- お役立ち記事
- Commutator Technology and Its Applications in Manufacturing
Commutator Technology and Its Applications in Manufacturing
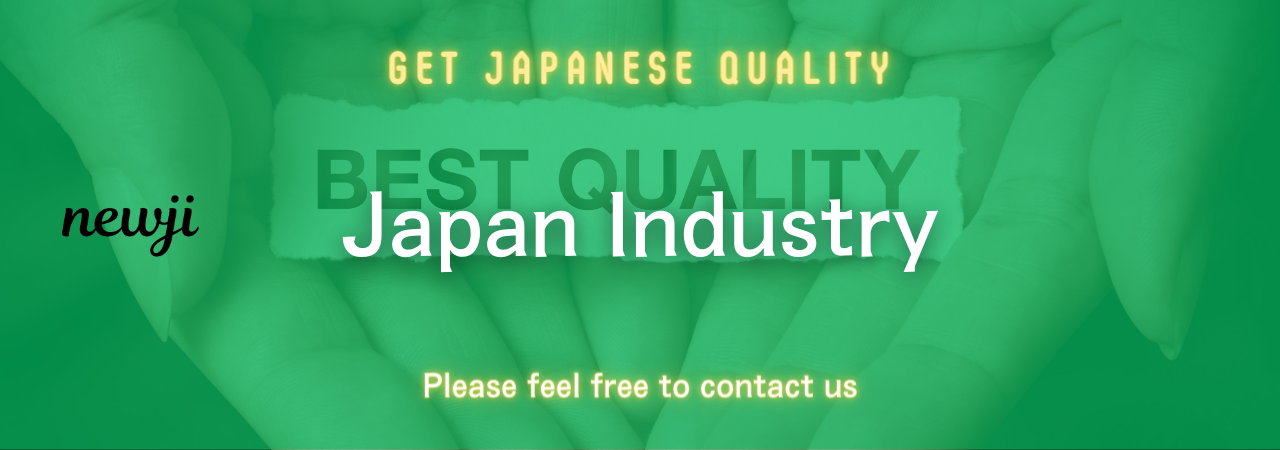
Commutator technology has long played a crucial role in the world of manufacturing. Understanding how a commutator works and its various applications can help improve manufacturing efficiency and product quality. This article will delve into what commutators are, their functions, and their broad applications in the manufacturing industry.
目次
What is a Commutator?
A commutator is an essential component in electric motors and generators. It consists of a cylindrical structure made of segmented metal contacts. These segments are separated by insulating material, typically mica. The main function of a commutator is to reverse the direction of current flow in the motor windings, ensuring that the motor produces a consistent unidirectional torque.
How Does a Commutator Work?
When current flows through the commutator from a power source, it energizes the motor windings. As the motor rotates, the commutator segments come into contact with stationary carbon brushes. These brushes transfer current to the commutator segments, which causes the flow of electricity to switch directions. This commutation ensures that the armature windings produce a continuous rotational force, which drives the motor.
Types of Commutators
There are several types of commutators used in different applications:
– **Cylindrical Commutators**: These are the most common type and are used in the majority of DC motors. They provide reliable and efficient commutation for various industrial applications.
– **Disc Commutators**: These are used in smaller, high-speed motors where space is a constraint. They are less durable than cylindrical commutators but are useful in specific applications.
– **Rational Axial Commutators**: These are designed for specialized motors, providing improved cooling and performance. They are typically used in high-stress environments.
Applications of Commutator Technology in Manufacturing
Commutator technology has a wide range of applications in manufacturing environments. Below are some key areas where this technology has made a significant impact.
Electric Motors
Commutators are a vital component of DC electric motors. These motors are widely used in manufacturing due to their efficiency, reliability, and precise control. Industries such as automotive manufacturing, machine tooling, and packaging utilize DC motors to drive conveyor belts, robotic arms, and other machinery.
Power Tools
Power tools like drills, saws, and sanders often rely on commutator-equipped motors. These tools deliver high torque and are essential in workshops and manufacturing plants. The commutator’s role in these tools ensures smooth and reliable operation, enabling workers to complete tasks with precision.
Generators
Generators convert mechanical energy into electrical energy, and commutators are crucial for ensuring consistent power output. Backup power systems, renewable energy generators, and portable power units frequently employ commutators. This technology helps maintain a stable electrical supply, which is essential for uninterrupted manufacturing processes.
Automotive Industry
In the automotive industry, commutator technology is employed in starter motors, windshield wiper systems, and electric window regulators. These components are vital for vehicle operation and safety. The reliable performance of commutators ensures that these systems function efficiently, enhancing overall vehicle quality.
Home Appliances
Many household appliances like washing machines, vacuum cleaners, and blenders use commutator-based motors. In manufacturing, these appliances are produced on a large scale, and the efficiency of commutator technology helps keep production lines running smoothly. This efficiency translates into cost savings and higher-quality products for consumers.
Advantages of Commutator Technology
The use of commutator technology in manufacturing offers several benefits:
High Efficiency
Commutator technology ensures that electric motors operate with high efficiency. This efficiency translates into reduced energy consumption and lower production costs. In industries where energy management is critical, the use of efficient motors is a significant advantage.
Precision Control
DC motors with commutators provide precise control over speed and torque. This level of control is crucial in manufacturing processes that demand accuracy, such as CNC machining and robotic assembly. With commutated motors, manufacturers can achieve the exact specifications required for their products.
Cost-Effectiveness
The reliability and durability of commutator technology contribute to lower maintenance costs. These components require minimal upkeep, reducing downtime and production interruptions. This cost-effectiveness benefits manufacturers by enhancing productivity and profitability.
Versatility
Commutator technology is versatile and adaptable to various manufacturing applications. Whether it’s driving machinery, powering tools, or generating electricity, commutators offer a wide range of uses. This versatility makes them a valuable asset in diverse industrial settings.
Challenges and Future Developments
While commutator technology has numerous advantages, it also faces certain challenges. One primary issue is wear and tear. The continuous contact between brushes and commutator segments can lead to abrasion and the eventual need for replacement. Technological advancements are ongoing to mitigate these issues, including the development of more durable materials and improved designs.
The future of commutator technology looks promising with innovations aimed at increasing efficiency and extending the lifespan of motors. The integration of advanced materials, such as carbon composites, promises to enhance the durability of commutators. Additionally, research into brushless DC motors presents an interesting direction, potentially reducing reliance on traditional commutator systems while retaining similar benefits.
Conclusion
Commutator technology is indispensable in the manufacturing industry. Its role in enabling efficient motor operation, precise control, and cost-effective production makes it a cornerstone of modern manufacturing processes. As technology continues to evolve, the future of commutator applications looks bright, promising even greater efficiency and reliability for industrial environments.
資料ダウンロード
QCD調達購買管理クラウド「newji」は、調達購買部門で必要なQCD管理全てを備えた、現場特化型兼クラウド型の今世紀最高の購買管理システムとなります。
ユーザー登録
調達購買業務の効率化だけでなく、システムを導入することで、コスト削減や製品・資材のステータス可視化のほか、属人化していた購買情報の共有化による内部不正防止や統制にも役立ちます。
NEWJI DX
製造業に特化したデジタルトランスフォーメーション(DX)の実現を目指す請負開発型のコンサルティングサービスです。AI、iPaaS、および先端の技術を駆使して、製造プロセスの効率化、業務効率化、チームワーク強化、コスト削減、品質向上を実現します。このサービスは、製造業の課題を深く理解し、それに対する最適なデジタルソリューションを提供することで、企業が持続的な成長とイノベーションを達成できるようサポートします。
オンライン講座
製造業、主に購買・調達部門にお勤めの方々に向けた情報を配信しております。
新任の方やベテランの方、管理職を対象とした幅広いコンテンツをご用意しております。
お問い合わせ
コストダウンが利益に直結する術だと理解していても、なかなか前に進めることができない状況。そんな時は、newjiのコストダウン自動化機能で大きく利益貢献しよう!
(Β版非公開)