- お役立ち記事
- DX in Layout Design Accelerates Startup of Mass Production of Advanced Semiconductors
DX in Layout Design Accelerates Startup of Mass Production of Advanced Semiconductors
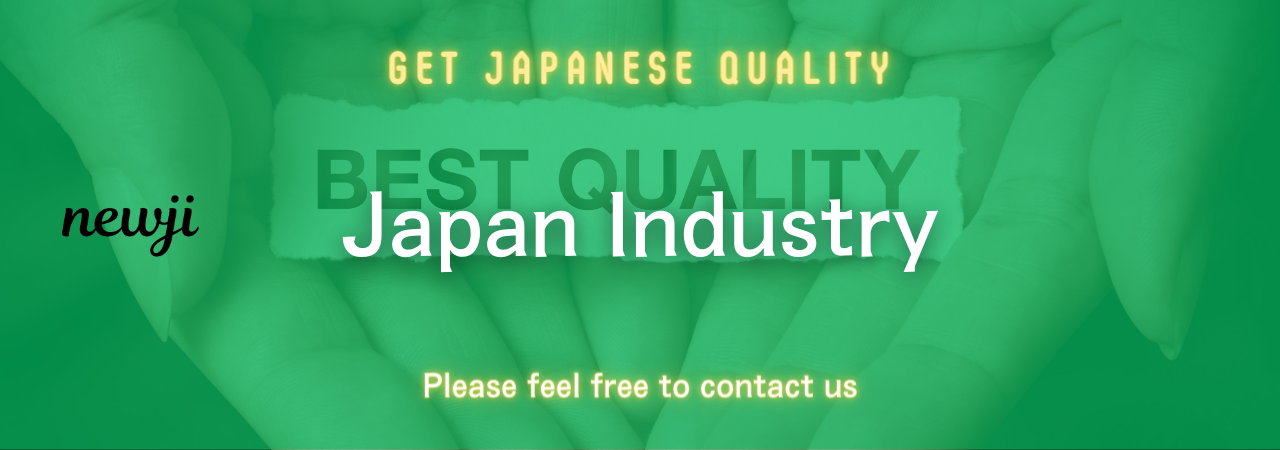
In the ever-evolving world of technology, the production of advanced semiconductors plays a critical role, forming the backbone of numerous modern devices.
However, designing and mass-producing these tiny yet complex components is no small feat.
This is where Digital Transformation (DX) in layout design comes into play.
It speeds up the entire process, allowing for efficient scaling of production and ensuring that technology keeps up with growing demands.
目次
What is Digital Transformation (DX) in Layout Design?
Digital Transformation, often abbreviated as DX, involves integrating digital technology into all areas of a business.
When it comes to layout design for semiconductors, DX encompasses the utilization of advanced digital tools and methodologies to optimize the design and manufacturing processes.
This transformation not only streamlines workflows but also enhances accuracy, reduces costs, and shortens the time required to bring new semiconductor products from concept to market.
Why DX Matters in Semiconductor Production
The semiconductor industry is incredibly competitive and fast-paced.
Any delay in production can translate to significant financial losses and a setback in innovation.
Traditional design methods are becoming increasingly insufficient to meet the urgent needs of the market.
This is where DX becomes crucial.
By adopting digital tools and techniques, companies can accelerate the design and manufacturing process, ensuring they remain ahead of the curve.
Key Benefits of DX in Layout Design
Speeding Up the Design Process
The design phase of semiconductor production is intricate and time-consuming.
DX leverages automation and advanced algorithms to expedite this process.
For example, computer-aided design (CAD) software can quickly simulate and optimize layouts, significantly reducing the time designers spend in the conceptual phase.
This allows for faster iteration cycles, ultimately leading to a quicker transition from design to prototype.
Enhancing Precision and Quality
Human errors are inevitable in any manual process.
However, in semiconductor production, even the smallest mistake can lead to defective products and wasted resources.
DX tools bring a level of precision that’s hard to achieve manually.
Automated rule checks and real-time error detection during the layout design phase ensure higher quality and consistency in the final product.
This not only reduces the risk of defects but also ensures that the semiconductors meet the required performance standards.
Improving Collaboration
The process of designing a semiconductor often involves multiple teams, including designers, engineers, and stakeholders.
DX facilitates seamless collaboration by providing cloud-based platforms where team members can work together in real-time, regardless of their geographical location.
These platforms offer centralized storage for all project files, real-time updates, and integrated communication tools, making it easier for teams to collaborate and make informed decisions swiftly.
Cost Reduction
While the initial investment in digital tools and training might seem high, the long-term benefits far outweigh these costs.
DX reduces the need for physical prototypes, as simulations can identify potential issues early in the design phase.
This leads to significant savings on materials and resources.
Moreover, the optimization and automation capabilities of DX tools minimize the need for manual interventions, reducing labor costs and increasing overall operational efficiency.
How DX is Facilitating Mass Production
Scalable Solutions
One of the greatest challenges in semiconductor production is scaling up from prototype to mass production.
DX provides scalable solutions that allow manufacturers to ramp up production without compromising on quality.
Automation tools can handle repetitive tasks with high precision and speed, ensuring that each semiconductor chip is produced to the same specifications.
Streamlined Supply Chain
A streamlined supply chain is essential for mass production.
DX tools offer advanced logistics and supply chain management solutions that optimize the procurement, production, and distribution processes.
By tracking inventory in real-time and predicting future needs, manufacturers can avoid delays caused by material shortages or bottlenecks.
Predictive Maintenance
Downtime can be devastating in a mass production setting.
Predictive maintenance, powered by DX, uses data analytics to predict when and where equipment failures might occur.
This allows for proactive maintenance, reducing the risk of unexpected downtime and ensuring that production continues smoothly.
Data-Driven Decisions
DX leverages big data analytics to provide manufacturers with valuable insights into their operations.
By analyzing data from various stages of the production process, manufacturers can identify inefficiencies, predict trends, and make data-driven decisions that enhance overall productivity and profitability.
The Future of DX in Semiconductor Production
The digital transformation of semiconductor layout design is a continuous journey.
As technology evolves, so do the tools and techniques that drive DX.
With advancements in Artificial Intelligence (AI) and Machine Learning (ML), we can expect even greater levels of automation and optimization.
AI and ML algorithms can analyze vast amounts of data to improve design accuracy, predict potential issues, and suggest innovative solutions, further accelerating the production process.
Moreover, the integration of the Internet of Things (IoT) in manufacturing environments will enable smarter factories with interconnected systems that communicate and collaborate autonomously.
This will result in increased efficiency, reduced downtime, and higher-quality semiconductor products.
In conclusion, DX in layout design is revolutionizing the field of semiconductor production.
By embracing digital transformation, companies can accelerate their production processes, improve product quality, enhance collaboration, and reduce costs.
As the demand for advanced semiconductors continues to grow, the adoption of DX will be crucial in keeping pace with technological advancements and staying competitive in the market.
資料ダウンロード
QCD調達購買管理クラウド「newji」は、調達購買部門で必要なQCD管理全てを備えた、現場特化型兼クラウド型の今世紀最高の購買管理システムとなります。
ユーザー登録
調達購買業務の効率化だけでなく、システムを導入することで、コスト削減や製品・資材のステータス可視化のほか、属人化していた購買情報の共有化による内部不正防止や統制にも役立ちます。
NEWJI DX
製造業に特化したデジタルトランスフォーメーション(DX)の実現を目指す請負開発型のコンサルティングサービスです。AI、iPaaS、および先端の技術を駆使して、製造プロセスの効率化、業務効率化、チームワーク強化、コスト削減、品質向上を実現します。このサービスは、製造業の課題を深く理解し、それに対する最適なデジタルソリューションを提供することで、企業が持続的な成長とイノベーションを達成できるようサポートします。
オンライン講座
製造業、主に購買・調達部門にお勤めの方々に向けた情報を配信しております。
新任の方やベテランの方、管理職を対象とした幅広いコンテンツをご用意しております。
お問い合わせ
コストダウンが利益に直結する術だと理解していても、なかなか前に進めることができない状況。そんな時は、newjiのコストダウン自動化機能で大きく利益貢献しよう!
(Β版非公開)