- お役立ち記事
- DXing of Milling Processes Directly Improves Product Development Capability
DXing of Milling Processes Directly Improves Product Development Capability
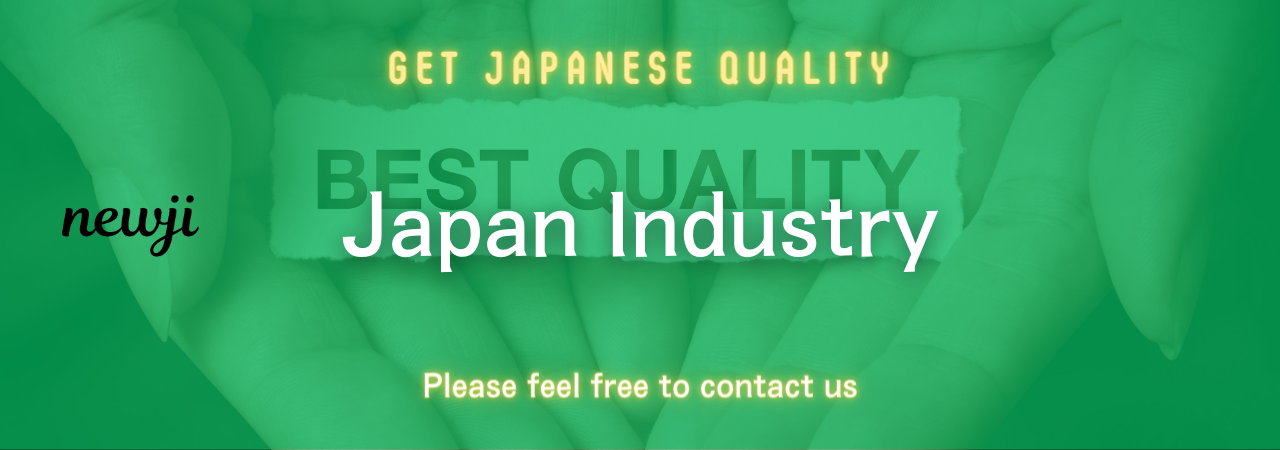
In today’s rapidly evolving industrial landscape, organizations constantly seek ways to improve efficiency and product quality.
One of the most transformative technologies in manufacturing is Digital Transformation (DX), especially when applied to milling processes.
Milling, a critical operation in manufacturing, involves the removal of material from a workpiece to achieve a desired shape or finish.
Integrating DX into milling processes directly enhances product development capabilities, leading to numerous benefits for manufacturers.
目次
What is Digital Transformation (DX) in Milling?
Digital Transformation (DX) refers to leveraging digital technologies to revolutionize business processes and operations.
In the context of milling, DX involves the integration of advanced tools like Computer-Aided Design (CAD), Computer-Aided Manufacturing (CAM), Internet of Things (IoT), and data analytics.
These technologies can optimize milling operations by improving precision, efficiency, and overall process management.
Benefits of Implementing DX in Milling Processes
There are several compelling reasons to adopt digital transformation in milling operations.
Enhanced Precision and Accuracy
One of the primary benefits of DX in milling is enhanced precision.
Advanced CAD and CAM software allow for precise design and machining, reducing errors and ensuring consistent product quality.
By simulating milling operations before actual execution, manufacturers can foresee potential issues and make necessary adjustments, enhancing overall accuracy.
Increased Efficiency and Productivity
DX technologies streamline milling processes, significantly increasing efficiency.
Automated systems and real-time monitoring reduce downtime and minimize human error.
IoT-enabled machines can communicate and coordinate with each other, optimizing the workflow and ensuring seamless operations.
Additionally, data analytics can identify bottlenecks and suggest improvements, leading to faster production cycles.
Cost Reduction
Incorporating DX into milling processes can result in substantial cost savings.
Improved precision reduces material waste, while predictive maintenance, facilitated by IoT, minimizes machine downtime and repair costs.
Overall process optimization leads to lower operational expenses and increased profitability.
Enhanced Product Development
With DX tools, product development becomes more efficient and innovative.
Manufacturers can rapidly prototype and test new designs, shortening the development cycle.
Real-time data and feedback allow for quick adjustments, enabling more agile and responsive product development.
This capability is crucial in a competitive market where the speed of innovation can be a key differentiator.
Key Technologies Driving DX in Milling
Several key technologies drive digital transformation in milling processes, each contributing uniquely to enhanced capabilities.
Computer-Aided Design (CAD) and Computer-Aided Manufacturing (CAM)
CAD and CAM software are central to digital milling operations.
CAD allows designers to create detailed 3D models of products, which can then be used to generate precise instructions for milling machines via CAM.
This integration ensures high precision and facilitates the seamless transfer of design data to the manufacturing floor.
Internet of Things (IoT)
IoT technology enables connectivity between milling machines and other equipment, creating a networked environment.
IoT devices gather and transmit data in real-time, providing valuable insights into the performance and health of machinery.
This data-driven approach can optimize machine operation and maintenance, significantly enhancing reliability and productivity.
Data Analytics and Artificial Intelligence (AI)
Data analytics and AI play a crucial role in optimizing milling processes.
By analyzing data from various sources, AI algorithms can predict maintenance needs, identify patterns, and suggest process improvements.
AI can also enhance the decision-making process, providing actionable insights that lead to better operational outcomes.
Case Studies: Successful DX Implementation in Milling
Several manufacturing companies have successfully implemented DX in their milling processes, demonstrating its tangible benefits.
Automotive Industry
In the automotive industry, companies have used DX to enhance precision and efficiency in milling engine components.
By integrating CAD/CAM and IoT technologies, they reduced errors and sped up production times, leading to faster time-to-market for new vehicle models.
Aerospace Sector
Aerospace manufacturers have leveraged DX to produce highly complex and precise components.
Using advanced analytics and AI, they optimized their milling processes, achieving higher durability and performance in critical parts.
The improved accuracy also resulted in significant cost savings in material and labor.
Medical Device Manufacturing
In the medical field, manufacturers have adopted DX to ensure the highest standards of quality and precision.
By utilizing data analytics and real-time monitoring, they achieved near-zero defects in life-critical components, enhancing patient safety and regulatory compliance.
Challenges and Considerations in Adopting DX
While the benefits of DX are clear, manufacturers need to consider several challenges and factors before implementing these technologies.
Initial Investment and Training
The initial investment in advanced technologies and software can be substantial.
Companies must also invest in training their workforce to effectively use these new tools.
However, the long-term benefits and cost savings often outweigh the upfront costs.
Data Security and Privacy
With increased connectivity comes the need for robust data security measures.
Companies must ensure that their digital ecosystems are protected against cyber threats and that sensitive data is properly managed.
Cultural Change
Adopting DX requires a cultural shift within the organization.
Employees must be open to change and willing to adapt to new workflows and technologies.
Effective communication and change management strategies are crucial for a successful transition.
The Future of DX in Milling
As technology continues to advance, the role of DX in milling processes will only become more significant.
Emerging technologies such as augmented reality (AR) and virtual reality (VR) could further enhance design and simulation capabilities.
Moreover, ongoing developments in AI and machine learning will lead to even more intelligent and autonomous milling operations.
In conclusion, the digital transformation of milling processes directly improves product development capability, offering numerous advantages from enhanced precision and efficiency to cost savings and innovative potential.
By embracing DX, manufacturers can stay competitive in an increasingly demanding market and deliver high-quality products faster and more efficiently.
The journey towards a fully digitalized milling process is not without its challenges, but the rewards make it a worthwhile investment for the future.
資料ダウンロード
QCD調達購買管理クラウド「newji」は、調達購買部門で必要なQCD管理全てを備えた、現場特化型兼クラウド型の今世紀最高の購買管理システムとなります。
ユーザー登録
調達購買業務の効率化だけでなく、システムを導入することで、コスト削減や製品・資材のステータス可視化のほか、属人化していた購買情報の共有化による内部不正防止や統制にも役立ちます。
NEWJI DX
製造業に特化したデジタルトランスフォーメーション(DX)の実現を目指す請負開発型のコンサルティングサービスです。AI、iPaaS、および先端の技術を駆使して、製造プロセスの効率化、業務効率化、チームワーク強化、コスト削減、品質向上を実現します。このサービスは、製造業の課題を深く理解し、それに対する最適なデジタルソリューションを提供することで、企業が持続的な成長とイノベーションを達成できるようサポートします。
オンライン講座
製造業、主に購買・調達部門にお勤めの方々に向けた情報を配信しております。
新任の方やベテランの方、管理職を対象とした幅広いコンテンツをご用意しております。
お問い合わせ
コストダウンが利益に直結する術だと理解していても、なかなか前に進めることができない状況。そんな時は、newjiのコストダウン自動化機能で大きく利益貢献しよう!
(Β版非公開)