- お役立ち記事
- Introduction and benefits of DDM: Improving the efficiency of digital product design and manufacturing processes
Introduction and benefits of DDM: Improving the efficiency of digital product design and manufacturing processes
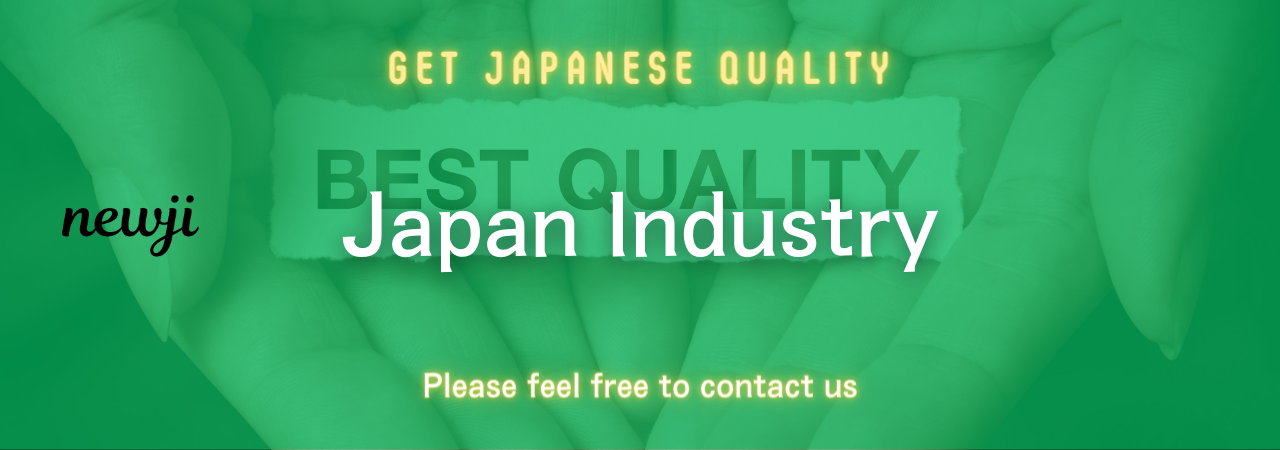
目次
Understanding Digital Design and Manufacturing (DDM)
Digital Design and Manufacturing (DDM) is a revolutionary approach that leverages digital tools and technologies to streamline the product design and manufacturing process.
Essentially, DDM encompasses the entire lifecycle of a product—from conceptualization and prototyping to final production—using advanced software and computer-aided techniques.
By integrating digital solutions, DDM enhances efficiency, reduces errors, and accelerates time-to-market.
At its core, DDM represents a transformative shift from traditional, manual processes to more automated, precise methodologies.
The Core Components of DDM
Computer-Aided Design (CAD)
One of the foundational elements of DDM is Computer-Aided Design (CAD).
CAD software allows designers to create detailed 3D models and simulations of products before they are manufactured.
With CAD, it becomes easier to visualize and modify designs, ensuring that the final product meets the required specifications and quality standards.
Computer-Aided Manufacturing (CAM)
Computer-Aided Manufacturing (CAM) is another critical component of DDM.
CAM software translates the digital designs created in CAD into machine instructions, which are then executed by manufacturing equipment such as CNC machines and 3D printers.
This level of automation minimizes human intervention, reducing the likelihood of errors and enhancing production efficiency.
3D Printing and Additive Manufacturing
3D printing, also known as additive manufacturing, plays a vital role in DDM by enabling rapid prototyping and production.
With 3D printing, complex geometries and customized parts can be produced on demand, significantly shortening the development cycle.
This technology is particularly beneficial for creating prototypes and small-batch productions.
Benefits of Implementing DDM in Product Design and Manufacturing
Enhanced Precision and Accuracy
One of the most significant advantages of DDM is the improved precision and accuracy it offers.
Digital tools ensure that every detail of the design is meticulously captured and translated into the manufacturing process.
This results in products that are consistently high in quality and meet exact specifications.
Reduced Time-to-Market
By streamlining the product development process, DDM helps manufacturers bring their products to market faster.
Digital simulations and rapid prototyping eliminate the need for multiple physical iterations, allowing for quicker refinements and adjustments.
This accelerated timeline is crucial in industries where time-to-market is a critical competitive factor.
Cost Savings
DDM can lead to substantial cost savings by reducing material waste and minimizing the need for rework.
The precision of digital tools ensures that resources are used efficiently, and errors are caught early in the design phase.
In addition, the automation provided by CAM reduces labor costs and improves overall operational efficiency.
Customization and Flexibility
Another notable benefit of DDM is the ability to offer customized products without incurring significant additional costs.
With digital tools, manufacturers can easily tweak designs and produce tailored solutions to meet specific customer needs.
This flexibility enhances customer satisfaction and opens up new market opportunities.
Challenges in Adopting DDM
High Initial Investment
One of the primary challenges in adopting DDM is the high initial investment required for advanced software and machinery.
While the long-term benefits are substantial, small and medium-sized enterprises may find the upfront costs prohibitive.
Careful planning and phased implementation can help mitigate this barrier.
Need for Skilled Workforce
Implementing DDM requires a workforce that is proficient in using digital tools and technologies.
This necessitates ongoing training and development programs to ensure that employees are equipped with the necessary skills.
Partnering with educational institutions and leveraging online learning platforms can be effective strategies for addressing this challenge.
Data Security Concerns
As with any digital transformation, data security is a critical concern when adopting DDM.
Manufacturers must invest in robust cybersecurity measures to protect their designs and intellectual property from cyber threats.
Implementing best practices such as encryption, access controls, and regular security audits can help safeguard sensitive information.
Future Trends in DDM
Integration of Artificial Intelligence (AI)
The integration of Artificial Intelligence (AI) in DDM is poised to revolutionize the industry further.
AI can enhance design optimization, predictive maintenance, and quality control, leading to even greater efficiencies.
AI-powered tools can analyze vast amounts of data to identify patterns and make informed decisions, driving continuous improvement in the manufacturing process.
Advancements in 3D Printing
The future of DDM will also see significant advancements in 3D printing technologies.
Innovations such as multi-material printing and bioprinting are expanding the range of applications for 3D printing.
These advancements will enable the production of more complex and functional prototypes, further enhancing the capabilities of DDM.
Blockchain for Supply Chain Transparency
Blockchain technology is emerging as a solution for enhancing transparency and traceability in the supply chain.
By providing a secure and immutable record of transactions, blockchain can ensure product authenticity and reduce the risk of counterfeiting.
The integration of blockchain with DDM can lead to a more secure and efficient manufacturing ecosystem.
Conclusion
Digital Design and Manufacturing (DDM) offers a transformative approach to the product design and manufacturing process.
By leveraging digital tools and technologies, DDM enhances precision, reduces time-to-market, and offers significant cost savings.
While there are challenges in adopting DDM, the long-term benefits far outweigh the initial hurdles.
As technology continues to evolve, the potential of DDM will only grow, paving the way for more innovative and efficient manufacturing solutions.
Embracing DDM is not just a trend but a strategic move towards a more sustainable and competitive future in the manufacturing industry.
資料ダウンロード
QCD調達購買管理クラウド「newji」は、調達購買部門で必要なQCD管理全てを備えた、現場特化型兼クラウド型の今世紀最高の購買管理システムとなります。
ユーザー登録
調達購買業務の効率化だけでなく、システムを導入することで、コスト削減や製品・資材のステータス可視化のほか、属人化していた購買情報の共有化による内部不正防止や統制にも役立ちます。
NEWJI DX
製造業に特化したデジタルトランスフォーメーション(DX)の実現を目指す請負開発型のコンサルティングサービスです。AI、iPaaS、および先端の技術を駆使して、製造プロセスの効率化、業務効率化、チームワーク強化、コスト削減、品質向上を実現します。このサービスは、製造業の課題を深く理解し、それに対する最適なデジタルソリューションを提供することで、企業が持続的な成長とイノベーションを達成できるようサポートします。
オンライン講座
製造業、主に購買・調達部門にお勤めの方々に向けた情報を配信しております。
新任の方やベテランの方、管理職を対象とした幅広いコンテンツをご用意しております。
お問い合わせ
コストダウンが利益に直結する術だと理解していても、なかなか前に進めることができない状況。そんな時は、newjiのコストダウン自動化機能で大きく利益貢献しよう!
(Β版非公開)