Supplier Coordination Issues:** Limited communication with suppliers resulted in mismatches between supply and production requirements.
4. **Quality Control Challenges:** Variability in supplier quality affected the consistency of the final products.
Formulating a BPR Strategy
With a clear understanding of the problems, the team developed a strategic plan for re-engineering the supply chain.
Key elements of the strategy included:
1. **Supplier Consolidation:** Reducing the number of suppliers to establish more strategic partnerships.
2. **Implementing Just-In-Time (JIT) Inventory:** Aligning procurement closely with production schedules to minimize inventory levels.
3. **Enhanced Supplier Collaboration:** Establishing regular communication channels to improve coordination and responsiveness.
4. **Quality Assurance Mechanisms:** Implementing standardized quality checks at both supplier and in-house levels.
Implementation Phase
Supplier Consolidation
Initially, the company worked with over 50 suppliers, many of whom provided similar components.
Through a rigorous evaluation process, the company narrowed this down to the top 15 suppliers that met their quality, cost, and reliability criteria.
Just-In-Time Inventory Management
To implement JIT principles, the company invested in an advanced inventory management system.
This system provided real-time visibility into inventory levels and production schedules, ensuring that materials were ordered and delivered just as they were needed for production.
Enhanced Supplier Collaboration
Regular meetings and communication platforms were established with key suppliers.
This involved setting up bi-weekly virtual meetings to discuss forecasts, production plans, and any potential issues.
By fostering a closer relationship, suppliers were better able to align their production schedules with the company’s needs.
Quality Assurance Improvements
A collaborative approach to quality control was adopted.
The company and its suppliers worked together to establish standardized quality checklists and processes.
Regular audits were conducted to ensure compliance, and any discrepancies were addressed promptly.
Challenges and Solutions
Resistance to Change
One of the major challenges faced was resistance to change, both internally and from suppliers.
To address this, the company conducted extensive training sessions to explain the benefits of BPR and how it would improve overall efficiency.
Incentives were also provided to encourage adoption.
Technological Integration
Another significant challenge was integrating the new inventory management system with existing technology.
This required careful planning, phased rollouts, and close collaboration with IT specialists to ensure a seamless transition.
Maintaining JIT Consistency
Maintaining JIT inventory levels was initially difficult, especially in the face of unforeseen demand fluctuations.
To mitigate this, the company established safety stock levels for critical components and built flexibility into their supply chain to respond rapidly to changes.
Results and Key Takeaways
The re-engineering of the supply chain yielded numerous benefits:
1. **Reduced Lead Times:** The average lead time was reduced by 40%, enabling faster production cycles.
2. **Lower Inventory Levels:** Inventory holding costs decreased by 30% as a result of improved JIT practices.
3. **Enhanced Supplier Relationships:** Closer collaboration with suppliers led to better alignment and responsiveness.
4. **Improved Quality Control:** Consistent quality checks resulted in a 20% reduction in defects.
Lessons Learned
1. **Stakeholder Involvement:** Involving all relevant stakeholders throughout the BPR process is crucial for buy-in and successful implementation.
2. **Continuous Improvement:** BPR is not a one-time effort.
Regular reviews and updates are necessary to adapt to changing market conditions and technological advancements.
3. **Balanced Approach:** While JIT has its advantages, maintaining a balance with safety stock for critical components is important to mitigate risks.
Conclusion
Revolutionizing the supply chain through BPR has proven to be a game-changer for this leading Japanese manufacturer.
By addressing inefficiencies and fostering closer relationships with suppliers, the company was able to achieve significant improvements in lead times, inventory management, and product quality.
For other manufacturing companies looking to enhance their supply chain processes, the key lies in thorough analysis, strategic planning, and unwavering commitment to continuous improvement.
By learning from this successful case, companies can harness the power of BPR to stay competitive and thrive in an ever-evolving market.
資料ダウンロード
QCD調達購買管理クラウド「newji」は、調達購買部門で必要なQCD管理全てを備えた、現場特化型兼クラウド型の今世紀最高の購買管理システムとなります。
ユーザー登録
調達購買業務の効率化だけでなく、システムを導入することで、コスト削減や製品・資材のステータス可視化のほか、属人化していた購買情報の共有化による内部不正防止や統制にも役立ちます。
NEWJI DX
製造業に特化したデジタルトランスフォーメーション(DX)の実現を目指す請負開発型のコンサルティングサービスです。AI、iPaaS、および先端の技術を駆使して、製造プロセスの効率化、業務効率化、チームワーク強化、コスト削減、品質向上を実現します。このサービスは、製造業の課題を深く理解し、それに対する最適なデジタルソリューションを提供することで、企業が持続的な成長とイノベーションを達成できるようサポートします。
オンライン講座
製造業、主に購買・調達部門にお勤めの方々に向けた情報を配信しております。
新任の方やベテランの方、管理職を対象とした幅広いコンテンツをご用意しております。
お問い合わせ
コストダウンが利益に直結する術だと理解していても、なかなか前に進めることができない状況。そんな時は、newjiのコストダウン自動化機能で大きく利益貢献しよう!
(Β版非公開)