- お役立ち記事
- How to Provide High-Quality Cast Products with Die Casting OEM Manufacturing
How to Provide High-Quality Cast Products with Die Casting OEM Manufacturing
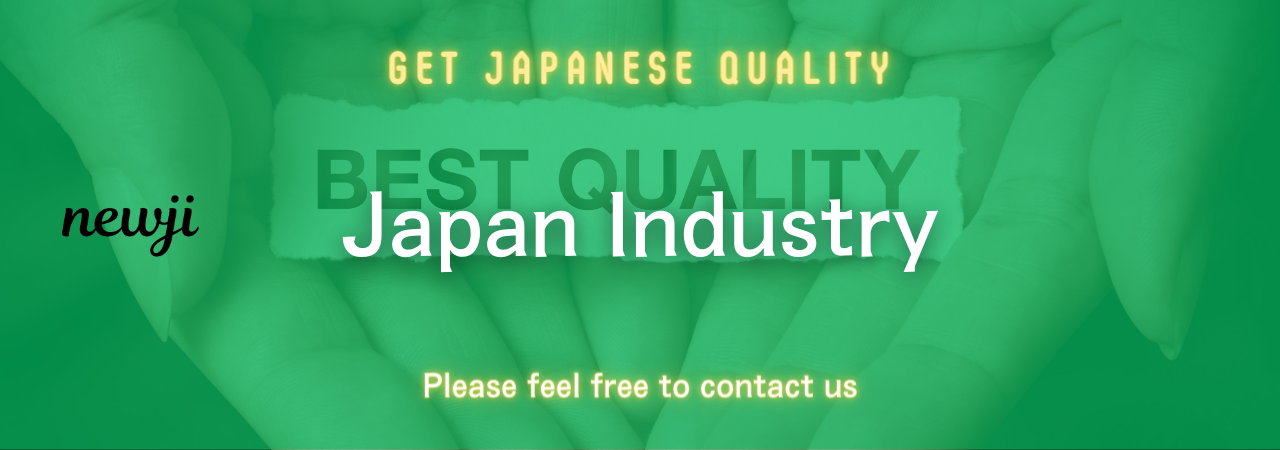
Die casting OEM manufacturing is a sophisticated process used to create intricate metal items for various industries.
This method guarantees precision, consistency, and cost-effectiveness, making it highly sought after.
But how do you ensure you produce high-quality cast products using this technique?
In this article, we’ll delve into the essential steps and considerations needed to achieve this.
目次
Understanding Die Casting OEM Manufacturing
Die casting is a manufacturing process where molten metal is injected into a mold to produce a product.
OEM (Original Equipment Manufacturer) manufacturing refers to companies that make parts or products for another company’s brand.
Combining these two concepts, die casting OEM manufacturing involves creating customized metal parts for other brands using the die casting method.
The Importance of Quality
For any manufacturing process, quality is imperative.
High-quality cast products ensure durability, efficiency, and customer satisfaction.
Moreover, subpar products can lead to costly recalls, damaged reputations, and loss of business.
Hence, achieving top-notch quality is non-negotiable in the world of die casting OEM manufacturing.
The Essential Steps in Die Casting OEM Manufacturing
1. Design and Engineering
Before embarking on the actual manufacturing, meticulous planning and design are crucial.
Collaboration between engineers and designers ensures that the product’s specifications align perfectly with the final output.
Advanced software is often used to create 3D models and simulations to foresee potential issues and rectify them beforehand.
2. Material Selection
Choosing the right material is foundational for producing high-quality cast products.
Common materials used in die casting include aluminum, zinc, magnesium, and copper.
Each material has distinct properties that make it suitable for specific applications.
For instance, aluminum is lightweight and corrosion-resistant, making it perfect for automotive parts.
Understanding the unique requirements of the product will guide the material selection process.
3. Mold Creation
The mold, or die, is an integral part of the die casting process.
Creating a high-precision die is crucial as it directly impacts the final product’s quality.
Typically made from hardened steel, the die consists of two halves that align perfectly to form the product’s shape.
Regular inspections and maintenance of molds ensure their longevity and precision.
4. Prepping the Die and Metal
Before injecting the molten metal, the die is prepped to ensure a flawless process.
This involves cleaning the mold and applying a lubricant to facilitate easy ejection of the cast part.
Simultaneously, the chosen metal is melted at optimal temperatures to achieve the right fluidity for casting.
5. Injection Process
Once everything is ready, the molten metal is injected into the die at high pressure.
This high-pressure injection ensures that the metal fills every nook and cranny of the mold, capturing even the smallest details.
Monitoring pressure parameters during this phase is vital to prevent defects like air pockets or incomplete sections.
Ensuring Consistent High Quality
1. Rigorous Quality Control
Implementing a stringent quality control system is key to maintaining high standards.
This involves routine checks at various stages, from raw material inspection to the final finished product.
Advanced techniques such as X-ray inspection and ultrasonic testing can detect internal defects that are not visible to the naked eye.
2. Skilled Workforce
Having a team of experienced and skilled professionals can make a significant difference.
Continuous training on the latest techniques and technologies ensures that your workforce remains adept at handling various challenges.
Encouraging a culture of quality awareness can lead to proactive identification and resolution of potential issues.
3. Technology and Automation
Incorporating modern technology and automation can enhance precision and efficiency.
Automated machines ensure consistency, especially for large-scale productions.
Moreover, technologies like real-time monitoring and AI-driven analytics can provide insights into the manufacturing process, allowing for immediate adjustments and improvements.
4. Continuous Improvement
Adopting a mindset of continuous improvement is vital.
Regularly analyzing feedback, both from internal processes and external customers, can highlight areas of improvement.
Implementing changes based on this feedback can lead to incremental enhancements in quality and efficiency.
The Role of Communication and Collaboration
Effective communication and collaboration between all stakeholders are essential.
This includes clear communication between the OEM manufacturer and the hiring company to ensure all specifications and expectations are met.
Additionally, fostering collaborative efforts between engineers, designers, quality control teams, and production workers can result in a smoother and more efficient manufacturing process.
Engaging with Suppliers
Building strong relationships with material and equipment suppliers can also impact the quality of your products.
Reliable suppliers ensure timely delivery of high-quality materials, reducing delays and maintaining the production schedule.
Regular communication and feedback with suppliers can cultivate mutual understanding and cooperation.
Environmental Considerations
Incorporating eco-friendly practices in die casting OEM manufacturing is becoming increasingly important.
Reducing waste, recycling scrap metal, and minimizing energy consumption not only help the environment but also improve cost efficiency.
Adopting sustainable practices can enhance your company’s reputation and appeal to environmentally-conscious customers.
Regulatory Compliance
Adhering to industry standards and regulatory requirements is non-negotiable.
Ensuring that your manufacturing process complies with international and local regulations guarantees the safety and reliability of your products.
Regular audits and updates to your compliance protocols ensure that your operations remain in good standing.
In conclusion, producing high-quality cast products through die casting OEM manufacturing involves meticulous planning, rigorous quality control, and continuous improvement.
By focusing on each stage of the manufacturing process, from design and material selection to injection and finishing, you can achieve superior results.
Moreover, fostering a collaborative environment, engaging with reliable suppliers, and incorporating sustainable practices can further enhance the overall quality and efficiency of your production.
資料ダウンロード
QCD調達購買管理クラウド「newji」は、調達購買部門で必要なQCD管理全てを備えた、現場特化型兼クラウド型の今世紀最高の購買管理システムとなります。
ユーザー登録
調達購買業務の効率化だけでなく、システムを導入することで、コスト削減や製品・資材のステータス可視化のほか、属人化していた購買情報の共有化による内部不正防止や統制にも役立ちます。
NEWJI DX
製造業に特化したデジタルトランスフォーメーション(DX)の実現を目指す請負開発型のコンサルティングサービスです。AI、iPaaS、および先端の技術を駆使して、製造プロセスの効率化、業務効率化、チームワーク強化、コスト削減、品質向上を実現します。このサービスは、製造業の課題を深く理解し、それに対する最適なデジタルソリューションを提供することで、企業が持続的な成長とイノベーションを達成できるようサポートします。
オンライン講座
製造業、主に購買・調達部門にお勤めの方々に向けた情報を配信しております。
新任の方やベテランの方、管理職を対象とした幅広いコンテンツをご用意しております。
お問い合わせ
コストダウンが利益に直結する術だと理解していても、なかなか前に進めることができない状況。そんな時は、newjiのコストダウン自動化機能で大きく利益貢献しよう!
(Β版非公開)